Safety Benchmarking - A Case Study
Summary
TLDRThe script from the 'Safety Benchmarking with Dyne McDermott' video highlights the company's exceptional safety record, achieved through a culture change that empowers employees. By integrating behavior-based safety, direct observation, and a no-punishment policy, McDermott reduced incidents dramatically without excessive costs. The video offers an in-depth look at their safety program, emphasizing the importance of employee involvement and management support in fostering a proactive safety culture.
Takeaways
- 📈 The US Bureau of Labor Statistics reported over four million workplace incidents in 2006, costing hundreds of billions of dollars, despite extensive safety measures.
- 🏆 Deine McDermott Petroleum has achieved exceptional safety records, winning the Robert W Campbell award, the Baldrige award, and OSHA VPP star status at all four of its facilities.
- 👷♂️ The company's safety program involves a combination of behavior-based safety, direct observation, employee empowerment, and a no punishment atmosphere.
- 🔧 Management at Deine McDermott supports employee ideas for safety improvements, ensuring they are vetted and implemented efficiently.
- 🤔 The program delves into the 'why' behind unsafe behaviors, aiming to understand and address the root causes of such actions.
- 🙅♂️ Punishing unsafe behaviors is avoided to prevent a culture of fear and to encourage open communication about safety concerns.
- 👥 Employee committees play a crucial role in identifying and resolving safety issues through various tools and techniques.
- 🛠️ Direct observation is used to keep safety at the forefront of every employee's mind, making them more safety-conscious and aware.
- 🔄 A culture change is emphasized as the key to achieving safety excellence, which is more easily spoken of than attained but is very reachable.
- 💡 Involvement of every level of employee is crucial for the cultural change to start and for seeing tangible results in safety improvements.
- 🏢 The success of Deine McDermott's safety program is a testament that safety excellence can be achieved through employee involvement and management support.
Q & A
What was the reported number of workplace-related incidents in private industry in 2006 according to the US Bureau of Labor Statistics?
-In 2006, over four million workplace-related incidents were reported in private industry.
What are some of the common safety efforts mentioned that are implemented in factories and offices?
-Common safety efforts include safety policies, rules, procedures, committees, signage, and other safety-related initiatives.
Despite extensive safety efforts, why do workplace incidents and accidents continue to occur?
-The script suggests that despite extensive safety efforts, incidents and accidents may continue because they could be seen as an unavoidable part of life, regardless of the efforts made.
Which company is highlighted in the script for achieving a high level of safety excellence?
-Dyne McDermott Petroleum is highlighted for achieving an unexpected level of safety excellence.
What prestigious safety awards has Dyne McDermott Petroleum received?
-Dyne McDermott Petroleum has received the Robert W. Campbell Award for Safety Excellence, the Baldrige Award, and achieved OSHA VPP Star status at each of its four facilities.
What approach did Dyne McDermott use to drastically reduce their safety incidents?
-Dyne McDermott used a combination of behavior-based safety, including direct observation, peer reinforcement, employee empowerment, and a no-punishment atmosphere, along with strong management support to reduce their safety incidents.
What was the result of Dyne McDermott's safety program in terms of incident reduction?
-The safety incidents at Dyne McDermott were reduced from over 50 a year to just 6 in a very short period of time.
How does Dyne McDermott's program ensure that safety remains a priority among employees?
-The program keeps safety in the forefront of employees' minds through continuous training, behavior-based safety processes, and direct observation, making safety a daily focus.
What role does management play in Dyne McDermott's safety program?
-Management plays a crucial role by avoiding punishment for unsafe behaviors, supporting employee ideas for safety improvements, and ensuring that safety-related suggestions are implemented quickly and effectively.
What is one of the key factors that contributed to the cultural change in safety at Dyne McDermott?
-A key factor was involving every level of employee in the safety process, which fostered a sense of ownership and responsibility among workers, leading to significant cultural change.
