Preventive Maintenance Meter Based and PM Hierarchies
Summary
TLDRThis video from the Maximo Bite Size series, hosted by Andrew Jeffery, offers an in-depth look at Meter-based Preventive Maintenance (PM) and PM Hierarchies within Maximo Manage. It explains how meter readings trigger PM work orders, the importance of recording meter readings regularly, and the nuances between fixed and floating schedules. The video also delves into the creation and management of PM Hierarchies, emphasizing the generation of work order hierarchies and the impact of asset or location status on the PM process. Viewers are encouraged to subscribe for more insights on Maximo's maintenance planning functionalities.
Takeaways
- 📚 The video is part of a series on Maximo Manage, focusing on the functionality of Preventive Maintenance (PM) application.
- 🔧 Andrew Jeffery discusses Meter-based PMs and PM Hierarchies, emphasizing the importance of understanding these for effective maintenance planning.
- 🕒 Meter-based PMs are more complex than time-based PMs and require regular recording of meter readings for accurate work order generation.
- 📈 The 'Units to Go' field in PMs is calculated based on the difference between the 'Next Meter Reading' and the 'Life To Date' for the asset, considering the 'Generate WO Ahead By' tolerance.
- 🔄 PMs support both fixed and floating schedules, which affect how the 'Estimated Next Due Date' is calculated and when work orders are generated.
- 📝 For new assets without a history of meter readings, the Average Calculation Method should be set to STATIC with an initial value for Average Units/Day.
- 🔄 Historical meter readings can be entered for existing assets to establish an initial 'Life to Date' and average usage, which is crucial for PM effectiveness.
- 🔗 PM Hierarchies allow for the grouping of PMs to be performed together, creating a Work Order Hierarchy that can mimic the structure of asset or location hierarchies.
- 📉 The 'Use this PM to Trigger PM Hierarchy' field is pivotal in determining when a complete work order hierarchy is generated based on the earliest 'Earliest Next Due Date'.
- ⏰ The video emphasizes the flexibility of PMs, including on-demand PMs with zero frequency and null 'Estimated Next Due Date', which can be useful for major equipment shutdowns with uncertain dates.
- 🔑 The video concludes with a reminder of the importance of regular meter readings, the correct setup of PM Hierarchies, and the impact of these settings on work order generation and maintenance planning.
Q & A
What is the main topic of the ninth episode in the Maximo Bite Size series?
-The main topic of the ninth episode is Meter-based Preventive Maintenance (PM) and PM Hierarchies in Maximo Manage.
What are the two types of PMs discussed in the video?
-The two types of PMs discussed in the video are Time-Based PMs and Meter-Based PMs.
Why are Meter-based PMs considered more complex than Time-Based PMs?
-Meter-based PMs are more complex because they involve the calculation of the Estimated Next Due Date based on meter readings and the Average Units/Day, which requires regular recording of meter readings for accuracy.
What is the purpose of the 'Generate WO Ahead By' field in the context of PMs?
-The 'Generate WO Ahead By' field is a tolerance value that allows for the generation of a work order a bit earlier than the exact meter reading indicates, typically to account for the time needed to assemble tools and materials for the work.
How does a Fixed Schedule differ from a Floating Schedule in the context of PMs?
-A Fixed Schedule uses the 'Last Start Date' of the PM to determine the Estimated Next Due Date, while a Floating Schedule uses the 'Last Completion Date' of the last work order to determine this date.
What is the significance of recording regular meter readings for Meter-based PMs?
-Regular meter readings are crucial for the effectiveness of Meter-based PMs as they provide the data needed to calculate when maintenance is due, ensuring that work orders are generated at the correct time.
Why might a company choose to use Time-Based PMs over Meter-Based PMs?
-A company might choose Time-Based PMs over Meter-Based PMs if they are not prepared to regularly record meter readings, or if the equipment does not have meters that can provide the necessary data for meter-based calculations.
