Design Capacity and Effective Capacity - Calculating Capacity Utilization and Efficiency Rate
Summary
TLDRThis video script explores the concepts of design and effective capacity, introducing capacity metrics such as utilization and efficiency rates. It uses a glass of water as a metaphor to explain the difference between design capacity (maximum potential) and effective capacity (real-world maximum). The script provides a detailed example of a production facility to illustrate how to calculate these capacities and their respective rates, emphasizing the importance of understanding and managing capacity for operational efficiency.
Takeaways
- 📏 **Design Capacity**: It's the maximum output a system or process is designed to achieve under perfect conditions.
- 🥤 **Actual Output**: Represents the real amount produced, which can be less than the design capacity due to various factors.
- 🔧 **Effective Capacity**: The maximum output achievable under current circumstances, considering factors like staff availability and equipment downtime.
- 💡 **Capacity Utilization**: A metric that shows how much of the total design capacity is being used, calculated by dividing actual output by design capacity.
- 🔄 **Efficiency Rate**: Indicates the efficiency of using the capacity, calculated by dividing actual output by effective capacity.
- 🚫 **Limitations of Design Capacity**: Effective capacity cannot exceed design capacity due to inherent system limitations.
- 🔄 **Adjustability of Effective Capacity**: It can be influenced by changing circumstances such as staff availability or machine maintenance.
- ⏱️ **Impact of Downtime**: Scheduled maintenance or employee absence can reduce effective capacity and overall production.
- 📈 **Importance of Capacity Metrics**: Understanding design and effective capacity, along with utilization and efficiency rates, is crucial for operational planning and improvement.
- 🛠️ **Strategic Planning**: Having a clear understanding of capacity metrics allows for better strategic planning, especially in response to demand fluctuations.
- 🔍 **Monitoring and Optimization**: Regularly monitoring capacity utilization and efficiency rates can help identify areas for process optimization and cost reduction.
Q & A
What is the definition of design capacity?
-Design capacity refers to the maximum amount that a system or process is designed to achieve under ideal conditions, without considering any real-world constraints.
Can you provide an example to illustrate design capacity?
-Sure, a glass designed to hold 12 ounces of liquid has a design capacity of 12 ounces, which is the maximum it can hold without spilling.
What is actual output in the context of capacity?
-Actual output is the amount that is being used or produced in reality, which can be less than the design capacity due to various factors.
How is effective capacity different from design capacity?
-Effective capacity is the maximum amount that can be produced under a given set of circumstances, considering real-world factors like employee availability, equipment downtime, and other constraints, whereas design capacity is an ideal maximum without considering such factors.
Can effective capacity ever exceed design capacity?
-No, effective capacity cannot exceed design capacity because it is limited by the design's maximum capacity and influenced by practical conditions.
What factors can affect the effective capacity of a production process?
-Factors such as the number of employees, downtime of production and equipment changeovers, and other operational constraints can affect the effective capacity.
How is capacity utilization calculated?
-Capacity utilization is calculated by dividing the actual output by the design capacity. It represents the percentage of capacity that is being used.
What does a high capacity utilization rate indicate about a production process?
-A high capacity utilization rate indicates that a production process is efficiently using its capacity, but it also suggests that there may be limited room for increased production without expanding capacity.
How is efficiency rate different from capacity utilization?
-The efficiency rate is calculated by dividing the actual output by the effective capacity, showing how well the production process is using its capacity under current conditions, whereas capacity utilization compares actual output to design capacity.
What does an efficiency rate of 88% mean for a production process?
-An efficiency rate of 88% means that the production process is using 88% of its effective capacity, indicating a high level of efficiency in production.
Why is it important to have some unused capacity in a production process?
-Having some unused capacity is important as it provides flexibility to handle increases in demand without needing immediate expansion or drastic measures, and it can also accommodate unexpected downtimes or fluctuations in production.
