Digital Transformation OEM Summit 2023 - Athena iServ Keynote Presentation
Summary
TLDRThis video explores the transformation of industrial operations through digital solutions, emphasizing remote connectivity, predictive maintenance, and data-driven insights. The speakers discuss leveraging secure communication methods, such as OPC and tunneling, to ensure data integrity while managing remote equipment. With a focus on automation and optimizing machine performance, the session highlights the role of virtual networks and GPRS in enabling real-time monitoring and maintenance. The key takeaway is the importance of adapting to digital technologies for improved operational efficiency and service delivery in modern industrial environments.
Takeaways
- 😀 The solution enables customers to unlock new business opportunities by improving equipment performance and enhancing operational efficiency.
- 😀 The software connects to deployed equipment in the field, gathering real-time data and providing actionable insights.
- 😀 Predictive capabilities alert users to potential issues, helping to proactively address problems before they impact production.
- 😀 A mobile app provides self-service tools for customers to resolve issues quickly, reducing the need for direct support calls.
- 😀 The app allows customers to create tickets, schedule technician calls, and manage parts, streamlining the service process.
- 😀 OEMs (Original Equipment Manufacturers) can offer a digital service offering, generating additional revenue through service packages for customers.
- 😀 A tiered customer service model enables varying levels of service packages, from basic ticketing systems to high-value, proactive services.
- 😀 The solution can be integrated with existing systems, such as CRM, parts management, and e-commerce, to streamline operations.
- 😀 Predictive maintenance and performance monitoring improve equipment uptime, reducing service costs and improving overall productivity.
- 😀 Monetization strategies include charging for value-added services, such as predictive maintenance, mobile app access, and advanced support.
- 😀 The software supports flexible communication methods, including secure parallel networks, to ensure data integrity and safe operations.
Q & A
What is the main purpose of the solution described in the video?
-The main purpose of the solution is to enable OEMs and their customers to monitor equipment performance remotely, facilitate predictive maintenance, and offer self-service options for troubleshooting, thereby improving operational efficiency and reducing downtime.
How does the mobile app assist technicians and end-users?
-The mobile app allows technicians and end-users to scan QR codes on equipment to access self-guided troubleshooting resources. If issues aren't resolved, users can create service tickets directly from the app to contact support, streamlining the service process.
What monetization opportunities are available for OEMs through this solution?
-OEMs can generate additional revenue by offering services such as remote monitoring, predictive maintenance, and customer self-service tools. These services can be packaged and sold to customers at varying price points depending on the service level.
What role does predictive maintenance play in this solution?
-Predictive maintenance helps customers anticipate potential equipment failures before they occur, enabling them to take corrective action in advance, thus reducing unexpected downtime and increasing machine uptime.
How does the system ensure secure communication with the equipment?
-The system ensures secure communication by using a parallel, isolated network for OEM data. This network is separate from the customer’s plant network, preventing potential security breaches and ensuring that only the required data is transmitted securely.
What are the benefits of the self-guided service feature in the app?
-The self-guided service feature allows users to troubleshoot issues without needing to contact support, saving time and reducing the number of service tickets. This empowers users to resolve common problems independently.
What is the significance of the service manager portal for OEMs?
-The service manager portal provides OEMs with a centralized platform to manage customer data, monitor equipment performance, and track service tickets. This helps OEMs deliver more efficient support and streamline their service operations.
How does the solution support scalability for businesses?
-The solution is designed to be modular and scalable, meaning businesses can start with basic features like performance monitoring and gradually integrate more advanced services like predictive maintenance and remote support, making it adaptable to different customer needs.
What types of data can be collected by the solution?
-The solution collects data related to machine performance, usage patterns, and operational metrics. This data is aggregated to provide insights on potential issues and support predictive maintenance efforts.
How does the solution integrate with existing systems like PLM or CRM?
-The solution integrates seamlessly with existing systems such as PLM, CAD, and CRM, enabling businesses to tie together operational data and service management in a unified platform, improving overall efficiency and customer experience.
