How It's Made Cotton yarn
Summary
TLDRThis script narrates the evolution of yarn production from primitive spindles to modern automated machines. It details the process of transforming raw cotton into commercial yarn, involving cleaning, combing, and stretching stages. The script also highlights the use of winding machines for quality control and the transition from manual to automated processes, culminating in the production of a fine yarn used in fabrics like jeans and tops.
Takeaways
- 📚 The process of spinning yarn from plant or animal fibers dates back to ancient times.
- 🌏 The spinning wheel, invented in India around 500 BC, revolutionized yarn production.
- 🏭 Modern factories utilize fully automated spinning machines that operate on the same principle as the spinning wheel.
- 🧶 A two-ply commercial yarn, used for weaving fabric in jeans and tops, is made from raw cotton.
- 🌿 Cotton naturally contains leaves and stems, which are removed in the initial stages of processing.
- 🔍 The first cleaning machine processes 500 kg of cotton per hour to blend and clean the fibers.
- 🔧 A second cleaning machine further refines the cotton to ensure it is clean enough for spinning.
- 📏 The carding machine combs out tangled fibers and aligns them in parallel rows, discarding any too short to process.
- 🔄 The coiler forms the first stage yarn called sliver from the aligned fibers.
- 📌 The drawing machine and roving frame further process the yarn by stretching and thinning it to increase strength.
- 🔗 The final stage of yarn production involves stretching the roving up to 30 times thinner to strengthen it further.
- 🔄 The winding machine transfers the finished yarn from small spools onto large industrial cones for quality control and packaging.
- 👁️🗨️ An optical sensor performs a quality control check, cutting off and reattaching yarn that doesn't meet specifications.
- ⏱️ The entire process of spinning yarn from start to finish takes approximately 48 hours.
Q & A
What is the historical origin of the spinning wheel?
-The spinning wheel originated in India around 500 BC.
What is the purpose of the first cleaning machine in the cotton processing?
-The first cleaning machine removes a 5 mm layer of cotton and processes 500 kg of cotton per hour to blend and clean it, but it is not yet clean enough for further processing.
What does the second cleaning machine do to the cotton?
-The second cleaning machine finishes the job of cleaning the cotton, making it ready for the next stages of processing.
What is the function of the carding machine in the yarn production process?
-The carding machine combs out tangled fibers and lines them up in parallel rows, also discarding any fibers that are too short to process.
What is the first stage yarn called that is formed by the coiler?
-The first stage yarn formed by the coiler is called sliver.
How does the drawing machine contribute to the yarn production?
-The drawing machine lines up six rows of fibers at a time and draws them out, stretching them to form a second stage yarn.
What is the purpose of the roving frame in the yarn-making process?
-The roving frame stretches the second stage yarn, strengthening it by thinning it out until it reaches the desired consistency.
How much thinner is the final yarn compared to the initial sliver?
-The final yarn is 200 times lighter than the initial sliver that came out of the carding machine.
What is the role of the winding machine in transferring yarn onto industrial size cones?
-The winding machine winds the yarn from small spools onto large industrial size cones, automatically attaching and discarding spools as they empty.
How does the optical sensor on the winding machine ensure quality control?
-The optical sensor performs a quality control check, stopping the winding if a portion of yarn doesn't meet specifications, cutting off the offending portion, reconnecting the ends, and resuming winding.
What is airjet spinning and how does it differ from the winding method described?
-Airjet spinning is another method of making yarn from slivers and winding it onto giant spools known as tubes. It uses a suction tube to connect the yarn spools with tiny knots, which is a more automated process than the manual nodding that was done before the invention of fully automated machines.
How long does it take to spin the yarn from start to finish?
-Spinning the yarn from start to finish takes 48 hours.
