Epoxy Table TIPS & TRICKS For BEGINNERS
Summary
TLDRIn this instructional video, the creator shares top tips for crafting epoxy tables, from sourcing clients on Instagram to the meticulous building process. He discusses common mistakes, moisture content checks with a delm moisture meter, and the importance of a proper mold (MT). The video offers insights on epoxy application, vacuum chamber usage, and the transition to deep casting epoxy for fewer bubbles. A three-hour epoxy master class is teased for those seeking in-depth knowledge, and the creator invites feedback on content balance and future project ideas, showcasing his journey from DIY to running a custom furniture company.
Takeaways
- 🛠️ The video provides a step-by-step guide on building an epoxy table, including the process and mistakes to avoid.
- 🔍 Importance of checking the moisture content in the slab with a delm moisture meter to prevent issues with the epoxy table build.
- 📏 A tip to always cut the table slab larger than the final desired size to account for trimming during the manufacturing process.
- 💡 The suggestion to build a mold (Mt) slightly larger than the table dimensions and using white melamine sheets to prevent epoxy from penetrating the wood.
- 🧼 The use of wax or tuck tape to seal the mold and ensure a clean epoxy pour.
- 🌬️ The necessity of cleaning the wood with an air hose to remove dust before applying epoxy to avoid trapped particles.
- 🔗 The video creator's journey from a DIY garage start to running a custom furniture company, emphasizing the growth and challenges faced.
- 🤝 A call to action for viewers to support the YouTube community by liking, subscribing, and engaging with content.
- 🎓 Mention of a 3-hour long epoxy master class for those interested in a detailed guide on building epoxy tables.
- ⏱️ The significance of waiting for the epoxy to become tacky before applying additional layers to ensure a strong bond.
- 🛑 The creator's emphasis on learning from mistakes and adapting methods, such as using a vacuum chamber to remove air bubbles from epoxy.
Q & A
What is the main topic of the video script?
-The main topic of the video script is providing tips for building epoxy tables and sharing the process of creating a six-seater epoxy table.
How does the client acquisition process work for the table builders as mentioned in the script?
-The client acquisition process for the table builders mainly happens through Instagram, where they source most of their clients.
What was the initial mistake made during the manufacturing process of the first epoxy table?
-The initial mistake was manufacturing the table to the exact size the client wanted without accounting for the final cutting stage, resulting in a slightly smaller table than intended.
Why is checking the moisture content important in the table building process?
-Checking the moisture content is crucial because it ensures the wood is dry before use, preventing issues with the epoxy bonding and the overall durability of the table.
What is the purpose of building a mold table (MT) slightly bigger than the final table size?
-Building the mold table slightly bigger than the final table size allows for adjustments and prevents the final product from being too small after cutting down to the desired size.
What is the role of melamine sheets in the mold table construction?
-Melamine sheets are used in the mold table construction to prevent the epoxy from penetrating into the wood, ensuring a clean and smooth epoxy surface.
Why is it recommended to clean the wood before casting epoxy?
-Cleaning the wood before casting epoxy helps to remove dust particles and debris, ensuring a clean surface for the epoxy to adhere to and preventing imperfections in the final product.
What is the significance of using a vacuum chamber in the epoxy table building process?
-A vacuum chamber is used to remove air bubbles from the epoxy mixture, which is essential for achieving a professional and flawless finish on the epoxy table.
What is the recommended method for determining when to apply the next layer of epoxy?
-The recommended method is to wait until the first layer of epoxy becomes tacky, similar to the feel of warm toffee, before applying the next layer for the strongest bond.
How does the epoxy master class help those interested in building epoxy tables?
-The epoxy master class provides in-depth knowledge and techniques for building epoxy tables, catering to all skill levels from beginners to experts, and covering everything needed to build a successful epoxy table.
What is the reason for applying a thin layer of epoxy to both the top and bottom of the table?
-Applying a thin layer of epoxy to both sides helps to close all small imperfections, cracks, and holes, ensuring a smooth and professional finish on the table.
What type of sandpaper grit is recommended for achieving a frosty smokey finish on an epoxy table?
-For a frosty smokey finish, it is recommended to sand the epoxy section to 320 grit or 400 grit, depending on the desired level of smoothness.
How does the script address the issue of negative comments and feedback on the YouTube channel?
-The script acknowledges the presence of negative comments and explains the journey from a DIY channel to a custom furniture company, emphasizing the growth and hard work behind the success, and inviting viewers to share their thoughts on finding a balance in video content.
