CYLINDER BORE GAUGE ' CARA MENGGUNAKAN, MEMBACA, DAN MENGUKUR DIAMETER SILINDER
Summary
TLDRThis tutorial walks viewers through the process of using a dial bore gauge to measure the diameter of a cylinder liner in a 4-stroke motorcycle engine. The video covers the tools needed, such as a caliper, micrometer, and dial bore gauge, and explains how to calibrate and set up the equipment. It also demonstrates how to measure the cylinder at different positions, record the results, and calculate the final diameters. Key tips for precise measurement and understanding ovality are included, making it an essential guide for engine maintenance and accuracy in measurement techniques.
Takeaways
- 😀 Proper calibration of the dial bore gauge is essential before measurement to ensure accuracy.
- 😀 A micrometer with 50-75 mm range and 0.01 mm precision is needed to measure the cylinder liner diameter.
- 😀 The use of a caliper is the first step to measure the inner diameter of the cylinder before using the dial bore gauge.
- 😀 The diameter measurement from the caliper should be rounded to the nearest millimeter for simplicity (e.g., 53 mm).
- 😀 Micrometer calibration should match the rounded value (e.g., 53 mm) to ensure the correct measurement.
- 😀 The dial bore gauge needs to be calibrated by adjusting the needle to zero before taking measurements.
- 😀 The measurement should be taken at different points on the cylinder liner (X1, X2, X3, Y1, Y2, Y3) for accuracy.
- 😀 When using the dial bore gauge, note the movement of the needle and adjust readings based on its position.
- 😀 The final diameter is calculated by subtracting the measurement value from the initial reading (e.g., 53 mm - 1.40 mm).
- 😀 Proper tool placement and careful handling during measurements are crucial to obtaining precise results.
- 😀 The process includes checking multiple points of the cylinder to ensure uniformity and accuracy in the measurements.
Q & A
What is the main tool used for measuring the cylinder diameter in the script?
-The main tool used for measuring the cylinder diameter is the dial bore gauge.
Why is it necessary to calibrate the micrometer before use?
-The micrometer must be calibrated to ensure accurate measurements, as the settings on the micrometer must match the required measurement for the dial gauge to work properly.
How should the micrometer be set when measuring the cylinder's diameter?
-The micrometer should be set to 53 mm, as the initial measurement taken from the Vernier caliper is rounded to 53 mm before proceeding with the micrometer calibration.
What is the purpose of using a caliper before using the dial bore gauge?
-The caliper is used to measure the internal diameter of the cylinder first, which helps determine the correct settings for the micrometer and the dial bore gauge.
How is the calibration of the dial bore gauge performed?
-The calibration of the dial bore gauge is done by setting the micrometer to the desired value (53 mm), ensuring the dial gauge's needle is at zero, and then checking for proper alignment before starting the measurements.
What is the role of the 'X' and 'Y' directions when measuring the cylinder?
-The 'X' and 'Y' directions refer to different measurement positions on the cylinder: X measures the top and bottom diameters (X1, X2, X3), and Y measures the side diameters (Y1, Y2, Y3). This helps provide a complete profile of the cylinder's dimensions.
What is the significance of the needle movement in the dial bore gauge?
-The movement of the needle on the dial bore gauge indicates the changes in the cylinder's diameter at different positions. The needle helps to detect any variations in the surface or roundness of the cylinder.
How do you calculate the final diameter after using the dial bore gauge?
-The final diameter is calculated by subtracting the reading from the dial bore gauge's needle from the initial measurement on the micrometer. For example, if the micrometer reads 53 mm and the dial bore gauge shows 1.4 mm, the final diameter is 51.6 mm.
Why is it important to record measurements at different points along the cylinder?
-Recording measurements at different points along the cylinder (e.g., X1, X2, X3, Y1, Y2, Y3) ensures an accurate understanding of the cylinder's overall condition, helping to detect any irregularities or wear in the cylinder.
How can you check if the dial bore gauge is correctly calibrated?
-To check if the dial bore gauge is correctly calibrated, observe if the needle is at zero when the gauge is in its resting position after calibration. Any deviation from zero indicates improper calibration.
