Video of the new parenteral drug manufacturing building of the CMIC CMO Ashikaga.
Summary
TLDRThe newly completed parenteral drug manufacturing facility in southwestern Cheeki Prefecture is designed to produce high-potency oncology drugs and biologics. It features two production lines with high sterility assurance, efficient rooms, and equipment compliant with cGMP and global standards. Innovative measures prevent cross-contamination, and the facility is equipped with advanced systems for power stability and hazardous material containment. The building also includes a visitor corridor for cleanroom observation, ensuring transparency and safety in pharmaceutical production.
Takeaways
- 🏭 A new parenteral drug manufacturing facility has been completed in the southwestern part of the Cheeki prefecture.
- 🔬 The facility is designed to manufacture oncology drugs and biologics, with a focus on parenteral drug production.
- 🚀 It consists of two production lines capable of producing both high-potency drugs and general injectables.
- 🛡️ The facility maintains a high level of sterility assurance and complies with PICs and global GMP requirements.
- 🔢 The manufacturing capacity ranges from 1,200 to 8,000 vials per hour for one milliliter to 250 milliliter vials.
- 🛂 The facility achieves high cross-contamination prevention with a one-way manufacturing flow and segregated areas.
- 💉 Innovative filling loss measures are implemented, such as flat tank design and gravity feeding pipe design to reduce initial flow loss.
- 🌐 The filling unit can switch to a pump filling system for single-use production, ensuring efficient operation.
- 🧪 After formulation, the solution is directly fed to the filling unit via piping, streamlining the process.
- 🧊 Lyophilization is performed while maintaining the sterile state, with low humidity air preventing condensation on vials.
- 🔄 The isolator unit can switch from positive to negative pressure for containment of hazardous materials post-lyophilization.
- 🛡️ A double HEPA filter is installed on the exhaust line to contain hazardous materials in case of unexpected leaks.
- 🔌 The facility has a dedicated wire for extra-high voltage electricity received at two delivery points to ensure stable power supply.
- 💦 A hazardous waste water treatment facility is installed to prevent environmental contamination.
- 🌿 The building design is based on four concepts: global GMP compliance, flexibility, stable operation, and prevention of cross-contamination and sterility assurance.
- 🧪 Semuc Group offers evaluation services for biologics and provides high-quality data in a GMP-compliant organization.
- 🌐 The group provides a total solution for pharmaceutical contract development and manufacturing, with facilities in Japan and overseas.
- 🔬 The Formulation Development Center is committed to meeting customer needs by providing cutting-edge technologies and innovative services.
Q & A
What is the purpose of the newly completed parenteral drug manufacturing building?
-The new parenteral drug manufacturing building is designed to produce oncology drugs and biologics, with a focus on high potency trucks and general injectables.
What are the two types of production lines in the facility?
-The facility has two production lines: one for high potency trucks and another for general injectables.
What level of sterility assurance does the manufacturing facility provide?
-The manufacturing facility provides a high level of sterility assurance, with highly efficient production rooms and equipment that comply with PIC/S and global GMP requirements.
What is the manufacturing capacity range of the facility for one milliliter and 250 milliliter vials?
-The manufacturing capacity ranges from 1,200 to 8,000 vials per hour for one milliliter and 250 milliliter vials.
How does the new facility prevent cross-contamination?
-The facility achieves a high level of cross-contamination prevention with a one-way manufacturing flow, segregated weighing and formulation areas, and various filling loss measures.
What design features help reduce initial flow loss during the filling process?
-Design features such as a flat tank with gravity feeding pipe design and the installation of fluid pushing nozzles before and after filtration help reduce initial flow loss.
How is the solution fed to the filling unit after formulation?
-The solution after formulation is directly fed to the filling unit via piping.
What system allows for a switchover to the pump filling system for single-use production?
-The filling unit is designed to allow switchover to the pump filling system for single-use production.
How does the facility handle hazardous materials during the lyophilization process?
-After lyophilization, the isolator unit switches from positive pressure to negative pressure for containment of hazardous materials.
What measures are in place to ensure operator safety in case of a leak in the lyophilizer area?