Outlines
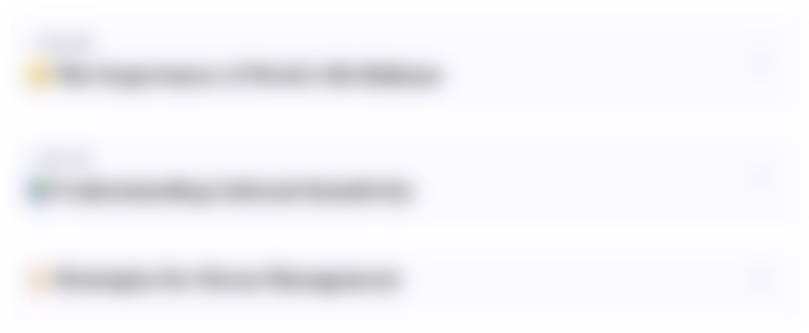
此内容仅限付费用户访问。 请升级后访问。
立即升级Mindmap
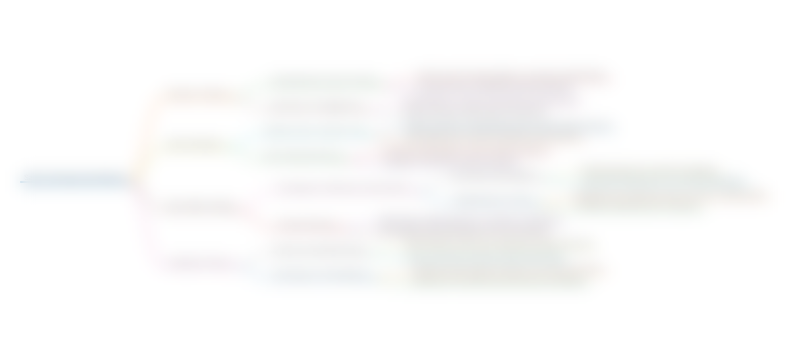
此内容仅限付费用户访问。 请升级后访问。
立即升级Keywords
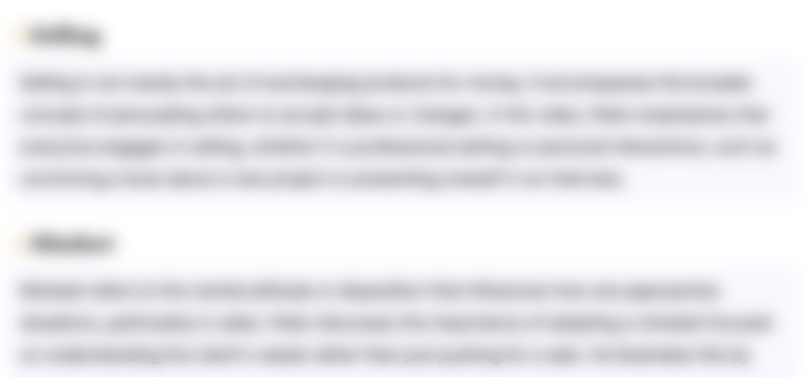
此内容仅限付费用户访问。 请升级后访问。
立即升级Highlights
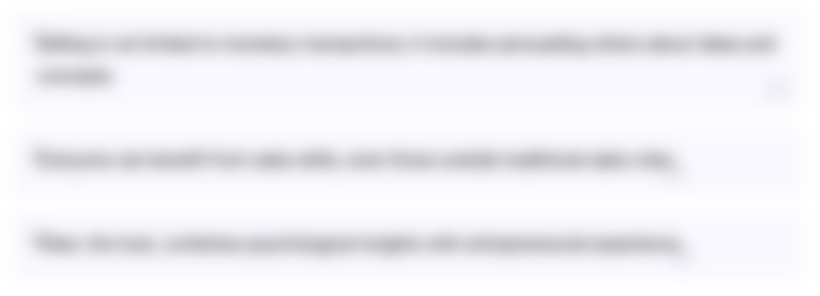