Outlines
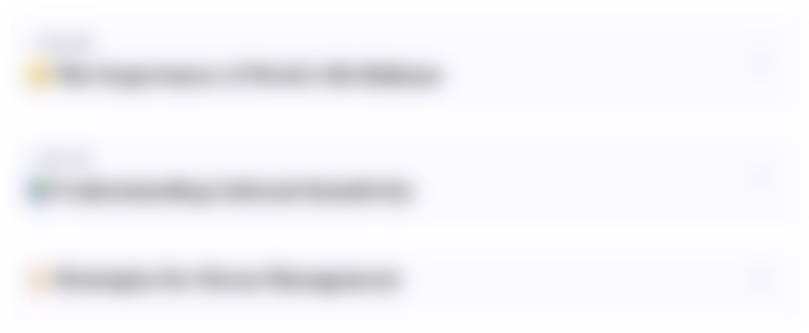
This section is available to paid users only. Please upgrade to access this part.
Upgrade NowMindmap
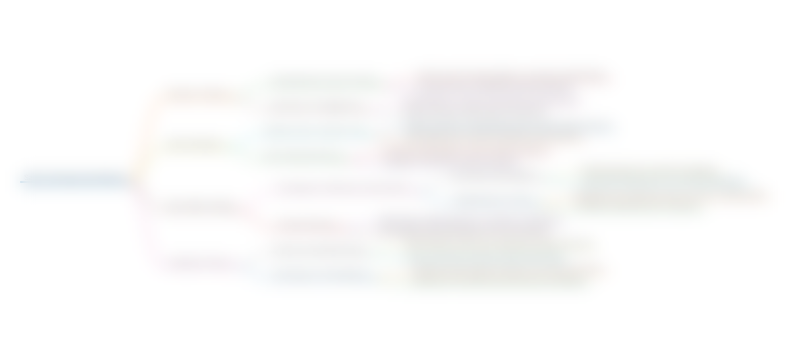
This section is available to paid users only. Please upgrade to access this part.
Upgrade NowKeywords
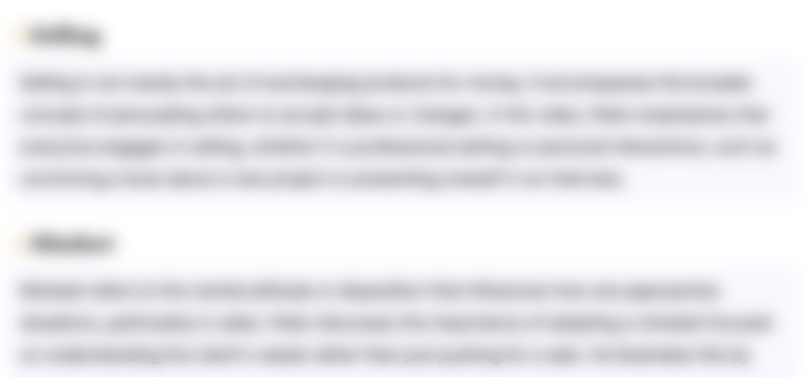
This section is available to paid users only. Please upgrade to access this part.
Upgrade NowHighlights
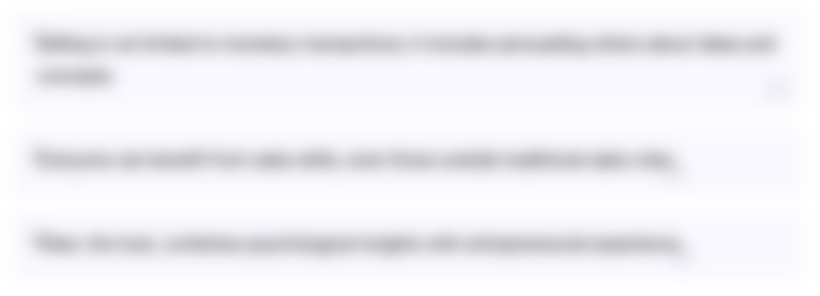
This section is available to paid users only. Please upgrade to access this part.
Upgrade NowTranscripts
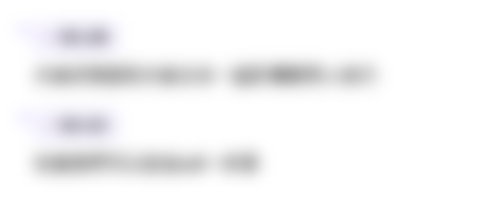
This section is available to paid users only. Please upgrade to access this part.
