Basic Hydraulic Systems - Hydraulics - Airframes & Aircraft Systems #6
Summary
TLDRThis lesson introduces the components of a basic hydraulic system, focusing on the open center and closed systems used in aircraft. The open center system, suitable for light aircraft, allows only one service at a time and operates with a pump that runs in an offloaded condition. In contrast, the closed system, common in large aircraft, enables multiple services simultaneously and maintains operating pressure. Key components include a reservoir, pump, selector valves, actuators, filters, and a relief valve. The lesson also explains hydraulic lock and the operation of pumps in both systems.
Takeaways
- 🔧 Most aircraft hydraulic systems are active, with a pump supplying pressure, unlike the passive Brahma press system.
- 💧 There are two main types of active hydraulic systems: open center and closed center systems.
- 📦 The six main components of hydraulic systems are reservoir, pump, selector or control valves, actuator, filters, and relief valve.
- 🚀 The open center system is simpler and used in light aircraft, but it can only operate one service at a time.
- 🔄 In the open center system, fluid flows through selector valves in sequence until it reaches the last valve, then returns to the reservoir.
- 🛠️ The relief valve in the open center system is crucial for relieving excess pressure if the selector is not returned to neutral.
- 🔑 The closed system is used in large aircraft and allows multiple services to operate simultaneously, limited only by the pump's volume flow capacity.
- 🔄 In closed systems, operating pressure is maintained, and mechanisms like automatic cutout valves or variable volume pumps prevent pump overload.
- 🔒 The hydraulic lock in closed systems locks fluid on both sides of the actuator, preventing any uncommanded movement.
- 🔌 Some light aircraft use a hydraulic power pack with an electrically driven pump and an accumulator for simpler hydraulic operations.
Q & A
What are the two types of basic hydraulic systems mentioned in the script?
-The two types of basic hydraulic systems mentioned are the open center system and the closed system.
What is the main disadvantage of the open center hydraulic system?
-The main disadvantage of the open center hydraulic system is that only one service can be operated at a time.
What are the six main components common to both open center and closed hydraulic systems?
-The six main components common to both systems are a reservoir of oil, a pump, selector or control valves, actuators, filters, and a relief valve.
How does the fluid flow in an open center hydraulic system when no service is operating?
-In an open center hydraulic system, if no service is operating, the fluid flows from the pump through the pressure filter to the selector valve, then through the central port to the next selector valve, and this can continue for as many valves as required, finally returning to the reservoir.
What happens when a user system is selected in an open center hydraulic system?
-When a user system is selected, the fluid is directed to the actuator, which moves, and the fluid from the other side of the actuator returns to the reservoir via the central port of the selector valve.
What is the purpose of the relief valve in a hydraulic system?
-The relief valve relieves excess pressure if the selector is not returned to its neutral position.
Why is the closed hydraulic system used on almost all large aircraft?
-The closed hydraulic system is used on almost all large aircraft because it allows multiple services to be operated at the same time, limited only by the volume flow capacity of the pump.
How does the closed system prevent overloading the pump?
-In systems with a fixed volume, constant delivery pump, an automatic cutout valve is used to divert pump output to the reservoir when pressure has built up to normal operating pressure. In other systems, a variable volume, constant pressure pump is used, which automatically reduces delivery flow as pressure increases.
What is the significance of returning the selector valve to neutral in a closed hydraulic system?
-In a closed hydraulic system, it is not as critical to return the selector valve to neutral once the operation is complete, as the pump control system is designed to handle the pressure increase. However, returning the selector valve to neutral creates a hydraulic lock across the actuator, preventing any uncommanded movement.
What is a hydraulic lock and why is it important?
-A hydraulic lock occurs when the fluid is locked in on both sides of the actuator, preventing any undemanding movement because the fluid is incompressible. It is important for maintaining the position of the actuator and ensuring stability.
