5S Explained: Whiteboard Animation
Summary
TLDRThe 5S methodology is a lean management system designed to organize and optimize the workplace. It focuses on five key steps: Sort (eliminate unnecessary items), Set in Order (organize tools and materials), Shine (maintain cleanliness and equipment), Standardize (create consistent processes), and Sustain (embed 5S into daily routines). This process helps improve efficiency, safety, and morale, while reducing waste and downtime. By fostering a culture of continuous improvement, 5S ensures long-term productivity and a safer, more organized work environment.
Takeaways
- 😀 5S is a lean methodology designed to transform messy workplaces into organized, efficient spaces.
- 😀 The 5S steps include Sort, Set in Order, Shine, Standardize, and Sustain, each focusing on specific areas of improvement.
- 😀 The 'Sort' step eliminates unnecessary tools and materials, reducing clutter to improve workflow.
- 😀 Red tags help identify and remove unneeded items by marking them for evaluation during the 'Sort' phase.
- 😀 'Set in Order' involves organizing tools and materials logically, making them easier to access and use, improving workflow.
- 😀 Floor marking and labels enhance organization and safety by indicating where tools, equipment, and materials should be placed.
- 😀 The 'Shine' step focuses on maintaining a clean workspace, which improves employee morale, reduces equipment breakdowns, and prevents injuries.
- 😀 Regular inspection and maintenance during 'Shine' help keep equipment in good condition and prevent disruptions.
- 😀 'Standardize' involves creating systems and routines to ensure the 5S steps are consistently followed by all employees.
- 😀 'Sustain' ensures that the principles of 5S become a part of the daily routine and continue to be practiced over time.
- 😀 Safety is integral to 5S, and programs that incorporate safety as the sixth S are known as '6S', contributing to a safer workplace.
Q & A
What is the primary goal of the 5S methodology?
-The primary goal of the 5S methodology is to create a clean, organized, and efficient workplace that increases productivity, safety, quality, and morale, while reducing waste.
What does the 'Sort' step in 5S focus on?
-The 'Sort' step focuses on eliminating unnecessary tools, materials, and items from the workspace. It aims to create a clutter-free environment by keeping only the items needed for daily work.
How does the 'Set in Order' step improve workplace organization?
-The 'Set in Order' step creates a standardized and consistent way to store and retrieve tools and materials. It emphasizes organizing items in the order of use, with frequently used items placed closest to the user.
Why are red tags used during the 'Sort' step?
-Red tags are used to identify and mark items that need to be removed from the workspace. They help employees evaluate which items are unnecessary and should be discarded or relocated.
What is the purpose of floor markings in the 'Set in Order' step?
-Floor markings are used to indicate where tools, materials, trash cans, and machinery should be placed. This improves organization, safety, and the workflow by clearly designating areas for each item.
How does the 'Shine' step contribute to workplace safety?
-The 'Shine' step involves regular cleaning and maintenance of tools and machinery, which helps reduce accidents, equipment breakdowns, and injuries. A clean workspace also contributes to a positive work environment.
Why is the 'Standardize' step important in the 5S process?
-The 'Standardize' step ensures that the practices of sorting, setting in order, and shining are consistently followed. It creates standardized systems for daily tasks and procedures, helping sustain the 5S practices over time.
How can the 'Sustain' step help maintain the results of 5S?
-The 'Sustain' step involves incorporating 5S into daily routines to ensure that it becomes a regular part of the workplace culture. This can be achieved through designated times for 5S activities and by engaging all employees in the process.
What role does management play in sustaining the 5S practices?
-Management plays a crucial role in sustaining 5S by leading by example, ensuring that employees follow the steps, and promoting engagement through initiatives like rotating committees, reminders, and periodic evaluations.
What is the 'sixth S' mentioned in the script, and why is it important?
-The 'sixth S' is Safety. It emphasizes the importance of creating a safe workplace through proper organization and safety measures such as personal protective equipment, clear labels, and safety training, all of which go hand in hand with the 5S principles.