此内容仅限付费用户访问。 请升级后访问。
立即升级Transcripts
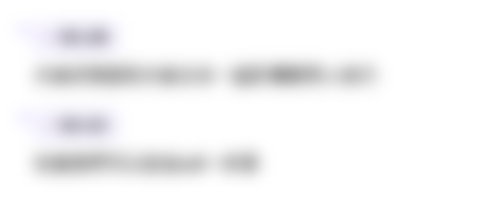
此内容仅限付费用户访问。 请升级后访问。
立即升级浏览更多相关视频
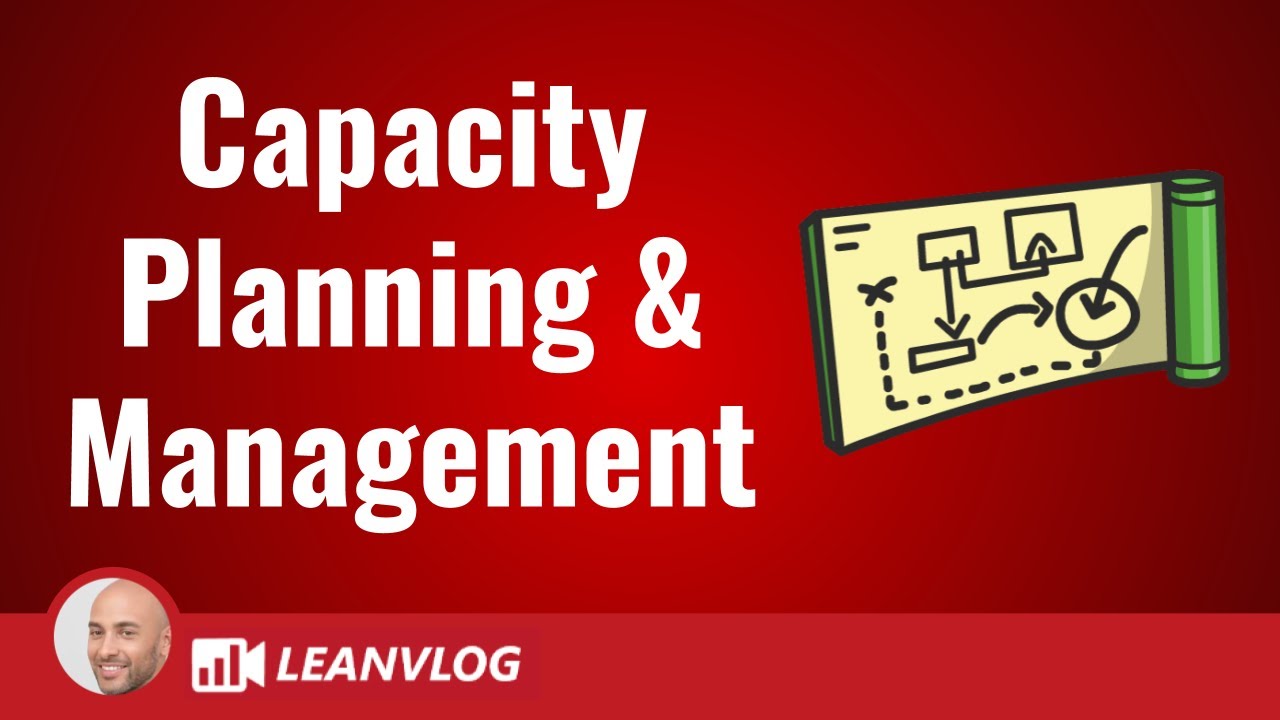
Capacity Planning - Overview and Key Concepts

Liane Okdinawati: Strategic Capacity (Part 2)

Capacity and Capacity Utilisation

