How are Microchips Made? 🖥️🛠️ CPU Manufacturing Process Steps
Summary
TLDRThis video script offers an in-depth exploration of microchip manufacturing, detailing the complex process of creating billions of transistors on a tiny chip. It delves into the semiconductor fabrication plant's operations, where silicon wafers undergo around a thousand processes over three months. The script explains the use of high-tech tools, the importance of cleanrooms, and the meticulous steps involved in building layers of metal interconnects and transistors. It also touches on the post-manufacturing testing and categorization of CPUs, providing a comprehensive look at the technology behind our modern devices.
Takeaways
- 📱 A single smartphone can contain 62 microchips with a total of 90 billion transistors, showcasing the high density of modern technology.
- 🏭 Microchips are manufactured in semiconductor fabrication plants, which are vast facilities with clean rooms spanning areas equivalent to 8 football fields.
- 💰 The machines in these plants are extremely expensive, ranging from a few million to 170 million dollars each, reflecting the high cost of microchip production.
- ⚙️ The production process involves around a thousand steps over a 3-month period, highlighting the complexity and time-consuming nature of microchip manufacturing.
- 🔬 Each silicon wafer can be covered in hundreds of CPU chips, each containing 26 billion transistors, indicating the scale of integration in modern chips.
- 🔍 The transistors are incredibly small, with FinFETs having dimensions of 36 by 6 by 52 nanometers, emphasizing the nanoscopic precision required.
- 🔗 The manufacturing process includes 80 different layers of patterns, each requiring a separate photomask, which are costly and crucial for the design transfer.
- 🛠️ There are six main groups of semiconductor tools: mask layer creation, material addition, material removal, material modification, wafer cleaning, and wafer inspection.
- 🔬 Ion implanters are used to modify the silicon by adding dopants to create P and N regions for transistors, and they are a key part of the front-end manufacturing process.
- 🧼 Cleaning and inspection steps are frequent to ensure the wafer's cleanliness and to check for defects, which is critical for the quality of the final product.
- 📈 The video script took over 1300 hours to create, demonstrating the extensive effort behind producing educational content on complex topics like microchip fabrication.
Q & A
How many microchips are inside the smartphone mentioned in the script?
-There are 62 microchips inside the smartphone.
What is the total number of transistors contained in the microchips of the smartphone?
-The microchips contain a total of 90 billion transistors.
What is the size of a clean room in a semiconductor fabrication plant as described in the script?
-The clean room in a semiconductor fabrication plant spans the area of 8 football fields.
How much does a single machine in the semiconductor fabrication plant cost?
-The cost of a single machine in the semiconductor fabrication plant ranges from a few million to 170 million dollars.
How many processes does a silicon wafer undergo in the microchip manufacturing process?
-A silicon wafer undergoes around a thousand processes in the microchip manufacturing process.
What is the number of CPU chips that can fit on a 300-millimeter silicon wafer?
-A 300-millimeter silicon wafer can fit 230 CPU chips.
How many billions of transistors does each CPU chip contain?
-Each CPU chip contains 26 billion transistors.
How many nanometers are the channel dimensions of the FinFETs transistors mentioned in the script?
-The channel dimensions of the FinFETs transistors are 36 by 6 by 52 nanometers.
What is the total number of metal layers of wires in the CPU described in the script?
-There are a total of 17 metal layers of wires in the CPU.
How many process steps are there in the sequence to build all the 80 layers of the die?
-To build all the 80 layers of the die, there are 940 process steps.
What is the purpose of the cleaning and inspection steps in the microchip manufacturing process?
-The purpose of the cleaning and inspection steps in the microchip manufacturing process is to remove any stray particles that may have fallen onto the wafer and to ensure that each of the processes is being executed with nanometer-level precision.
Outlines
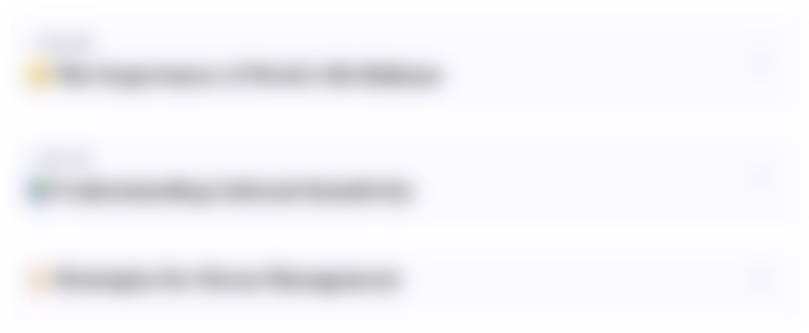
This section is available to paid users only. Please upgrade to access this part.