Outlines
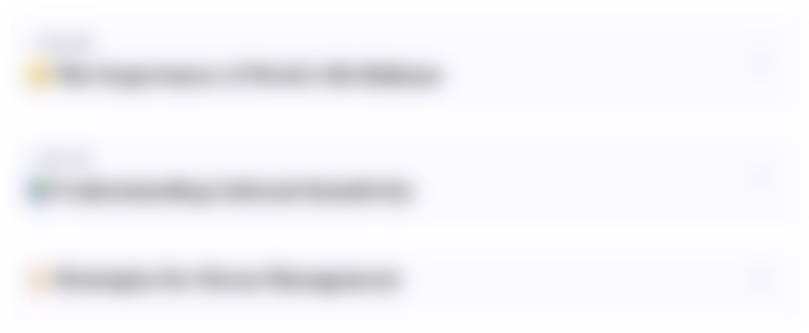
此内容仅限付费用户访问。 请升级后访问。
立即升级Mindmap
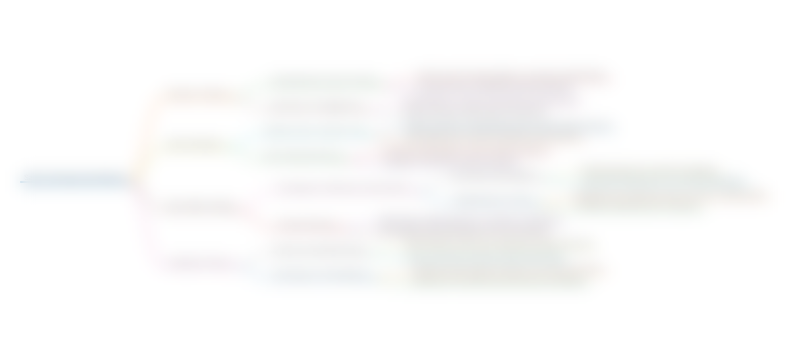
此内容仅限付费用户访问。 请升级后访问。
立即升级Keywords
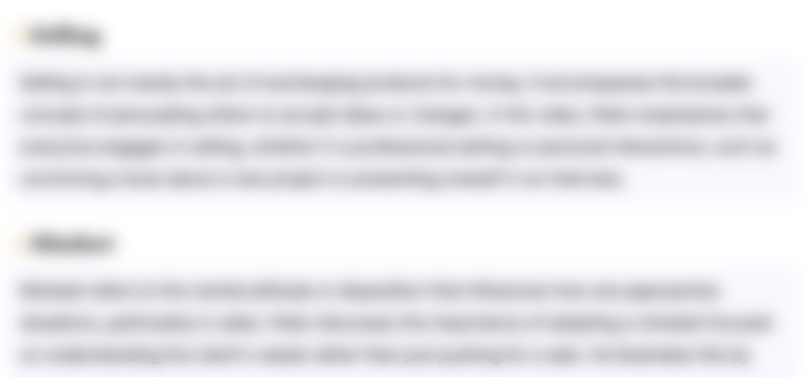
此内容仅限付费用户访问。 请升级后访问。
