Ford and Taylor Scientific Management (Edited)
Summary
TLDRThe script narrates the transformation of automobile manufacturing from handcrafted luxury to mass-produced affordability, led by Henry Ford's vision. Ford revolutionized production with the introduction of the assembly line, which increased efficiency and reduced the time to build a car to 1.5 hours. This innovation, combined with high wages, attracted a constant flow of workers to Detroit, leading to the creation of affordable cars and well-paid laborers. However, it also led to a loss of worker autonomy and strict factory discipline, as Ford's methods prioritized productivity over worker comfort.
Takeaways
- 🏭 The Vulcan Motor Company in Britain was known for its slow and careful hand-assembled cars, which were expensive and accessible only to the wealthy.
- 🚗 Henry Ford envisioned a simple, affordable car for the masses, the Model T, which would disrupt the luxury car market.
- 🛠️ Ford's strategy to produce the Model T cheaply involved reorganizing the factory and changing the way workers worked, influenced by efficiency expert Frederick Taylor.
- ⏱️ Taylorism introduced time studies and motion analysis to increase worker productivity, as exemplified by the pig iron experiment and the world's fastest typist record.
- 🔧 Automobile production was revolutionized by breaking down the process into simple, repetitive steps, eliminating the need for highly skilled craftsmen.
- 🔄 The introduction of the assembly line in 1913 by Ford was a groundbreaking innovation, significantly increasing production efficiency.
- 💹 Mass production at Ford's factory, enabled by the assembly line, led to a system that would dominate manufacturing for much of the 20th century.
- 💰 Ford's doubling of wages to $5 a day, despite the grueling work pace, attracted a flood of workers and set a new standard for wages in the industry.
- 🚫 Ford's factory had strict rules, with no unions allowed, and a private security force to maintain discipline and suppress dissent.
- 🏭 The constant influx of new workers to Detroit, due to the high demand for labor, gave Ford the power to set stringent work conditions.
Q & A
What was the Vulcan Motor Company's approach to car assembly in Britain?
-The Vulcan Motor Company in Britain was proud of their craftsmen who assembled cars slowly and carefully by hand, working at their own pace. This process was time-consuming and resulted in expensive, handmade cars.
How did Henry Ford's vision for car manufacturing differ from the traditional approach?
-Henry Ford envisioned making the simplest car ever, designed for rural America, akin to a 20th-century horse and buggy. He aimed to produce the Model T cheaply, which required changing the way cars were built and how workers worked.
Who influenced Henry Ford's reorganization of his factory, and what was the result?
-Henry Ford was influenced by efficiency expert Frederick Taylor. Taylor's methods, known as Taylorism, involved timing workers with stopwatches and breaking down tasks into simple, repetitive steps, which significantly increased production efficiency.
What was the significance of the assembly line introduced by Henry Ford?
-The assembly line introduced by Henry Ford was revolutionary as it allowed for mass production of cars. It moved the cars past the stationary workers, who added parts to the vehicle as it moved, greatly increasing the speed and efficiency of car assembly.
How did the assembly line impact the production speed and cost of the Model T?
-The assembly line drastically reduced the time taken to build each Model T to 1 and 1/2 hours, which in turn lowered the cost of production, making cars more affordable for the general public.
What was Henry Ford's strategy to attract and retain workers in his factory?
-Henry Ford doubled wages to an unprecedented $5 a day, which attracted a large number of applicants. This strategy, combined with mass production and low costs, created well-paid workers and affordable cars.
What were the working conditions like for workers on the assembly line?
-Working conditions on the assembly line were demanding, with workers facing high pressure to keep up with the pace set by the moving assembly line. There was little room for stopping or slowing down, and job security was minimal.
How did Ford's factory management maintain control over the workforce?
-Ford's private security force, the Plant Protection Service, enforced strict discipline. Recruiters for unions were fired, and company spies monitored for troublemakers. Workers had limited freedom, even needing permission for bathroom breaks.
What was the impact of Ford's high wages and strict work rules on the workers?
-Ford's high wages attracted workers, but the strict work rules and lack of job security made workers increasingly powerless. The constant supply of new workers willing to accept Ford's terms kept the factory running at a fast pace.
How did the introduction of the assembly line change the automotive industry?
-The introduction of the assembly line by Ford revolutionized the automotive industry by enabling mass production, which led to a significant reduction in car prices, making cars accessible to a much broader market and setting a new standard for manufacturing efficiency.
