Understanding STAR-DELTA Starter !
Summary
TLDRThis video script delves into the necessity and practical implementation of the Star-Delta starting technique for high power rating three-phase induction motors. It explains the motor's operation, highlighting the stator and rotor's roles in producing a rotating magnetic field (RMF) that induces current in the rotor, leading to motion. The script addresses the challenge of high starting current, which can cause voltage drops and affect other devices. The Star-Delta connection is introduced as a solution, reducing the starting current by initially connecting the motor in star configuration. The use of contactors and a timer to automate the transition from star to delta configuration is also discussed, ensuring a smooth and efficient start-up process.
Takeaways
- 🔧 Three-phase induction motors are crucial in industry due to their robustness and simplicity.
- 🌟 The Star-Delta starting technique is used for high power rating induction motors to reduce inrush current.
- 🏗️ An induction motor consists of two main parts: the stator, which receives input power, and the rotor, which turns due to the rotating magnetic field (RMF).
- 🔌 The stator's three coil sets, when excited by a three-phase AC supply, produce a two-pole RMF essential for motor operation.
- 🔁 The rotor's operation is based on electromagnetic induction, where the RMF induces electricity in the rotor bars, causing it to rotate.
- ⚡ At start-up, the rotor's speed is zero, leading to a high rate of flux cut and consequently high induced EMF and current in the rotor bars.
- 🔌 The high start current in the rotor also causes a high stator current, which can lead to voltage drops and affect other devices on the line.
- 📡 The Star-Delta connection mitigates the high start current issue by initially connecting the stator coils in star configuration, reducing the input voltage and current.
- 🔄 Contactors are used to automatically switch between star and delta configurations, simplifying the process and ensuring proper motor operation.
- ⏱️ A timer controls the exact timing of when the contactors switch the motor from star to delta configuration, ensuring smooth operation.
Q & A
Why are three-phase induction motors considered the workhorse of modern industry?
-Three-phase induction motors are considered the workhorse of modern industry due to their robustness and simplicity, which make them reliable and easy to maintain.
What is the Star-Delta starting technique used for?
-The Star-Delta starting technique is used to start high power rating induction motors by reducing the initial inrush current and providing a smooth start.
What are the two main parts of an induction motor?
-The two main parts of an induction motor are the stator and the rotor.
How does the stator of a three-phase induction motor produce a rotating magnetic field?
-The stator of a three-phase induction motor produces a rotating magnetic field when connected to a three-phase power supply, which induces electricity in the rotor bars.
What is the role of the rotor in an induction motor?
-The rotor in an induction motor is like current-carrying bars immersed in a magnetic field, which induces an electromagnetic force causing the rotor to rotate in the same direction as the rotating magnetic field.
Why is a star double starter needed for starting an induction motor?
-A star double starter is needed to reduce the initial high current draw during the start of an induction motor, which can cause voltage drop and affect other devices on the same line.
How does the rotor's interaction with the rotating magnetic field change at the start of the motor?
-At the start of the motor, the rotor speed is zero, causing the rotating magnetic field to cut the rotor bars at a very high rate, inducing a high EMF and current. As the rotor speed increases, the current induced decreases to a normal value.
What is the purpose of the Star Delta Connection in an induction motor?
-The Star Delta Connection is used to reduce the initial inrush current during the start of the motor by initially connecting the stator coils in star configuration, which reduces the voltage across each coil, and then switching to delta configuration once the motor is running.
How does the use of contactors facilitate the Star Delta starting process?
-Contactors are used to automatically switch between star and delta configurations without manual rearrangement of terminals, making the starting process more practical and efficient.
What determines the exact timing of the contactor action in a Star Delta starter?
-The exact timing of the contactor action in a Star Delta starter is determined by a timer, which ensures the motor transitions from star to delta configuration at the appropriate speed.
Why is it important to understand the operation of an induction motor before discussing the Star Delta connection?
-Understanding the operation of an induction motor is imperative before discussing the Star Delta connection because it provides the necessary background on how the motor works and why the connection method is necessary for starting high power rating motors.