Upgrade NowBrowse More Related Video
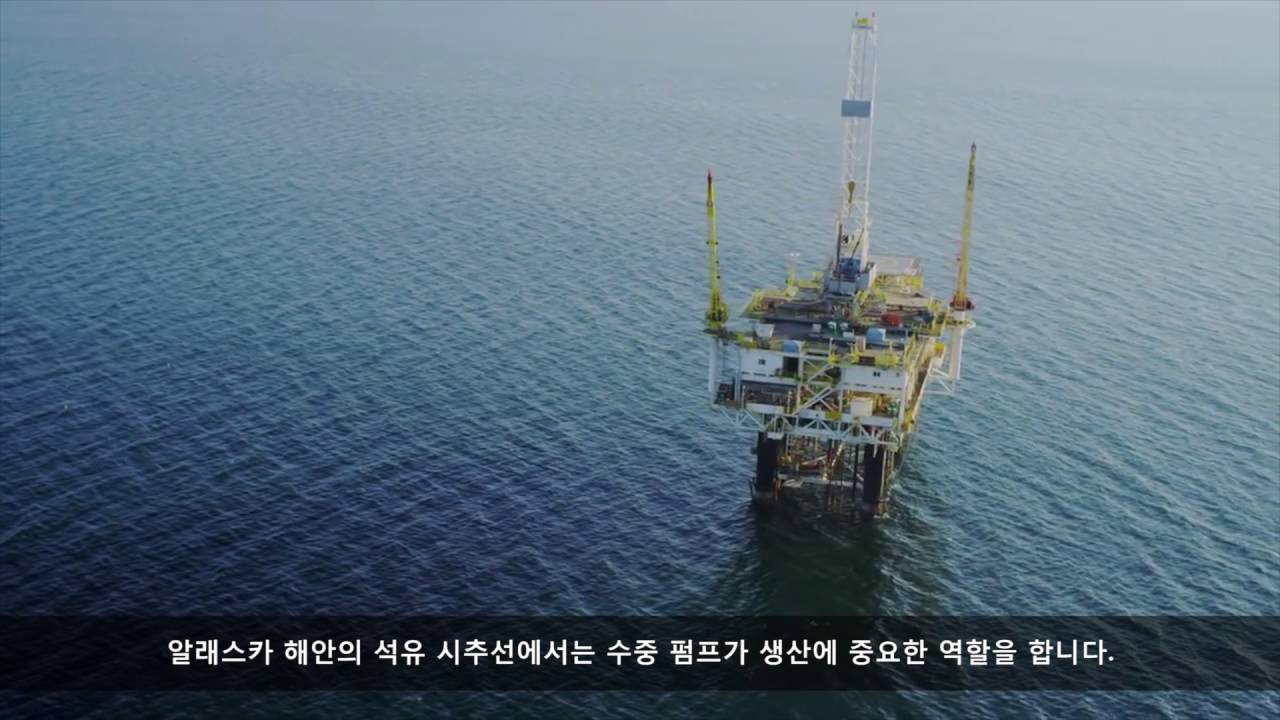
Rockwell Automation fuels the oil and gas industry with IoT subtitled

The Digital Transformation of Shell