What is the final step in the finishing process for the epoxy table as described in the script?
-The final step in the finishing process is applying a quick-set epoxy to close any micro cracks and holes, followed by sanding and polishing to achieve the desired finish.
Outlines
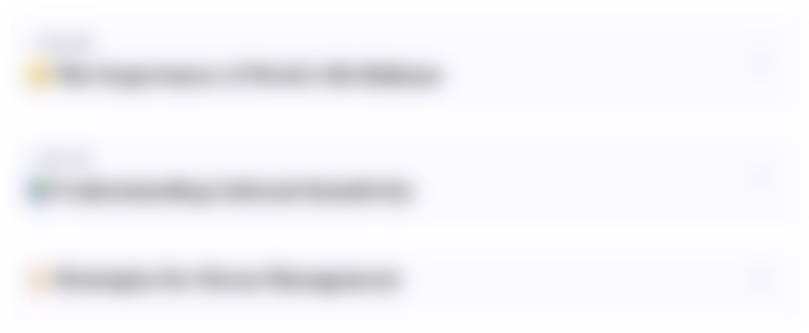
This section is available to paid users only. Please upgrade to access this part.
Upgrade NowMindmap
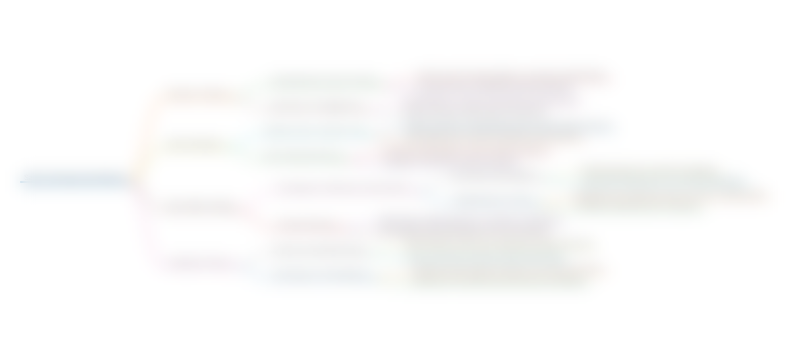
This section is available to paid users only. Please upgrade to access this part.
Upgrade NowKeywords
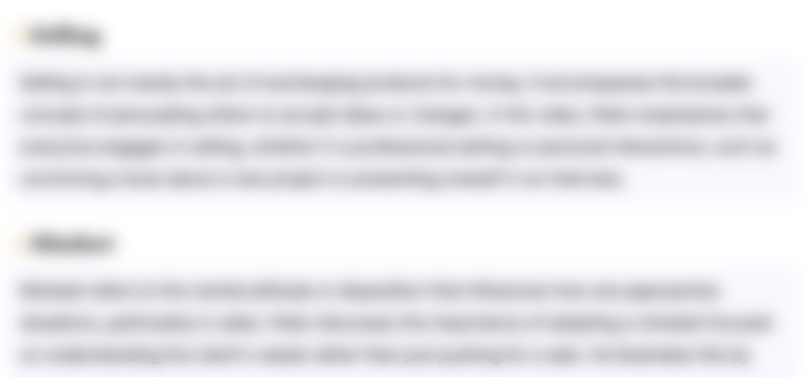
This section is available to paid users only. Please upgrade to access this part.
Upgrade NowHighlights
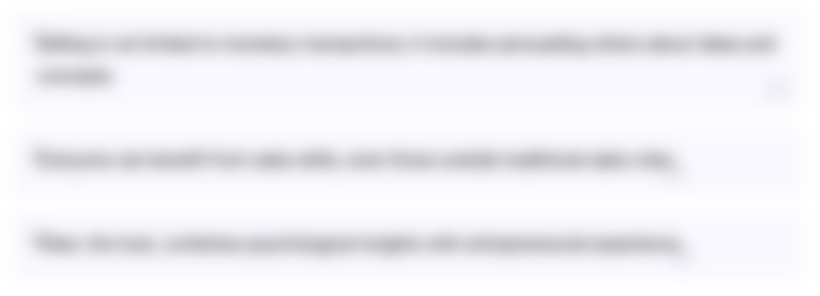
This section is available to paid users only. Please upgrade to access this part.