Upgrade NowMindmap
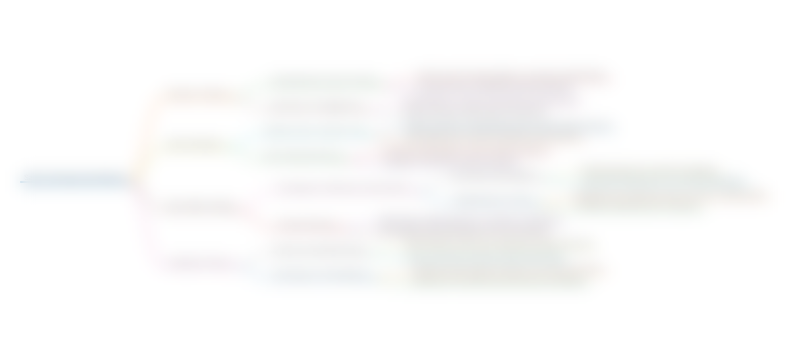
This section is available to paid users only. Please upgrade to access this part.
Upgrade NowKeywords
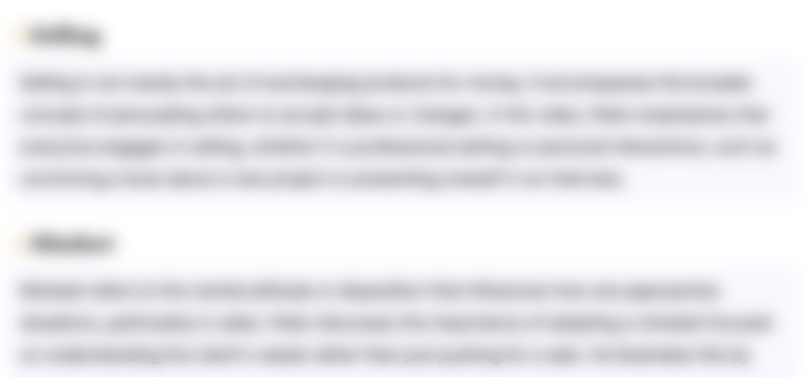
This section is available to paid users only. Please upgrade to access this part.
Upgrade NowHighlights
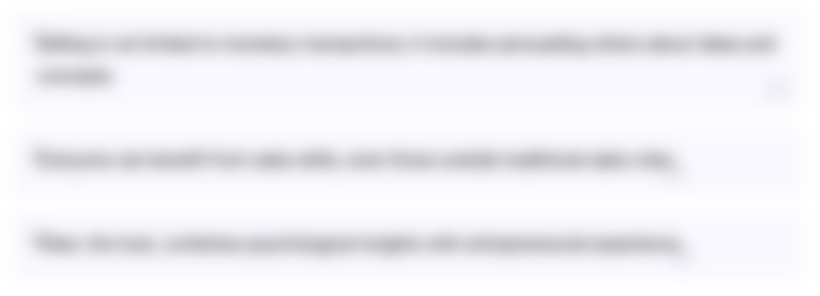
This section is available to paid users only. Please upgrade to access this part.
Upgrade NowTranscripts
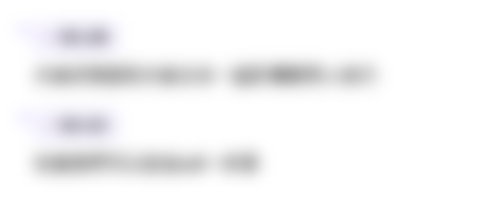
This section is available to paid users only. Please upgrade to access this part.
Upgrade NowBrowse More Related Video

💻 How Are Microchips Made?