Outlines
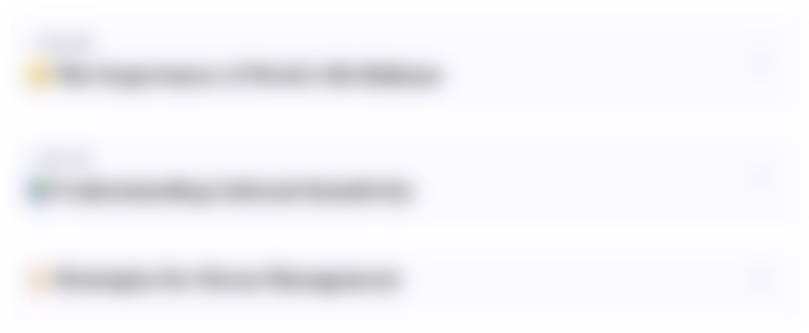
此内容仅限付费用户访问。 请升级后访问。
立即升级Mindmap
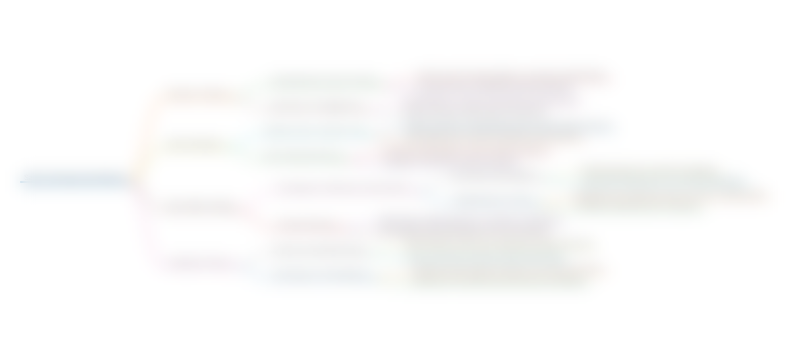
此内容仅限付费用户访问。 请升级后访问。
立即升级Keywords
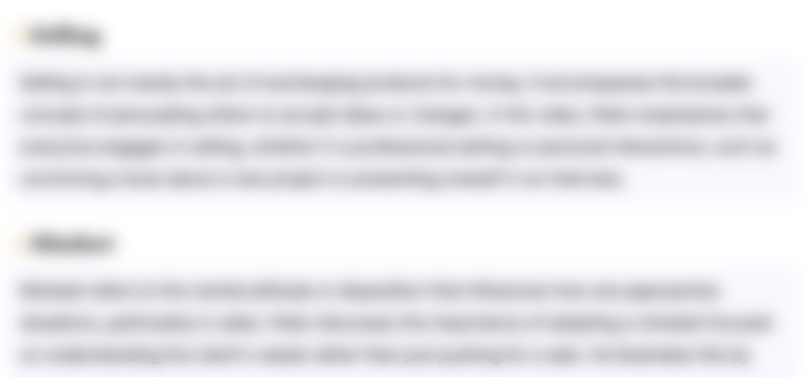
此内容仅限付费用户访问。 请升级后访问。
立即升级Highlights
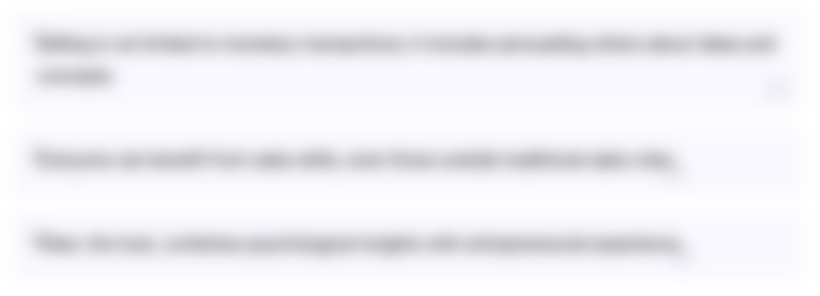
此内容仅限付费用户访问。 请升级后访问。
立即升级Transcripts
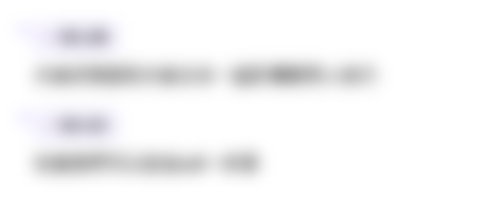
此内容仅限付费用户访问。 请升级后访问。
立即升级浏览更多相关视频

Toyota Material Handling | Why 5S?

