What is Kanban? Kanban Visual Systems Explained in 4 stages Easily.
Summary
TLDRThe video discusses the origins and mechanics of the Kanban system, a Japanese workflow management method introduced by Toyota. Inspired by American supermarket restocking practices, Kanban uses visual signals to manage inventory efficiently. The system is designed to streamline production by replenishing components based on actual demand, minimizing waste and ensuring high quality. The four stages of Kanban involve visual cues for replenishment, movement of materials, and just-in-time production, leading to reduced inventory, less storage space, and early defect detection.
Takeaways
- 🏭 Kanban originated from the Toyota Motor Company in Japan as an inventory control system inspired by American supermarkets' restocking methods.
- 📝 The term 'Kanban' means 'billboard' or 'signboard' in Japanese and is used to signal when action is required, such as replenishing components.
- 🔄 Kanban is a pull system, where production is triggered by customer demand rather than pushing products into the market based on forecasts.
- 👷♂️ The system involves four stages: component requisition, supply replenishment, production activation, and restocking the assembly line.
- 🔑 Each component has its own Kanban card that signals when it needs to be replenished, ensuring just-in-time inventory management.
- 🚶♂️ The process includes a supply worker, 'Mizosomashi,' who moves through the aisles to collect and deliver components based on Kanban signals.
- 📍 Kanban cards contain specific information such as component name, identification number, and storage location, facilitating precise inventory tracking.
- 🔄 The replenishment process is cyclical, with regular intervals for checking and restocking to maintain an efficient workflow.
- 🛠️ Small-batch production facilitated by Kanban allows for easier defect detection, contributing to higher component quality.
- 📉 The use of Kanban reduces inventory levels and storage space requirements, leading to cost savings and improved efficiency.
- 🌐 Kanban has expanded beyond manufacturing into various industries, including software development, as a method for visualizing and managing workflow.
Q & A
What does the term 'Kanban' mean in Japanese?
-Kanban is a Japanese word that translates to 'flag' or 'signal', and it is used as a visual aid to indicate that action is required.
Which company originally introduced the Kanban inventory control system?
-The Kanban inventory control system was originally introduced by the Toyota Motor Company in Japan.
What inspired Toyota's Vice President Taiichi Ohno to implement the Kanban system?
-Taiichi Ohno was inspired by the technique used by American supermarkets for replenishing empty shelves and racks, which used an empty shelf as a simple and visible trigger for restocking.
How does the Kanban system work in the context of Toyota's assembly lines?
-The Kanban system uses a trigger or card to alert the manufacturing area when the assembly area is running low on components, ensuring that each component has its own Kanban to signal when it needs to be replenished.
What is the definition of Kanban in the context of workflow management?
-Kanban is a workflow management method designed to help visualize work, maximize efficiency, and increase agility.
How does the Kanban system represent a change from traditional manufacturing practices?
-The Kanban system represents a pull system, where production is based on customer demand, as opposed to the standard push practice of producing goods in bulk and pushing them to the market.
What are the four stages of the Kanban system as explained in the script?
-The four stages are: 1) A worker needs components and takes them from the racks, removing the Kanban card. 2) A supply worker collects Kanban cards and empty bins, and moves them to the store racks. 3) The supply worker replenishes the bins at the assembly line racks. 4) A manufacturing cell worker produces components to fill the bins and returns them to the assembly line racks.
What is the purpose of the requisition Kanban card in the Kanban system?
-The requisition Kanban card contains information about the component, its identification number, and the location in the store, and it signals the need for replenishment of the component at the assembly line.
What is the role of the 'Mizusumashi' in the Kanban system?
-The Mizusumashi is a supply worker who moves through the aisles, collects hanging requisition Kanban cards and empty bins, and replenishes the bins at the assembly line racks according to the information on the cards.
What is the purpose of the production Kanban card in the Kanban system?
-The production Kanban card contains the name and identification number of the component to be manufactured, and it signals the manufacturing cells to produce the components in the exact quantities needed to fill the empty bins.
What are the benefits of using the Kanban system mentioned in the script?
