Bene Bono's Warehouse Production Line: Web Technologies Meet Industrial Sensors
Summary
TLDRこのスクリプトは、Bonuというフランスの会社が、食品ロスを減らすために不規則な形や色の果物や野菜を販売するビジネスモデルと、その生産ラインの最適化について説明しています。Bonuは、顧客がオンラインで注文をカスタマイズできるフルカスタマイズ機能を提供し、生産性向上とエラーの減少を目指して、新しいセンサー技術を導入しました。このイノベーションにより、Bonuはより効率的で信頼性の高いサービスを提供し、将来的にはデータ利活用とより多くの機能拡張を計画しています。
Takeaways
- 📈 会社のミッションは、食品ロスから良い製品(果物や野菜)を救うことです。
- 🥦 販売している商品は、通常の店では販売されないが、理由があって販売されない商品も含まれています。
- 📊 3年間の運用により、フランスとスペインの6つの主要都市に存在し、2万以上の顧客を有しています。
- 🚀 週に1万を超える注文を準備し、最大の倉庫でその数は数ヶ月以内に倍増する予定です。
- 🛠️ 現在の生産システムはシンプルで効率的ですが、よりカスタマイズされた注文に対応できないため、改善が必要とされています。
- 🔄 新しい生産ラインには、紙レスで、従業員のトレーニングが不要、果物や野菜のリストが変わると自動的に対応できるシステムが採用されています。
- 🔧 技術的な選択においては、ロックインされていない高度に信頼性のあるシステムを追求し、技術チームのスキルを最大限に活用することを目指しています。
- 🌐 産業用センサーを使用しつつ、オープンのEthernet/IPプロトコルを利用することで、プロペティのハードウェアから離れています。
- 📱 従業員用のスクリーンは、消費者向けのタブレットで、従業員が簡単に注文を準備できるようになっています。
- 🔄 部署には多くのスクリーンがあり、生産ライン上の各ステーションで何が起こっているかをリアルタイムで確認できます。
- 🔍 データの利活用により、マージン計算や納品チームの選択肢に役立つ情報を得ることができます。
- 🚧 今後の課題としては、より高い信頼性を確保し、アプリのバージョンアップや監視システムの改善が挙げられます。
Q & A
Bonuのミッションは何ですか?
-Bonuのミッションは、食品ロスを減らすことです。具体的には、通常の店では販売されない理由がある果物や野菜をセーブし、それらを消費者に届けることです。
Bonuが提供する商品はどのようなものですか?
-Bonuは果物や野菜を始めとして、一年半後の現在では食品用品や卫生・家事用品、ペットフードまで展開しています。これらの商品は通常の店では販売されないが、品質には問題がありません。
Bonuの配達システムはどのように動作しますか?
-Bonuはサブスクリプションモデルを採用しており、顧客は毎週の注文を準備し、直接消費者に商品を販売しています。また、フルカスタマイズ可能な注文システムを導入し、顧客は毎週の提供商品から自分の注文を完全にカスタマイズすることができます。
Bonuの生産システムの課題は何でしたか?
-Bonuの生産システムは非常に基本的で、デジタルツールがありませんでした。従業員は注文準備中に紙のリストを読み、注文の準備を行っていました。しかし、注文の量が増加し、よりカスタマイズされた注文に対応するためには、現在のシステムの改善が必要でした。
新しい生産システムの設計原則は何でしたか?
-新しい生産システムの設計原則は、紙レスで、新入社員のトレーニングが不要、果物や野菜の販売リストが変わることに対応できること、そして、新しい技術を導入するための大きなCAPEXコストがなくなるように、技術を選択することが重要でした。
Bonuが選んだ技術はどのようなものでしょうか?
-Bonuは、Go言語を使用したバックエンド技術、Reactを使用したアプリケーション開発、そしてIndustrial sensorsを使用しました。また、消費者向けのタブレットを使用し、産業用SENSORと接続することで、より柔軟で信頼性の高いシステムを実現しました。
新しい生産システムの利点は何ですか?
-新しい生産システムは、従業員が注文を準備する際に紙のリストを読む必要がなく、タブレット上での直感的なインターフェースを使用できるため、より迅速で正確な作業が可能になります。また、システムのカスタマイズ性や柔軟性が高まり、生産ラインの改善や新しいサービスの導入が容易になります。
新しい生産システムの導入に直面した課題は何でしたか?
-新しい生産システムの導入に直面した課題には、適切なセンサーの選定、APIの遅延、常にオンのスクリーンの管理などが含まれます。特に、センサーの選定では、高品質で安価な製品を見つけることが難しく、APIの遅延は画面の即時反映に影響を与え、スクリーンの管理ではMDMソフトウェアの複雑さとHTTPS接続の課題が必要に対応する必要がありました。
Bonuは今後どのような方向性を進める予定ですか?
-Bonuは、生産ラインで収集されたデータを活用し、マージンの計算や購入チームの選択肢の最適化などに役立てることを目指しています。また、システムの信頼性を向上させるために、センサーの交換を迅速に行えるようにし、アプリのバージョンアップを自動化することも計画されています。
Bonuのフルカスタマイズ可能な注文システムはどのようなものですか?