Outlines
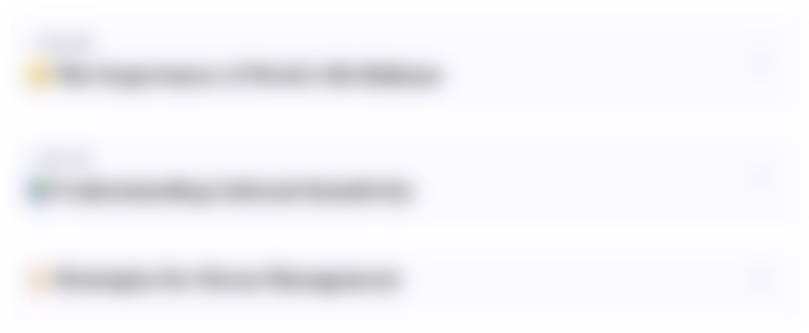
此内容仅限付费用户访问。 请升级后访问。
立即升级Mindmap
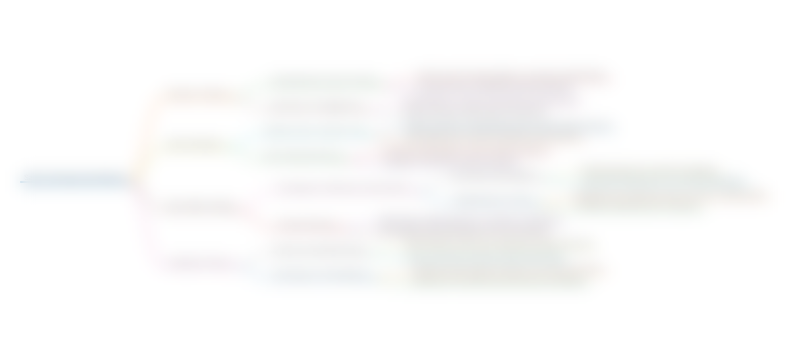
此内容仅限付费用户访问。 请升级后访问。
立即升级Keywords
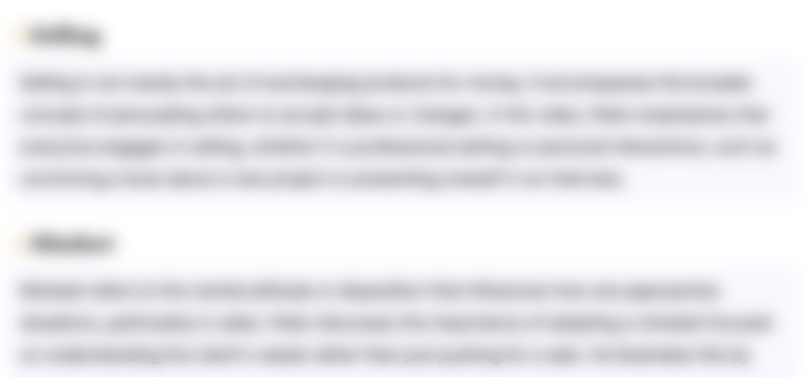
此内容仅限付费用户访问。 请升级后访问。
立即升级Highlights
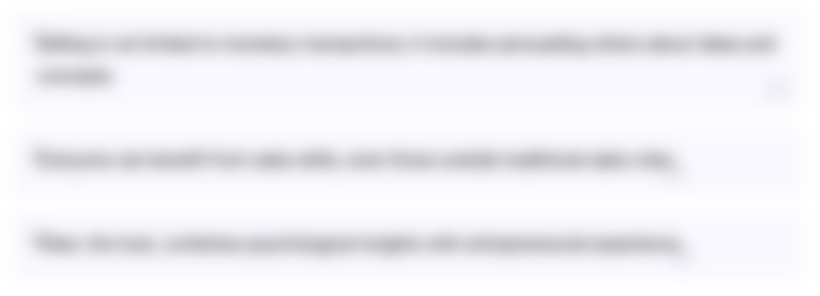
此内容仅限付费用户访问。 请升级后访问。
立即升级Transcripts
