Managing Your Assets 02 - Current Manufacturing Asset Challenges
Summary
TLDRThis presentation highlights the challenges faced by aging manufacturing plants, with 75% of U.S. plants over 20 years old. As automation systems near end-of-life, plant operations risk unplanned downtime, leading to costly disruptions. Key issues include sourcing replacement parts, managing extended downtime, and adapting to new technologies like Industry 4.0. The session emphasizes the importance of planning ahead to avoid costly downtime and ensure that critical components are reliable and available. It also explores the future of connected enterprise systems and the integration challenges that many plants face today.
Takeaways
- π 75% of US manufacturing plants are over 20 years old, presenting challenges in modernizing facilities.
- π Many of these plants have automation systems that are reaching the end of their lifespan, with $65 billion worth of automation systems at risk.
- π End-of-life automation systems may face difficulties sourcing replacement parts and lack the in-house expertise to support them.
- π Legacy equipment can be reliable, but as components age, the systems become harder to maintain and may no longer be feasible.
- π Unscheduled downtime due to broken or outdated equipment can cost plants up to $20 billion annually.
- π Planned downtime is manageable, but unplanned downtime, especially during emergencies, is costly and disruptive.
- π The availability of replacement parts can make downtime worse, especially if the parts are hard to find or have long lead times.
- π Fewer than 14% of US plants have fully integrated and connected machinery, signaling that many are not yet ready for future advancements like Industry 4.0.
- π Industry 4.0 technologies like augmented reality are becoming part of manufacturing, but many plants are still not fully integrated.
- π The process of integrating newer technologies into existing plants is challenging, and understanding what parts or steps are necessary is a major hurdle for many executives.
- π Key issues faced by plants include the availability of replacement parts, the trustworthiness of suppliers, and ensuring the parts will work and provide good value.
Q & A
What is a major challenge faced by many U.S. manufacturing plants today?
-A major challenge is that 75% of U.S. plants are over 20 years old, with many automation systems reaching the end of their life, creating difficulties in sourcing parts and maintaining the equipment.
How much is estimated to be spent on outdated automation systems?
-It is estimated that $65 billion worth of automation systems are reaching the end of life.
What can happen when automation systems reach the end of their life?
-When automation systems reach the end of their life, replacement parts become harder to source, and in-house knowledge about these systems is often lost or diminished.
Why is unscheduled downtime such a significant issue for manufacturing plants?
-Unscheduled downtime is costly because it happens unexpectedly, often causing production halts that disrupt operations and lead to significant financial losses. The cost of unscheduled downtime in plants is estimated to be $20 billion.
What are the two major consequences of part failure in a manufacturing plant?
-The two major consequences of part failure are extended downtime and the difficulty in finding replacement parts, which can further delay repairs.
What role do suppliers play in addressing downtime caused by part failures?
-Suppliers must ensure that parts are available and reliable. If a replacement part is unavailable or unreliable, it can extend downtime and complicate repairs.
Why is it important for plants to assess the availability and condition of replacement parts before a failure occurs?
-Assessing the availability and condition of replacement parts before a failure helps to avoid extended downtime and ensures that the necessary parts are ready for replacement when needed.
What is the relationship between industry 4.0 and manufacturing plants in terms of automation?
-Industry 4.0 is focused on digital tools and automation technologies, such as connected machines and augmented reality, to improve efficiency and integration within manufacturing plants. However, fewer than 14% of U.S. plants are fully integrated into such systems.
What is one reason why fewer than 14% of U.S. plants are fully integrated into Industry 4.0?
-One reason for this low integration is the difficulty in starting the integration process when plants are unsure of their current system's capabilities and what steps to take first.
What is the core takeaway from the presentation regarding downtime and parts availability?
-The core takeaway is that manufacturers must proactively ensure they have the right parts and systems in place to minimize downtime, avoid production disruptions, and ensure they are getting value from their investments.
Outlines
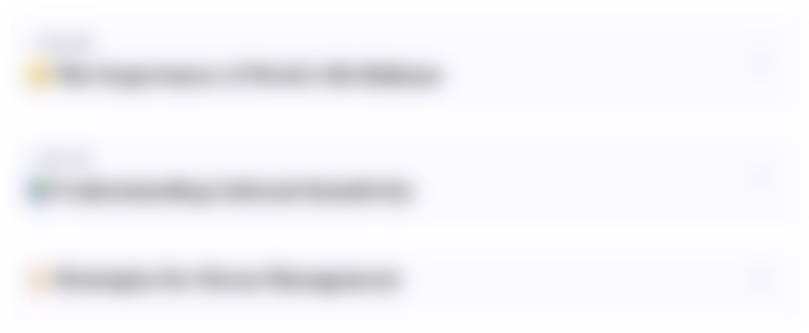
This section is available to paid users only. Please upgrade to access this part.
