How does Buck Converter work? | DC-DC Converter - 1
Summary
TLDRThis video script delves into the workings of a Buck converter, a device that efficiently steps down DC voltage levels. It explains the use of a PWM signal to control a MOSFET, the role of an inductor and capacitor in stabilizing voltage, and the importance of feedback for load adjustments. The script also covers the generation of the PWM signal through an op-amp and comparator, and the use of P-channel MOSFETs for efficient voltage regulation. The summary highlights the closed-loop operation of the Buck converter, emphasizing its ability to maintain a consistent output voltage despite varying loads.
Takeaways
- 🔌 A buck converter is used to step down DC voltage efficiently.
- 🕒 The operation of a buck converter is based on the concept of Pulse Width Modulation (PWM) and duty cycle.
- 🔄 The average voltage output is determined by the duty cycle of the PWM signal, which can be adjusted to reduce voltage.
- 🛠️ An electrical switch, such as a MOSFET, is used in place of a simple mechanical switch for better control and efficiency.
- 🧲 An inductor is added to the circuit to smooth out the voltage spikes and maintain constant current flow.
- 🔁 The inductor opposes changes in current flow, helping to stabilize the voltage after the switch opens.
- 💡 A Schottky diode is included to provide a path for electrons when the switch is open, preventing damage from high negative voltage.
- ⚡ High-frequency PWM signals are used to minimize voltage and current instability caused by the inductor.
- 🔋 A capacitor is used in parallel to further smooth the output voltage by storing and releasing energy as needed.
- 🔄 Feedback mechanisms are crucial for adjusting the PWM signal in response to load changes, ensuring a stable output voltage.
- ⚙️ The complete buck converter circuit includes an op-amp for error amplification, a comparator for PWM signal generation, and a P-channel MOSFET for efficient switching.
Q & A
What is the purpose of a buck converter?
-A buck converter is used to step down DC voltage efficiently, converting a higher input voltage to a lower output voltage as required by the load.
How does a PWM signal relate to the operation of a buck converter?
-A Pulse Width Modulation (PWM) signal controls the switching of the MOSFET in a buck converter. The duty cycle of the PWM signal determines the average voltage output, which in turn steps down the input DC voltage.
What is the role of an inductor in a buck converter?
-The inductor in a buck converter helps to maintain a constant current flow by changing the voltage across itself. It also stores energy in its magnetic field during the switch-on phase and releases it during the switch-off phase, smoothing out the output voltage.
Why is a Schottky diode used in a buck converter?
-A Schottky diode is used to provide a path for the electrons when the inductor tries to maintain the current flow as the switch opens, preventing high voltage spikes that could damage the components.
What is the function of a capacitor in the buck converter circuit?
-A capacitor in a buck converter circuit is used to smooth out the output voltage by changing the current through it. It stores energy in its electric fields during the switch-on phase and supplies current when the switch is off, helping to maintain a stable output voltage.
How does the feedback mechanism in a buck converter work?
-The feedback mechanism in a buck converter adjusts the duty cycle of the PWM signal based on the voltage across the load. It uses a voltage divider to reduce the output voltage and feed it into an operational amplifier (op-amp), which compares it with a reference voltage and adjusts the PWM signal accordingly.
What is the significance of the duty cycle in a PWM signal?
-The duty cycle of a PWM signal is the proportion of time the signal is in the active (on) state during one period. It directly affects the average voltage output in a buck converter, with a higher duty cycle resulting in a higher average output voltage.
Why is a P-channel MOSFET used instead of an N-channel MOSFET in a buck converter?
-A P-channel MOSFET is used because it turns on when the gate voltage is below the source voltage, which is suitable for the buck converter's design where the gate voltage needs to be lower than the source voltage to turn on the MOSFET.
How does the operational amplifier (op-amp) function in the buck converter's feedback loop?
-The op-amp in the buck converter's feedback loop acts as an error amplifier, amplifying the difference between the input voltage (which is a fraction of the output voltage) and a reference voltage. It adjusts its output to minimize this difference, effectively controlling the duty cycle of the PWM signal.
What is the purpose of the triangle wave generator in the buck converter circuit?
-The triangle wave generator provides a varying voltage input to the comparator in the buck converter circuit. It interacts with the error amplifier's output to generate the PWM signal, with the comparator outputting a high voltage when the triangle wave is higher than the error amplifier's output and a low voltage otherwise.
How can the output voltage of a buck converter be adjusted?
-The output voltage of a buck converter can be adjusted by changing the value of the feedback resistors in the voltage divider or by using a potentiometer to alter the feedback voltage. This change in feedback affects the error amplifier's output and, consequently, the PWM signal's duty cycle.
