Understanding Plane Stress
Summary
TLDRThis video script delves into the concept of plane stress in solid mechanics, a simplification technique for three-dimensional problems. It explains that plane stress occurs when all acting stresses are confined to one plane, making it particularly useful for analyzing thin components. The script illustrates how to determine if a structure can be modeled under plane stress assumptions, using examples like a perforated plate, pressure vessels, and gear teeth. It highlights the reduction of stress components from six to three, simplifying the problem to a 2D matrix, and emphasizes the need for engineering judgment in applying this assumption.
Takeaways
- 📚 Analyzing 3D solid mechanics problems can be complex, but simplifications like plane stress can make them more manageable.
- 🔍 Plane stress is applicable when all acting stresses are confined to a single plane, which is common in thin components.
- 🎯 The condition for plane stress requires that all stresses in the Z direction are close to zero, often due to the thinness of the component.
- 🔧 To apply plane stress assumptions, it's necessary to ensure that loads are applied in the same plane and that the component's thickness is minimal.
- 🌐 Normal and shear stresses at a free surface are always zero, which supports the assumption of zero stress in the Z direction for thin plates.
- 🔑 The plane stress assumption reduces a 3x3 stress tensor matrix to a 2x2 matrix, simplifying the problem to two dimensions.
- 🛠️ Plane stress is particularly useful for analyzing thin structures under single-plane loading, such as perforated plates.
- 🔬 Engineering judgment is required to decide the applicability of plane stress conditions, as stresses in the Z direction are unlikely to be exactly zero.
- 👷♂️ Examples of structures that can be modeled using plane stress assumptions include pressure vessels and the teeth of spur gears, under certain conditions.
- 📉 The reduction in stress components from six to three simplifies the analysis, making it easier to solve engineering problems.
- 🔄 Plane stress is a valuable simplification for turning complex 3D solid mechanics problems into simpler 2D problems for easier analysis.
Q & A
What is the main challenge in analyzing solid mechanics problems in three dimensions?
-Analyzing solid mechanics problems in three dimensions can be challenging due to the complexity and the multitude of variables involved, which makes it difficult to solve.
What are the two main simplifications used in solid mechanics to reduce a three-dimensional problem to a two-dimensional one?
-The two main simplifications are plane stress and plane strain conditions, which are frequently used to simplify the analysis of solid mechanics problems.
What does it mean for a component to be in a condition of plane stress?
-A component is in a condition of plane stress when all the stresses acting on it are confined to the same plane.
Why is the plane stress condition most relevant for the analysis of thin components?
-Plane stress is most relevant for thin components because the thickness of the component allows for the assumption that stresses in the out-of-plane direction are negligible.
How can we determine if a perforated plate can be modeled using plane stress assumptions?
-To determine if a perforated plate can be modeled using plane stress, we need to check if all loads are applied in the same plane and if the plate is thin enough to assume that stresses in the out-of-plane direction are close to zero.
What is the significance of the thickness of a plate in the context of plane stress?
-The thickness of a plate is significant because it affects the variation of stress through the plate's thickness. A very thin plate is more likely to have negligible stress variation in the thickness direction, supporting the plane stress assumption.
Why are normal and shear stresses at a free surface always zero?
-Normal and shear stresses at a free surface are always zero because there is no material beyond the surface to exert forces on it, thus no stress can be transmitted across the boundary.
How does the plane stress assumption simplify the analysis of a stress element?
-The plane stress assumption simplifies the analysis by reducing the number of stress components acting at a point from six to three, making it a two-dimensional problem that is easier to solve.
What is the difference between the stress tensor of a three-dimensional case and that of a plane stress condition?
-The stress tensor for a three-dimensional case is a 3x3 matrix, whereas for plane stress conditions, it is reduced to a 2x2 matrix, simplifying the calculations.
Can you provide examples of situations where plane stress conditions might be assumed?
-Examples include modeling thin pressure vessels where hoop and axial stresses are predominant, and the teeth of a narrow spur gear where the width is small enough to assume negligible radial stresses.
What is the key takeaway from the video regarding the application of plane stress in engineering problems?
-The key takeaway is that plane stress is a useful simplification for turning complex three-dimensional solid mechanics problems into simpler two-dimensional ones for thin structures loaded in a single plane, although it requires engineering judgment to decide its applicability.