Upgrade NowMindmap
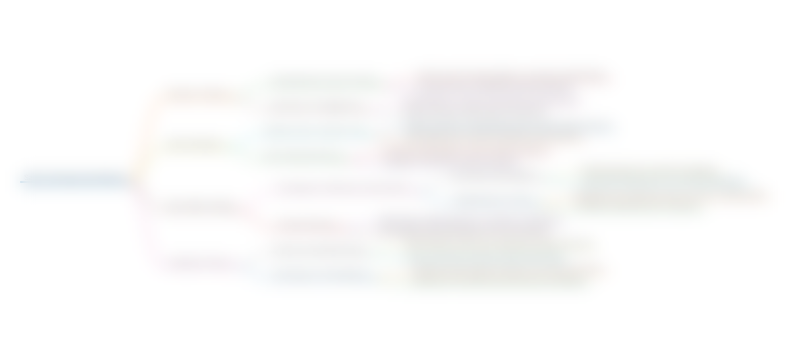
This section is available to paid users only. Please upgrade to access this part.
Upgrade NowKeywords
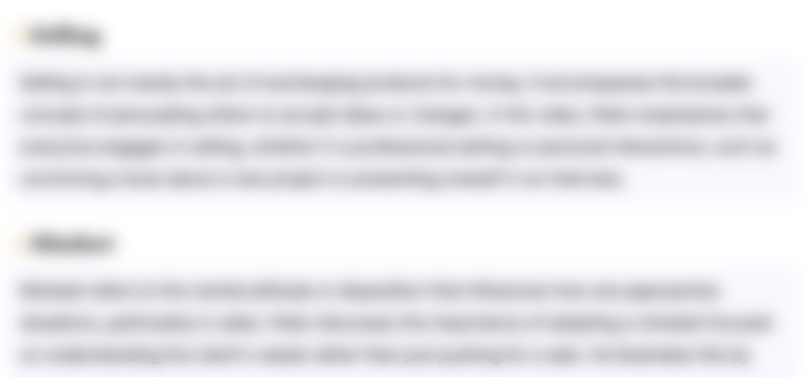
This section is available to paid users only. Please upgrade to access this part.
Upgrade NowHighlights
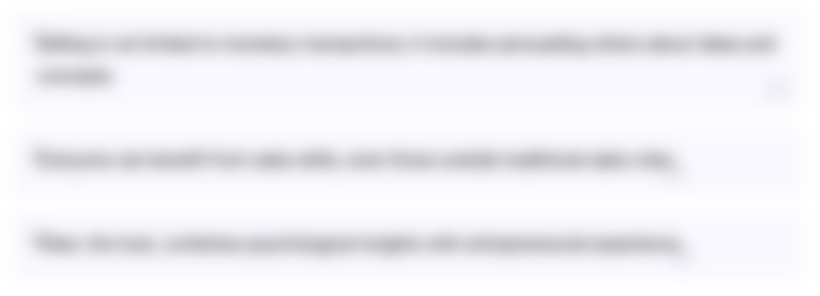
This section is available to paid users only. Please upgrade to access this part.
Upgrade NowTranscripts
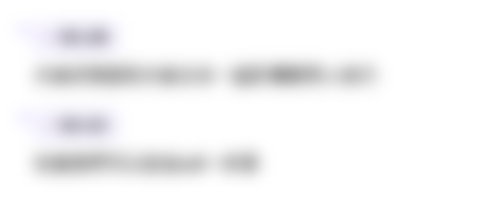