Outlines
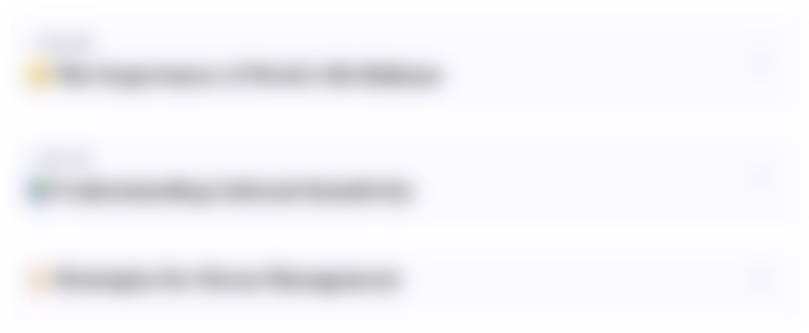
此内容仅限付费用户访问。 请升级后访问。
立即升级Mindmap
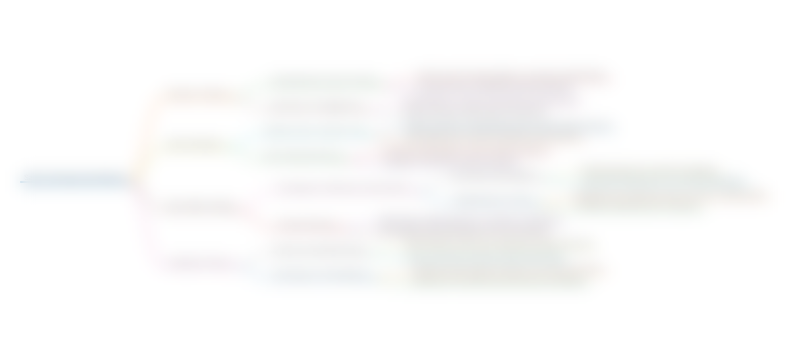
此内容仅限付费用户访问。 请升级后访问。
立即升级Keywords
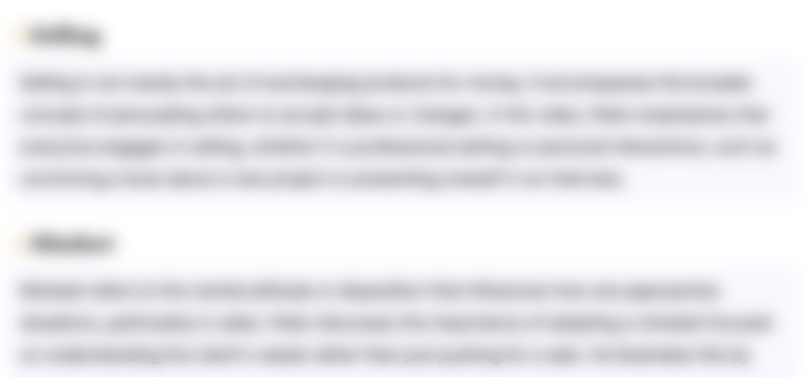
此内容仅限付费用户访问。 请升级后访问。
立即升级Highlights
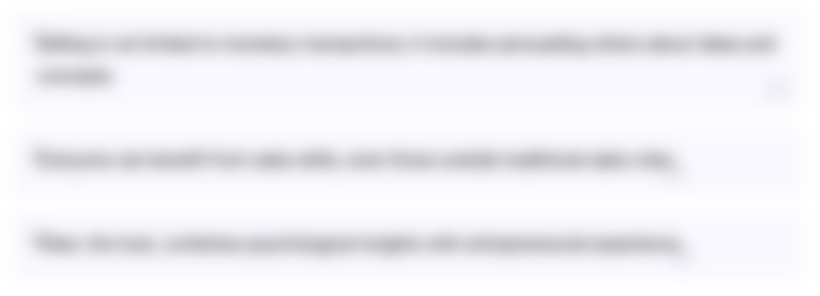
此内容仅限付费用户访问。 请升级后访问。