Upgrade NowTranscripts
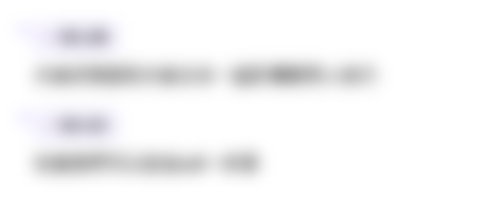
This section is available to paid users only. Please upgrade to access this part.
Upgrade NowBrowse More Related Video
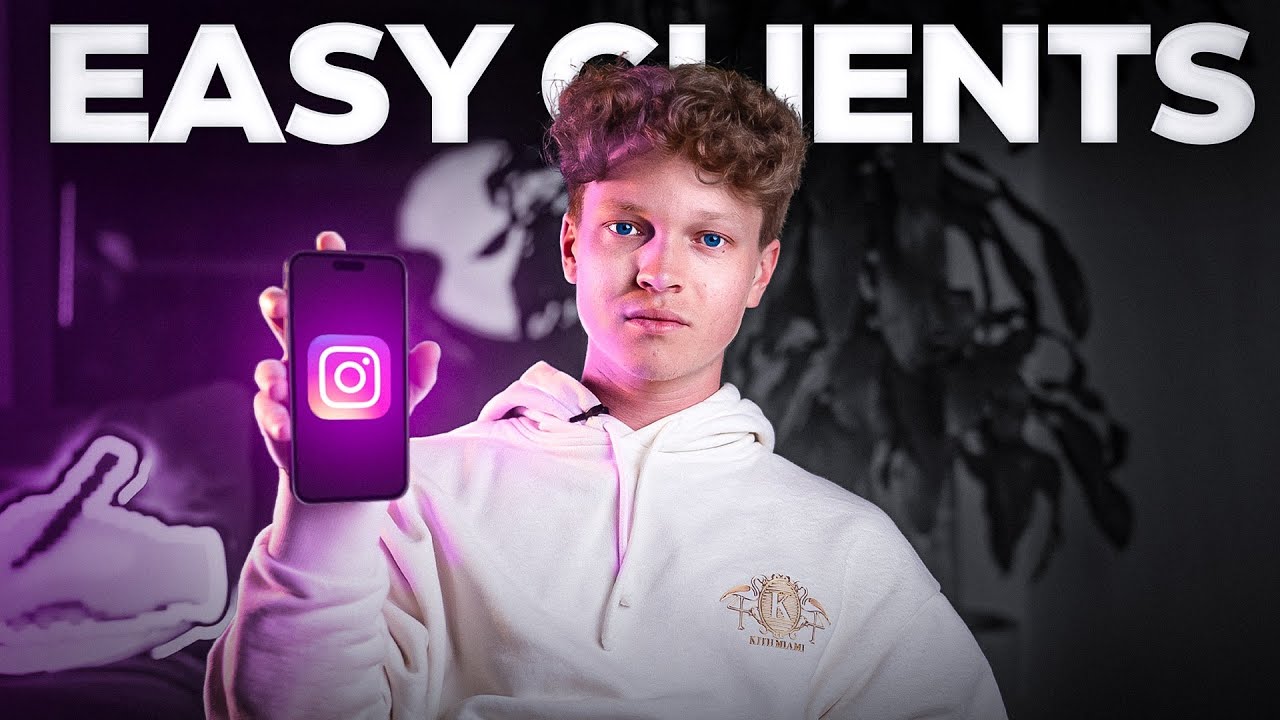
The NEW Way Of Getting Copywriting Clients In 2024