Outlines
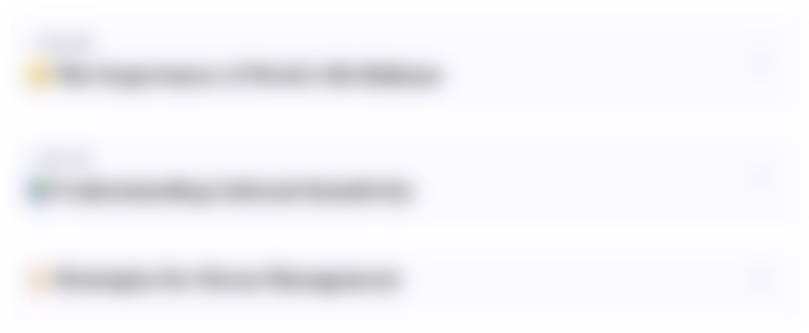
此内容仅限付费用户访问。 请升级后访问。
立即升级Mindmap
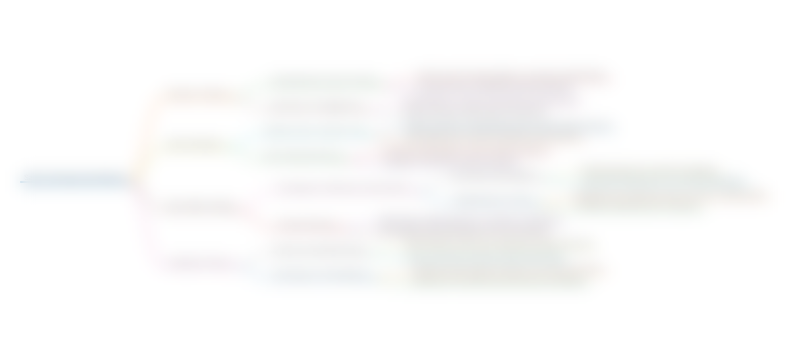
此内容仅限付费用户访问。 请升级后访问。
立即升级Keywords
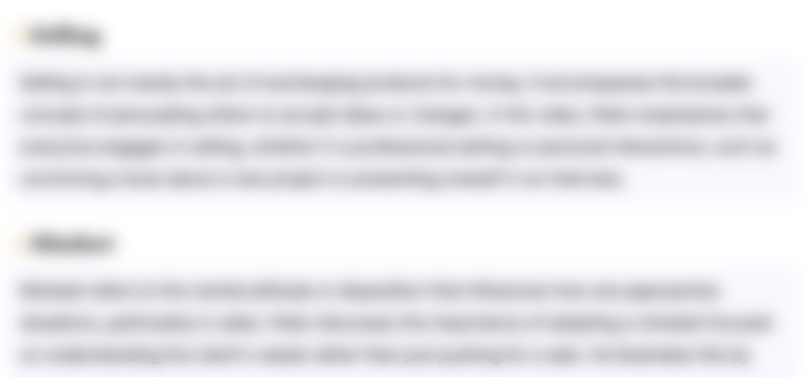
此内容仅限付费用户访问。 请升级后访问。