-The benefits of using the Kanban system include reduced inventory, less storage space required, and higher quality of components due to the ease of detecting defects in small batch production.
Outlines
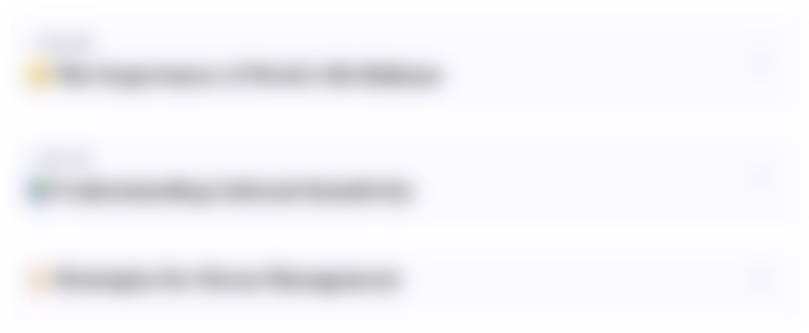
هذا القسم متوفر فقط للمشتركين. يرجى الترقية للوصول إلى هذه الميزة.
قم بالترقية الآنMindmap
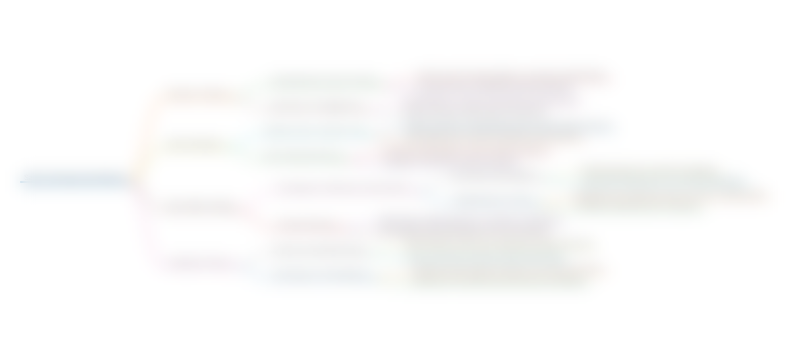
هذا القسم متوفر فقط للمشتركين. يرجى الترقية للوصول إلى هذه الميزة.
قم بالترقية الآنKeywords
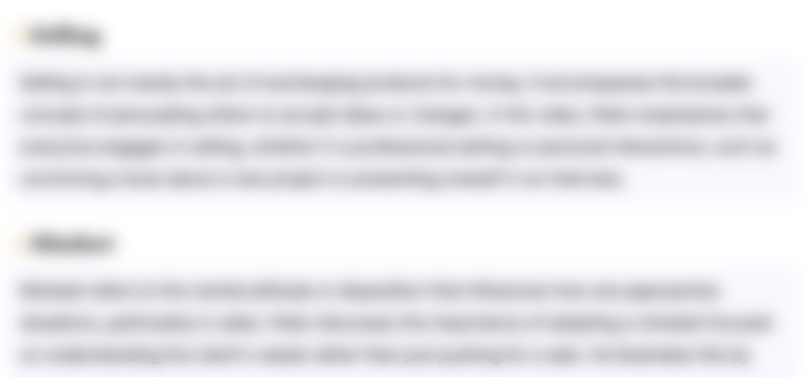
هذا القسم متوفر فقط للمشتركين. يرجى الترقية للوصول إلى هذه الميزة.
قم بالترقية الآنHighlights
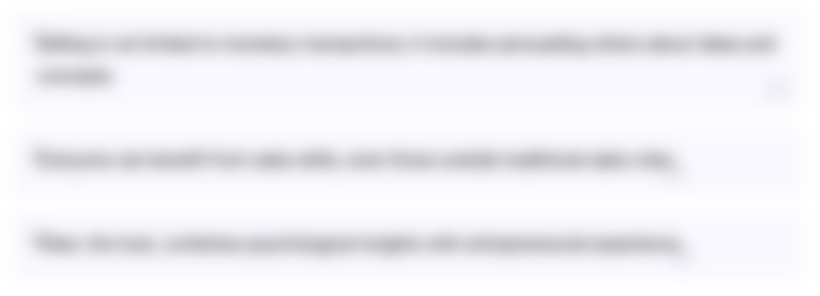
هذا القسم متوفر فقط للمشتركين. يرجى الترقية للوصول إلى هذه الميزة.