This section is available to paid users only. Please upgrade to access this part.
Upgrade NowBrowse More Related Video
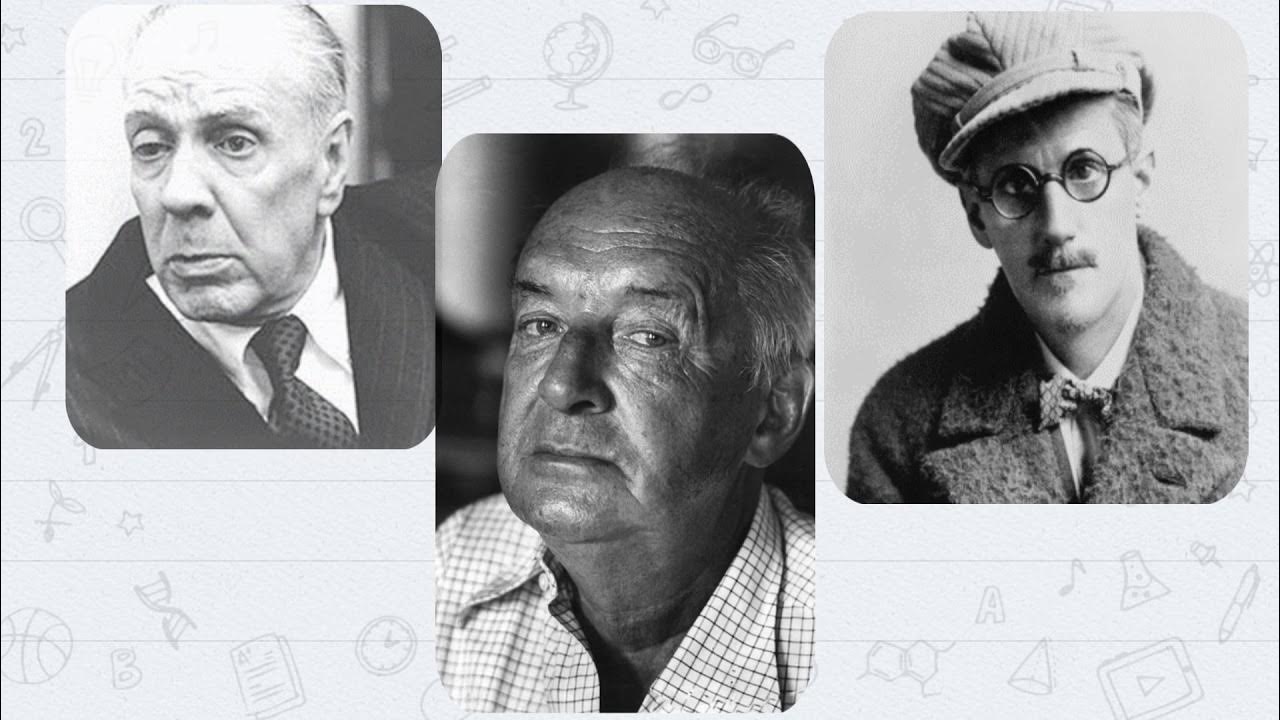
Issues and Challenges in Contemporary Literature

Demografiska transitionen
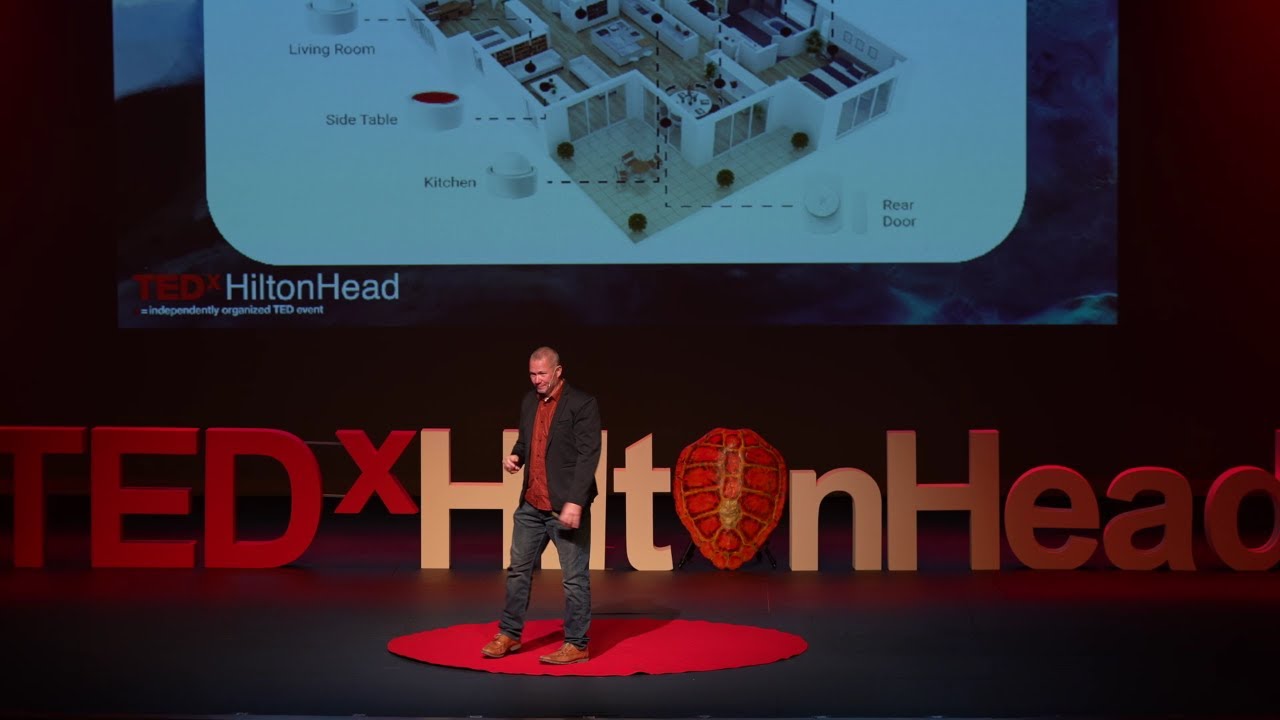
Smart Home, Safe Home: Safely Aging at Home | Ryan Herd | TEDxHiltonHead

Inspirasi Usaha Kreatif - ECOPRINT dan Cara Pembuatan Ecoprint

Age & Aging: Crash Course Sociology #36

Kalah 6-0 dari Korea Utara, Timnas Indonesia U17 Gagal ke Semifinal Piala Asia
5.0 / 5 (0 votes)