立即升级Highlights
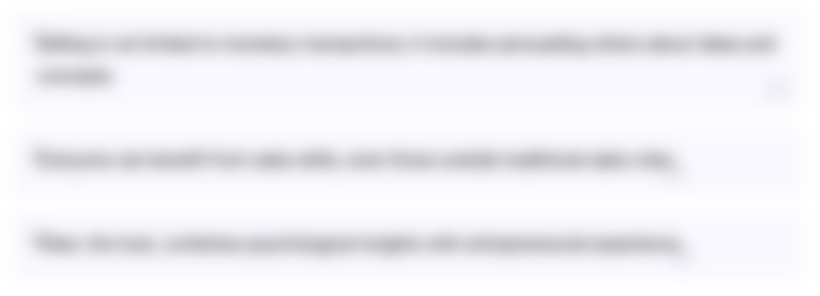
此内容仅限付费用户访问。 请升级后访问。
立即升级Transcripts
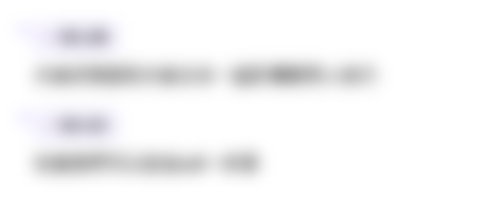
此内容仅限付费用户访问。 请升级后访问。
立即升级浏览更多相关视频
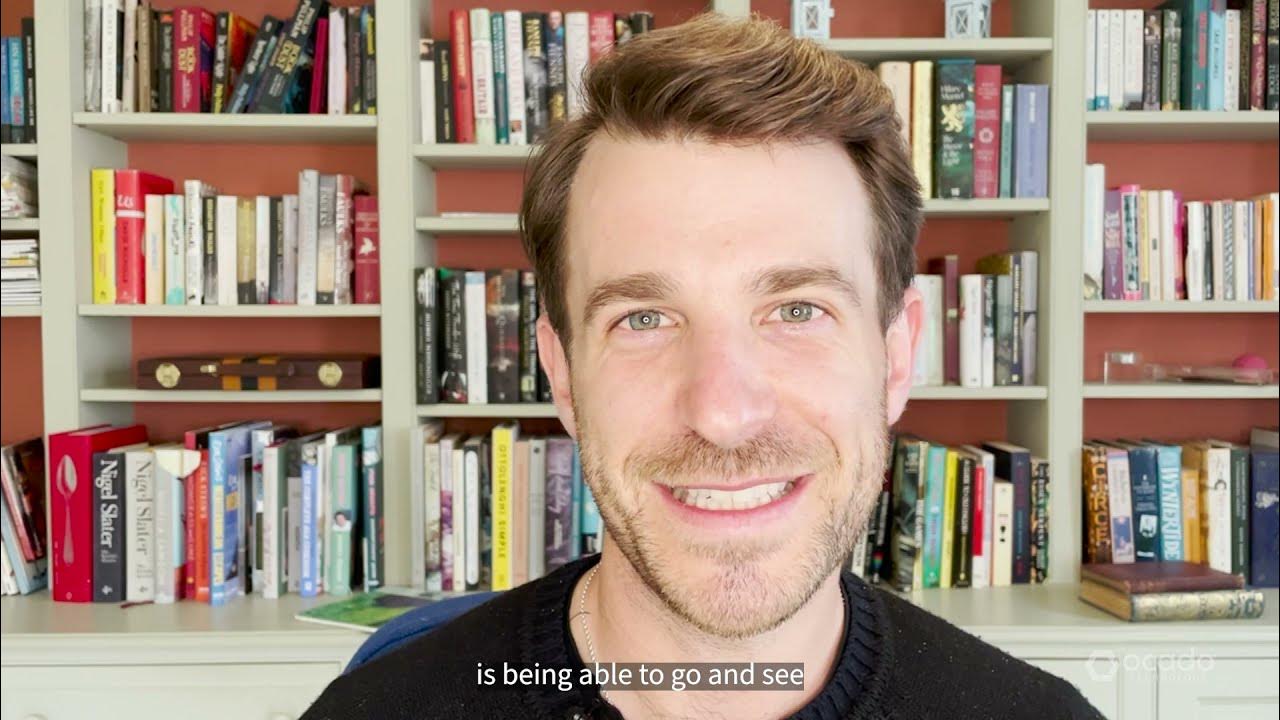
Starting Your Ocado Technology Career