MATERI KULIAH MANAJEMEN OPERASIONAL - PERENCANAAN KAPASITAS
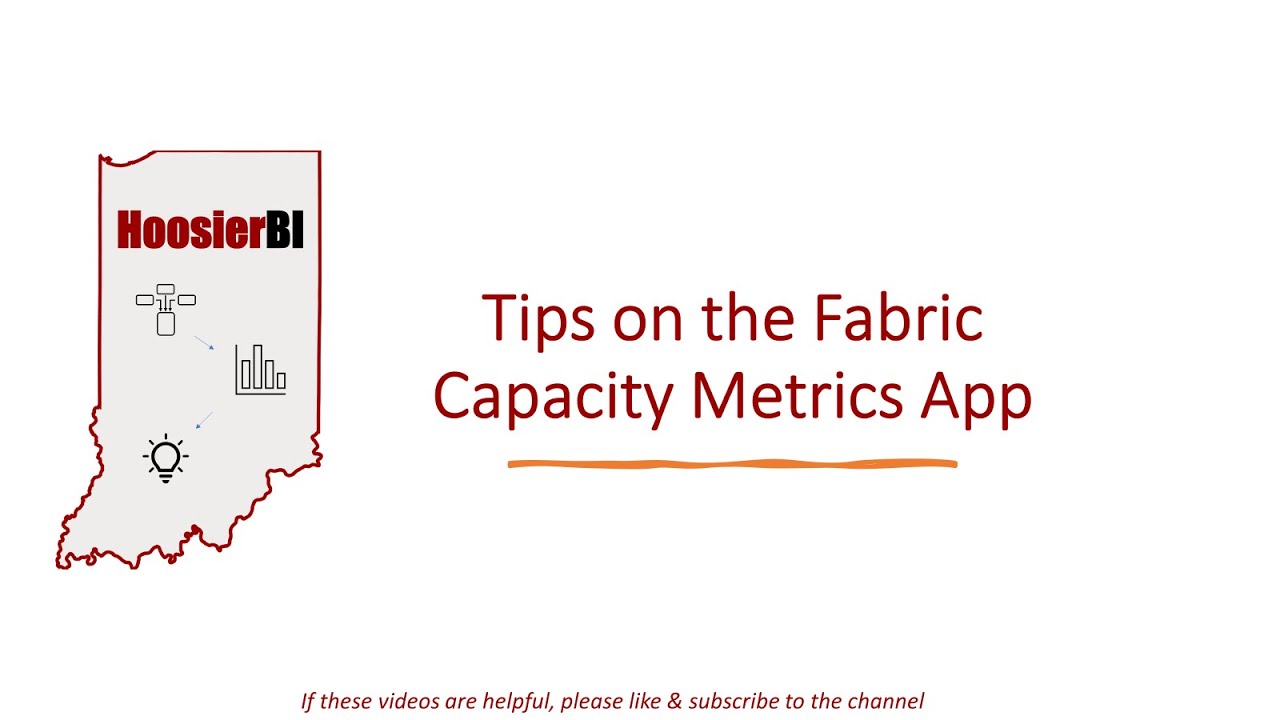
Tips on Using the Fabric Capacity Metrics App
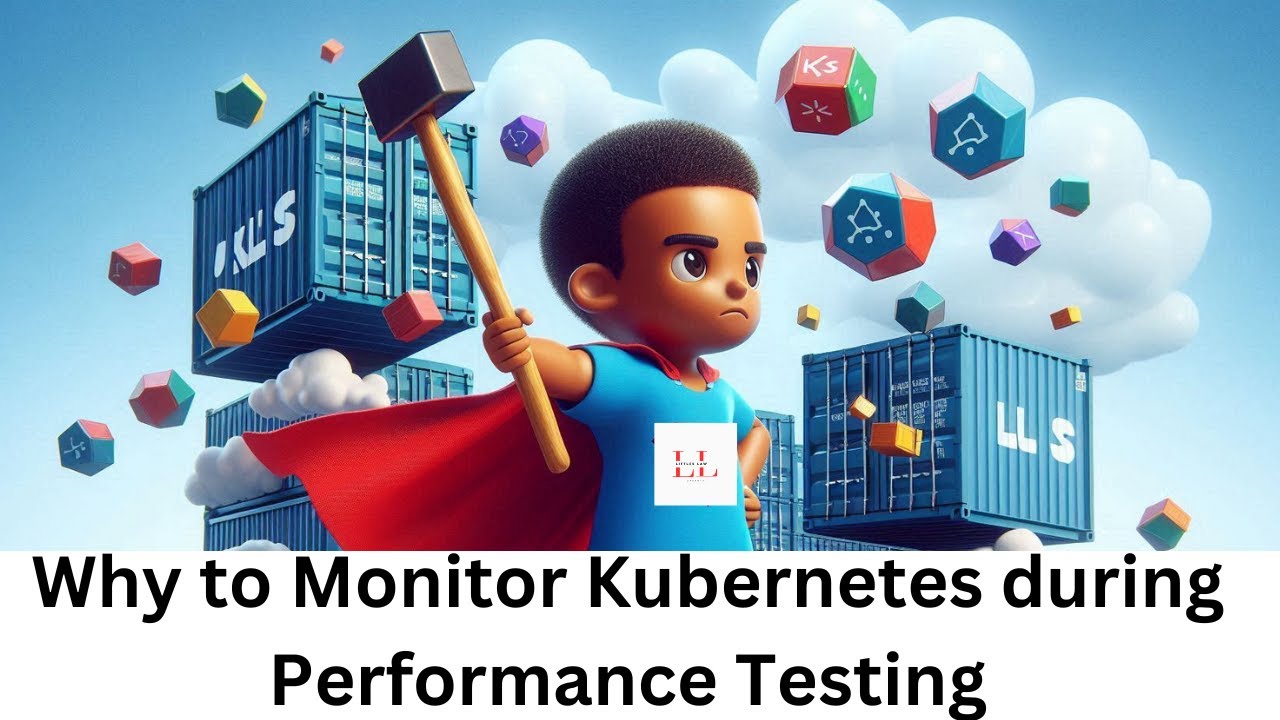
Why should I monitor Kubernetes during Performance testing #kubernetes #performanceengineering
5.0 / 5 (0 votes)