立即升级Transcripts
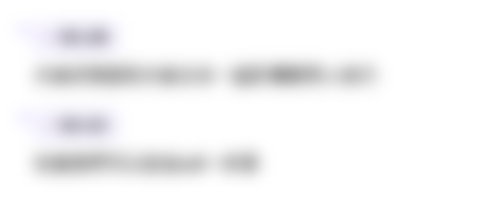
此内容仅限付费用户访问。 请升级后访问。
立即升级浏览更多相关视频
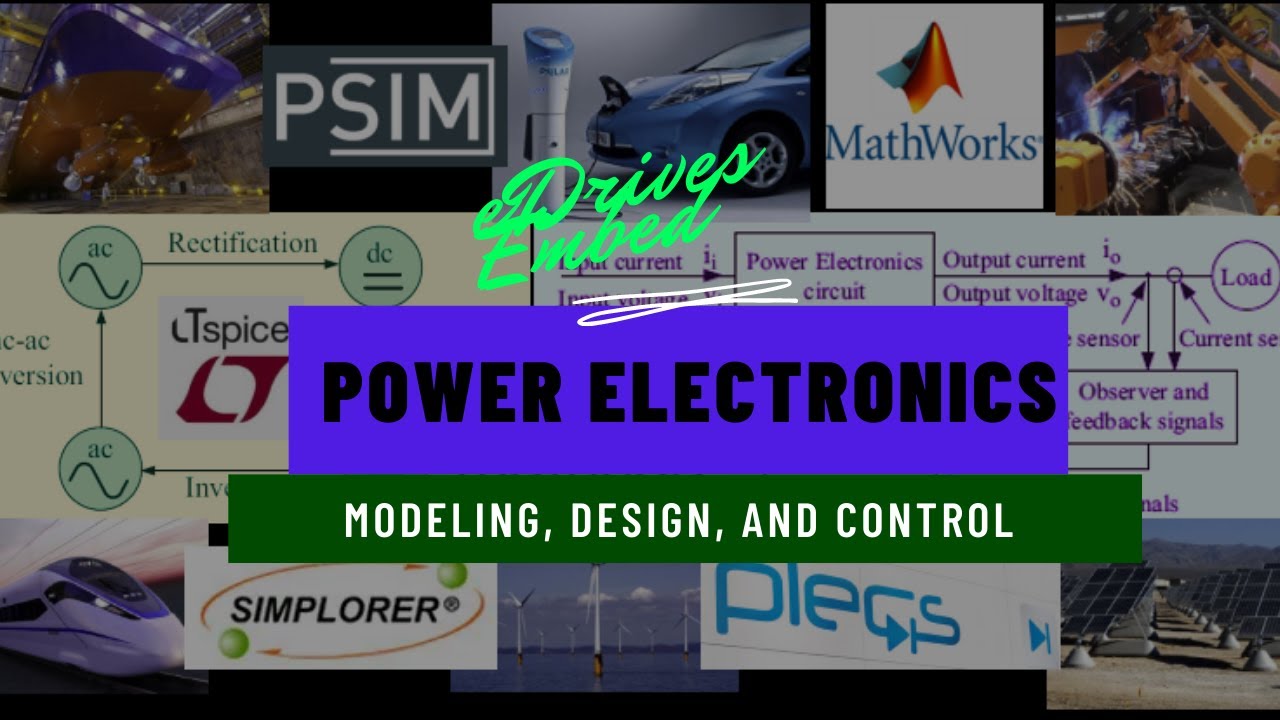
entrance into the DC DC Converter Basic Topologies

Introduction to DC-DC Converters Basic Topologies
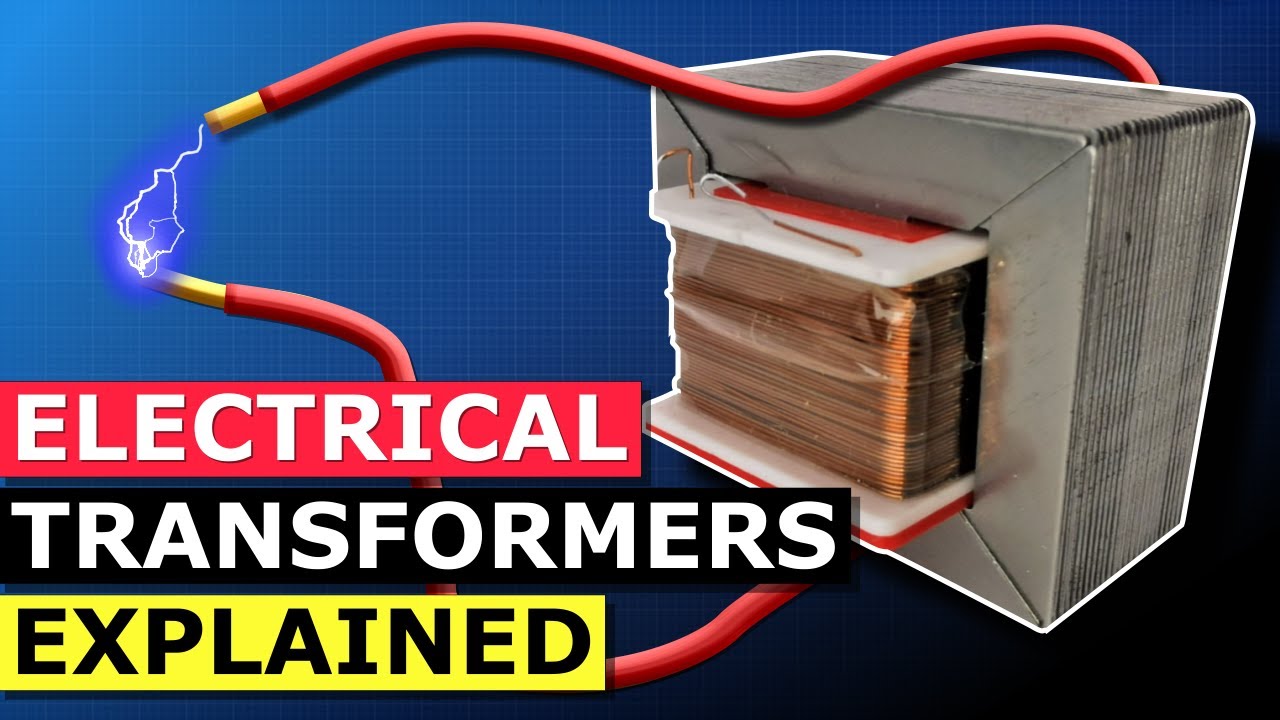
Transformers Explained - How transformers work