-A double HEPA filter is installed on the exhaust line to contain hazardous materials, and a port is attached for immediate filter change in case of a leak, ensuring operator safety.
How does the facility ensure stable operation and power supply during manufacturing?
-The facility receives dedicated extra high voltage electricity at two delivery points and has UPS and backup generators to supply power to important equipment in case of power failure.
What services does the facility offer for biologics?
-The facility offers a say evaluation service for biologics, with biological analysis experts in a GMP compliant organization providing high-quality data for a one-stop service from manufacturing to analytical testing and midi subtract products.
What is the overall goal of the facility in terms of pharmaceutical contract development and manufacturing?
-The facility aims to provide a total solution for pharmaceutical contract development and manufacturing of almost all drug formulations, from formulation development to commercial production, with cutting-edge technologies and innovative services.
Outlines
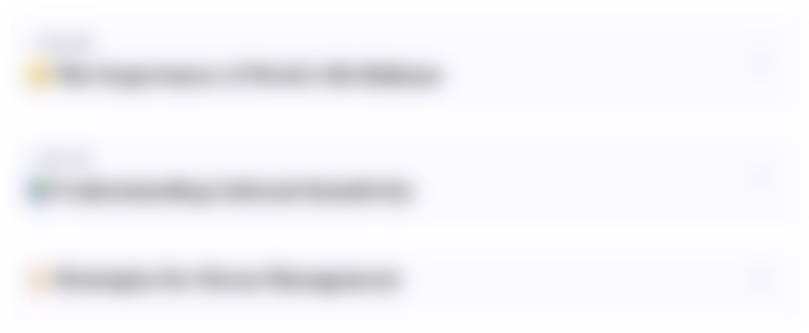
This section is available to paid users only. Please upgrade to access this part.
Upgrade NowMindmap
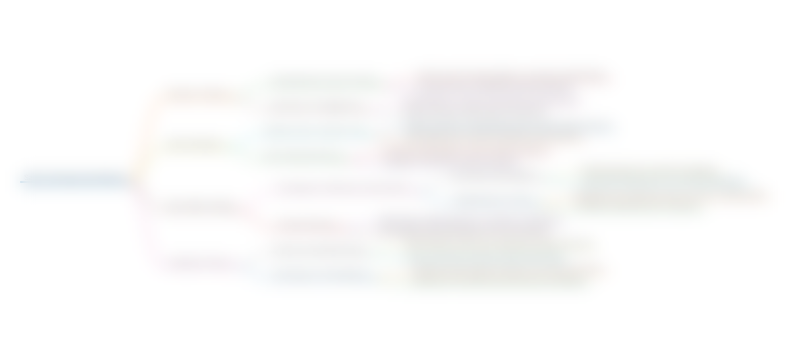
This section is available to paid users only. Please upgrade to access this part.
Upgrade NowKeywords
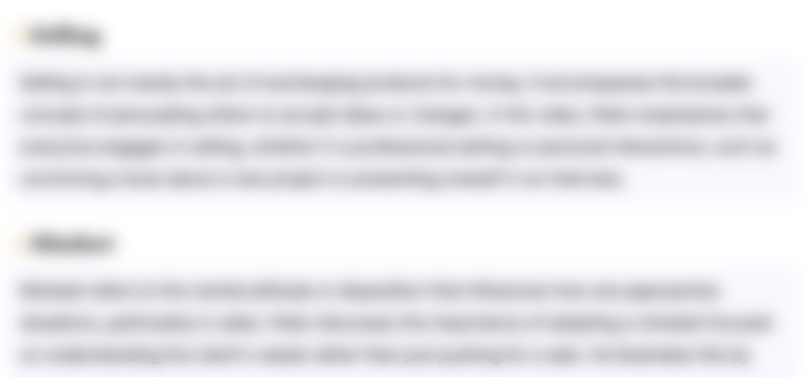
This section is available to paid users only. Please upgrade to access this part.