Understand the Basics of 5S, Explanations and 5S Steps

The 5S Game (Lean Six Sigma)
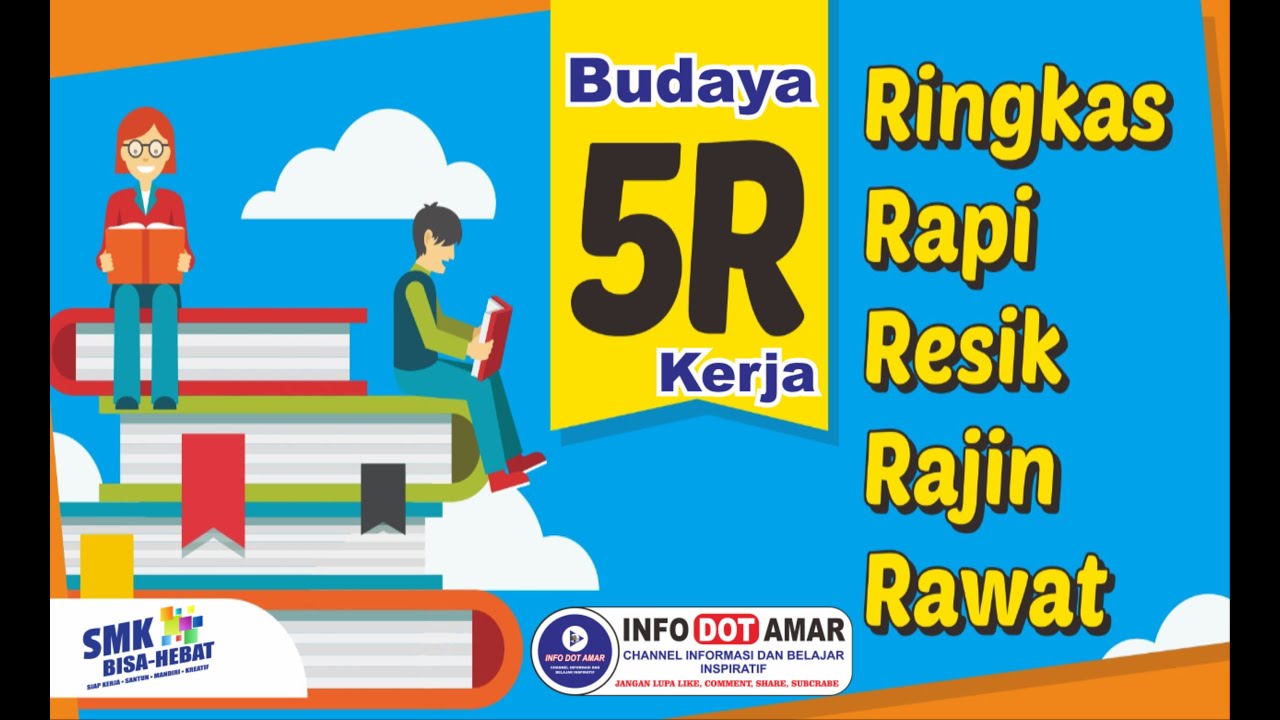
Budaya Kerja 5R || P5BK || Penguatan Projek Profil Pelajar Pancasila || SMK

Strategi 5S/5R Kaizen di Tempat Kerja Untuk Meningkatkan Produktivitas Usaha
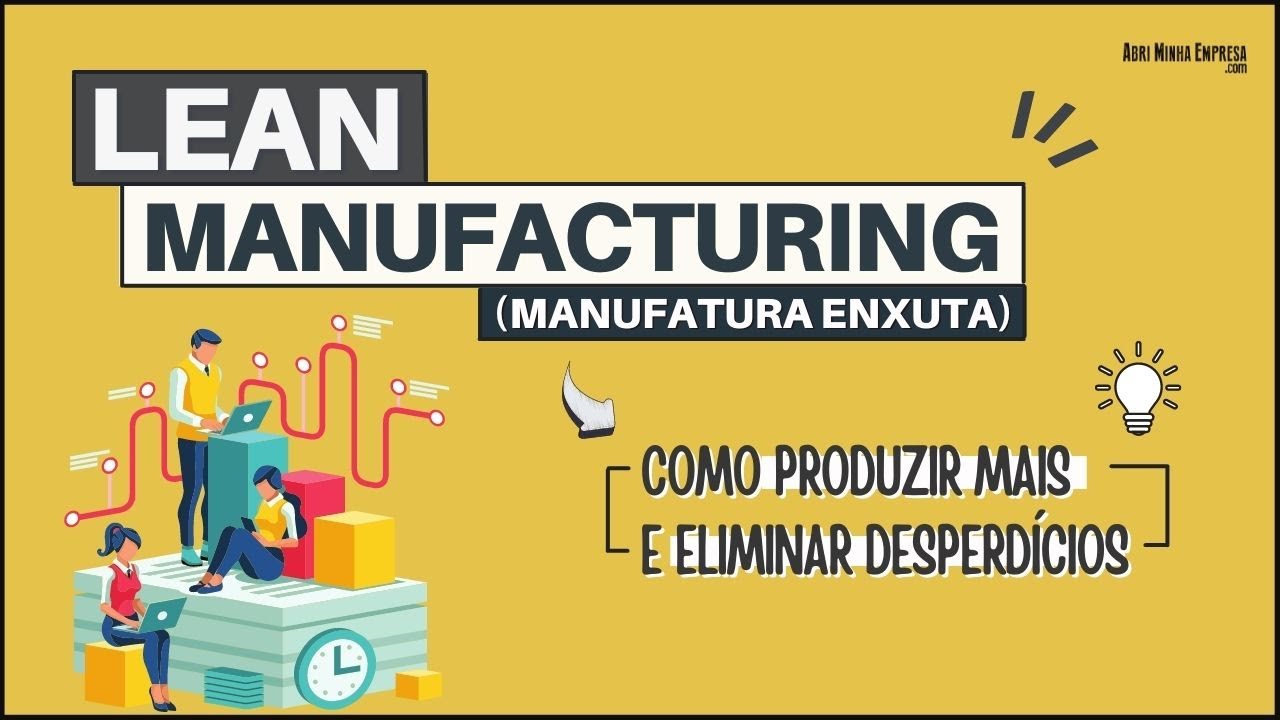
LEAN MANUFACTURING (Manufatura Enxuta) | Conheça os 8 Principais Tipos de Desperdícios
5.0 / 5 (0 votes)