Outlines
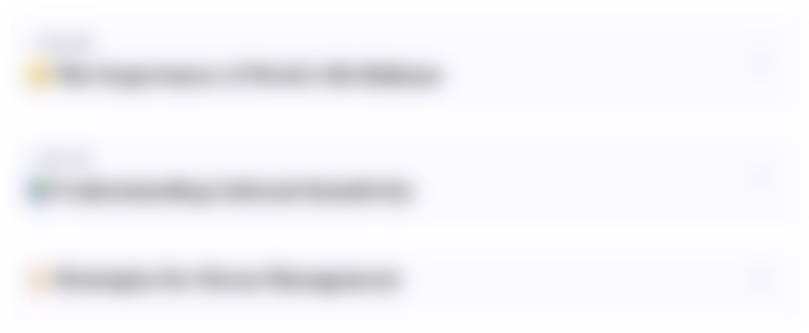
此内容仅限付费用户访问。 请升级后访问。
立即升级Mindmap
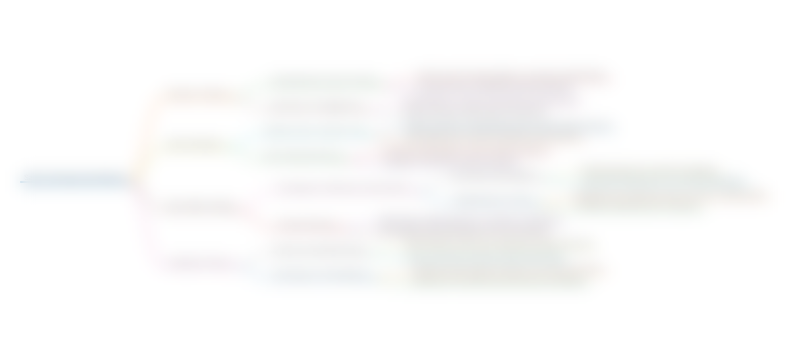
此内容仅限付费用户访问。 请升级后访问。
立即升级Keywords
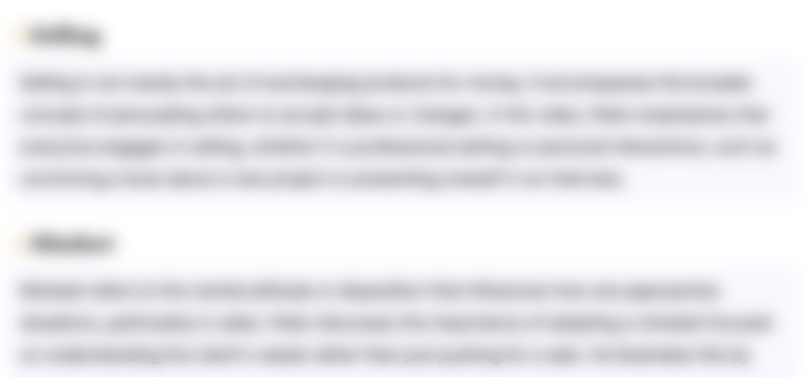
此内容仅限付费用户访问。 请升级后访问。
立即升级Highlights
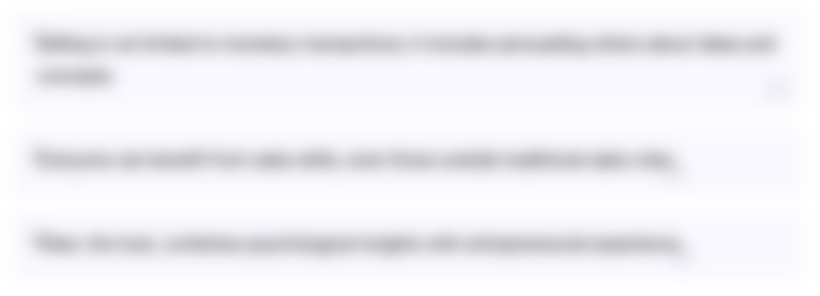
此内容仅限付费用户访问。 请升级后访问。
