Estudos Organizacionais - Henry Ford e a Linha de Montagem - Fordismo
Summary
TLDRIn this video lesson, we explore the revolutionary contributions of Henry Ford to modern administration through his introduction of the assembly line, which transformed manufacturing. Ford's principles of productivity, intensification, and economic efficiency dramatically reduced production costs and time, making cars more affordable to the masses. His innovations, including standardized parts, vertical integration, and pre-sold products, redefined industrial production. Ford's methods led to the creation of a middle class, as his employees could afford the cars they built. His vision for mass production continues to influence business practices worldwide, and his impact on the automotive industry remains lasting.
Takeaways
- 😀 Henry Ford revolutionized manufacturing through the introduction of the assembly line, drastically changing industrial production.
- 😀 Fordism is a system of mass production, focusing on standardized parts, an assembly line, and efficient use of labor and materials.
- 😀 Ford's three main principles were productivity, intensification, and economic efficiency, which helped lower production costs and prices.
- 😀 The introduction of the assembly line reduced the time to produce a vehicle from over 12 hours to just 2 hours and 38 minutes.
- 😀 Ford eliminated the need for large inventories by aiming for immediate use of raw materials and quick product delivery to the market.
- 😀 Ford paid workers higher wages than most companies at the time, creating a new class of workers who could afford to buy the products they made.
- 😀 The Model T, introduced in 1908, became the first affordable car for the masses and a symbol of mass production success.
- 😀 Ford's innovative approach to pre-selling products before manufacturing them helped reduce financial risks and ensured quick sales.
- 😀 The concept of vertical integration was introduced by Ford, where the company controlled all aspects of production, including raw materials.
- 😀 Ford's development of **Fordlândia** in the Amazon to secure rubber supply for car production was a key example of vertical integration.
- 😀 Ford's principles helped establish the modern middle class by paying workers enough to afford the products they made, thus promoting broader access to wealth.
Q & A
What is Fordism, and who was Henry Ford?
-Fordism refers to the system of mass production and standardized products pioneered by Henry Ford. Henry Ford, born in 1863 in Michigan, was an entrepreneur and engineer who revolutionized the automobile industry and modern administration practices. He is best known for founding the Ford Motor Company and creating the Model T, which made cars affordable for the masses.
What were Henry Ford's key principles of production?
-Henry Ford's key principles included: 1) Productivity, which focused on maximizing output in a set period to reduce costs, lower prices, and increase workers' wages. 2) Intensification, which aimed to reduce manufacturing time by utilizing materials and equipment immediately, leading to faster production cycles. 3) Economic efficiency, which involved reducing the volume of raw materials and minimizing inventory.
How did Ford revolutionize automobile production?
-Ford revolutionized automobile production through the introduction of the assembly line, where the vehicle moved along a conveyor belt while workers performed simple, repetitive tasks. This method drastically reduced production time and costs, enabling mass production and making automobiles more affordable to a wider audience.
Why did Ford avoid maintaining inventory in his factories?
-Ford avoided maintaining inventory because storing raw materials and finished products was costly and inefficient. Inventory required space, management, security, and incurred risk from theft or obsolescence. Instead, he focused on using materials immediately and selling products before they were manufactured.
What was the impact of Ford’s production methods on car prices?
-Ford's production methods led to a dramatic decrease in car prices. By 1920, the price of the Ford Model T dropped to $290, making it accessible to a broader population. This was a significant reduction from the original price of $850 in 1908.
How did Ford contribute to the creation of the middle class?
-Ford’s decision to pay his workers higher wages than other companies allowed them to afford the very product they were producing—cars. This helped establish a middle class who could now purchase cars, thus creating a new consumer base and changing the social dynamics of the time.
What was the role of Fordlandia, and why was it significant to Henry Ford's operations?
-Fordlandia was a city established by Henry Ford in Brazil for rubber production. This was part of Ford's strategy to control all aspects of production for his vehicles, ensuring a steady supply of raw materials like rubber, which was crucial for manufacturing cars.
What changes did Ford make to the design and production of cars compared to previous methods?
-Ford introduced standardized parts and mass production techniques. Unlike earlier methods, where each car was custom-made with parts that were sometimes adapted on the spot, Ford's system used standardized, interchangeable parts, allowing for efficient assembly and reducing production costs.
How did Ford's assembly line differ from earlier production methods?
-Before Ford's assembly line, automobiles were produced through a slow, manual process where workers individually worked on each vehicle. In contrast, Ford's assembly line allowed for a continuous, efficient flow where the car moved along a conveyor belt, and workers performed simple tasks, speeding up production drastically.
How did Ford's decision to offer cars in only one color—black—impact production efficiency?