قم بالترقية الآنTranscripts
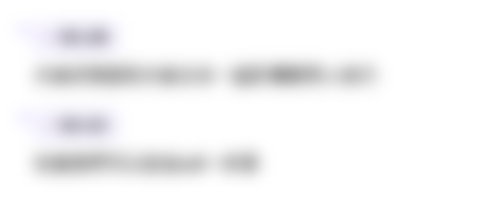
هذا القسم متوفر فقط للمشتركين. يرجى الترقية للوصول إلى هذه الميزة.
قم بالترقية الآنتصفح المزيد من مقاطع الفيديو ذات الصلة

O que é o Método Kanban - Introdução à Melhoria de Processos para Desenvolvimento de Software
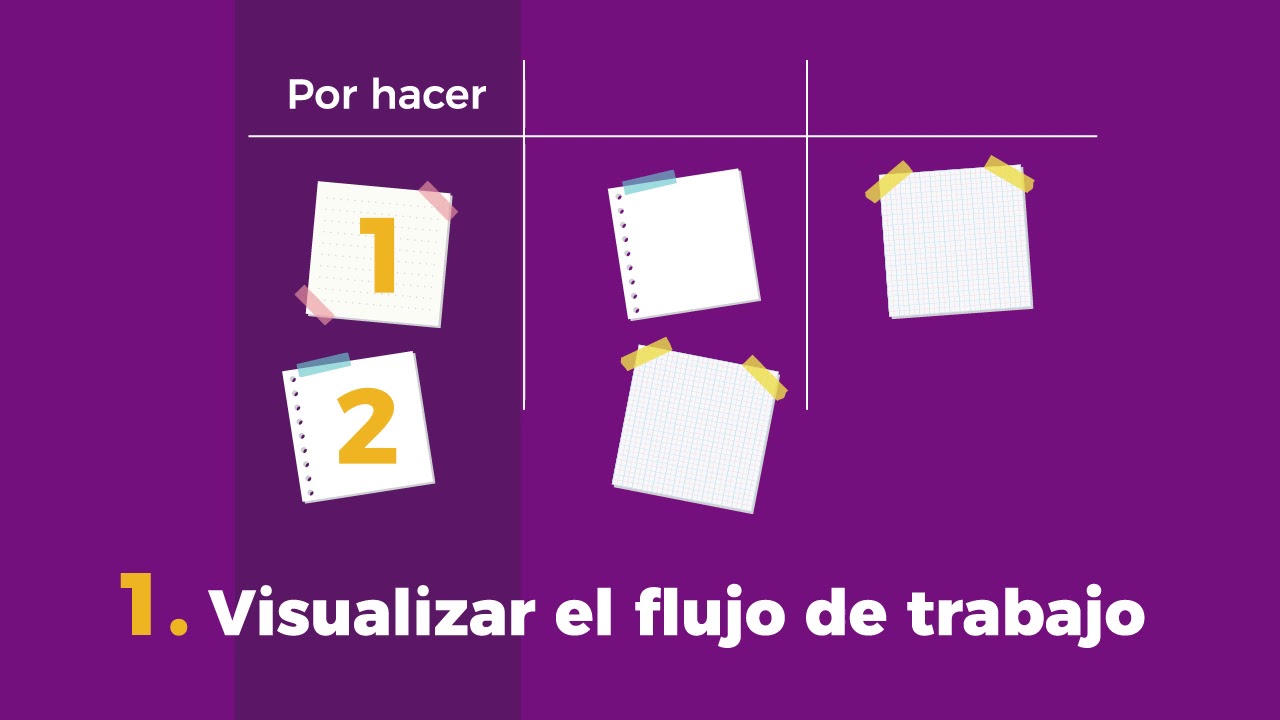
Metodología Kanban
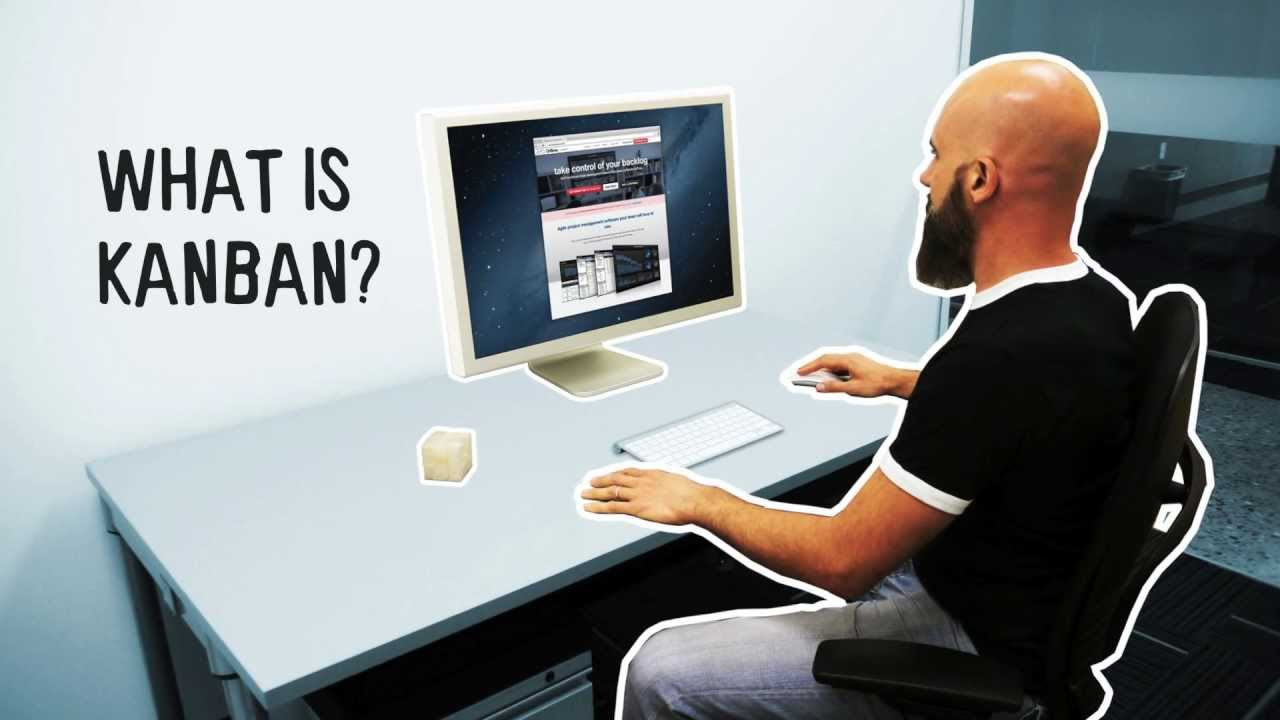