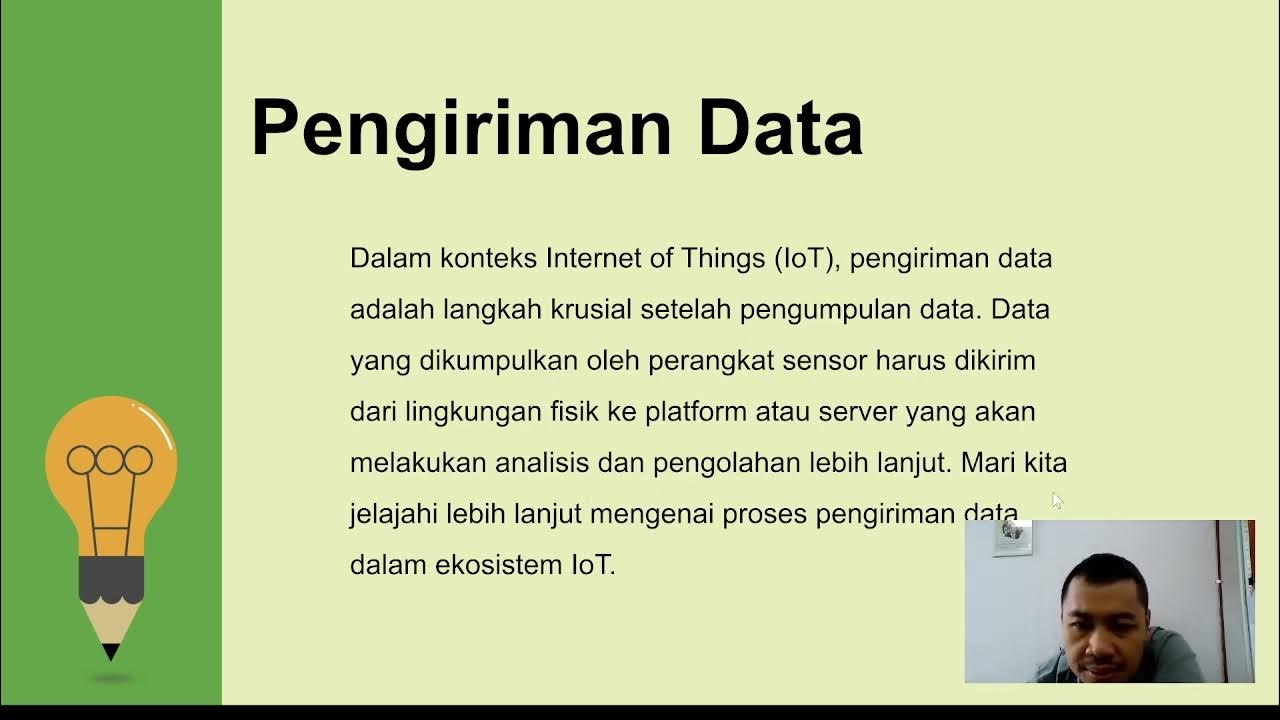
Pertemuan 4 : Pengolahan Data IOT

Industrial Internet of Things (IIOT) Explained in Hindi
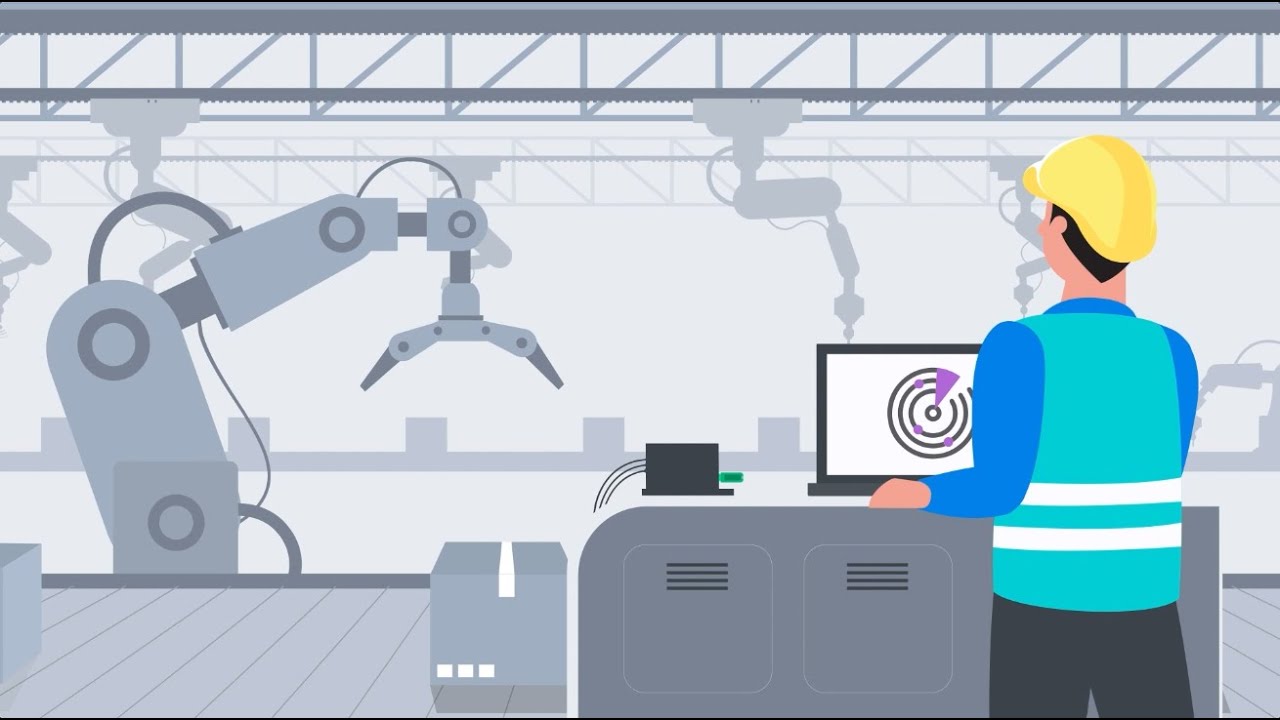
Cybersecurity for Industrial