Hydraulic Actuators & Motors - Hydraulics - Airframes & Aircraft Systems #9
Summary
TLDRThis lesson delves into hydraulic actuators, essential for converting hydraulic pressure into mechanical movement in aircraft systems. It distinguishes between single-acting actuators, which move in one direction via hydraulic pressure and rely on springs for the return, and double-acting actuators, which operate in both directions hydraulically. The latter are further categorized into unbalanced, where the piston rod's presence creates a force imbalance, and balanced, which apply equal force on both piston sides. The script also explores hydraulic motors, their construction akin to multi-piston pumps, and their operation dependent on oil flow rate, with applications ranging from flap drives to power transfer units.
Takeaways
- ⚙️ Hydraulic actuators are devices that convert hydraulic pressure into mechanical movement, and they come in various sizes and constructions to handle different operating loads.
- 🔧 Single-acting actuators operate hydraulically in one direction and use a spring to return, commonly used as locking devices like landing gear up-locks.
- 🔄 Double-acting unbalanced actuators are prevalent in aircraft systems, providing more force during extension due to the smaller area on the piston rod side.
- 🎯 Double-acting balanced actuators allow equal force application on both sides of the piston, often used in applications like nose wheel steering and flight control systems.
- 🔒 A hydraulic lock occurs when fluid is trapped between the actuator piston and a valve, locking the actuator in position due to the incompressible nature of the fluid.
- 🔌 Hydraulic motors are rotary actuators that can drive components like screw jacks for flap drives or operate auxiliary systems like generators and pumps.
- 🔄 The speed of a hydraulic motor is typically dependent on the flow rate of oil into it, with a fixed swashplate angle in most designs.
- 🛠️ Hydraulic motors can transfer power between hydraulic systems without fluid exchange, useful in scenarios like main pump failure in aircraft systems.
- 💧 Flow control valves maintain a constant flow of fluid to components, ensuring they operate at a consistent speed, crucial for systems like trailing edge flaps.
- 🔧 The construction of a hydraulic motor is similar to a multi-piston pump, with pressure used to rotate the pistons around a usually fixed swashplate.
Q & A
What is the primary function of hydraulic actuators?
-Hydraulic actuators are used to convert hydraulic pressure into mechanical movement, which can be either linear or rotary motion.
What are the main components of a hydraulic actuator?
-The main components of a hydraulic actuator include an outer cylinder, a piston and seal assembly, and a piston rod or ram that passes through a seal and wiper ring assembly.
What are the three types of actuators used in aircraft systems?
-The three types of actuators used in aircraft systems are single-acting, double-acting unbalanced, and double-acting balanced.
How does a single-acting actuator operate?
-A single-acting actuator is hydraulically operated in one direction only, with the force to move it in the other direction provided by a spring, typically used as a locking device.
What is the difference between double-acting unbalanced and double-acting balanced actuators?
-Double-acting unbalanced actuators have a smaller area on the side with the piston rod, allowing more force during extension than retraction. Double-acting balanced actuators can apply equal force to both sides of the piston, achieved by having rods attached to both phases of the piston.
Why are double-acting unbalanced actuators more commonly found in aircraft systems?
-Double-acting unbalanced actuators are more commonly found in aircraft systems because they can apply more force during extension, which is often the direction that offers greater resistance, such as raising the landing gear.
What is a hydraulic lock and how is it formed?
-A hydraulic lock is a state where the actuator is unable to move because fluid is trapped between the actuator piston and a valve, preventing any movement even when an external load is applied.
What is the role of a hydraulic motor in an aircraft system?
-Hydraulic motors are a form of rotary actuator that can be used to drive components such as generators, pumps, or screw jacks, and can also transfer power between hydraulic systems without exchanging fluid.
How does the construction of a hydraulic motor differ from that of a multi-piston pump?
-While a hydraulic motor is generally similar in construction to a multi-piston pump, the swashplate angle in a hydraulic motor is usually fixed, making its speed dependent on the flow rate of oil into it.
What is the purpose of a flow control valve in a hydraulic system?
-A flow control valve in a hydraulic system maintains a constant flow of fluid to a particular component, allowing it to operate at a constant speed, such as in a trailing edge flap system.