Outlines
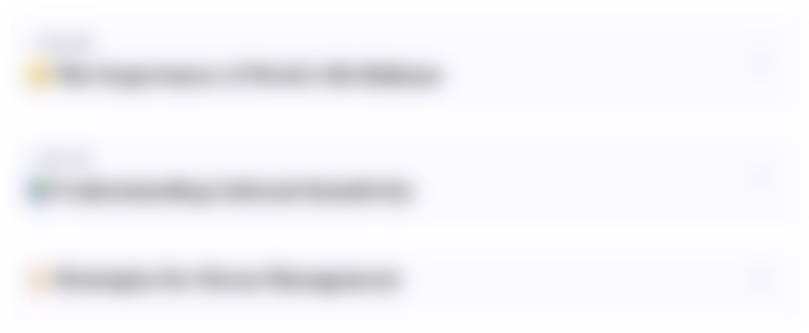
此内容仅限付费用户访问。 请升级后访问。
立即升级Mindmap
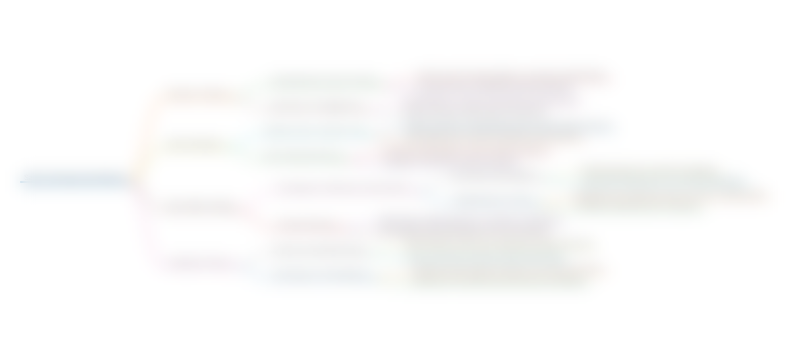
此内容仅限付费用户访问。 请升级后访问。
立即升级Keywords
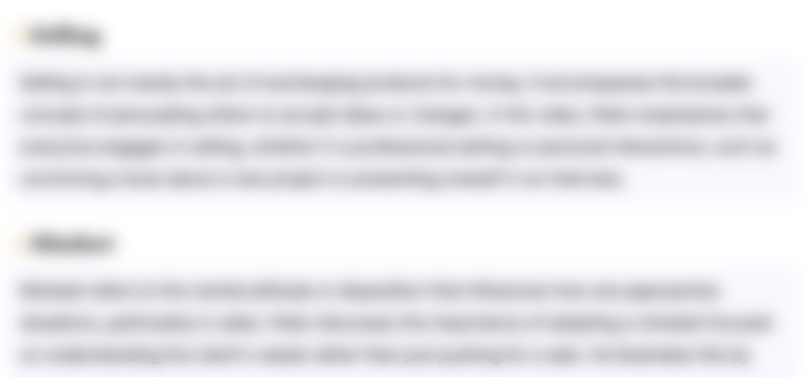
此内容仅限付费用户访问。 请升级后访问。
立即升级Highlights
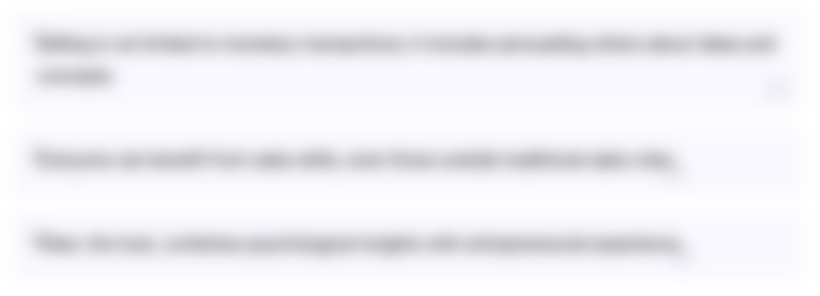
此内容仅限付费用户访问。 请升级后访问。
立即升级Transcripts
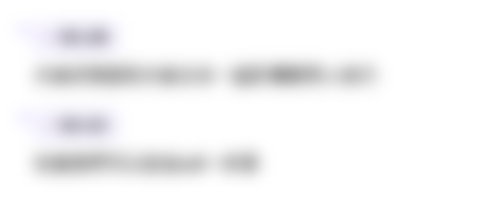
此内容仅限付费用户访问。 请升级后访问。
立即升级浏览更多相关视频
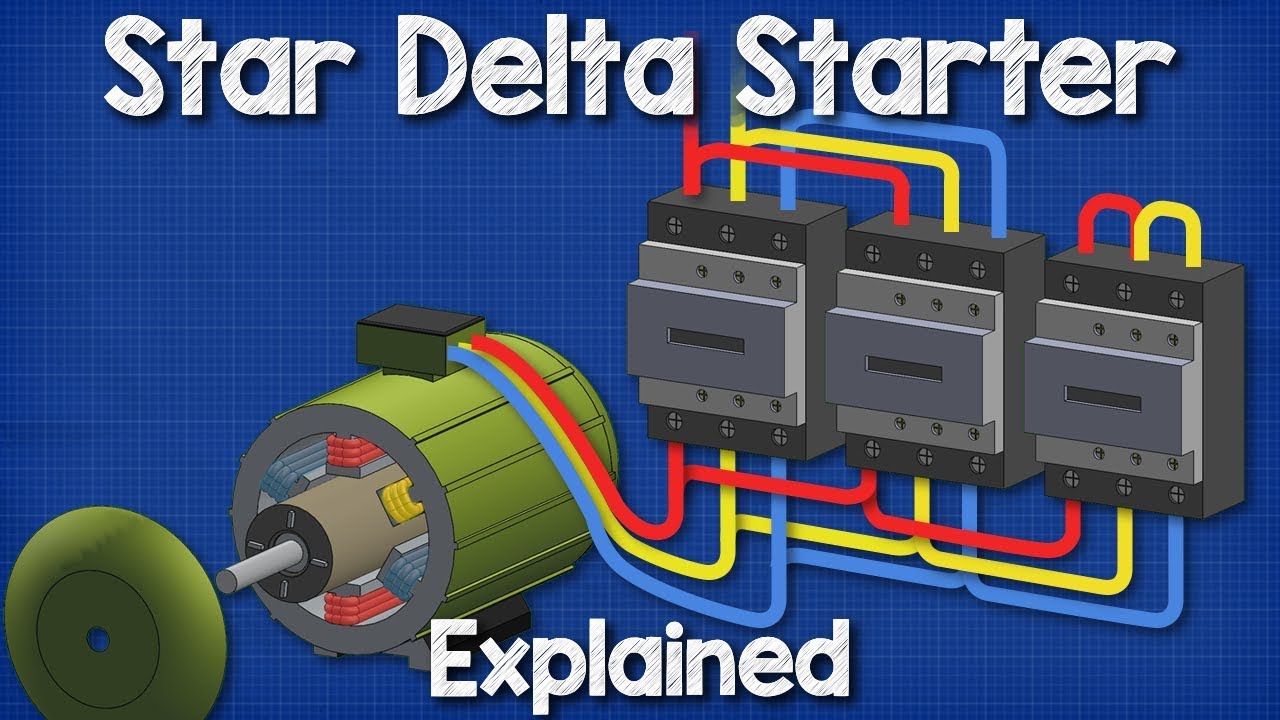