立即升级Transcripts
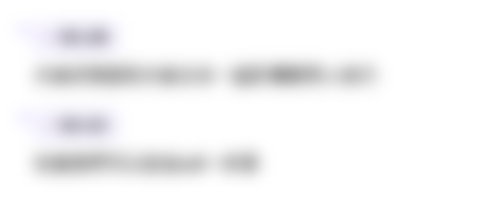
此内容仅限付费用户访问。 请升级后访问。
立即升级浏览更多相关视频
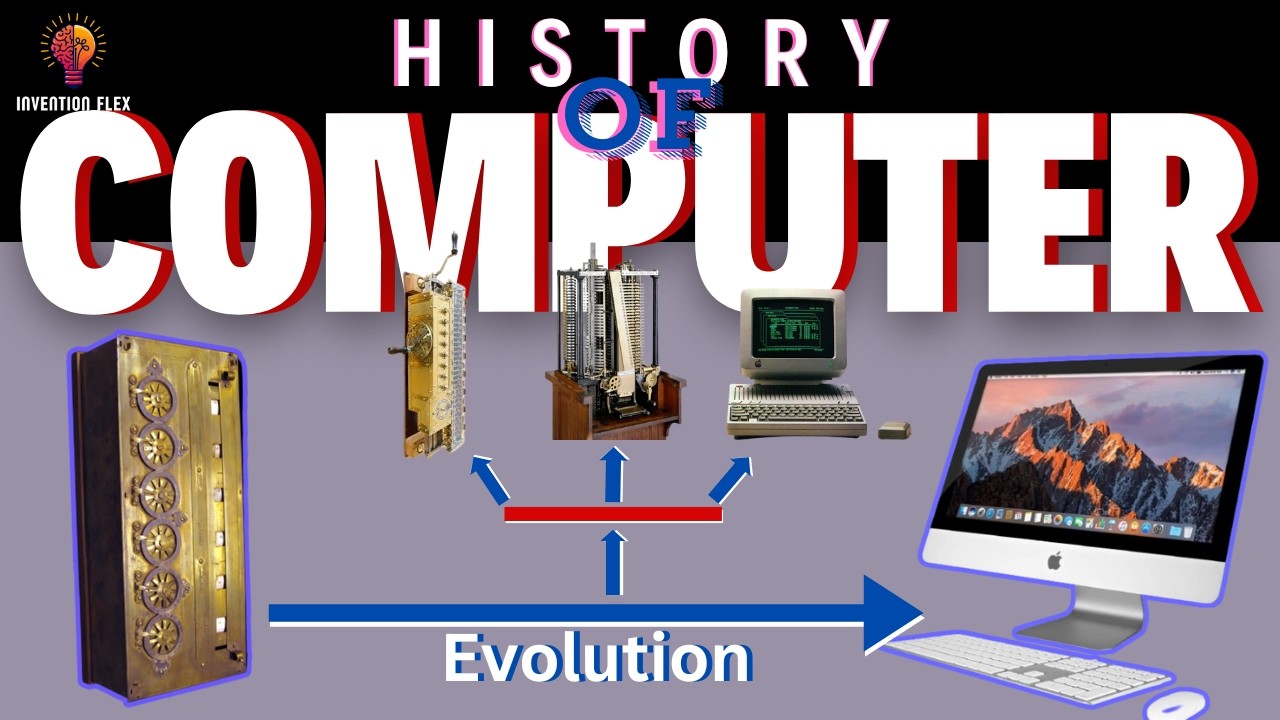
History Of Computer | Full History And Evolution Of Computers Till Date

Art of Spinning (Making of Thread from cotton)by Madhav Sahasrabudhe