What is the role of the 'Units to Go' field in Meter-based PMs?
-The 'Units to Go' field is calculated when a meter reading is recorded and is used to determine how many units are left before the next maintenance is due. It is calculated by subtracting the 'Life To Date' for the asset and the 'Generate WO Ahead By' values from the 'Next Meter Reading' value.
How does the 'Life To Date' field differ from the 'Average Units/Day' field in the context of PMs?
-The 'Life To Date' field represents the accumulated total meter reading for the asset, while the 'Average Units/Day' field represents the average consumption rate of the meter, which is used to estimate when maintenance should occur.
What is the importance of setting up the correct initial values for a new asset when setting up Meter-based PMs?
-Setting up the correct initial values for a new asset is important because it establishes the starting point for the 'Life to Date' and 'Average Units/Day' calculations, which are critical for determining the timing of future maintenance work orders.
What is the recommended approach when creating a PM hierarchy in Maximo?
-The recommended approach is to create the PMs that will be the parents and other ancestors first, then create the PM hierarchy itself. This ensures that all PMs in the hierarchy start with a Draft status, reducing the likelihood of errors during the hierarchy creation.
What is the impact of the 'Child Work Orders and Tasks Will Inherit Status Changes?' field on work order hierarchies in PMs?
-When this field is set, it allows the status of all the work orders in a work order hierarchy to be changed from the top-level work order. This can be useful for managing the status of multiple work orders at once, but should be used carefully to avoid unintended status changes.
Why is it recommended to have the same frequency for all PMs in a hierarchy?
-Having the same frequency for all PMs in a hierarchy simplifies the understanding and management of when work orders will be generated. It avoids confusion that can arise when different PMs have different frequencies or are based on different criteria.
What should be considered when deciding whether to use actual meter readings or estimated projections for generating work orders?
-The decision should be based on the frequency and reliability of meter readings, the tolerance for variation in the 'Average Units/Day', and the importance of generating work orders precisely when a certain meter reading is reached versus using an estimate for planning purposes.
How does the 'Extended Date' affect work order generation in PMs?
-The 'Extended Date' delays the generation of the next work order for Fixed Schedule and Floating Schedule PMs by postponing the Time Based Frequency - Estimated Next Due Date. For Meter Based PMs, the 'Extended Date' cannot be used because the Time Based Frequency - Estimated Next Due Date is null.
What is the significance of the 'Use this PM to Trigger PM Hierarchy' field during work order generation?
-The 'Use this PM to Trigger PM Hierarchy' field determines if a PM in the hierarchy will initiate the generation of a complete work order hierarchy. If the earliest 'Earliest Next Due Date' of a PM with this field set is today or earlier, Maximo will generate the entire hierarchy of work orders.
Why is it necessary for assets or locations associated with PMs to be in an Operating state for work order generation?
-Assets or locations must be in an Operating state or a synonym for work order generation to proceed. If they are not, Maximo will not generate work orders for the associated PMs, as it assumes that the equipment is not ready for maintenance.
What is the recommended action for managing PMs when the frequency or criteria change?
-When the frequency or criteria for PMs change, it is recommended to update the relevant fields in the PM records, such as the 'Estimated Next Due Date' or 'Frequency', to ensure that the PMs are managed accurately and work orders are generated at the correct times.
