Preventive Maintenance Time Based
Summary
TLDRThis Maximo Bite Size video, hosted by Andrew Jeffery, offers an in-depth look at time-based Preventive Maintenance (PM) in Maximo Manage. Covering PM statuses, schedules, and work order generation, it explains fixed vs. floating schedules, job plan sequences, seasonal dates, and PM alerts. The episode is part of a series on Maintenance Planning, aiming to guide viewers through Maximo's PM functionalities, ensuring efficient work order management and maintenance operations.
Takeaways
- π The video series focuses on the functional aspects of Maximo Manage, particularly the Preventive Maintenance (PM) application.
- π The eighth episode specifically discusses time-based PM and inspections, with subsequent episodes covering meter-based PM and PM hierarchies, as well as PM forecasting.
- π The PM application is used for generating work orders based on frequency, which can be time-based, meter-based, or a combination of both.
- π PMs can be associated with Job Plan Sequences, allowing for different job plans to be attached to work orders depending on the occurrence count.
- ποΈ Fixed and floating schedules are explained, with fixed schedules using the last start date to determine the next work order, while floating schedules depend on the actual completion date of the previous work order.
- β οΈ PMs must be in an active state and associated with a location, asset, route, or General Ledger (GL) account to generate work orders.
- π The Counter field in PM is crucial, incrementing each time a work order is generated and determining which job plan is attached to the work order based on sequence.
- π The script covers how to handle seasonal dates and time zones in PM work order generation, ensuring work orders are scheduled appropriately.
- π The video explains the process of generating work orders manually and the importance of considering frequency criteria and look-ahead periods.
- β° The Time Zone Rules application is introduced to manage work order generation in different time zones, ensuring the target start time is relevant to the asset's or location's time zone.
- π Data from PMs or Job Plans is copied to work orders upon generation, including details like Work Type, Priority, and Responsibility fields.
Q & A
What is the main focus of the video series Maximo Bite Size?
-The Maximo Bite Size video series focuses on the functional aspects of Maximo Manage, particularly the Maintenance Planning application and its various functionalities.
Who is the presenter of the Maximo Bite Size series?
-Andrew Jeffery is the presenter of the Maximo Bite Size series.
What are the three types of Preventive Maintenance (PM) applications that will be covered in the video series?
-The three types of Preventive Maintenance applications covered are time-based PM, meter-based PM, and PM hierarchies.
What is the purpose of the Preventive Maintenance application in Maximo Manage?
-The Preventive Maintenance application in Maximo Manage is used for generating work orders based on frequency, either time, meter, or a combination of both, and is essential for maintenance and inspection tasks.
What are the statuses that a PM can have in Maximo Manage?
-A PM in Maximo Manage can have the statuses Draft, Active, or Inactive, and must be in the Active state to generate work orders.
What is the significance of the Lead Time in the Preventive Maintenance process?
-The Lead Time is the number of days prior to when the next work order will be required to start, providing time to prepare or plan the work order, including time needed to purchase materials or services.
What is the difference between fixed and floating schedules in PM?
-A fixed schedule uses the Target Start Date to determine when to generate the next work order, regardless of when the work order is completed. A floating schedule, on the other hand, uses the Actual Finish Date of the work order to set the Target Start of the next work order.
What is the purpose of the Counter field in PM?
-The Counter field in PM is used to track the number of work orders generated from the PM and increments by one every time a work order is generated. It helps in sequencing different Job Plans for the same PM.
How does the Seasonal Dates tab affect the generation of work orders?
-The Seasonal Dates tab allows the user to specify active days and times during which work orders can be generated. If a work order is due on a non-active day, Maximo will adjust the Target Start Date to the next active day or time.
What is the role of the Time Zone Rules application in Maximo Manage?
-The Time Zone Rules application in Maximo Manage allows for the generation of work orders with Target Start Dates that are adjusted according to the time zone of the asset or location where the work is performed, ensuring that the time makes sense to the user in that specific time zone.
What is the importance of the Alert Lead (Days) field in PM Alerts?
-The Alert Lead (Days) field in PM Alerts determines the number of days prior to the next due date when a user is prompted to generate the next PM work order early, in case they wish to perform the PM work order at the same time as a Corrective Maintenance work order.
How can the data from PM or Job Plan be copied to the work order when it is generated?
-When a work order is generated, data from the PM or the next due Job Plan according to the Job Plan Sequence is copied to the work order. This includes fields such as Work Type, Work Order Status, Priority, and other relevant information.
