Double Sheet Sensors for Reliable Double Material Detection
Summary
TLDRThe video script discusses the importance of accurate material feeding in production processes, particularly in industries like printing, battery, and cardboard production. It highlights the role of ultrasonic double sheet sensors, which consist of a transmitter and receiver, in preventing errors caused by multiple sheets being fed simultaneously. The script explains the working principle of these sensors, emphasizing the need for precise alignment to detect and differentiate between single and double layers of material effectively. It concludes by promoting the technology leader Pebble and Fox's optimized portfolio of double material detection systems for various applications.
Takeaways
- 🔉 Ultrasonic sensors are used for double material detection in machines that require continuous material feeding.
- 📏 Double sheet sensors consist of a transmitter and a receiver to ensure the detection of only one sheet at a time.
- 🛡️ Errors in material feed are prevented by the sensors, which are crucial for reliable production.
- 🔊 The ultrasonic transmitter emits sound waves that interact with the material surface and are reflected back.
- 🔍 If a second layer of material is present, the signal amplitude becomes highly muted, indicating a double sheet.
- 📡 Receivers pick up a small amplitude level which helps in detecting and distinguishing double layers from single layers.
- 🧭 Precise alignment of the transmitter and receiver is essential for the sensor to function correctly.
- 🎯 Both ultrasonic transducers are most sensitive at their center, requiring the sound beam to meet at this point for maximum amplitude.
- 📏 Minor deviations in alignment can lead to a significant loss of amplitude, affecting the sensor's performance.
- 🛠️ Accurate angular alignment is critical; inaccuracies of more than one degree can impact the sensor's reliability.
- 📚 Technology leader Pebble and Fox offers an optimized portfolio of double material detection systems for various applications.
Q & A
What is the primary function of ultrasonic sensors in the context of the video?
-The primary function of ultrasonic sensors in the video is to detect double sheets of material to prevent errors in the material feed of printing, folding, and die-cutting machines.
How do ultrasonic sensors detect double layers of material?
-Ultrasonic sensors detect double layers of material by emitting sound waves from a transmitter. These waves are partially reflected by the material's surface, with the remainder penetrating the material and being decoupled back into the air. If another layer of material is present, the signal amplitude becomes highly muted, allowing the sensors to distinguish between single and double layers.
Why is precise alignment of the transmitter and receiver essential in double sheet detection?
-Precise alignment is essential because both ultrasonic transducers are most sensitive at their center. Proper alignment ensures that the sound beam from the emitting transducer meets the receiving transducer at the central point, enabling the largest possible amplitude measurement and covering the widest material spectrum.
What impact do axial deviations have on the performance of the double sheet detection system?
-Axial deviations of more than one millimeter can lead to a significant loss of amplitude, negatively impacting the performance of the double sheet detection system.
How does angular misalignment affect the ultrasonic sensor system?
-Angular misalignment of more than one degree can cause a significant loss of amplitude, reducing the reliability and performance of the double sheet detection system.
What industries can benefit from the double material detection systems discussed in the video?
-Industries such as printing, battery production, and cardboard production can benefit from the double material detection systems discussed in the video.
What is the significance of the sound beam's alignment with the receiving transducer?
-The alignment of the sound beam with the receiving transducer is significant because it ensures the largest possible amplitude measurement, which is crucial for accurate double sheet detection.
What might happen if the alignment of the transmitter and receiver is not precise?
-If the alignment is not precise, it can lead to reduced amplitude measurements, making the system less reliable in detecting double layers of material.
Why is it important to ensure that only one sheet is inserted into the machines at a time?
-It is important to ensure that only one sheet is inserted at a time to guarantee reliable production and to prevent errors in the material feed, which can lead to machine malfunctions or production defects.
What role does Pebble and Fox play in the context of the video?
-Pebble and Fox are described as technology leaders offering an optimized portfolio of double material detection systems for various industries, including printing and cardboard production.
