Compressors Part 2 - Aircraft Gas Turbine Engines #06
Summary
TLDRThis script delves into the mechanics of compressor stalls in engines, explaining how the interplay between blade rotation speed and air's axial velocity determines the angle of attack. It outlines causes like fuel flow imbalances, engine speed variances, and disrupted airflow, leading to stall indications like RPM fluctuations and increased EGT. The narrative progresses to discuss preventative systems like variable inlet guide vanes and compressor bleeds, and the evolution of multi-spool compressors to enhance operational flexibility and reduce stall risks.
Takeaways
- 🔍 The angle of attack of a compressor blade is influenced by the axial velocity of air and the rotational speed of the blade.
- 🚫 A compressor stall can occur due to an imbalance between the rotational speed of the blade and the axial velocity of air, caused by factors like excessive fuel flow or engine operation outside design parameters.
- 🛠️ To demonstrate the effect of imbalance, the script suggests using buttons to adjust engine RPM and observe changes in blade angle of attack.
- ⚙️ Engine overspeed or underspeed can alter the rotational speed of compressor blades, affecting the angle of attack and potentially causing stall.
- 🌀 Turbulent air entering the engine or damaged compressor components can disrupt the airflow and lead to a stall by changing the axial velocity.
- 📈 Compressor stall indicators include fluctuations in engine RPM, increased engine vibration, and a rise in exhaust gas temperature (EGT).
- 🔁 Compressor stall is a progressive phenomenon that can start at a single blade and spread if unaddressed, potentially leading to a surge.
- 🛑 In case of a surge, the throttle of the affected engine must be closed slowly, and the cause investigated to prevent catastrophic failure.
- 🛠️ Systems like variable inlet guide vanes, variable stator vanes, compressor bleeds, and multi-spool compressors are designed to prevent compressor stalls and surges.
- ⚙️ Variable inlet guide vanes (VIVs) and variable stator vanes (VSVs) help maintain the correct angle of attack by adjusting the airflow path into the compressor.
- 💨 Compressor bleed systems allow excess air to escape from intermediate stages to maintain optimal airflow and prevent choking, thus reducing the risk of stall.
Q & A
What is the angle of attack of a compressor blade influenced by?
-The angle of attack of a compressor blade is influenced by the axial velocity of the air passing across it and the rotational speed of the blade.
What can cause an imbalance leading to compressor stall?
-An imbalance leading to compressor stall can be caused by an imbalance between the rotational speed of the blade and the axial velocity of the air passing across it, which can occur due to various reasons such as excessive fuel flow, engine operation outside design parameters, or turbulent airflow to the engine intake.
How can excessive fuel flow lead to compressor stall?
-Excessive fuel flow, possibly caused by abrupt throttle opening, can generate back pressure in the combustion chamber, leading to a reduction in the axial velocity of air through the compressor, potentially causing a stall.
What is the effect of engine operation outside its design RPM parameters?
-Operating the engine above or below its design RPM parameters can alter the rotational speed of the compressor blades, which may either increase or decrease the angle of attack to a point where blade efficiency is compromised, leading to a stall.
What are the indications of a compressor stall?
-Indications of a compressor stall can include fluctuations in engine RPM, increased engine vibration, audible noise in the cockpit, and an increase in exhaust gas temperature (EGT).
How does a compressor stall progress?
-Compressor stall is a progressive phenomenon that can initially occur at just one blade and, if unaddressed, can worsen to affect the whole engine, potentially leading to a complete breakdown of airflow called a surge.
What is the significance of a surge in an engine?
-A surge signifies a complete breakdown of airflow through the engine, which can cause an instantaneous reversal of airflow, loud bangs, and potentially catastrophic damage to the compressor rotor blades if not managed properly.
What are some systems designed to prevent compressor stall or surge?
-Systems designed to prevent compressor stall or surge include variable inlet guide vanes (VIVs), variable stator vanes, compressor bleeds, and multi-spool compressors.
How do variable inlet guide vanes help in preventing compressor stall?
-Variable inlet guide vanes can be automatically pivoted to vary the path of the airflow into the compressor, maintaining the proper relationship between the compressor rotational speed and the velocity of the airflow, thus preventing stall.
What is the purpose of compressor bleeds in an engine?
-Compressor bleeds allow excess volume of air to escape from intermediate stages of the compressor, reducing the choking effect and maintaining the axial velocity of the air closer to the optimum value, thereby reducing the likelihood of compressor stall.
Why are multi-spool compressors used in engines?
-Multi-spool compressors, where each compressor section is driven by its own turbine, allow for greater operational flexibility over a wider RPM range, reducing the chance of compressor stall by maintaining the optimum angle of attack over a broader range of conditions.
