Modul A - Uji Tarik
Summary
TLDRThis video provides an overview of tensile testing in a materials engineering lab. It introduces the specimen setup, explaining the various components of a tensile specimen, such as grips and fillet sections, as well as the process of measuring diameters. The video further demonstrates the operation of a tensile testing machine, showing how the specimen is gripped and loaded. It also covers the process of final measurement after testing, including elongation and final diameter, providing a comprehensive view of the tensile test procedure from start to finish.
Takeaways
- 😀 The speaker, Andhika, introduces the material testing assistant role and the mechanical testing space where various tests, such as tensile, bending, hardness, and torsion, are conducted.
- 😀 The specimen for tensile testing is introduced, with specific focus on parts such as the grip, fillet, and necking section, which are crucial for stress concentration.
- 😀 The speaker explains the process of measuring the diameter of the specimen, taking three measurements and using the smallest value as the reference.
- 😀 The concept of the 'get Slank' is explained, emphasizing that it is determined to be four times the diameter of the specimen, based on ASTM A370 standards.
- 😀 A caliper is used to measure the specimen's length, and the measured value is marked to aid in testing preparation.
- 😀 The tensile testing machine is described, with key components including the upper and lower grips, a central grade for specimen clamping, and a load cell to measure the applied load.
- 😀 The process of clamping the specimen in the tensile testing machine's grips is demonstrated, showing how the specimen is properly secured for the test.
- 😀 The load cell indicator, with two different scales for varying loads, is discussed, along with the machine’s control buttons that allow adjustment of the pull rate.
- 😀 The machine's adjustment buttons are highlighted, particularly the one for controlling the pulling speed of the specimen during the test.
- 😀 The script concludes with a final measurement demonstration, where the elongation and diameter change of the specimen are observed after testing, with specific reference to the final length and the fracture's characteristic.
Q & A
What is the purpose of the tensile testing procedure described in the transcript?
-The tensile testing procedure is used to measure the mechanical properties of materials by subjecting them to tension until they break, helping to evaluate strength and behavior under stress.
What are the key components of the tensile test specimen in this setup?
-The key components include the grips (which hold the specimen in place), the fillet or radius section (designed to reduce stress concentration), and the gauge length (the portion that will undergo measurement).
Why is the smallest diameter used to measure the specimen during the test?
-The smallest diameter is used because it represents the location where necking (local reduction in cross-section) will occur, which is where the material is most likely to fail.
How is the gauge length of the specimen determined?
-The gauge length is calculated as four times the diameter of the specimen, based on the standard ASTM A370, which for this example was 6.25 mm, leading to a gauge length of 25 mm.
What role does the load cell play in the tensile testing machine?
-The load cell measures the force applied to the specimen during the test, allowing the machine to record the load at different stages of the specimen’s deformation.
What is the function of the crosshead in the tensile testing machine?
-The crosshead is part of the machine that moves up and down to apply tension to the specimen, causing it to elongate until it reaches failure.
Why is it important to measure the specimen’s diameter at multiple points before testing?
-Measuring the specimen’s diameter at multiple points ensures accuracy in determining the smallest diameter, which is crucial for calculating stress and observing where necking will occur.
What happens to the specimen during the tensile test as it is subjected to tension?
-As the specimen is stretched, it elongates, and at the weakest point (smallest diameter), necking occurs, leading to the specimen eventually breaking.
What does the 'necking' phenomenon refer to in tensile testing?
-Necking refers to the localized reduction in the specimen’s cross-sectional area, typically occurring at the weakest point, which precedes fracture.
How is the final diameter of the specimen measured after the tensile test?
-The final diameter is measured at the point of fracture, where the specimen has typically formed a neck, and only one diameter is measured to assess the extent of deformation.