Outlines
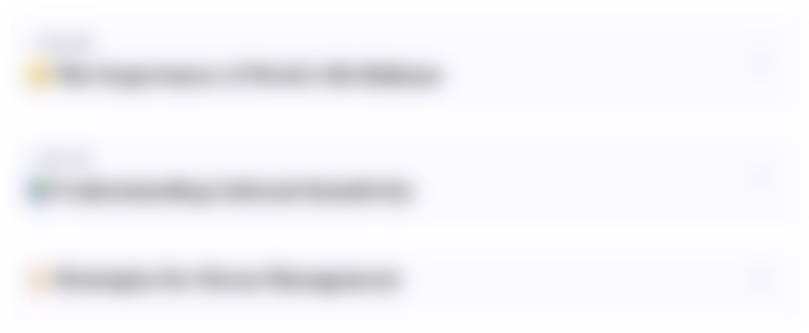
This section is available to paid users only. Please upgrade to access this part.
Upgrade NowMindmap
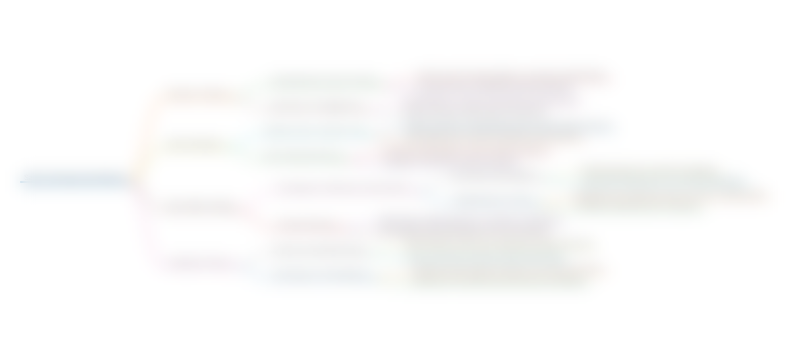
This section is available to paid users only. Please upgrade to access this part.
Upgrade NowKeywords
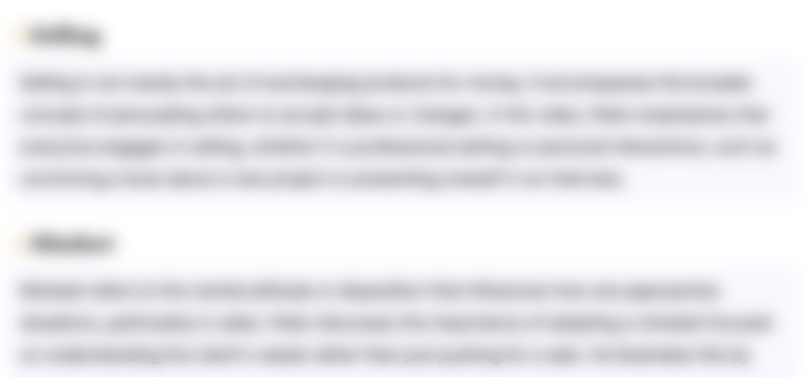
This section is available to paid users only. Please upgrade to access this part.
Upgrade NowHighlights
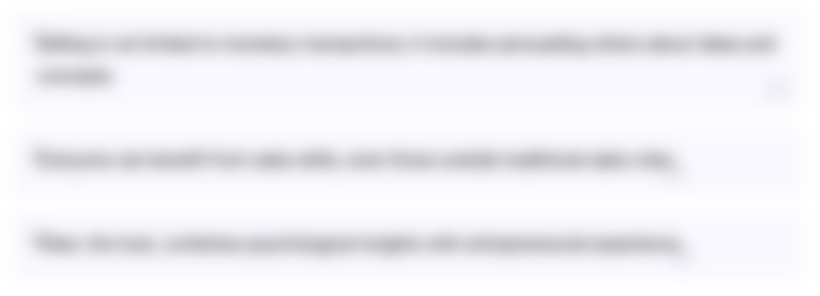
This section is available to paid users only. Please upgrade to access this part.
Upgrade NowTranscripts
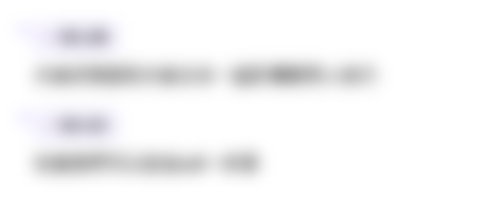
This section is available to paid users only. Please upgrade to access this part.