Star Delta Starter Explained - Working Principle

Why Motor Start in Star and Run in Delta| Star delta Starter| Why Motor Connected in Delta

Slip ring Induction Motor, How it works?

TotMec 4 4 Delta and Wye
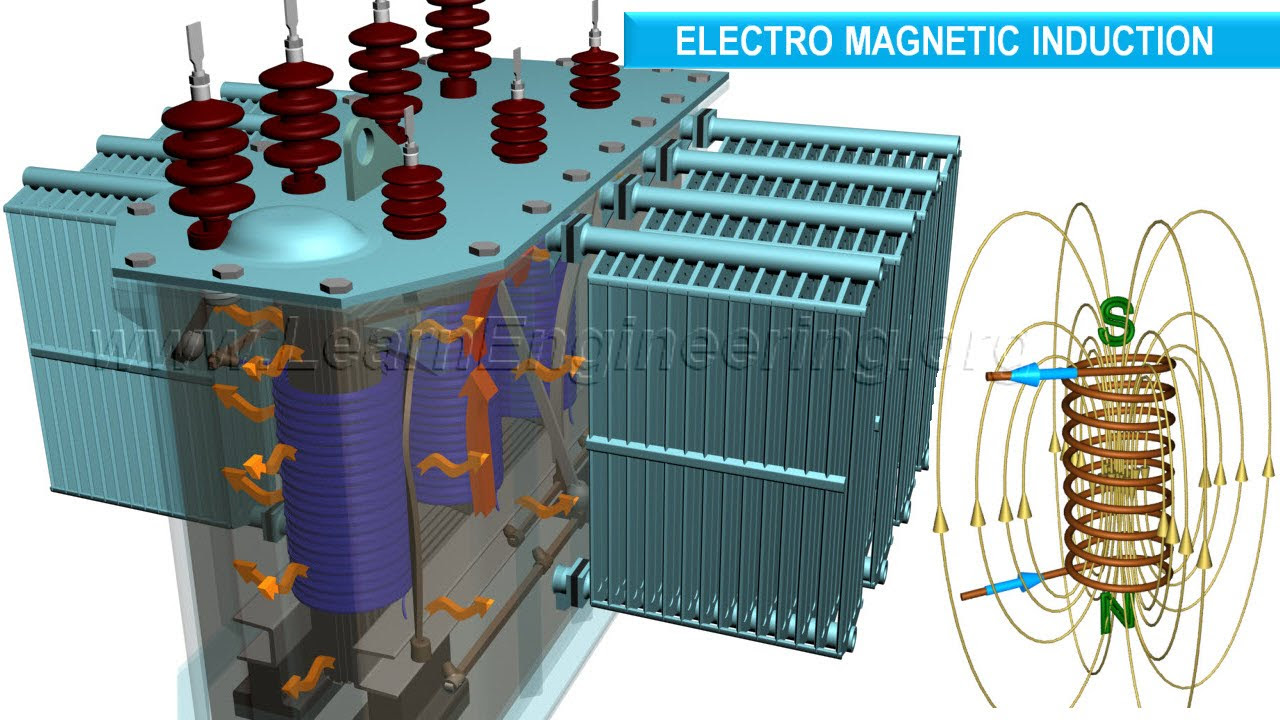
How does a Transformer work ?

Single phase Induction Motor / Capacitor start capacitor run motor / Capacitor start induction motor
5.0 / 5 (0 votes)