Outlines
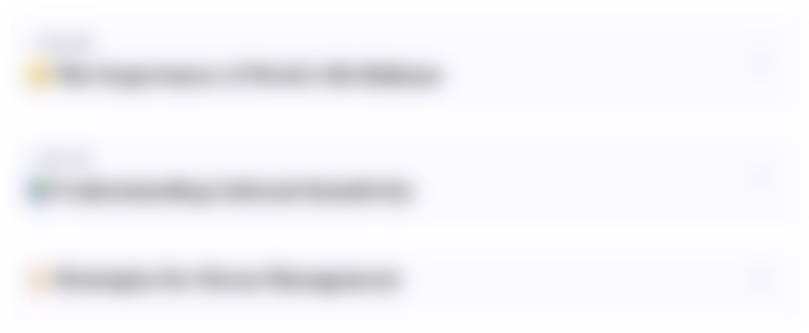
此内容仅限付费用户访问。 请升级后访问。
立即升级Mindmap
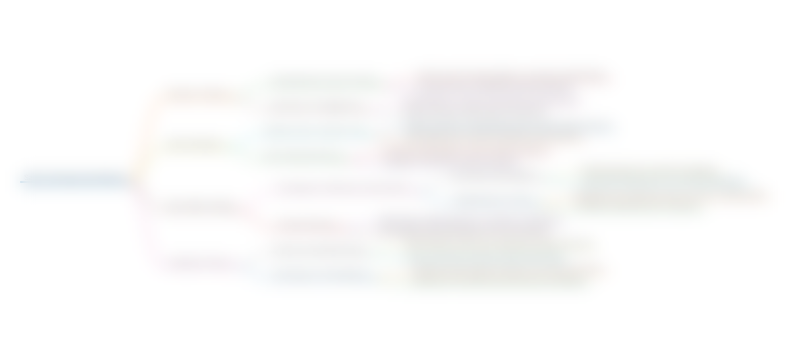
此内容仅限付费用户访问。 请升级后访问。
立即升级Keywords
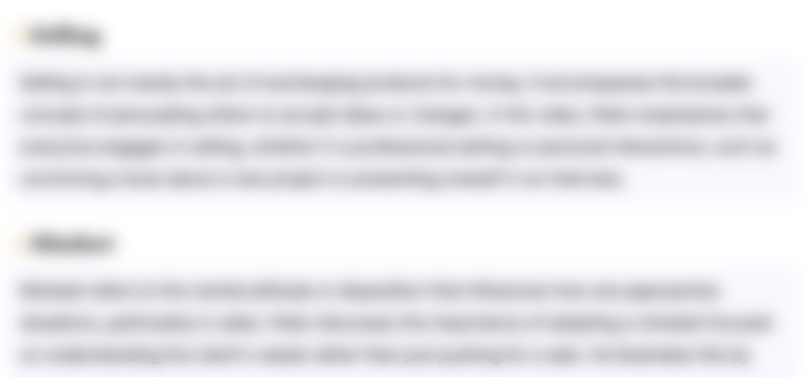
此内容仅限付费用户访问。 请升级后访问。
立即升级Highlights
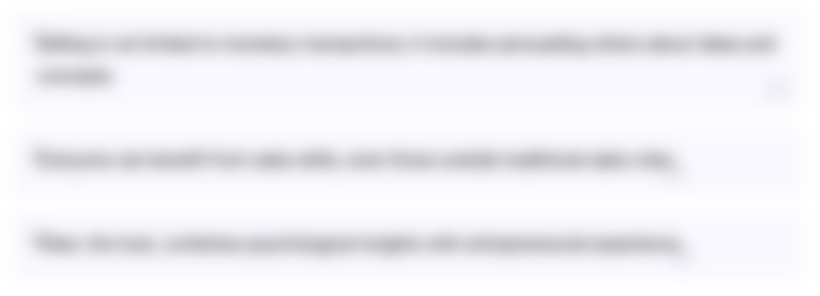
此内容仅限付费用户访问。 请升级后访问。
立即升级Transcripts
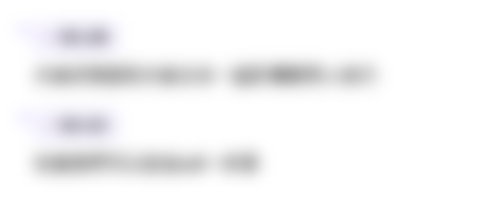
此内容仅限付费用户访问。 请升级后访问。
立即升级5.0 / 5 (0 votes)