Outlines
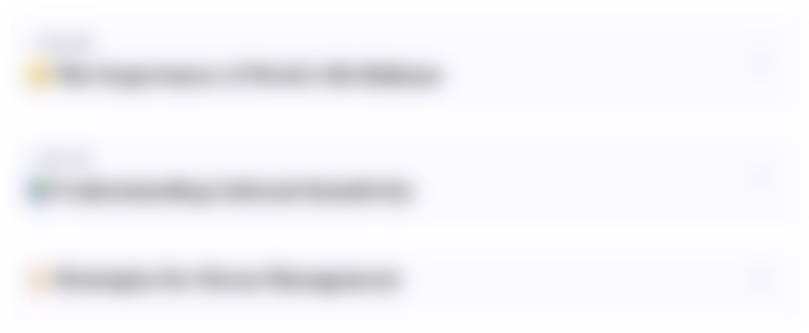
此内容仅限付费用户访问。 请升级后访问。
立即升级Mindmap
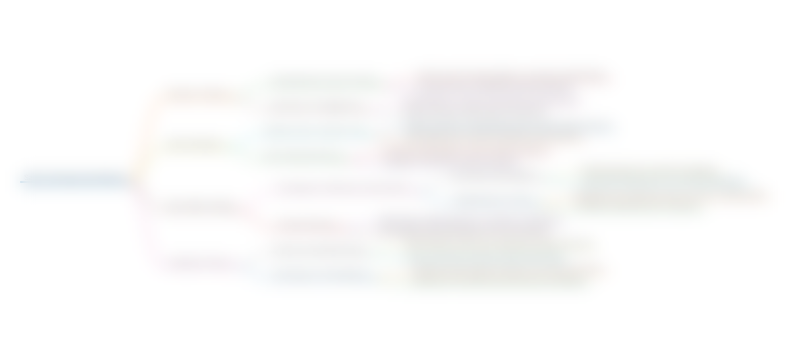
此内容仅限付费用户访问。 请升级后访问。
立即升级Keywords
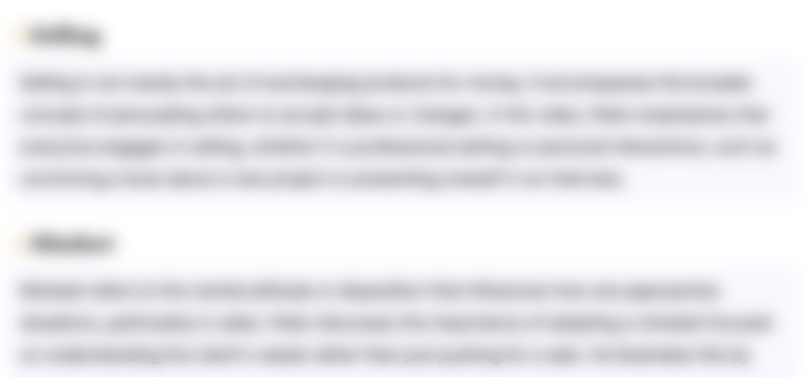
此内容仅限付费用户访问。 请升级后访问。
立即升级Highlights
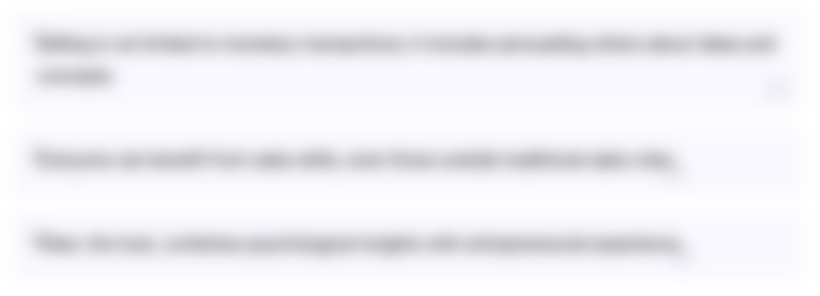
此内容仅限付费用户访问。 请升级后访问。
立即升级Transcripts
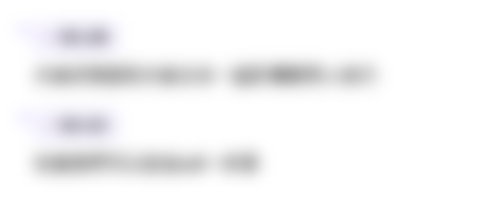
此内容仅限付费用户访问。 请升级后访问。
立即升级5.0 / 5 (0 votes)