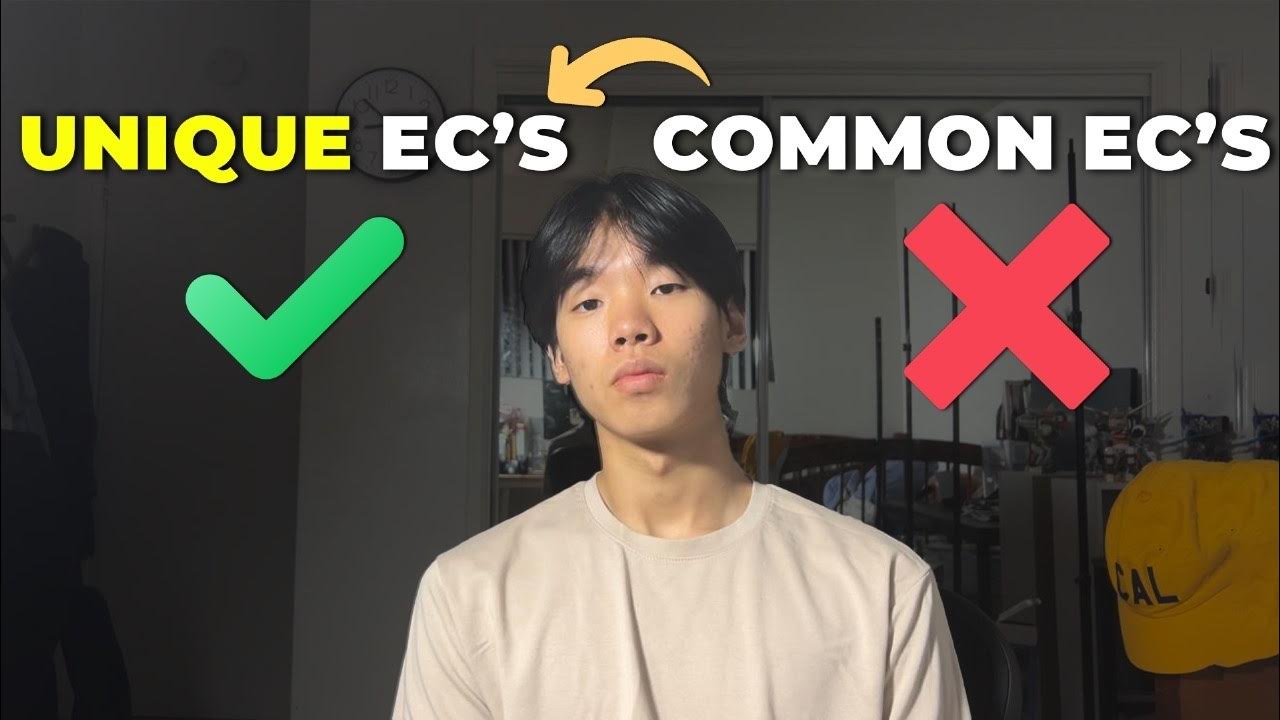
don't know what extracurricular to start in 2024? i gotchu.
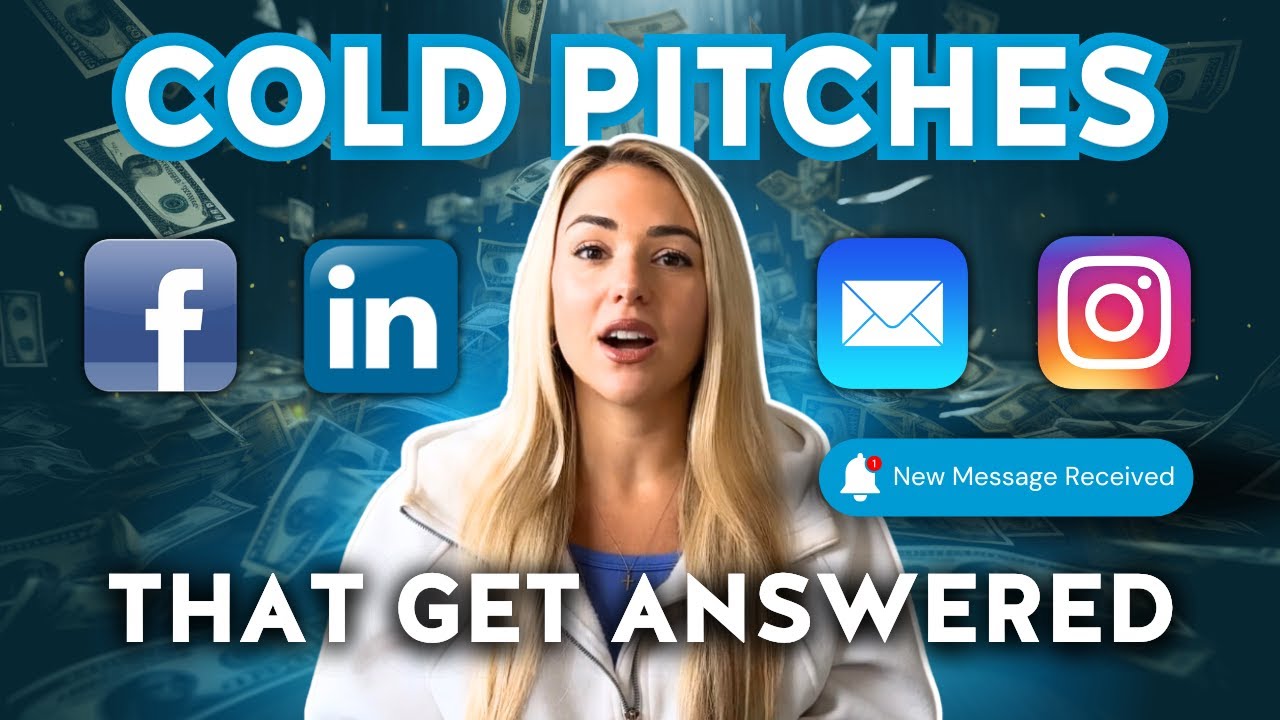
How to Cold Pitch Freelance Copywriting Clients (⚠️Avoid these mistakes to get responses)