How EUV lithography works
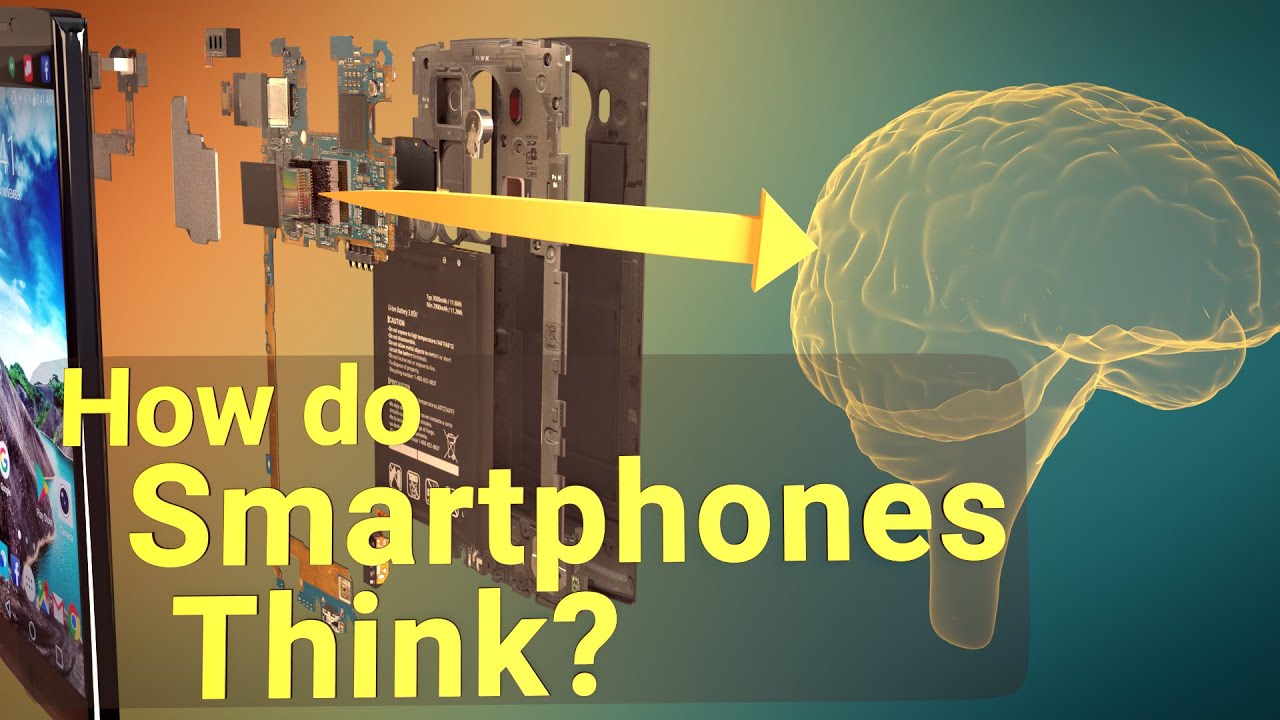
How do Smartphone CPUs Work? || Inside the System on a Chip

Introduction - Cadence Crash Course #1
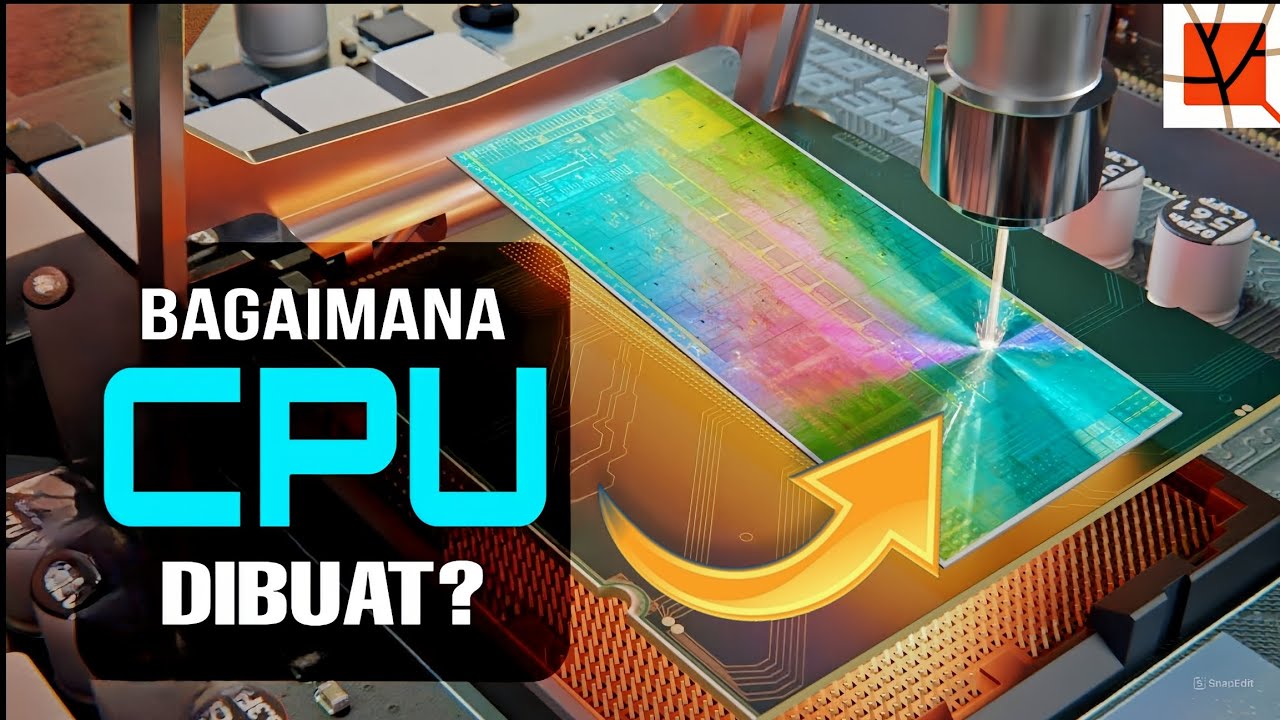