Upgrade NowBrowse More Related Video
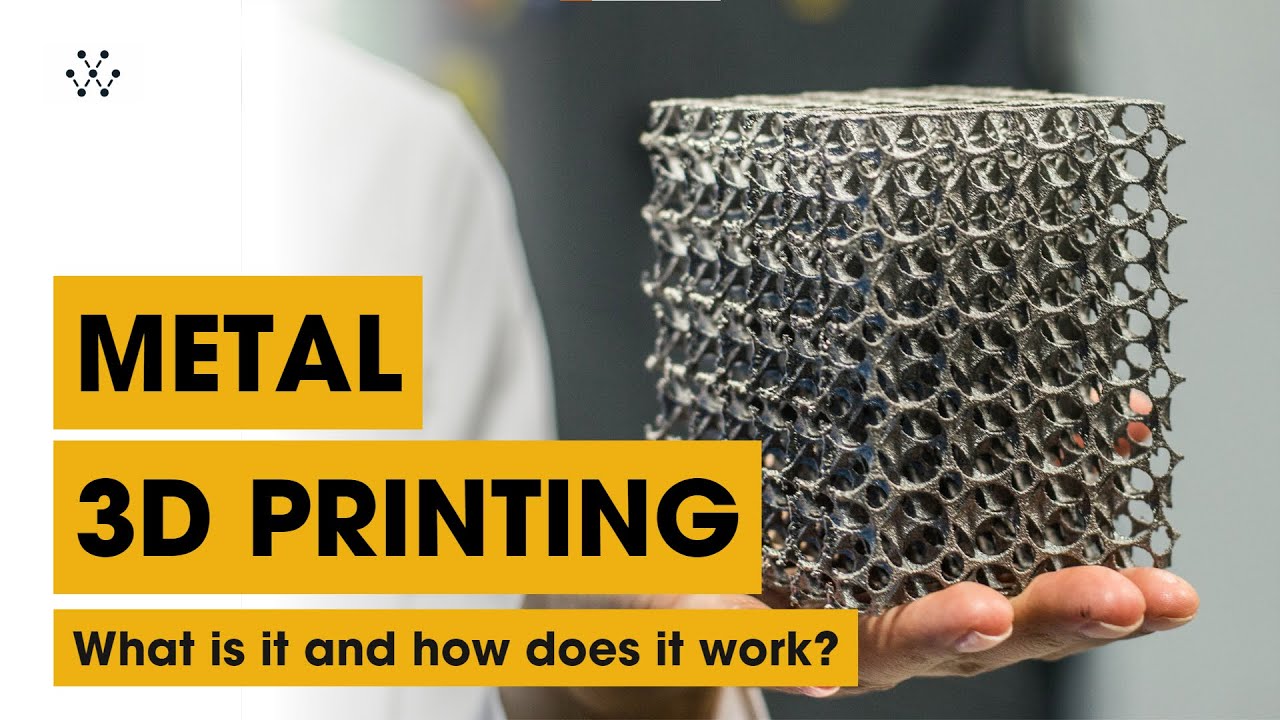
METAL 3D PRINTING | What is it and how does it work ?
