Concept Of Quality
Summary
TLDRThe transcript delves into the concept of quality in product design and manufacturing, emphasizing the importance of meeting customer expectations through proper design, performance, and reliability. It covers various quality dimensions, including durability, performance, and environmental impact, and highlights the necessity for continuous improvement in both products and services. The document stresses the significance of using statistical techniques and feedback loops to enhance quality control. It also addresses how organizations should prioritize customer needs and ensure that products meet or exceed these requirements to maintain competitive advantage.
Takeaways
- 😀 Quality is defined as the functionality of a product and its ability to meet customer requirements, ensuring fitness for use and freedom from deficiencies.
- 😀 A high-quality product must perform according to its design specifications and fulfill customer expectations both currently and in the future.
- 😀 The importance of continuous quality improvement is emphasized for organizations to remain competitive and ensure customer satisfaction.
- 😀 Quality dimensions include reliability, performance, maintainability, environmental impact, appearance, durability, and service quality.
- 😀 Effective quality management involves a focus on all aspects, from product design and manufacturing to service and customer interaction.
- 😀 Customer requirements play a crucial role in shaping product quality, with market surveys being essential for understanding preferences and needs.
- 😀 The role of the workforce in achieving quality is crucial; trained and motivated workers contribute significantly to the overall quality and productivity.
- 😀 Process control, including statistical techniques and proper material selection, is essential for maintaining high-quality standards in manufacturing.
- 😀 A well-designed product is not only about functional specifications but also about minimizing defects through proper planning and continuous monitoring.
- 😀 In service industries, flexibility and responsiveness to customer complaints and feedback are vital for maintaining quality and ensuring customer satisfaction.
- 😀 Quality assurance requires collaboration across various departments, including marketing, production, and service, to maintain consistent product standards and meet customer expectations.
Q & A
What is the core definition of 'quality' as mentioned in the transcript?
-Quality is defined as the functioning of a product, meaning how well a product performs according to its intended purpose and customer requirements.
How is the concept of quality linked to customer satisfaction?
-Quality is tied to customer satisfaction because it involves meeting customer requirements, which include freedom from deficiencies and ensuring fitness for use, confirming to specifications.
What are the key dimensions of product quality?
-The key dimensions of product quality mentioned are reliability, performance, maintainability, environmental impact, appearance, and durability.
Why is quality improvement important for organizations?
-Quality improvement is crucial for organizations as it directly impacts their competitiveness and organizational performance by ensuring products and services meet customer expectations and enhance overall value.
How does the design process influence product quality?
-The design process is critical in determining product quality because it involves selecting appropriate materials, processes, and controls to ensure that the final product meets the required standards and functions as expected.
What role do statistical techniques play in quality control?
-Statistical techniques help monitor and control the quality of products by analyzing data to identify variations and prevent defects in the production process.
What are the factors that influence the quality of incoming materials?
-The quality of incoming materials is influenced by their selection, the process and controls in place, and the storage and transportation methods used before they are incorporated into production.
How do customer requirements impact product design?
-Customer requirements play a significant role in product design as they define the essential features, performance expectations, and usability factors that the product must meet to satisfy the target market.
What is the importance of conducting market research in the context of quality?
-Market research is vital for understanding customer demands, preferences, and expectations, which helps in designing products and services that align with market needs and enhance overall quality.
What are some common challenges in maintaining product quality during production?
-Common challenges include ensuring consistent material quality, controlling production processes, preventing defects, and maintaining high standards in inspections, storage, and transport to ensure that the final product meets quality expectations.