Bagaimana Microchip Dibuat? || Langkah - Langkah Proses Pembuatan CPU Komputer
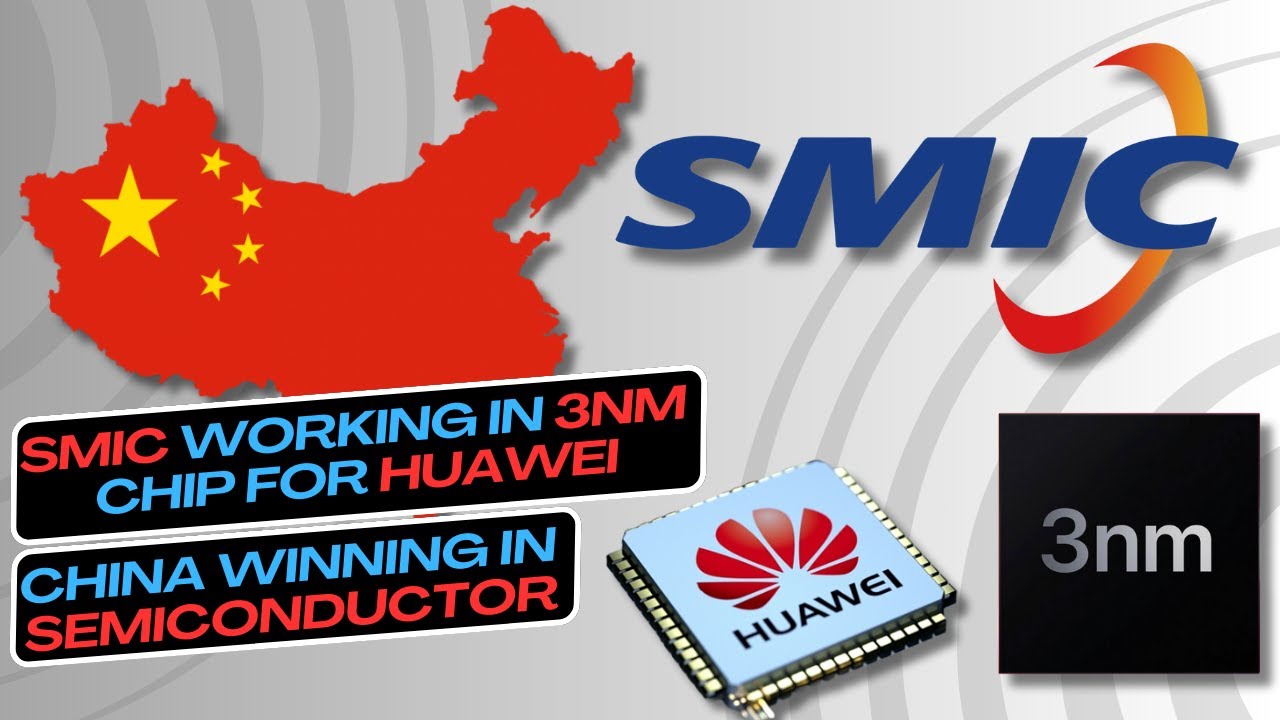
SMIC making a 3nm Chip for Huawei | China Semiconductor | Space Tech & Military Innovation AI
5.0 / 5 (0 votes)