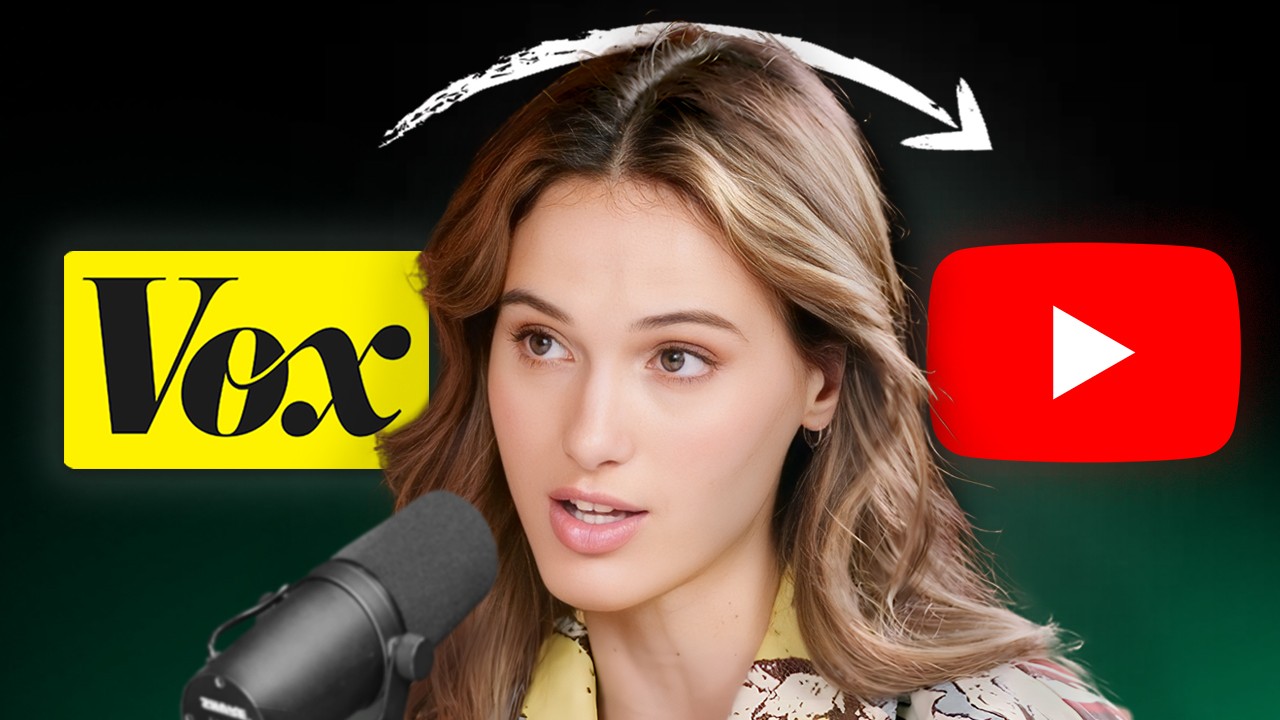
Why every Cleo Abram video goes viral

Cara Nyari Klien Ilustrasi (tutorial kirim porto dan email)
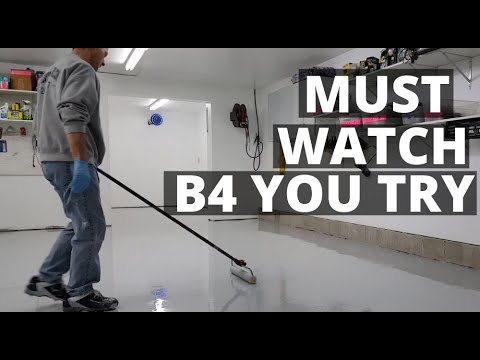
How To Epoxy Coat Your Garage Floor | Must Watch For Diy'rs
5.0 / 5 (0 votes)