立即升级Highlights
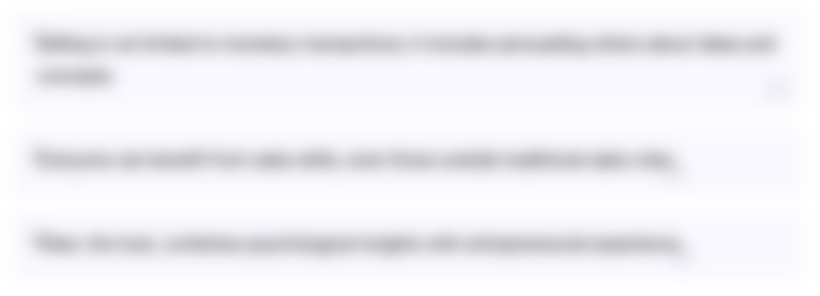
此内容仅限付费用户访问。 请升级后访问。
立即升级Transcripts
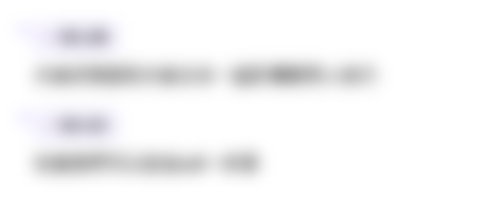
此内容仅限付费用户访问。 请升级后访问。
立即升级浏览更多相关视频
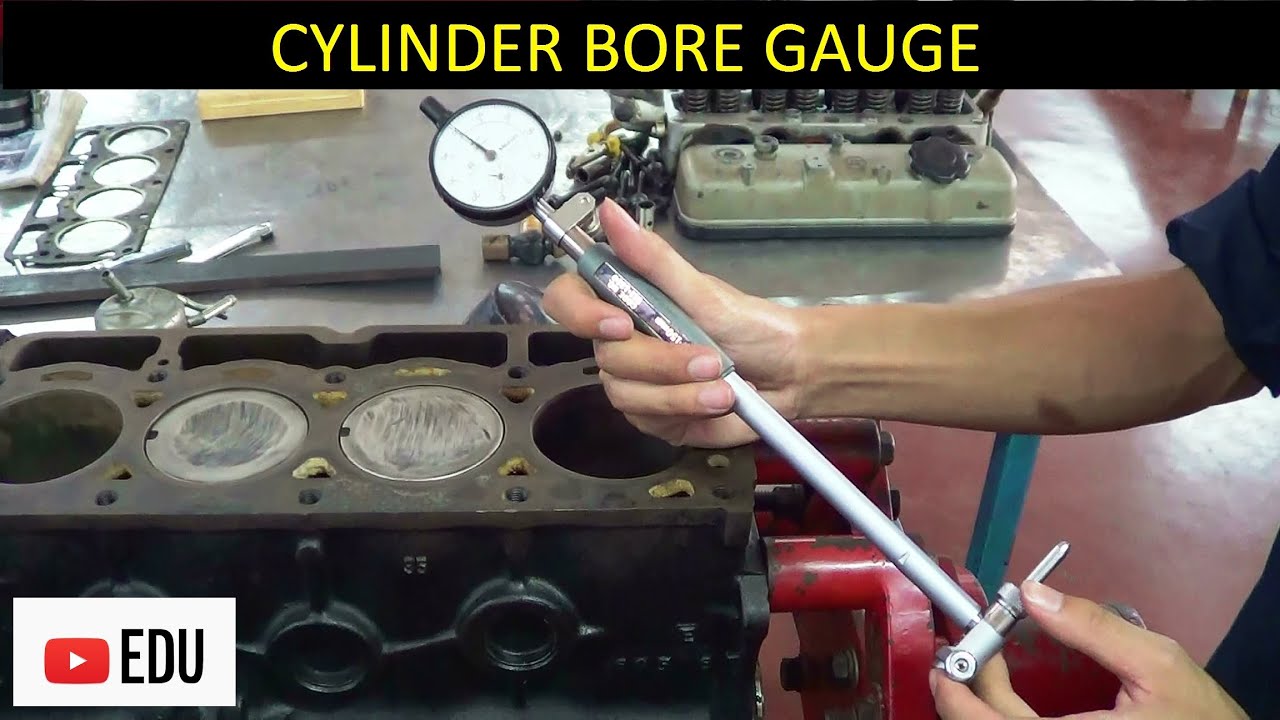