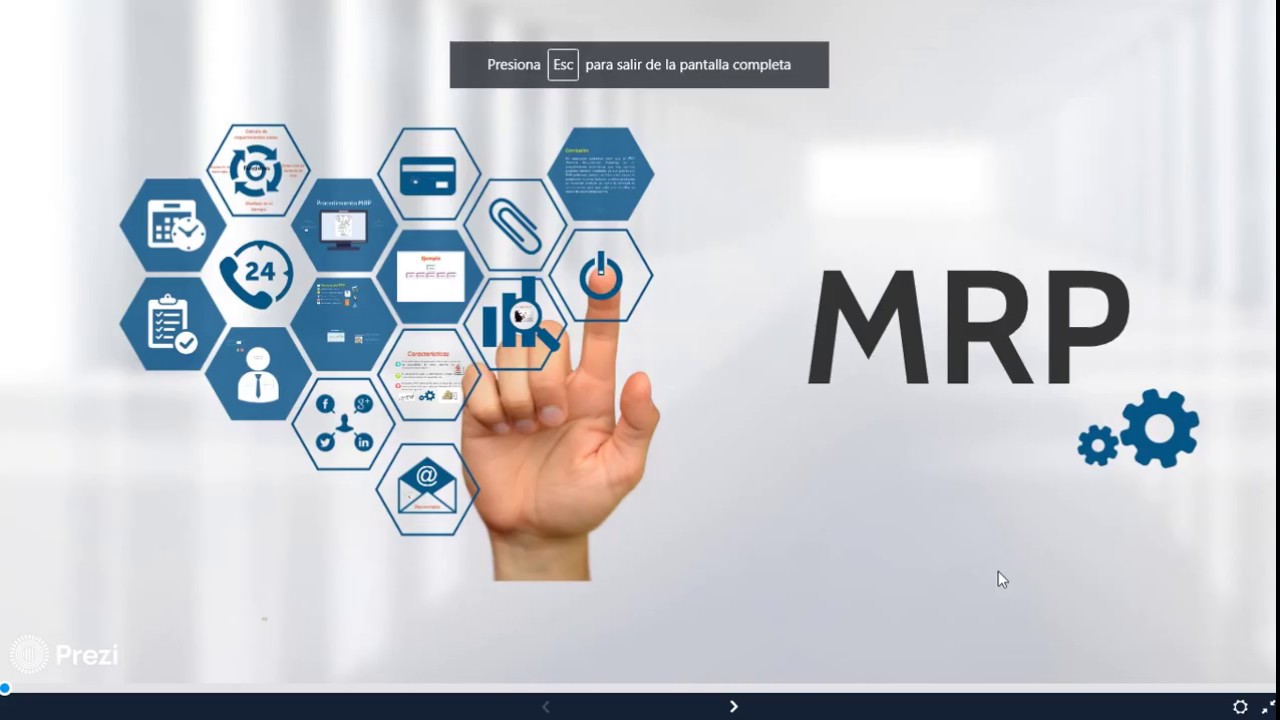
Explicación MRP
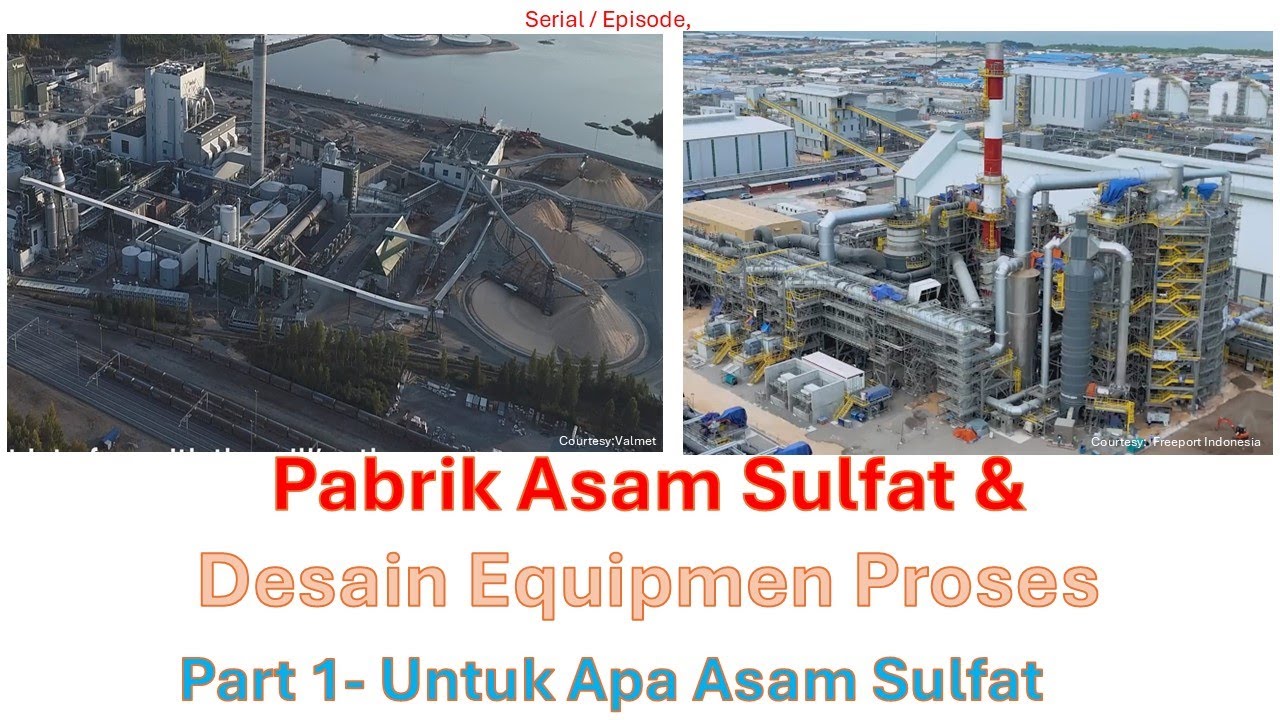
Part 1, Pabrik asam sulfat, Untuk Apa asam sulfat dipakai, dan industri yang konsumsi paling besar.