-Bonuのフルカスタマイズ可能な注文システムは、顧客が毎週提供される商品から自分の注文を完全にカスタマイズできるシステムです。顧客は木曜日に通知を受け取り、その中で注文をカスタマイズすることができます。そして、月曜日から注文が準備され、顧客に発送されます。
Bonuのサブスクリプションモデルの具体的な動作方法是どのようなですか?
-Bonuのサブスクリプションモデルでは、顧客は毎週の注文を準備し、選択した商品が毎週配送されます。顧客はサブスクリプションにコミットする必要はありません。毎週、顧客は受け取るバスケットを選択し、スキップすることも可能です。また、いつでもサブスクリプションを一時停止することができます。
Outlines
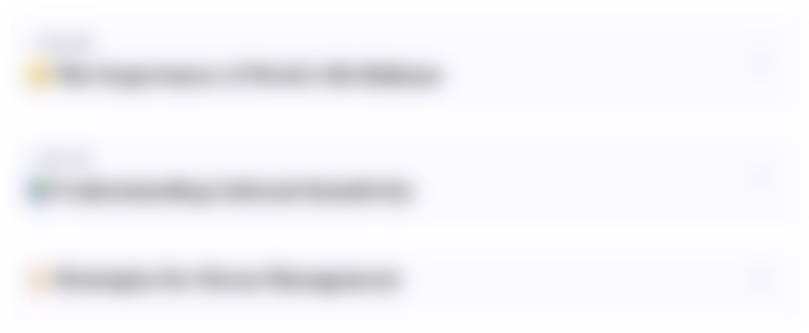
هذا القسم متوفر فقط للمشتركين. يرجى الترقية للوصول إلى هذه الميزة.
قم بالترقية الآنMindmap
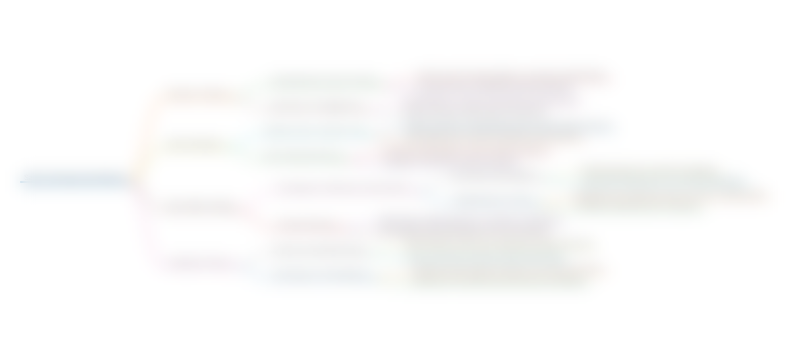
هذا القسم متوفر فقط للمشتركين. يرجى الترقية للوصول إلى هذه الميزة.
قم بالترقية الآنKeywords
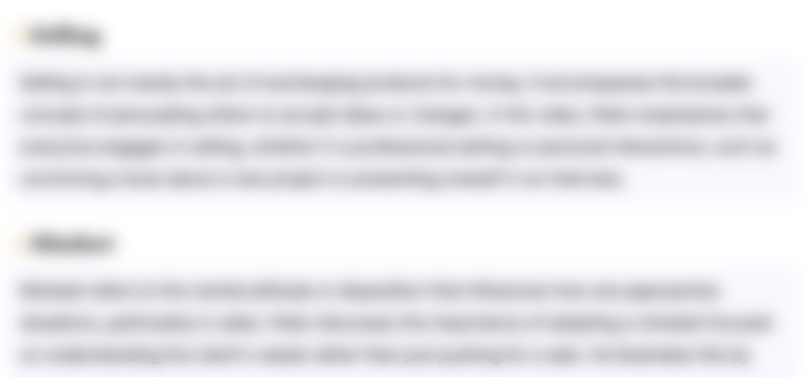
هذا القسم متوفر فقط للمشتركين. يرجى الترقية للوصول إلى هذه الميزة.
قم بالترقية الآنHighlights
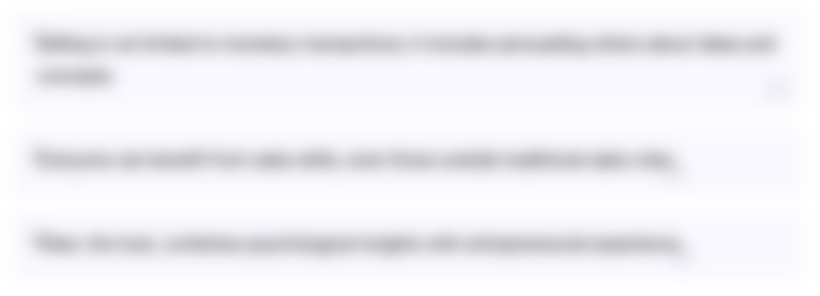
هذا القسم متوفر فقط للمشتركين. يرجى الترقية للوصول إلى هذه الميزة.
قم بالترقية الآنTranscripts
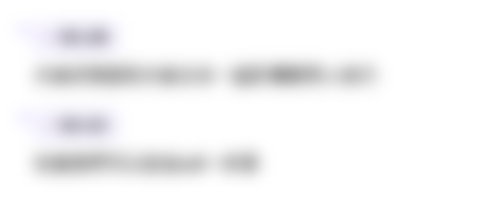
هذا القسم متوفر فقط للمشتركين. يرجى الترقية للوصول إلى هذه الميزة.
قم بالترقية الآن5.0 / 5 (0 votes)