Outlines
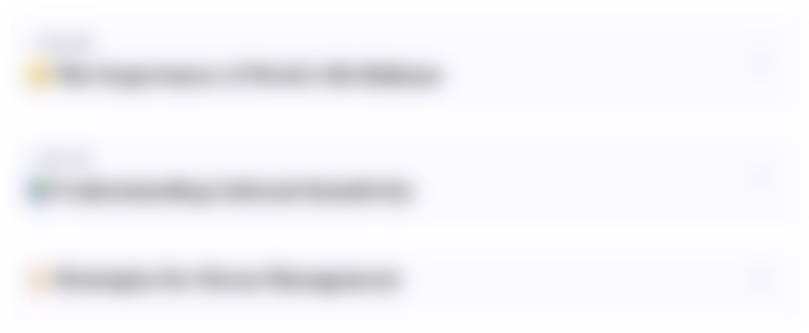
هذا القسم متوفر فقط للمشتركين. يرجى الترقية للوصول إلى هذه الميزة.
قم بالترقية الآنMindmap
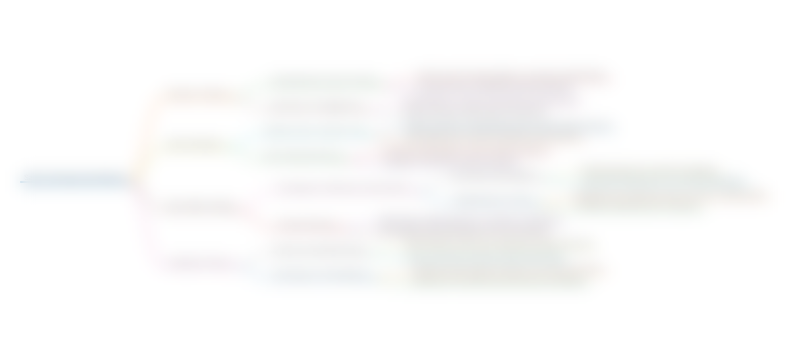
هذا القسم متوفر فقط للمشتركين. يرجى الترقية للوصول إلى هذه الميزة.
قم بالترقية الآنKeywords
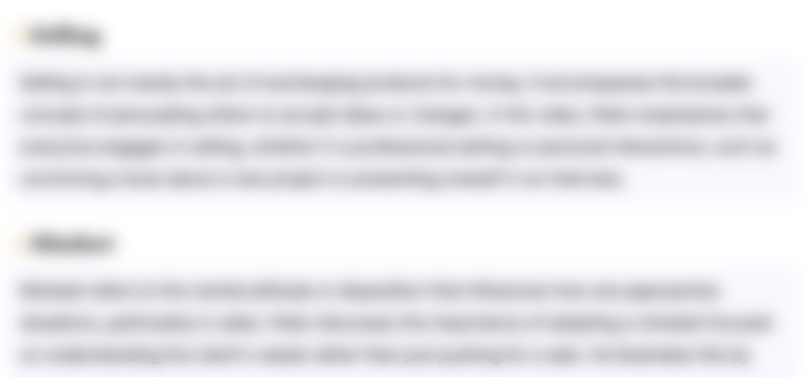
هذا القسم متوفر فقط للمشتركين. يرجى الترقية للوصول إلى هذه الميزة.
قم بالترقية الآنHighlights
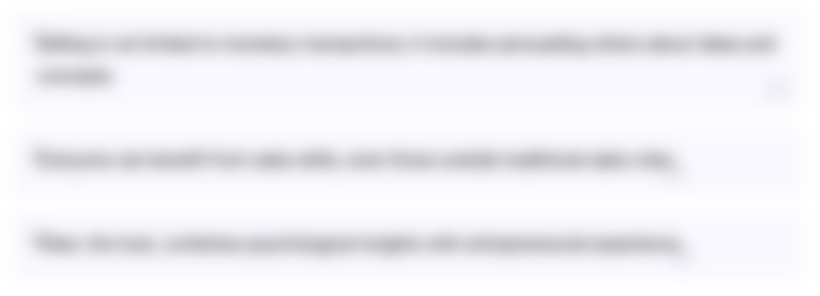
هذا القسم متوفر فقط للمشتركين. يرجى الترقية للوصول إلى هذه الميزة.
قم بالترقية الآنTranscripts
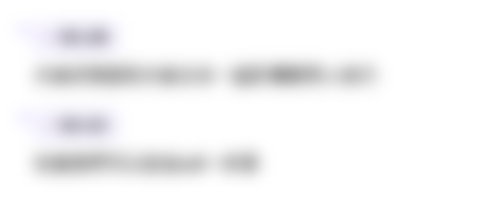
هذا القسم متوفر فقط للمشتركين. يرجى الترقية للوصول إلى هذه الميزة.