Outlines
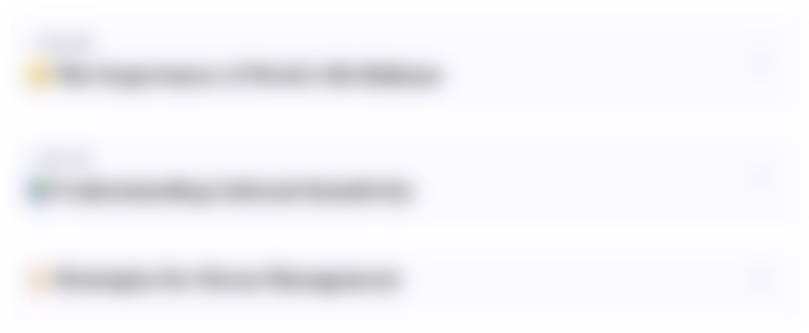
This section is available to paid users only. Please upgrade to access this part.
Upgrade NowMindmap
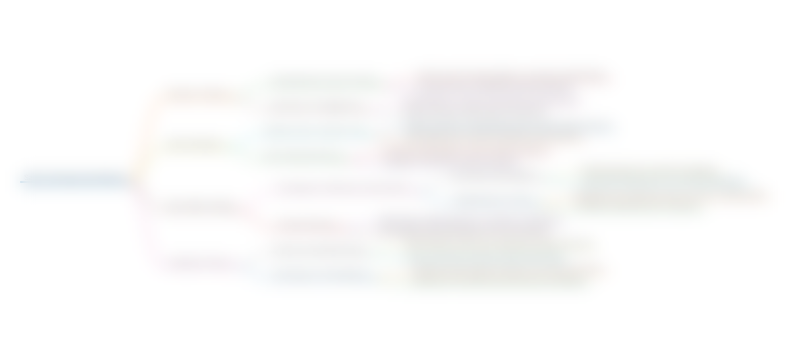
This section is available to paid users only. Please upgrade to access this part.
Upgrade NowKeywords
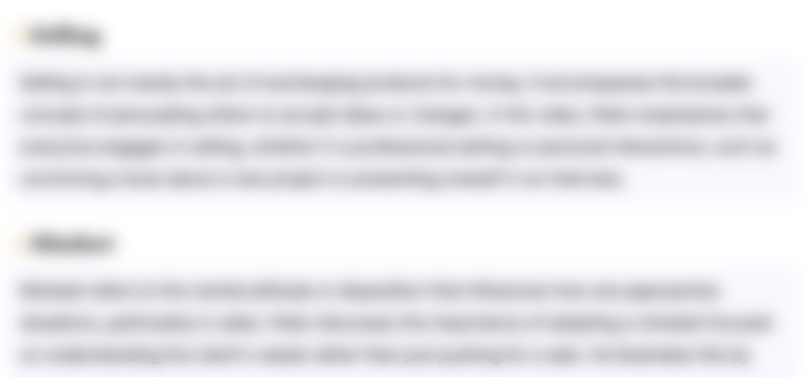
This section is available to paid users only. Please upgrade to access this part.
Upgrade NowHighlights
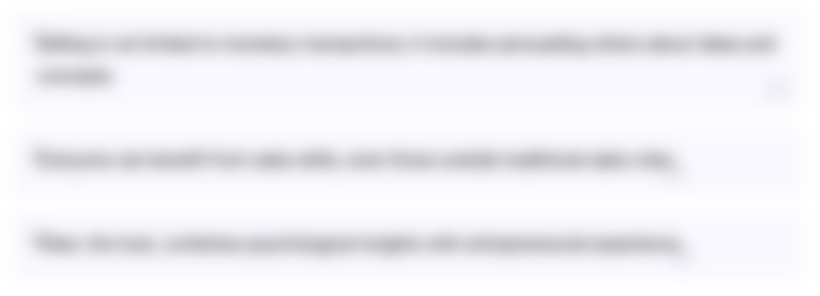
This section is available to paid users only. Please upgrade to access this part.
Upgrade NowTranscripts
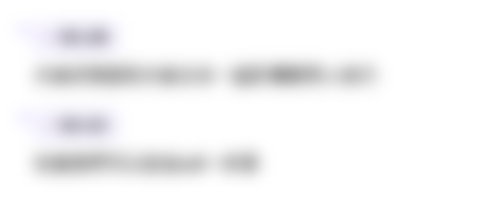
This section is available to paid users only. Please upgrade to access this part.
Upgrade NowBrowse More Related Video
5.0 / 5 (0 votes)