Upgrade NowHighlights
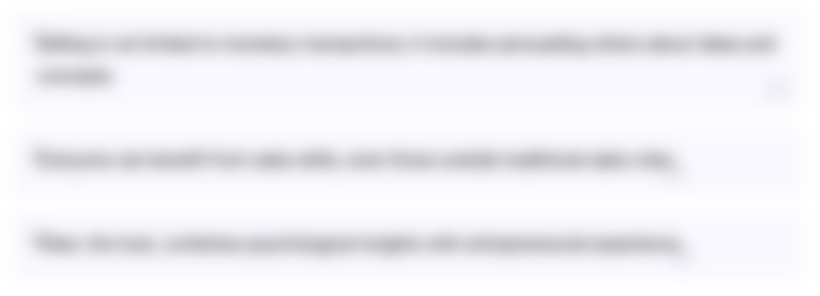
This section is available to paid users only. Please upgrade to access this part.
Upgrade NowTranscripts
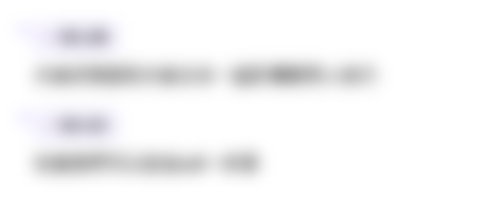
This section is available to paid users only. Please upgrade to access this part.
Upgrade NowBrowse More Related Video
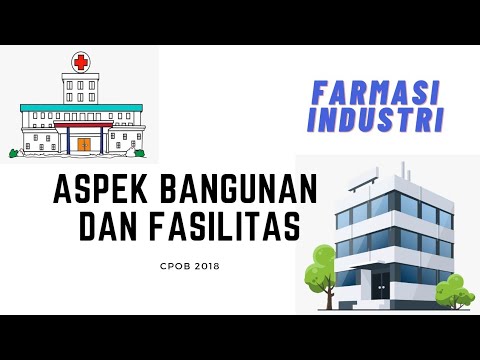
FASILITAS DAN BANGUNAN (FARMASI INDUSTRI)