Manufacturing Safety Employee Video
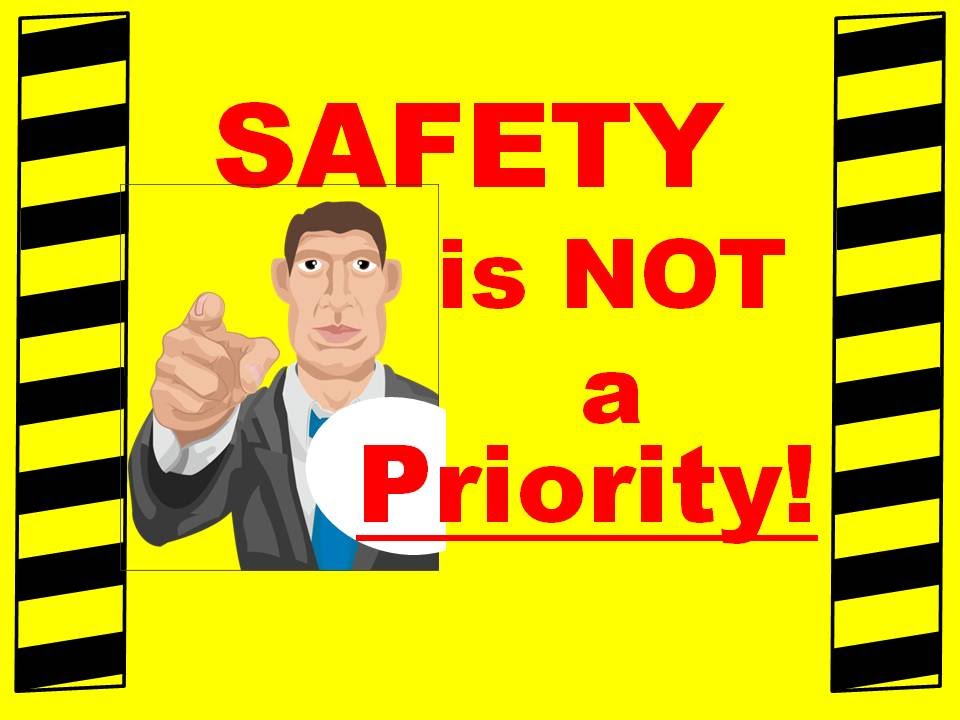
Safety is NOT a Priority - Safety Training Video - Preventing Workplace Accidents and Injuries
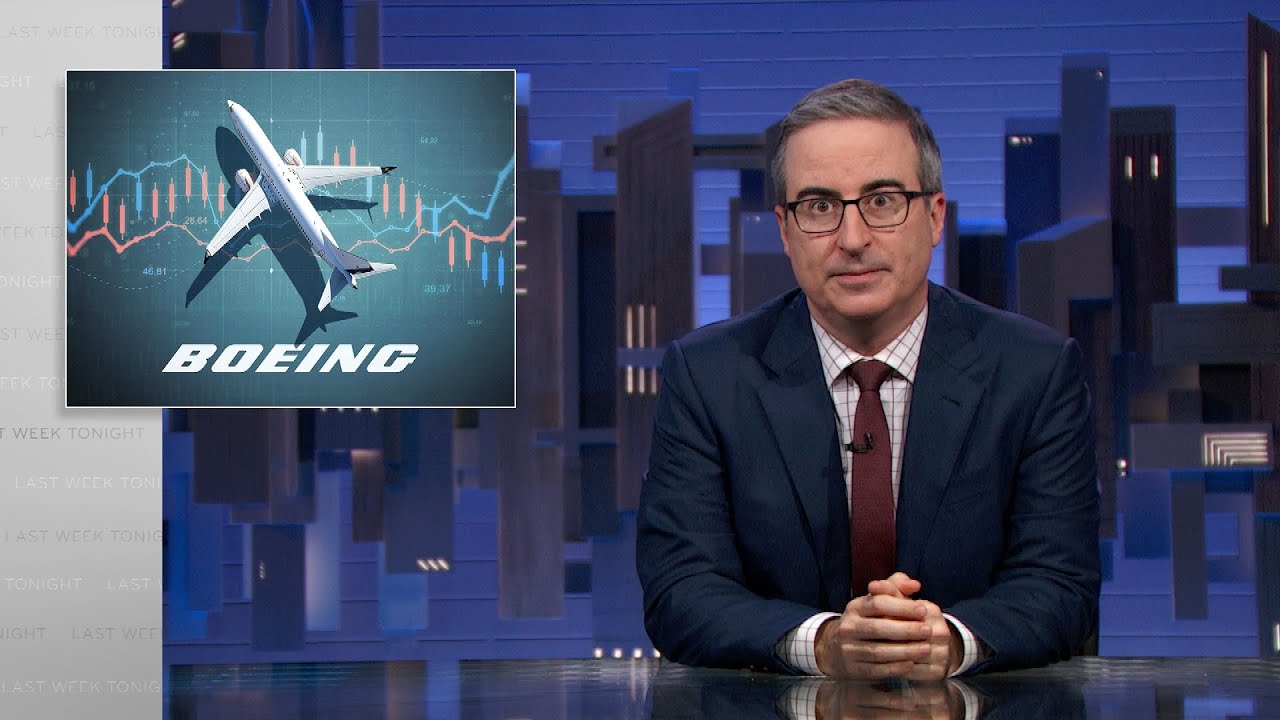