Intro to Kanban in Under 5 Minutes (What is Kanban, Learn Kanban)
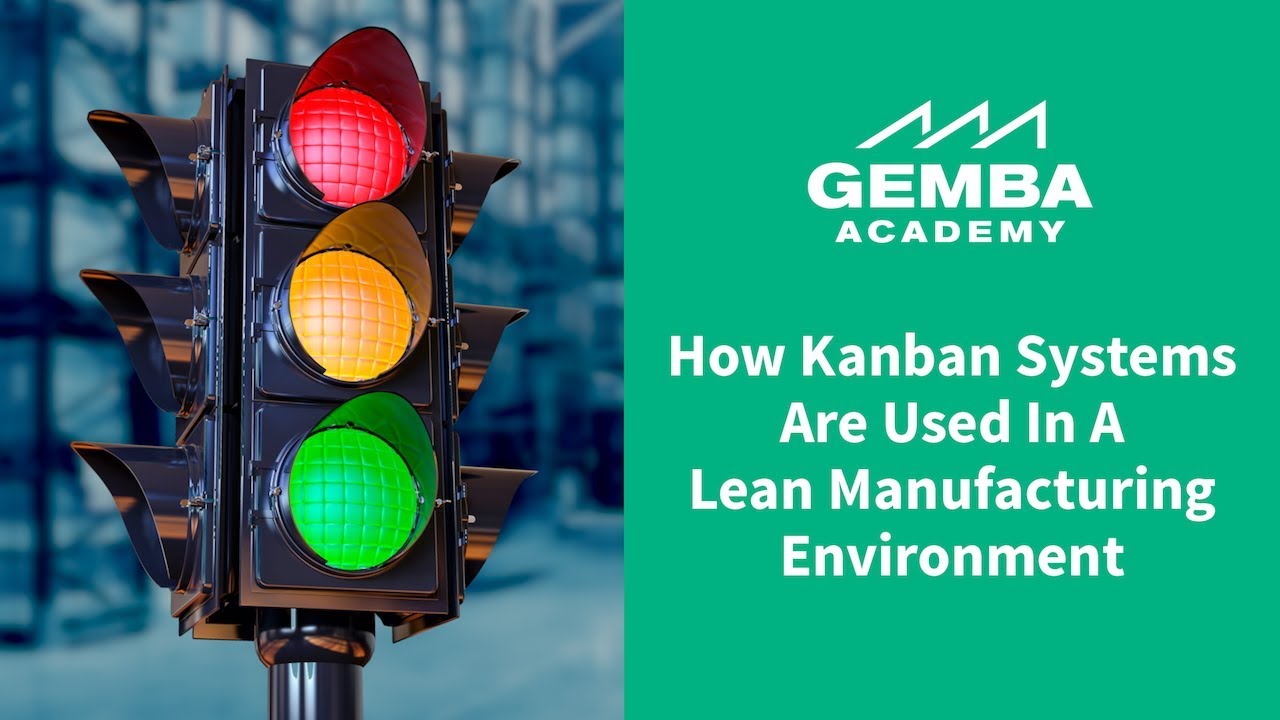
Learn How Kanban Systems are Used in a Lean Manufacturing Environment