Controls and Operational Technology Environments | Security Fabric
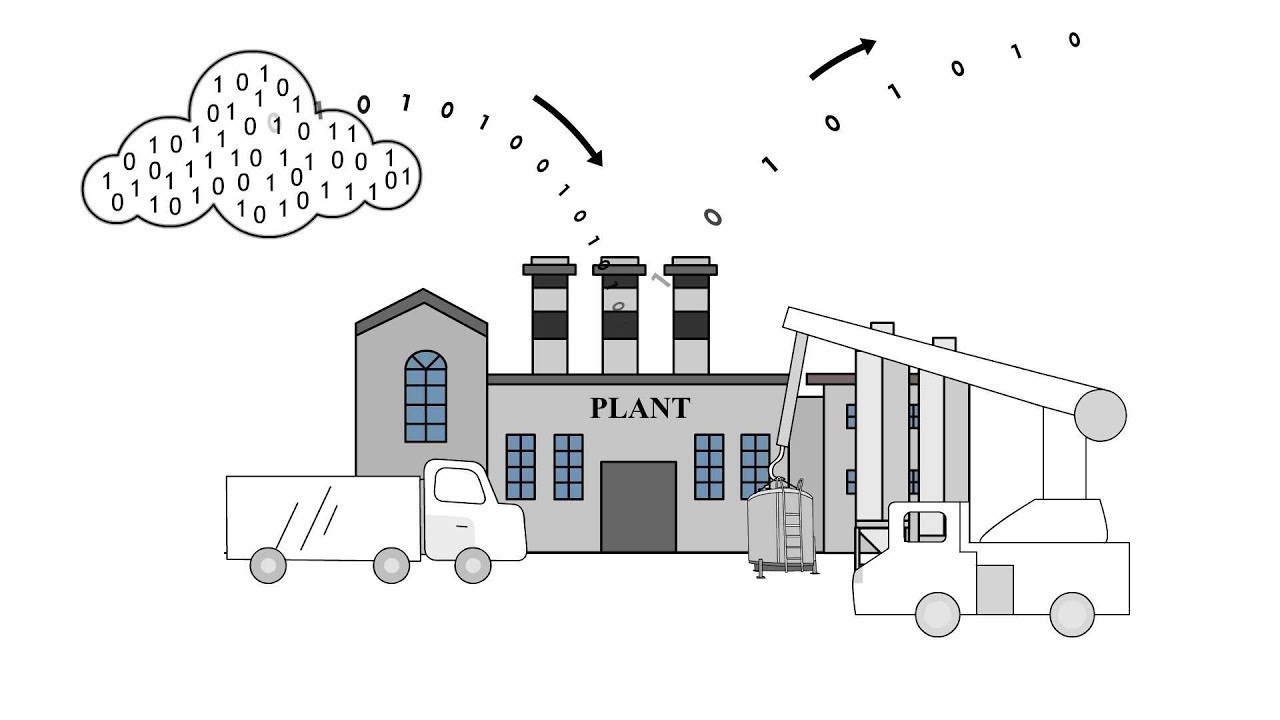
IoT, Industrial IoT, and Digital Twins in Food & Beverage Production
5.0 / 5 (0 votes)