Produksi | Bagian 1 - Rencana Produksi (Production Plan)
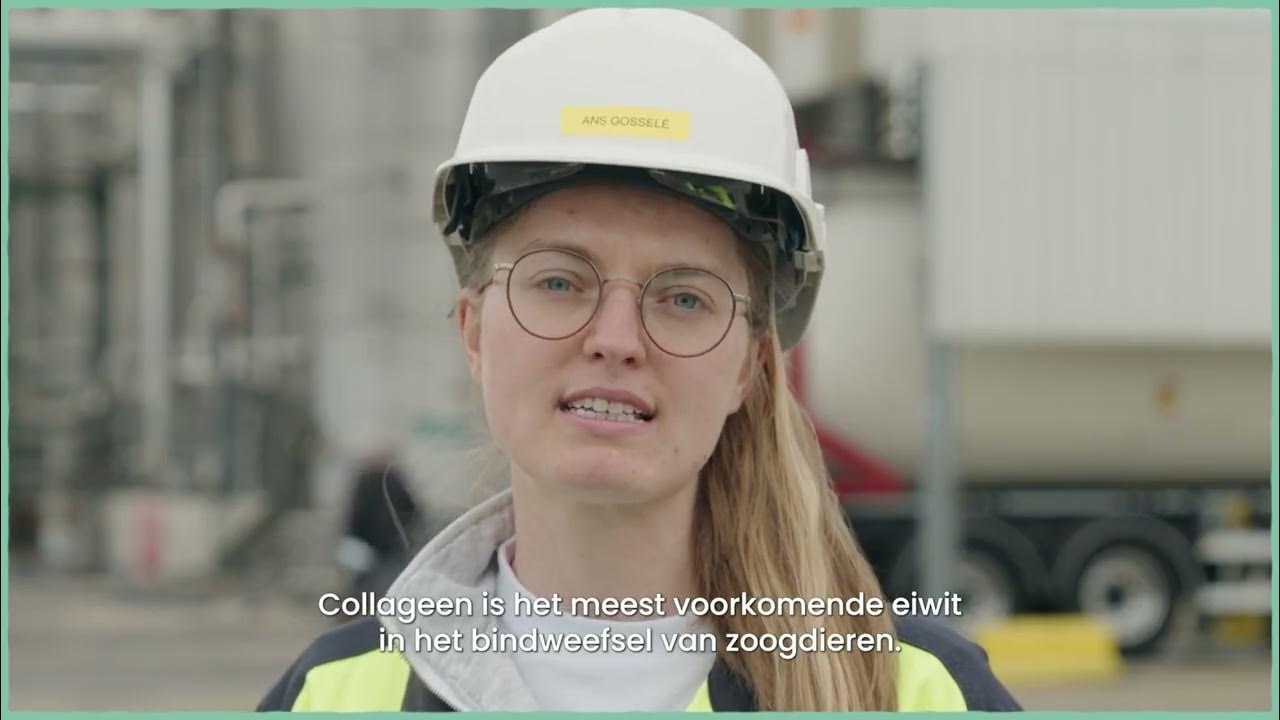
Regelkringen in productie- en procesinstallaties

Tópicos Avançados em Engenharia de Produção II - Manufatura Aditiva
5.0 / 5 (0 votes)