Chapter 11 - Managing International Operation (Part 1)
Summary
TLDRThis lecture delves into managing international operations, focusing on capacity planning and facility location strategies. It discusses assessing a company's production capabilities to meet fluctuating market demands, including decisions on reducing output or expanding facilities. The importance of selecting optimal production sites based on resource availability, labor costs, customer needs, and transportation is highlighted. The script also covers the economic benefits of location economies and the strategic decisions between centralization for cost efficiency and decentralization for market customization.
Takeaways
- 📈 Capacity Planning: It's crucial for a company to assess its ability to produce enough output to meet market demand, which can fluctuate and thus requires flexible production strategies.
- 🔍 Estimating Global Demand: Firms must accurately estimate the global demand for their products to align production with market needs effectively.
- 🛠️ Adjusting Production: When output exceeds demand, companies may reduce production by cutting manpower or work shifts to avoid overproduction.
- 🏭 Facility Expansion: Managers must decide whether to expand existing facilities or add new ones to meet growing market demands.
- 🌐 Location Decisions: Firms need to consider adding facilities in new locations to better serve customer demand in different areas.
- 🏗️ Facility Location Planning: Choosing the right location for manufacturing facilities is key, considering access to resources, labor, and transportation.
- 🌳 Resource Availability: The availability and cost of raw materials are significant factors in facility location decisions, with examples like Goodyear Tire opting for Malaysia due to abundant rubber resources.
- 💼 Labor Costs and Productivity: Multinational companies often seek locations with lower wages and high productivity to optimize labor costs.
- 🛒 Customer Needs and Accessibility: Firms must consider customer accessibility and needs, such as choosing non-congested areas for stores like Tesco with ample parking.
- 🚚 Factory to Market Proximity: The distance between production facilities and target markets affects transportation costs and delivery times, influencing location decisions.
- 🌐 Location Economies: Firms aim to locate production in areas that offer the best economic benefits, such as lower production costs, to achieve a competitive advantage.
- 🔧 Centralization vs. Decentralization: Centralization focuses on concentrating production in one optimal location for cost efficiency, while decentralization involves spreading facilities across different markets for product customization and adaptation.
Q & A
What does capacity planning involve in the context of managing international operations?
-Capacity planning involves assessing a company's ability to produce enough output to satisfy market demand, taking into account the fluctuating nature of customer demand, and making decisions on production adjustments, such as reducing manpower or work shifts when demand decreases.
How can a firm reduce production when the output exceeds market demand?
-A firm can reduce production by decreasing the number of workers or adjusting work shifts to align with the reduced market demand.
What factors must managers consider when market demand is growing and they need to expand output?
-Managers must determine whether the existing facility can expand output or if additional facilities are needed, considering the maximum capacity of the firm and potentially adding more machinery or manpower to fulfill the increased demand.
Why might a firm decide to open a new facility in a different location?
-A firm may decide to open a new facility in a different location if the existing facility cannot capture the demand anymore, requiring an estimation of the number of rooms, manpower, and other resources suitable for the new area to meet customer demand.
What is the concept of subcontracting in the context of capacity planning?
-Subcontracting involves letting another party produce part or all of the finished product on behalf of the firm, which can be a strategy to maintain good customer service and avoid stock unavailability.
What is facility location planning and why is it important?
-Facility location planning is the selection of an optimal location for production facilities, ensuring sufficient access to customers, resources, and transportation. It is important because it affects production costs, efficiency, and the ability to meet customer needs.
What are the key considerations for a firm when choosing a location for its manufacturing facility?
-Key considerations include the availability and cost of raw materials, labor costs and productivity, customer needs, and the distance between the factory and the market to minimize transportation costs and time.
Why might a firm choose a particular location for its production facility based on resource availability?
-A firm might choose a location with abundant and cost-effective resources, such as rubber in Malaysia for a tire manufacturing company, to ensure a steady supply of raw materials for production.
What is the significance of location economy in facility location planning?
-Location economy refers to the economic benefits derived from locating production in an optimal location, which can help lower the cost of production and achieve a competitive advantage by taking advantage of lower labor costs, skilled labor, or other economic incentives.
What are the two basic strategies for locating production facilities, and how do they differ?
-The two basic strategies are centralization, which involves concentrating production in one location to achieve economies of scale and lower costs, and decentralization, which involves spreading facilities across different locations to cater to regional markets and customize products according to local preferences.