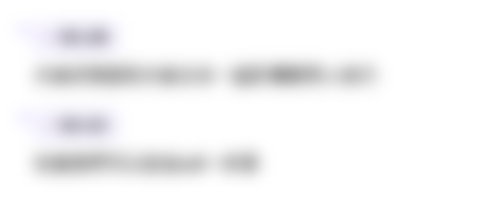
此内容仅限付费用户访问。 请升级后访问。
立即升级浏览更多相关视频

Hydraulic Pumps - Hydraulics - Airframes & Aircraft Systems #7
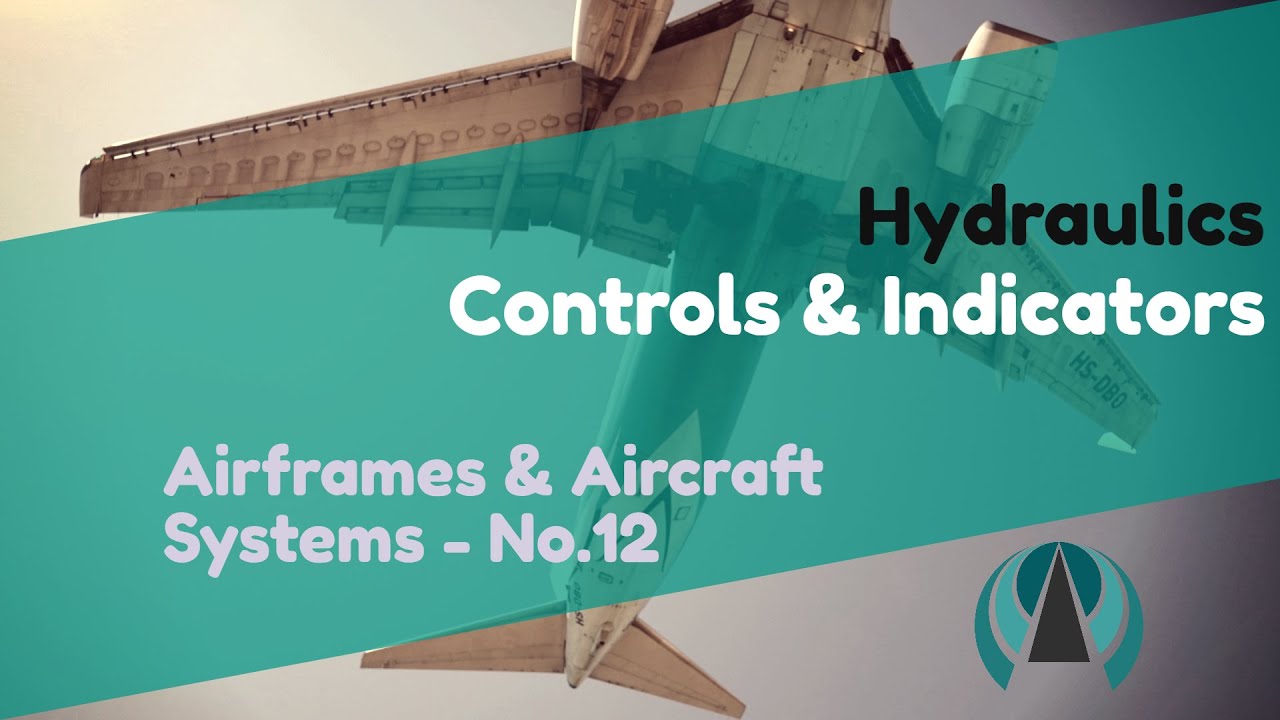
Controls & Indicators - Hydraulics - Airframes & Aircraft Systems #12

Pressure Control - Hydraulics - Airframes & Aircraft Systems #10