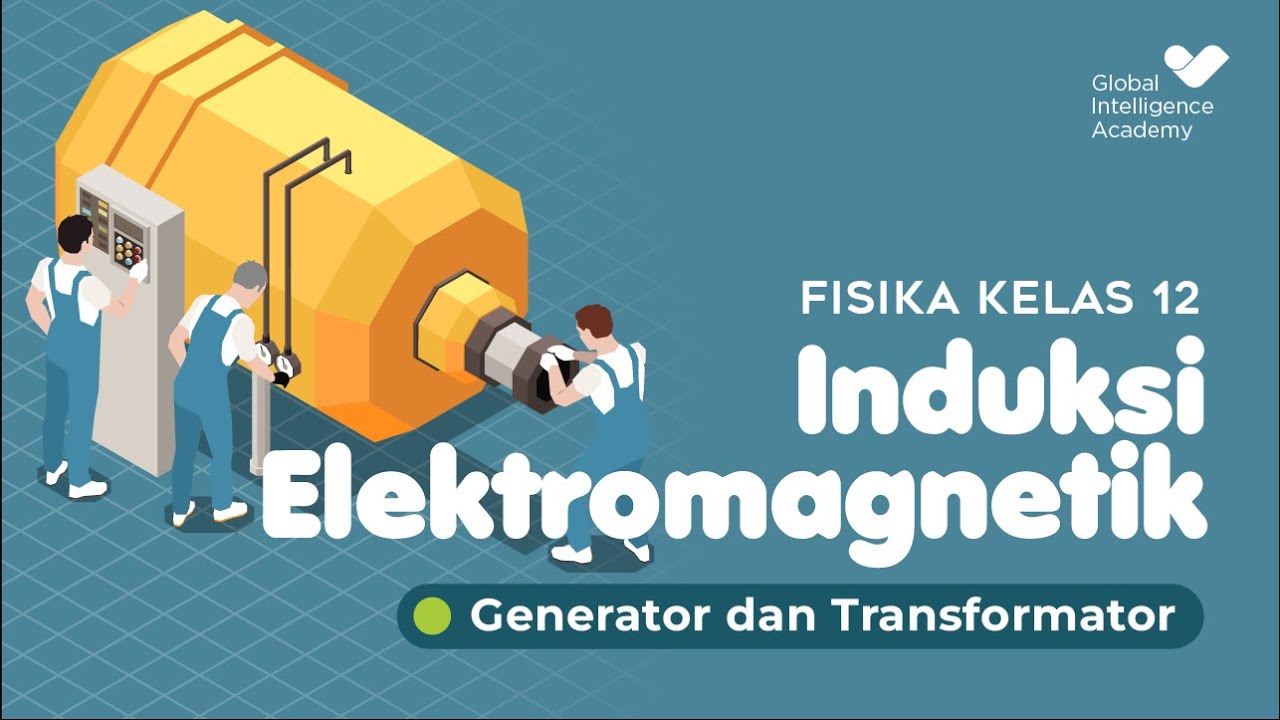
FISIKA Kelas 12 - Induksi Elektromagnetik: Generator & Transformator | GIA Academy

⚡ DC-DC Buck-Boost Converter Design 🔋 Power Electronics Calculations & MATLAB/Simulink

Mengenal cara kerja switch-mode power supply
5.0 / 5 (0 votes)