How does a firm benefit from centralizing its production facilities?
-Centralizing production allows a firm to focus on mass production in a location that offers lower costs, skilled labor, and other economic benefits, which can lead to reduced production costs and increased efficiency.
What are the advantages of decentralization in managing international operations?
-Decentralization allows a firm to have various regional or national facilities that can focus on producing customized products tailored to local market preferences, infrastructure, and government requirements, enhancing customer satisfaction and market adaptation.
Outlines
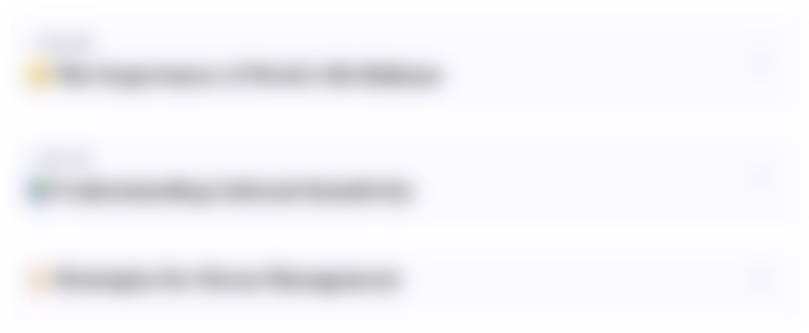
This section is available to paid users only. Please upgrade to access this part.
Upgrade NowMindmap
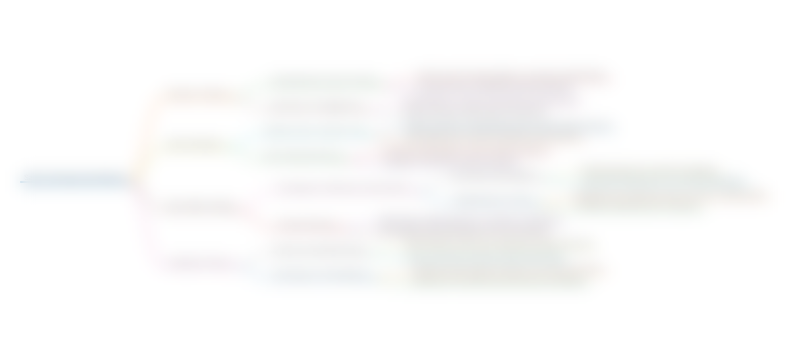
This section is available to paid users only. Please upgrade to access this part.
Upgrade NowKeywords
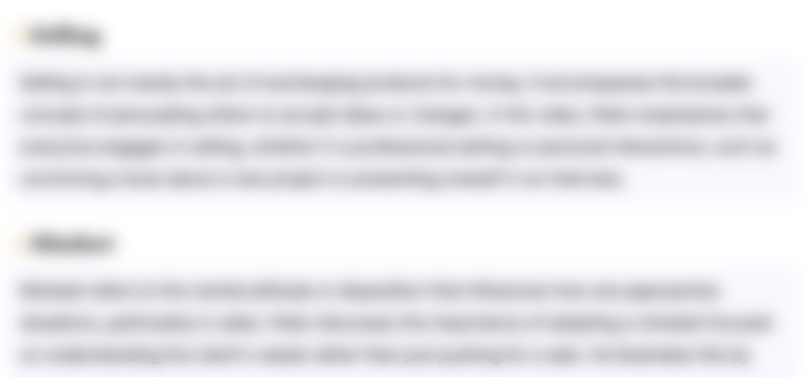
This section is available to paid users only. Please upgrade to access this part.
Upgrade NowHighlights
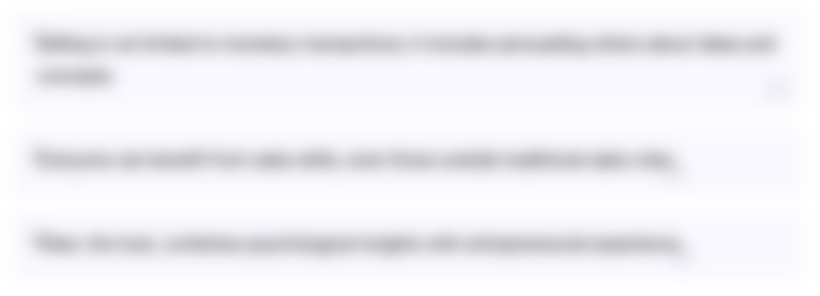
This section is available to paid users only. Please upgrade to access this part.