Cylinder Bore Gauge: Komponen, Fungsi dan Cara Menggunakan

Bagaimana Mesin Sepeda Motor 4 Tak Bekerja? - Cara Kerja Motor 4 Tak

Mengenal Bagian-bagian Mesin Motor Secara Detal Sampai Ke Baut-Bautnya
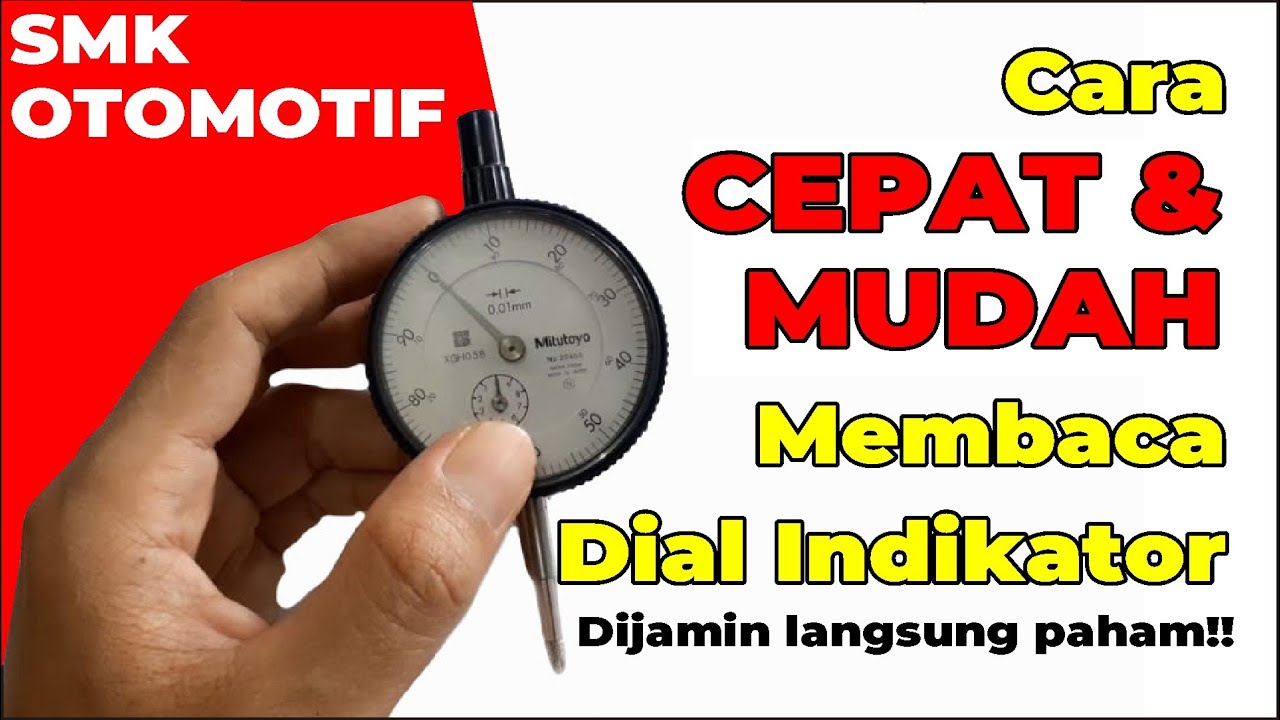