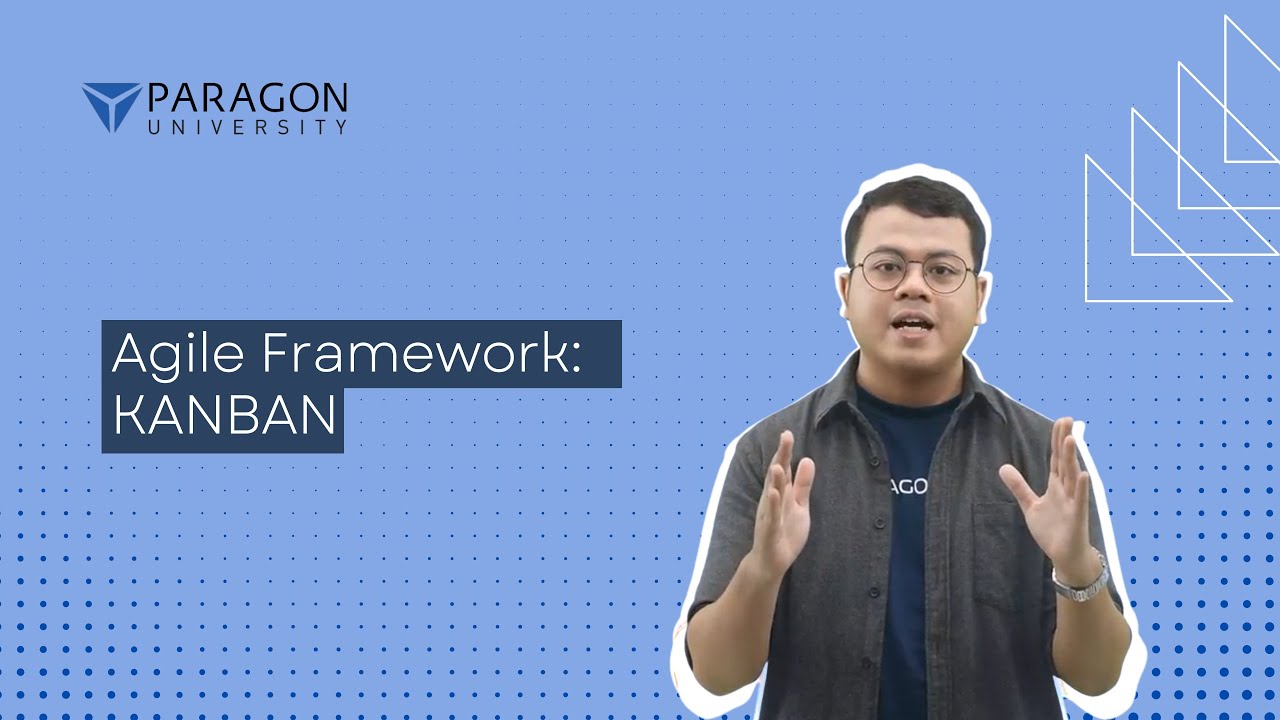
Project Management Part 10: Agile Framework - Kanban
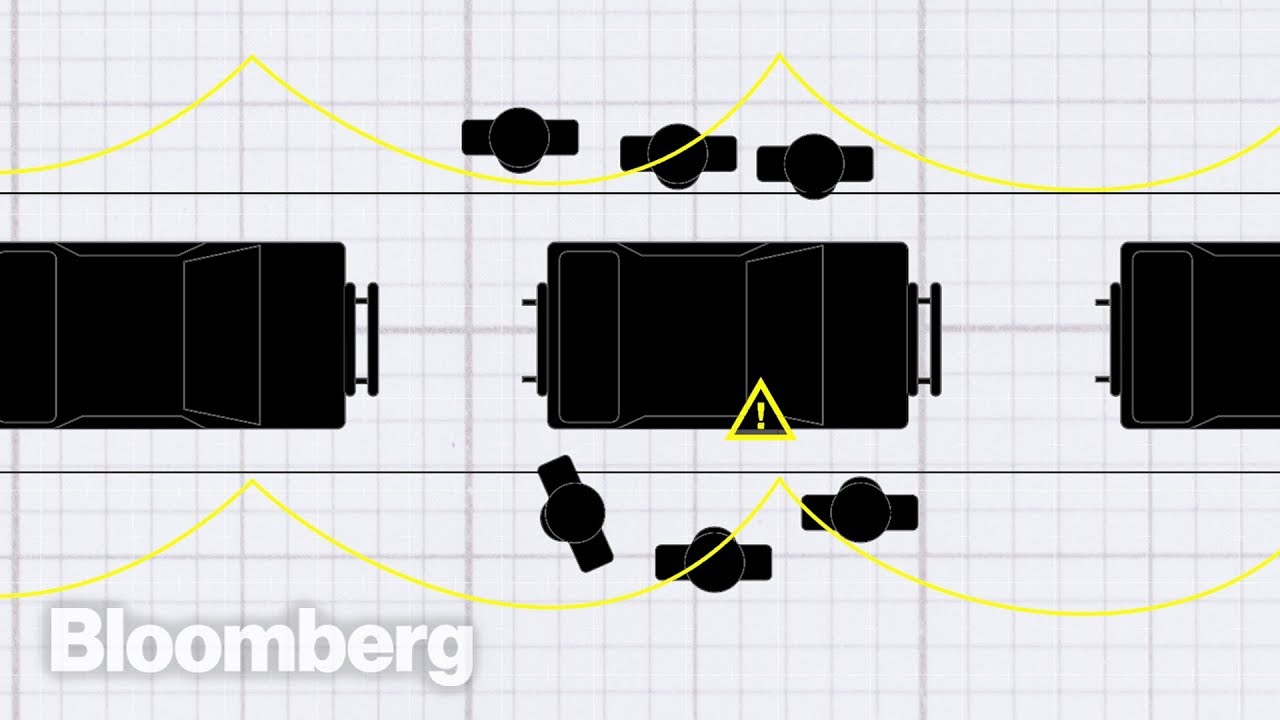
How Toyota Changed The Way We Make Things
5.0 / 5 (0 votes)