Boeing: Last Week Tonight with John Oliver (HBO)

Workplace Safety and Safety Culture
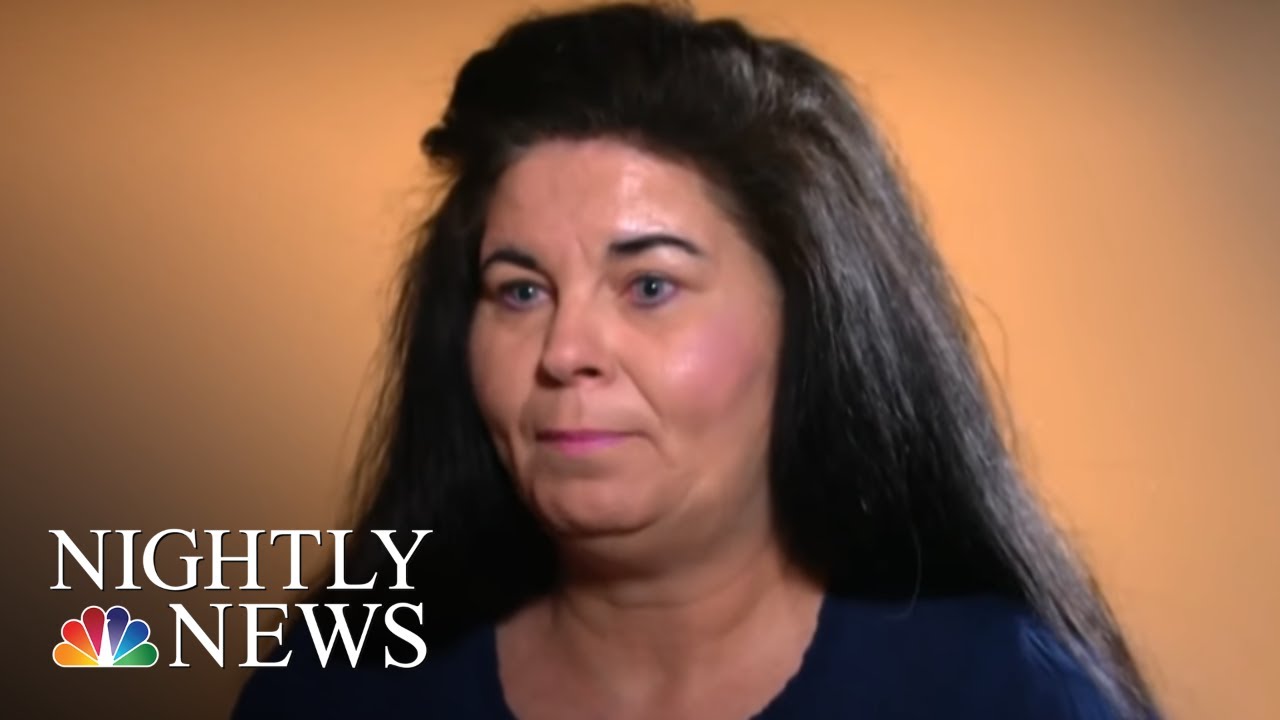
Amazon Employees Speak Out About Workplace Conditions | NBC Nightly News
5.0 / 5 (0 votes)