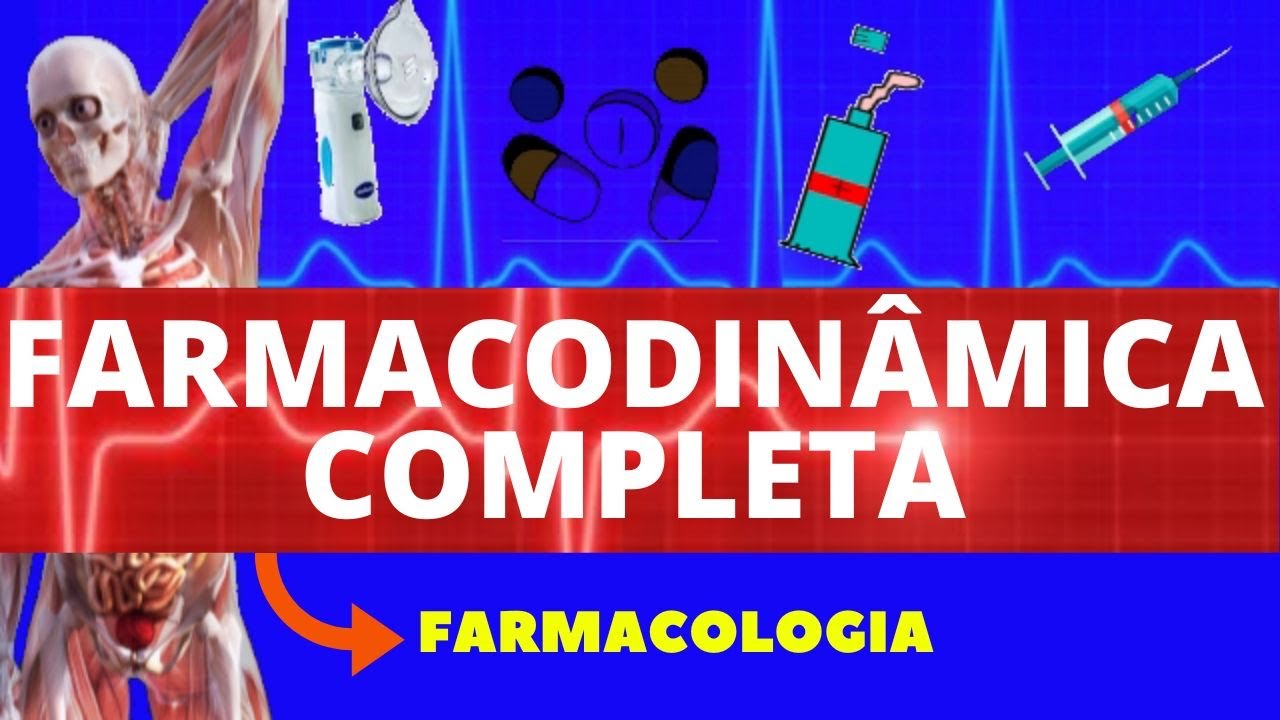
FARMACODINÂMICA COMPLETA (ENSINO SUPERIOR) - FARMACOLOGIA - MECANISMO DE AÇÃO DOS FÁRMACOS
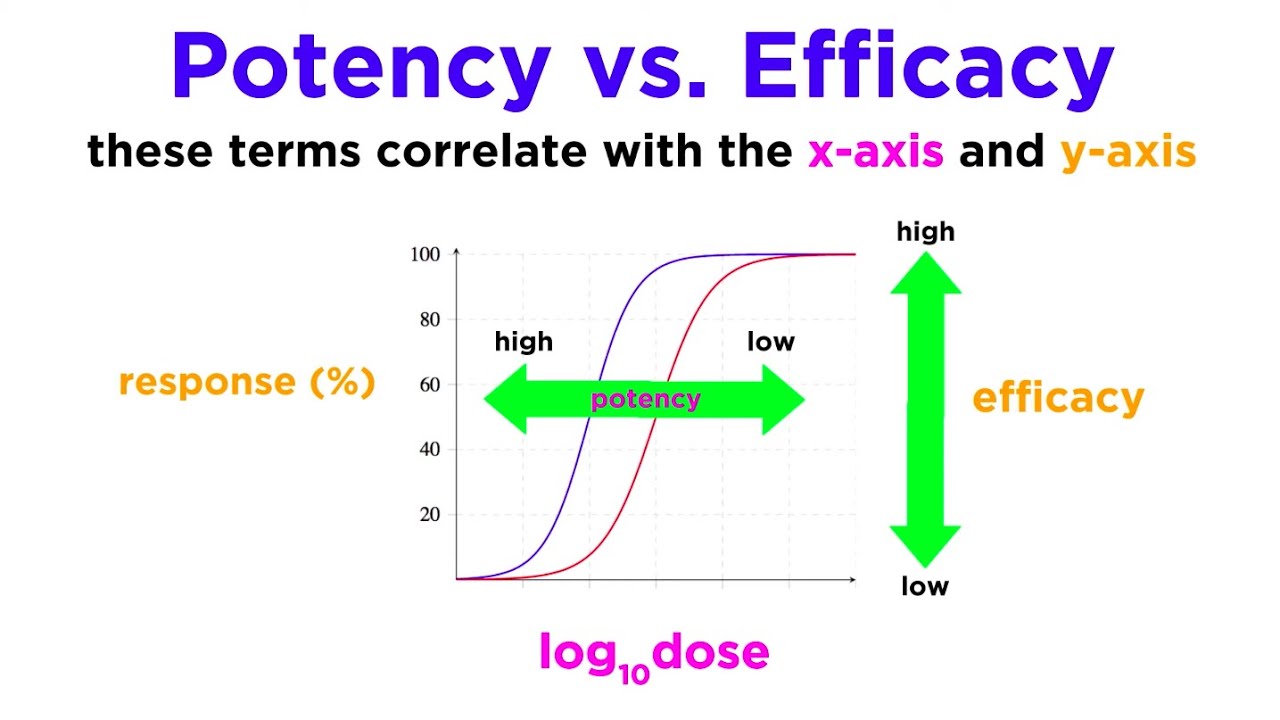
Pharmacodynamics: Mechanisms of Drug Action

Pharmacology Introduction in Hindi || Basic terms || Nursing || Pharmacy || 2nd year

Pharmacodynamics - Part 2: Dose-response Relationship

Pharmacology - PHARMACODYNAMICS (MADE EASY)
5.0 / 5 (0 votes)