Cara Membaca Dial Indikator
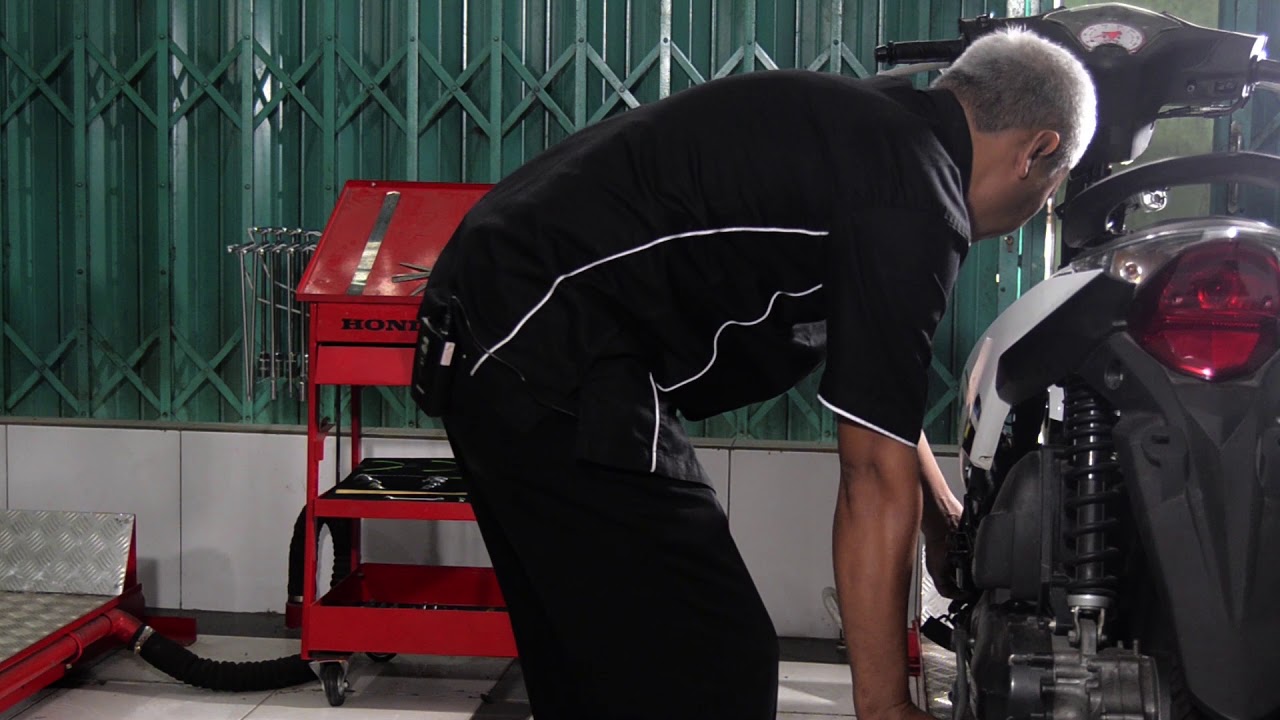
MERAWAT SECARA BERKALA MEKANISME KATUP
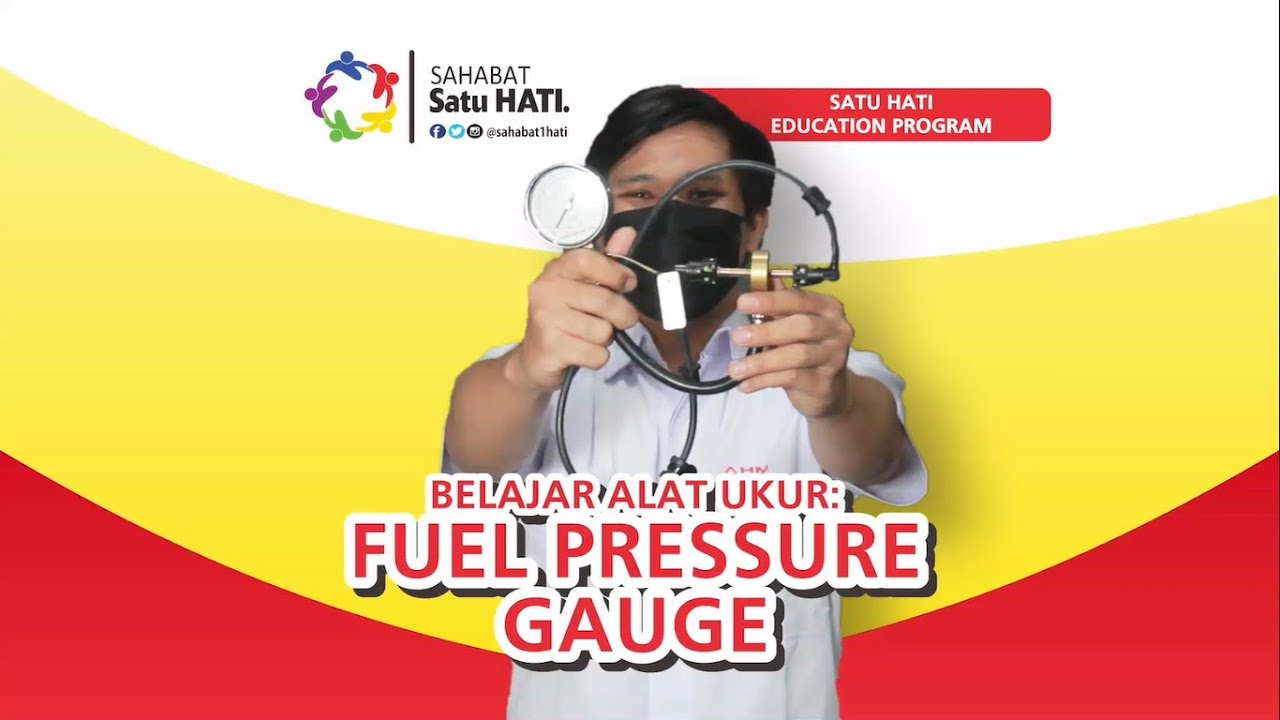
S01E07 - BELAJAR ALAT UKUR FUEL PRESSURE GAUGE
5.0 / 5 (0 votes)