قم بالترقية الآنتصفح المزيد من مقاطع الفيديو ذات الصلة
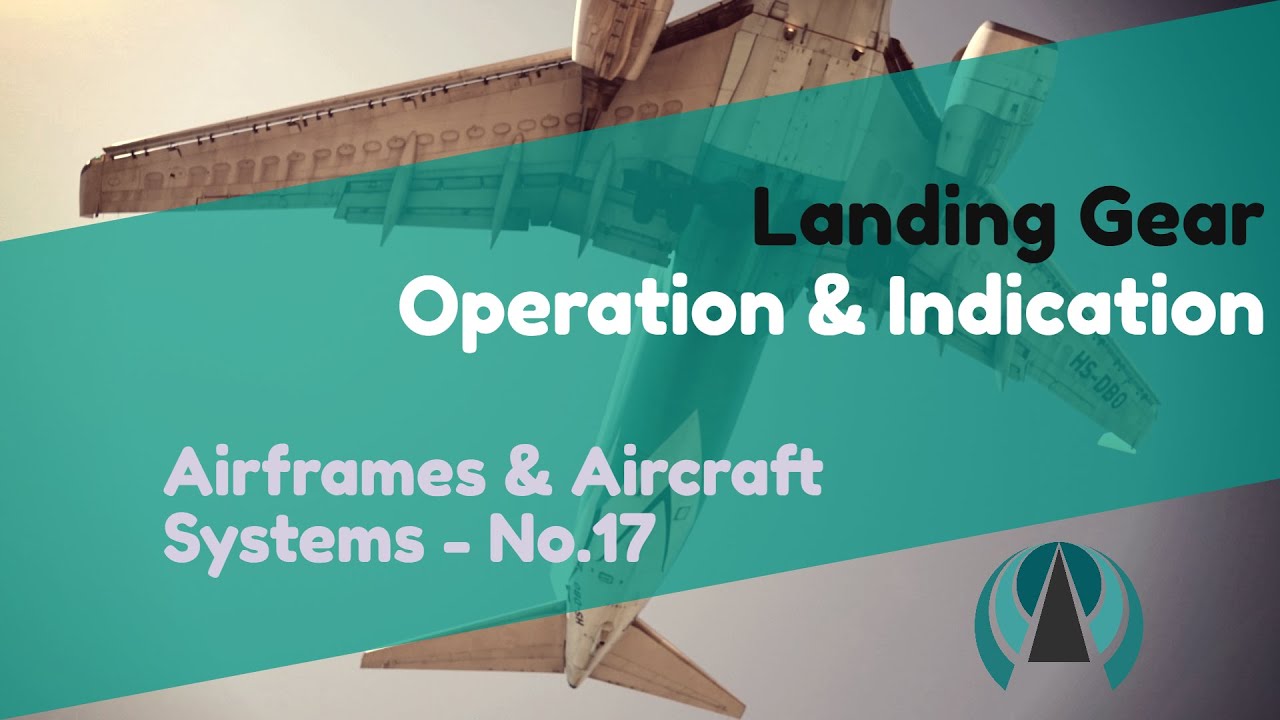
Operation & Indication - Landing Gear - Airframes & Aircraft Systems #17

HYDRAULIC ACTUATORS VICKERS HYDRAULIC TRAINING VEDIO BY MR PAUL COOK