Outlines
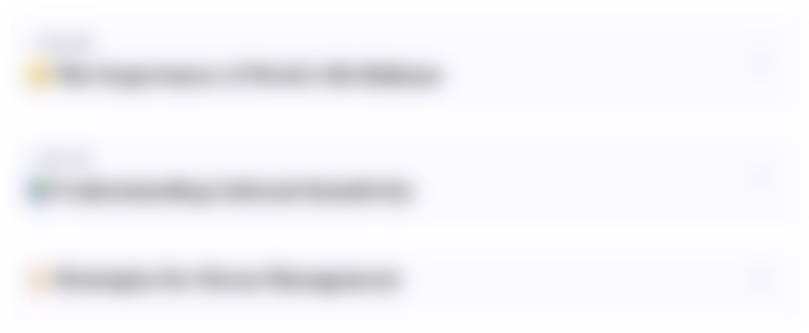
此内容仅限付费用户访问。 请升级后访问。
立即升级Mindmap
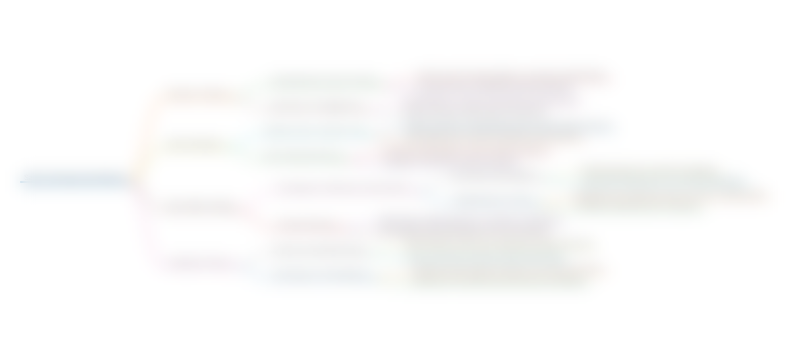
此内容仅限付费用户访问。 请升级后访问。
立即升级Keywords
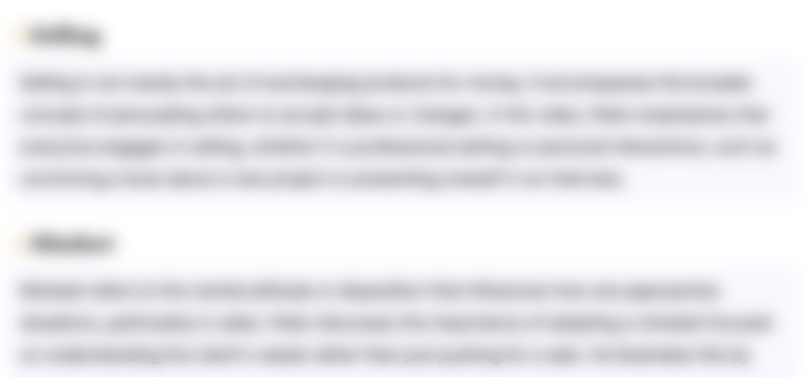
此内容仅限付费用户访问。 请升级后访问。
立即升级Highlights
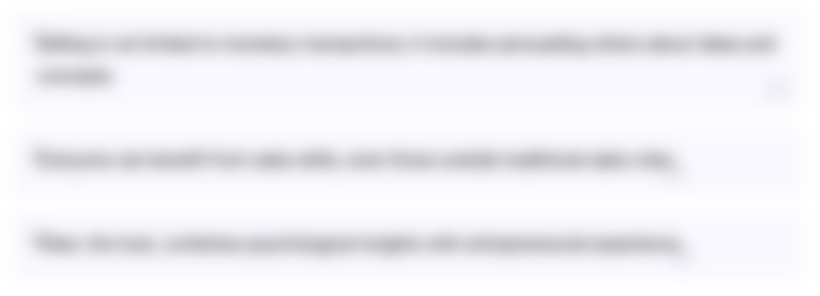
此内容仅限付费用户访问。 请升级后访问。
立即升级Transcripts
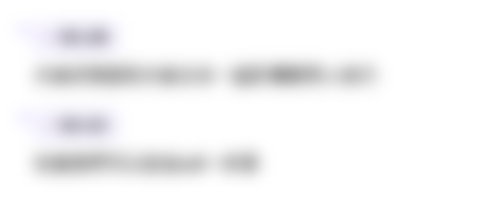
此内容仅限付费用户访问。 请升级后访问。
立即升级5.0 / 5 (0 votes)