Outlines
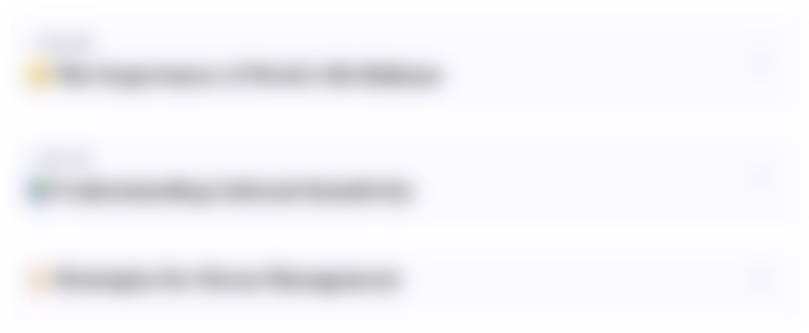
This section is available to paid users only. Please upgrade to access this part.
Upgrade NowMindmap
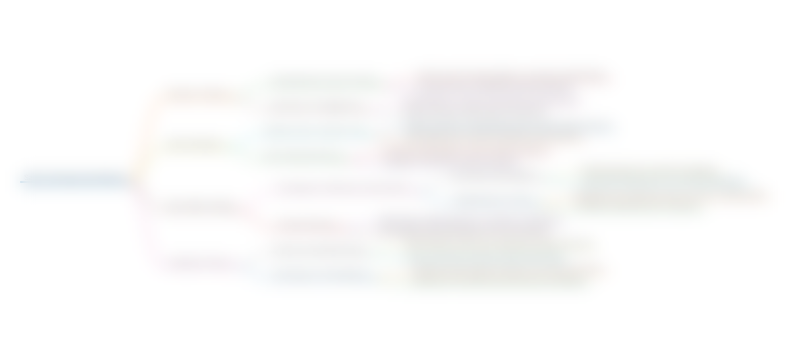
This section is available to paid users only. Please upgrade to access this part.
Upgrade NowKeywords
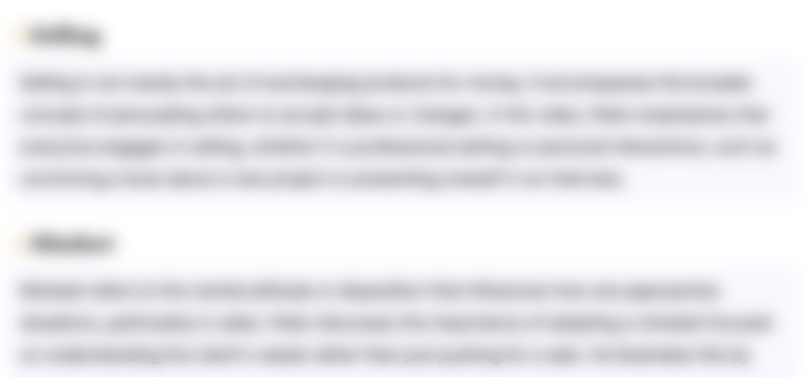
This section is available to paid users only. Please upgrade to access this part.
Upgrade NowHighlights
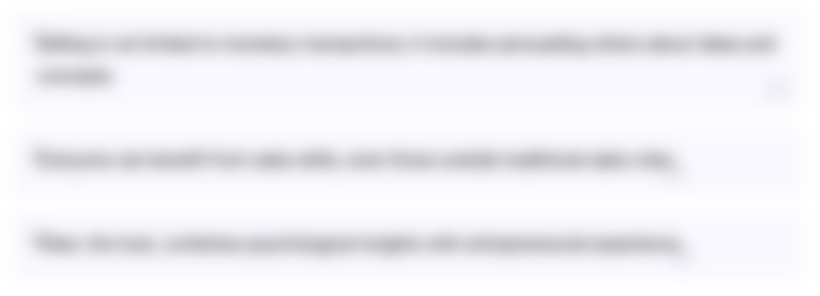
This section is available to paid users only. Please upgrade to access this part.
Upgrade NowTranscripts
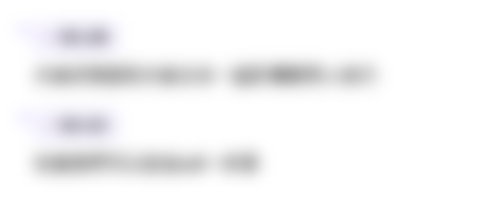
This section is available to paid users only. Please upgrade to access this part.
Upgrade NowBrowse More Related Video
5.0 / 5 (0 votes)