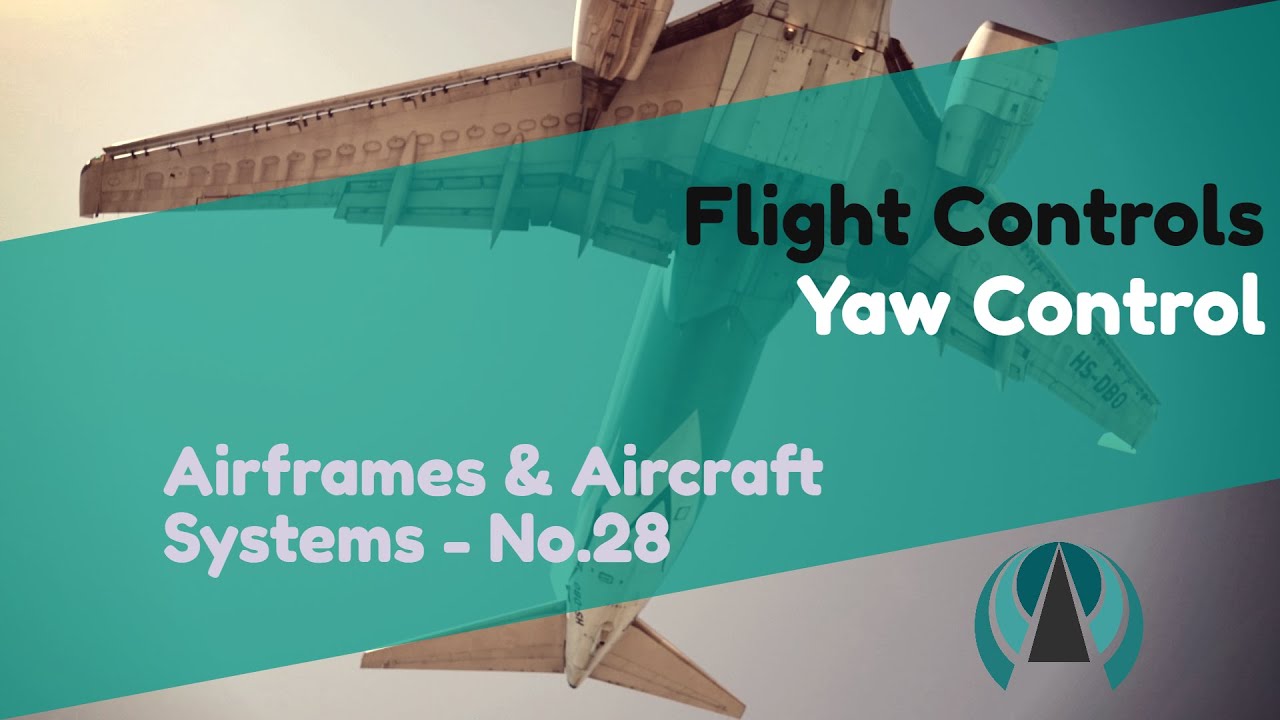
Yaw Control - Flight Controls - Airframes & Aircraft Systems #28
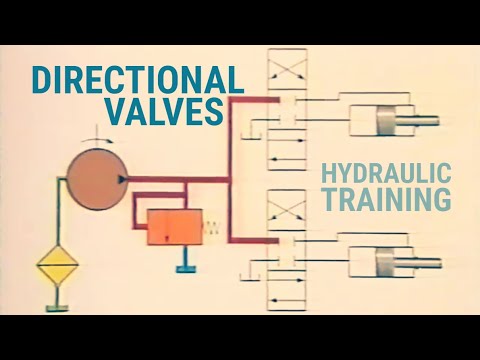
Hydraulic Training Series - Chapter 5 - Directional Valves

Hydraulics - Basic Principles of Hydromechanics - Airframes & Aircraft Systems #4
5.0 / 5 (0 votes)