Outlines
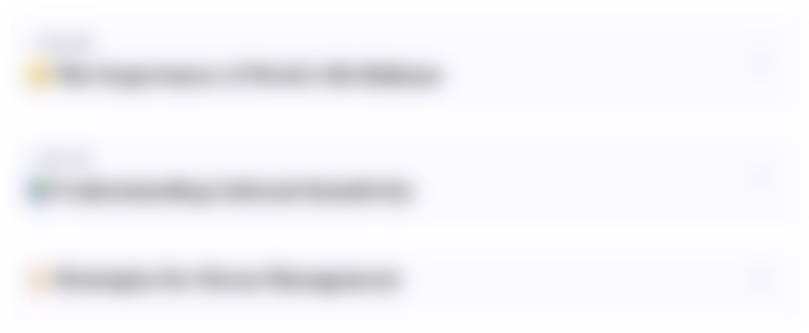
This section is available to paid users only. Please upgrade to access this part.
Upgrade NowMindmap
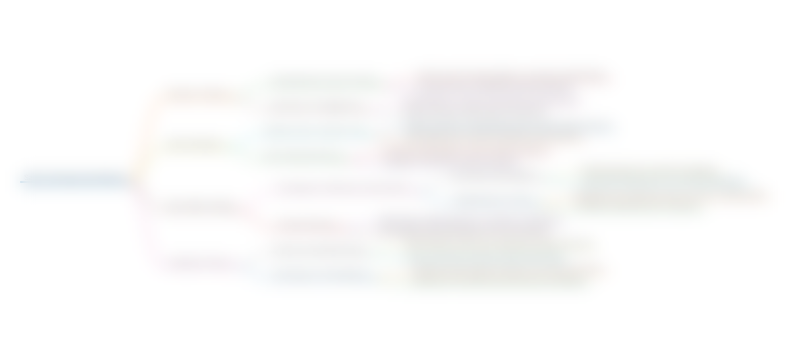
This section is available to paid users only. Please upgrade to access this part.
Upgrade NowKeywords
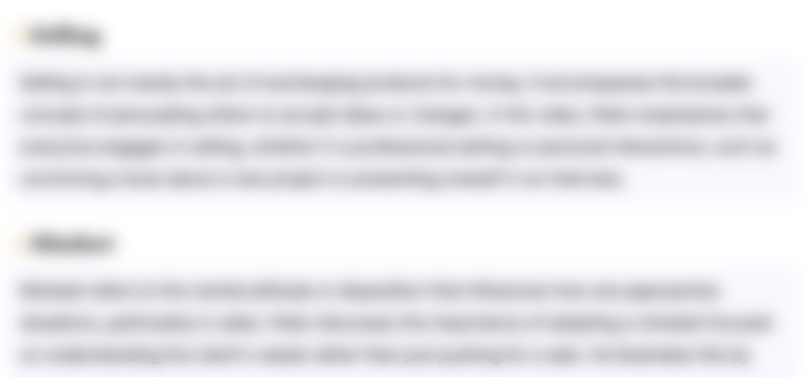
This section is available to paid users only. Please upgrade to access this part.
Upgrade NowHighlights
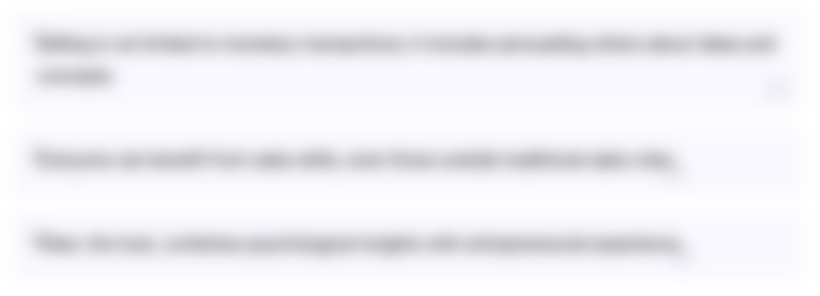
This section is available to paid users only. Please upgrade to access this part.
Upgrade NowTranscripts
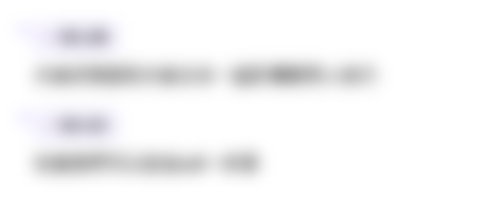
This section is available to paid users only. Please upgrade to access this part.