Outlines
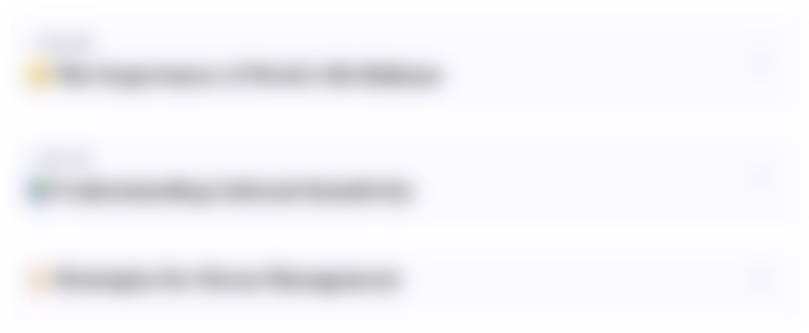
此内容仅限付费用户访问。 请升级后访问。
立即升级Mindmap
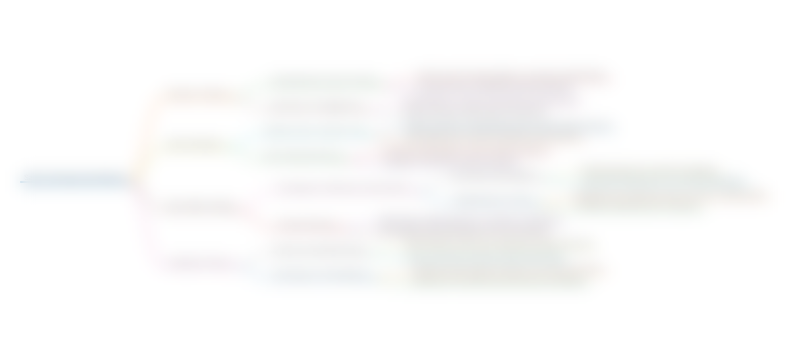
此内容仅限付费用户访问。 请升级后访问。
立即升级Keywords
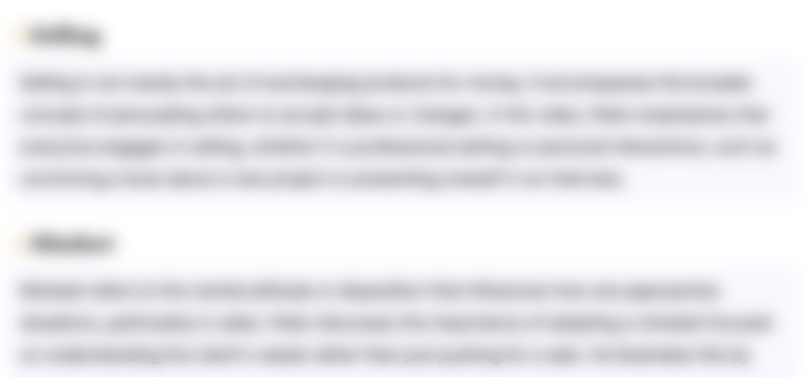
此内容仅限付费用户访问。 请升级后访问。
立即升级Highlights
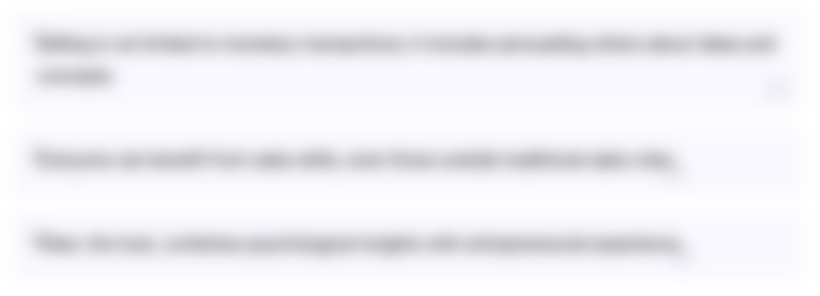
此内容仅限付费用户访问。 请升级后访问。
立即升级Transcripts
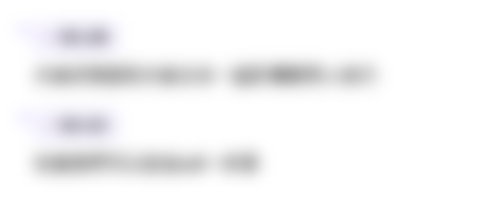
此内容仅限付费用户访问。 请升级后访问。
立即升级5.0 / 5 (0 votes)