Upgrade NowTranscripts
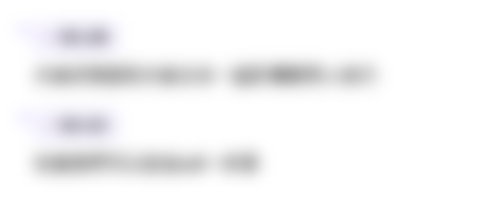
This section is available to paid users only. Please upgrade to access this part.
Upgrade NowBrowse More Related Video

MANAJEMEN OPERASI INTERNASIONAL -BISNIS INTERNASIONAL
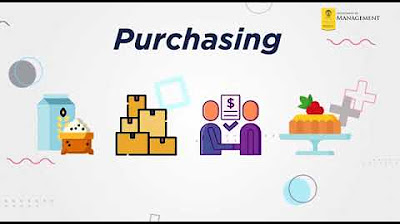
Pengantar Bisnis Sesi 11 Produksi dan Manajemen Operasi
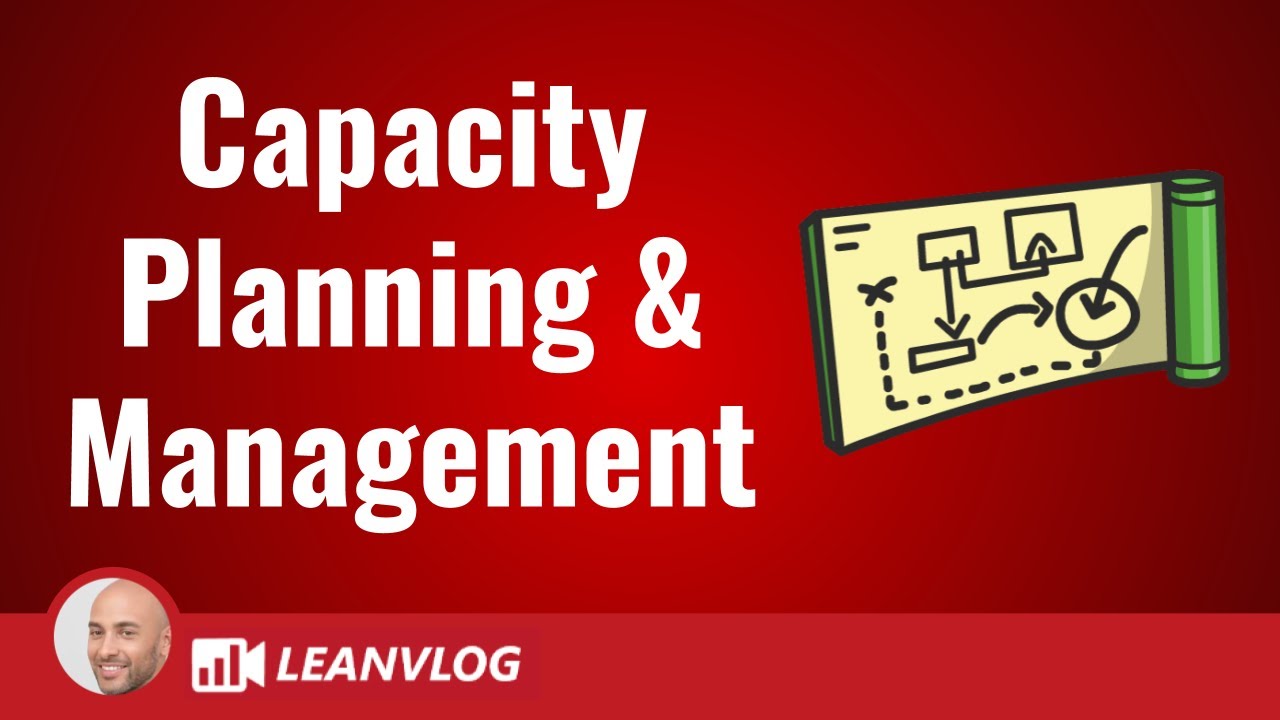
Capacity Planning - Overview and Key Concepts

Manajemen Keuangan Internasional dalam Mata Kuliah Bisnis Internasional

MATERI KULIAH MANAJEMEN OPERASIONAL - PERENCANAAN KAPASITAS

Perencanaan Agregat
5.0 / 5 (0 votes)