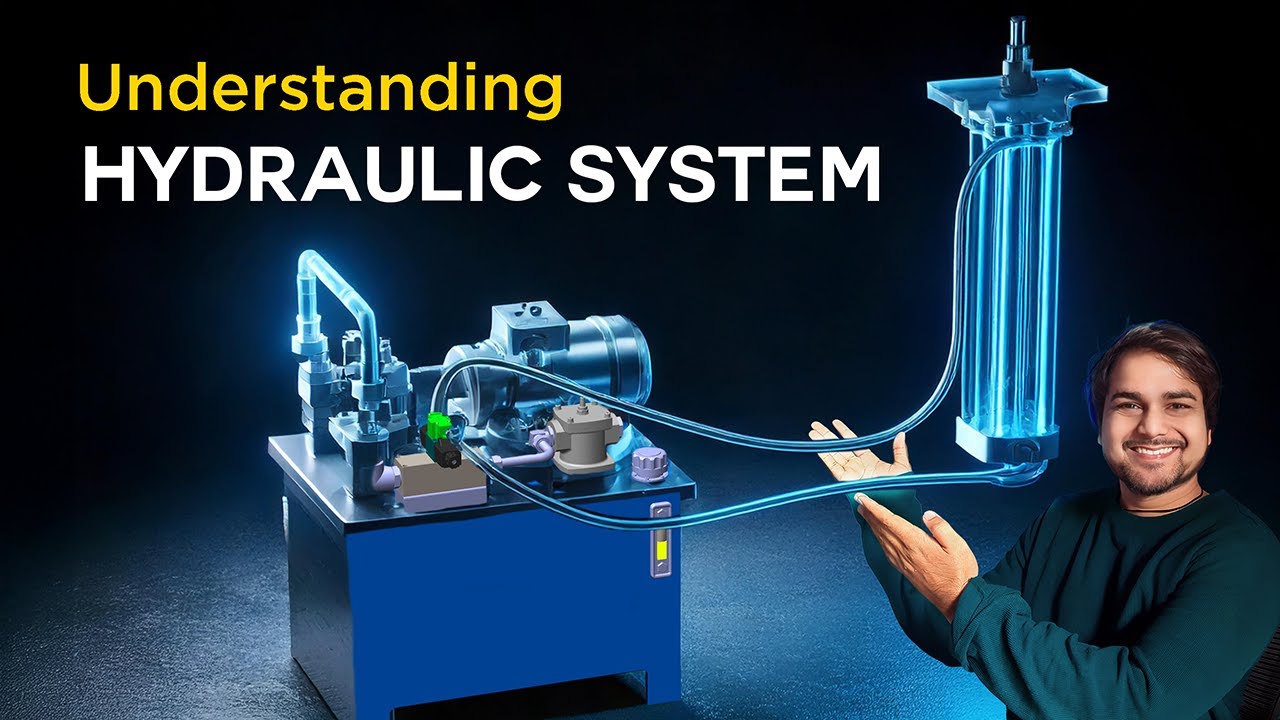
Hydraulic MasterClass: Essential Components, Working & Common Myths
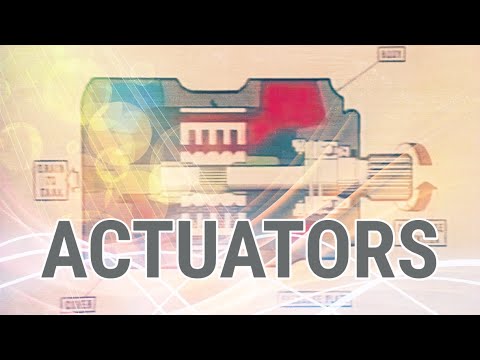
Hydraulic Training Series - Chapter 3 - Actuators