-Ford's decision to offer cars only in black was a deliberate move to streamline production. By limiting the color options, Ford avoided the complexity of changing production processes and ensured a faster, more efficient production line, as introducing other colors would have required halting the assembly line and resetting the production system.
Outlines
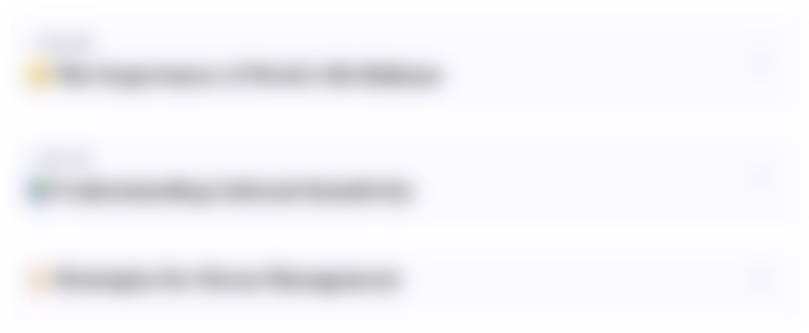
此内容仅限付费用户访问。 请升级后访问。
立即升级Mindmap
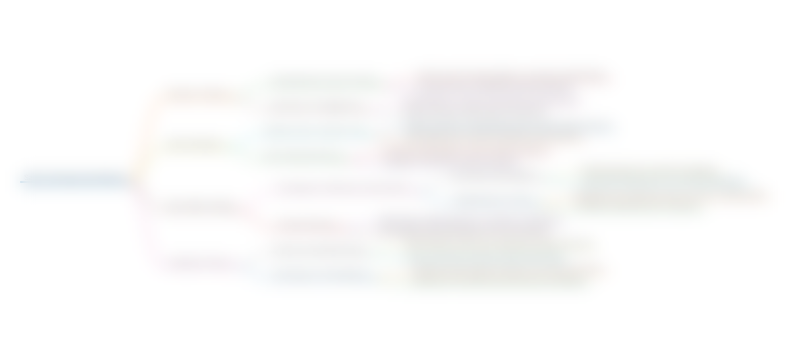
此内容仅限付费用户访问。 请升级后访问。
立即升级Keywords
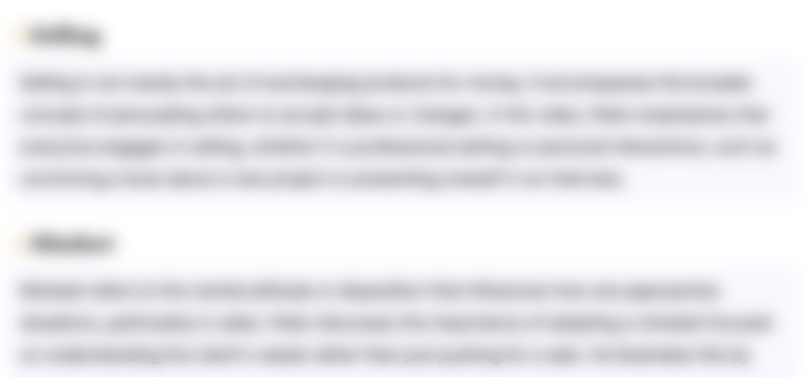
此内容仅限付费用户访问。 请升级后访问。
立即升级Highlights
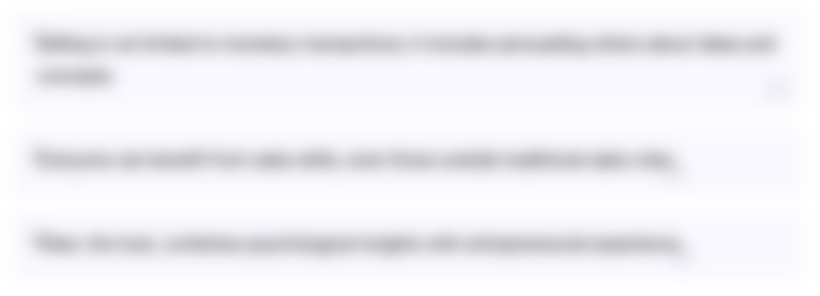
此内容仅限付费用户访问。 请升级后访问。
立即升级Transcripts
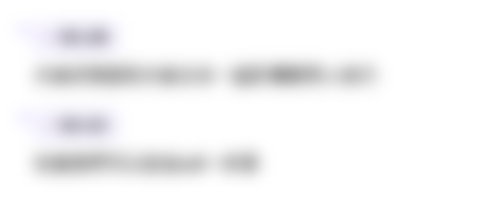
此内容仅限付费用户访问。 请升级后访问。
立即升级5.0 / 5 (0 votes)