Upgrade NowBrowse More Related Video
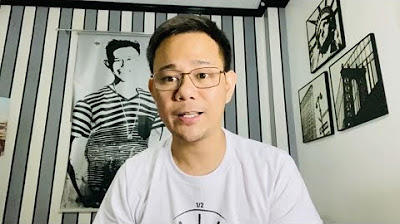
CBME 1 | Lesson 2 | Part 1/3

QFD (Quality Function Deployment): With Practical Example (PART-1)

Manajemen Produksi - Ep. 10 Pengendalian Kualitas Produk
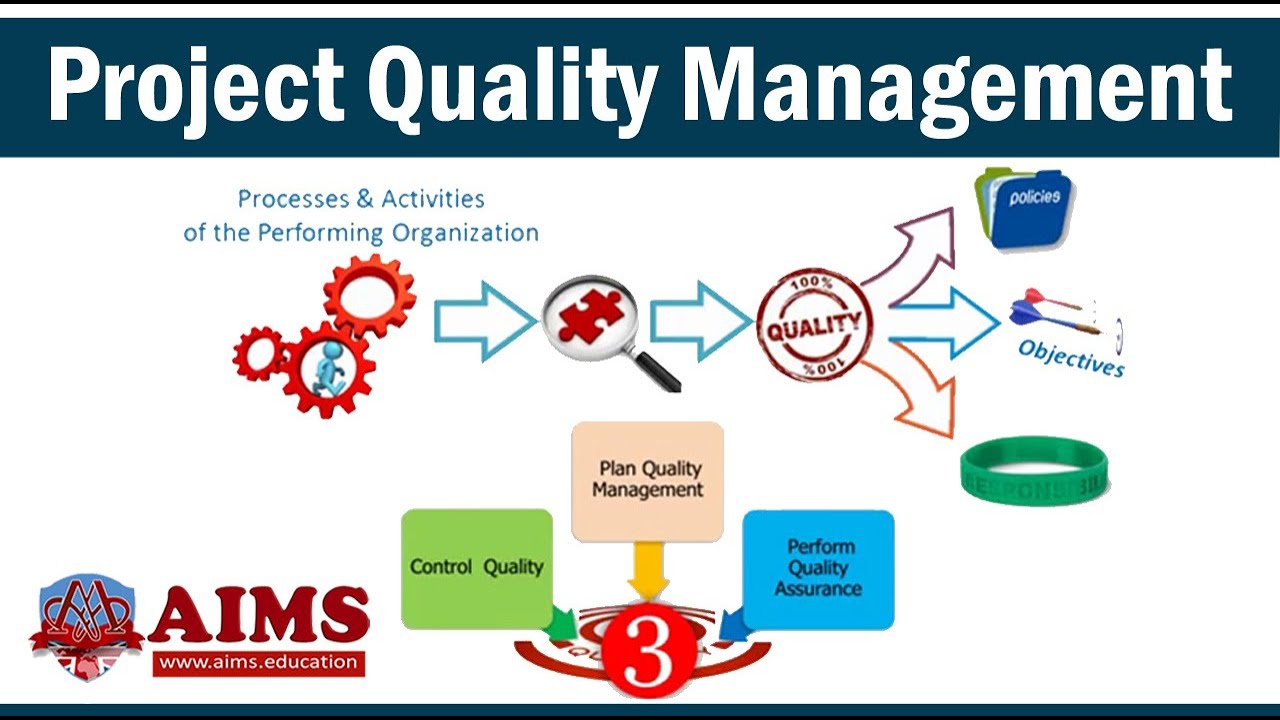
Project Quality Management - Processes and Seven Basic Quality Management Tools - AIMS UK

What is ISO 13485 for medical devices?

'SERVQUAL' or GAP model explained
5.0 / 5 (0 votes)