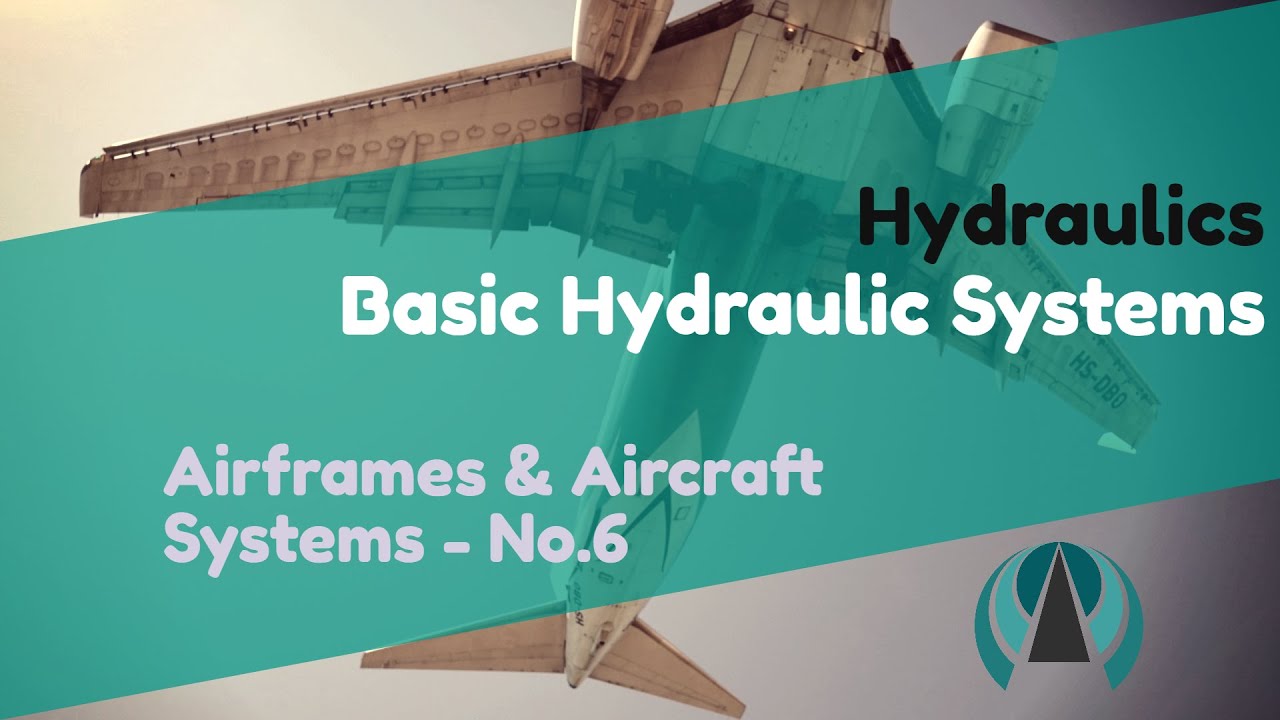
Basic Hydraulic Systems - Hydraulics - Airframes & Aircraft Systems #6
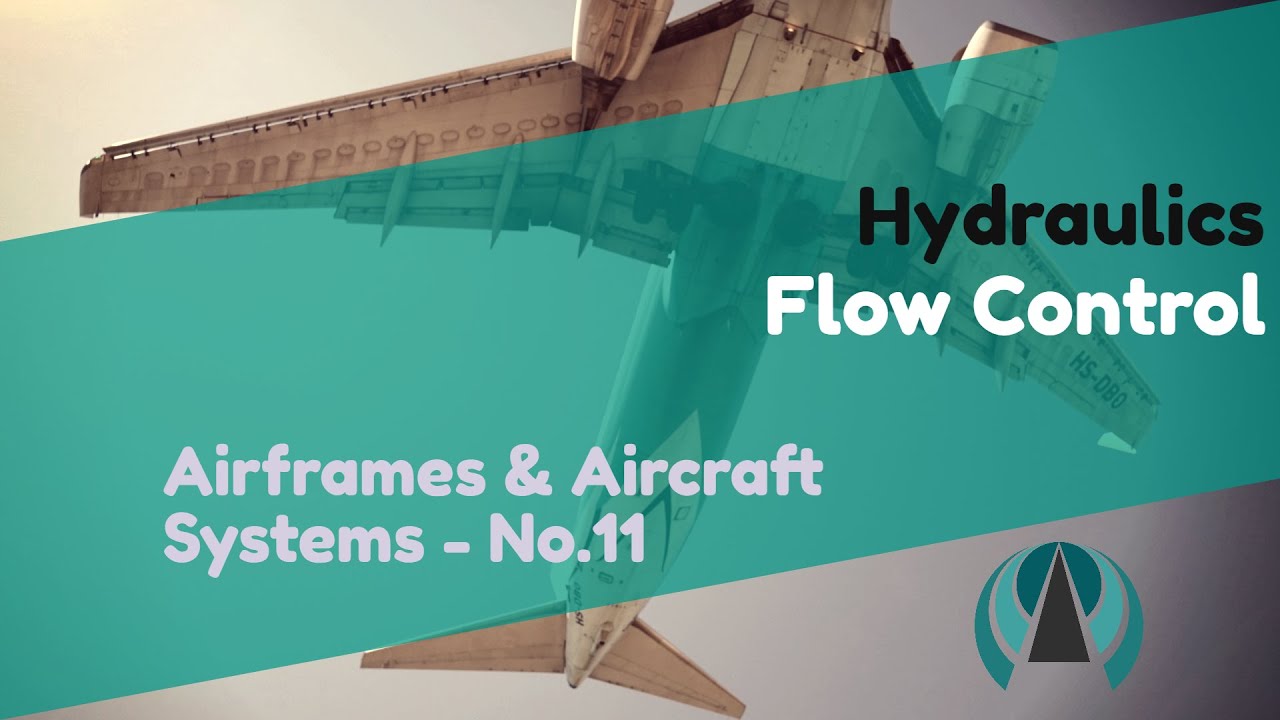
Flow Control - Hydraulics - Airframes & Aircraft Systems #11
5.0 / 5 (0 votes)