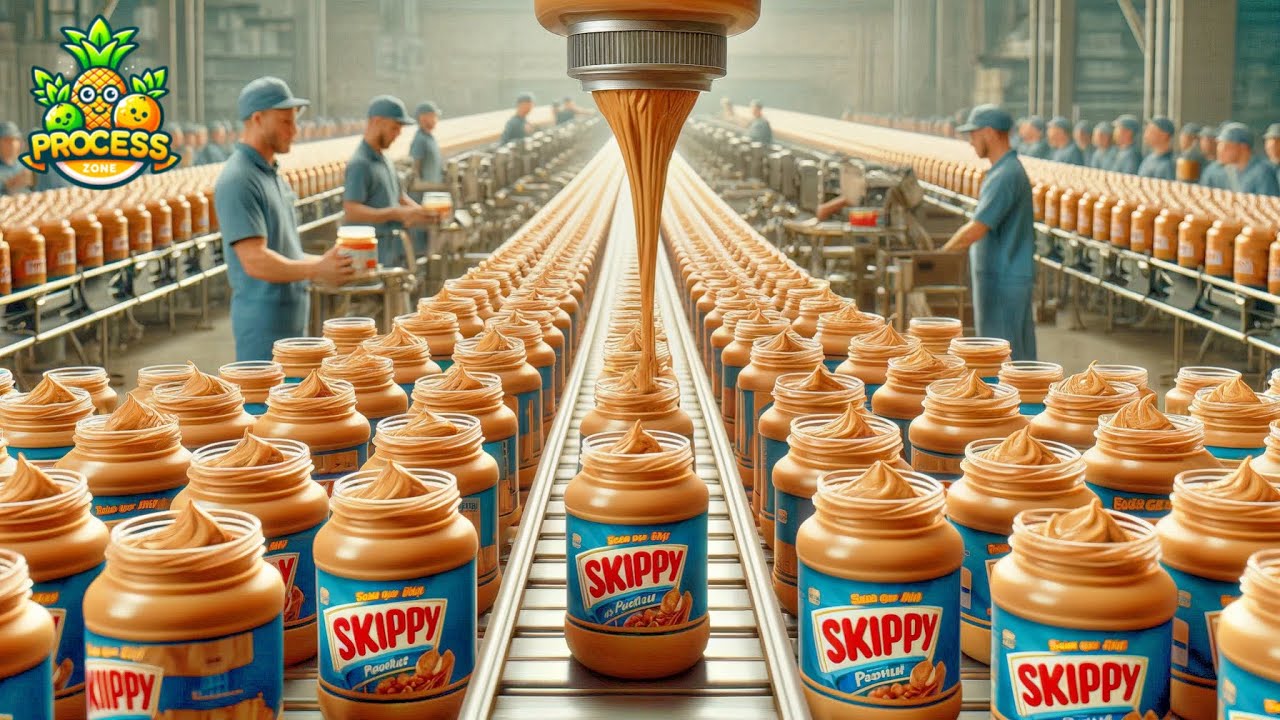
How Peanut Butter Is Made In Factory | Peanut Butter Factory Process
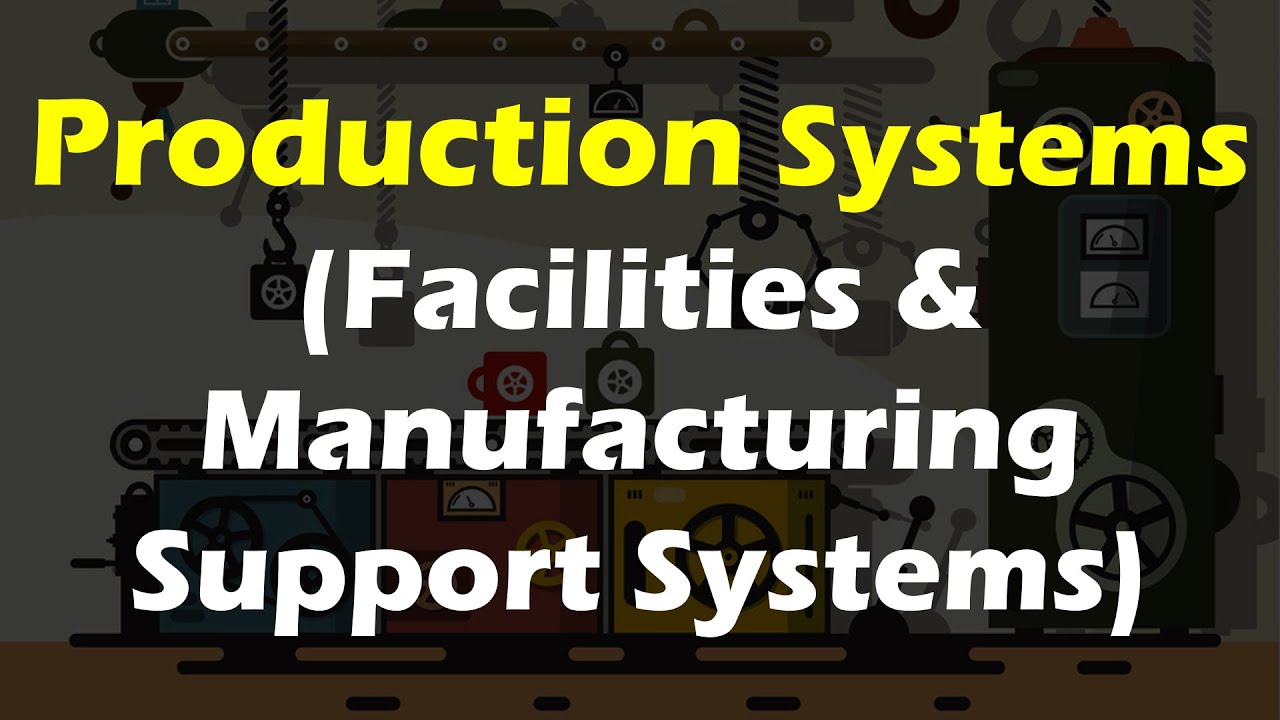
Production Systems - Facilities & Manufacturing Support Systems

Telecurso 2000 Universo da Mecânica 04 Máquinas

Video Pertemuan 1.PENDAHULUAN
5.0 / 5 (0 votes)