What is Bottleneck Analysis in Lean manufacturing ? | Bottleneck Analysis in explained with โ ๐๐๐๐๐๐๐
Summary
TLDRThis video script delves into the critical concept of bottleneck analysis, essential for identifying and resolving operational inefficiencies that lead to revenue loss, increased waiting times, poor product quality, and customer dissatisfaction. It explains the difference between short-term and long-term bottlenecks, utilizing animated examples and tools like 5Y root cause analysis and fishbone diagrams. The script also discusses strategies to overcome bottlenecks, such as increasing capacity, eliminating non-value-added steps, and balancing production lines, ultimately highlighting the benefits of streamlined processes, reduced inventory, improved product quality, and increased production capacity.
Takeaways
- ๐ Identifying bottlenecks is crucial for operations as they lead to revenue loss, increased waiting times, poor product quality, and customer dissatisfaction.
- ๐ Bottleneck analysis involves finding and fixing these operational restrictions to improve efficiency and output.
- ๐ The script explains the concept of bottlenecks with animated examples and covers the types, analysis, and benefits of addressing them.
- ๐ A bottleneck is an area in a production line that restricts the smooth flow of production, similar to how a narrow bottle neck slows the flow of liquid.
- ๐ทโโ๏ธ Bottlenecks can be caused by tasks exceeding maximum production capacity, leading to workflow delays and inefficiencies.
- ๐ There are two types of bottlenecks: short-term, caused by temporary problems, and long-term, which are reoccurring and can significantly impact production.
- ๐ Tools for bottleneck analysis include 5 Whys root cause analysis, fishbone diagrams, and the theory of constraints to identify and remove system limitations.
- ๐ Common causes of bottlenecks include poor line balancing and inadequate process controls.
- ๐ Solutions to bottlenecks may involve increasing workforce or capacity, eliminating non-value-added steps, and balancing the production line.
- ๐ก Benefits of bottleneck analysis include waste elimination, streamlined processes, reduced inventory, minimized poor quality, reduced downtime, and increased production capacity.
- ๐ฅ The video encourages viewers to subscribe, hit the bell icon for notifications, and engage with the content through likes and comments.
Q & A
What is a bottleneck in the context of operations management?
-A bottleneck is a specific area in a production line that restricts the smooth flow of production, similar to how the neck of a bottle slows down the flow of its contents.
Why is identifying bottlenecks important for a business?
-Identifying bottlenecks is essential as they can lead to loss in revenue, increased waiting time between operations, poor product quality, and loss of customers.
What are the consequences of not addressing bottlenecks in a production process?
-Not addressing bottlenecks can result in delays in workflow, reduced output, increased waste, and potentially significant financial and reputational damage to the business.
What are the two types of bottlenecks mentioned in the script?
-The two types of bottlenecks are short-term bottlenecks, which are caused by temporary problems and last for a shorter period, and long-term bottlenecks, which are recurring and can significantly impact production capacity.
What causes a short-term bottleneck?
-Short-term bottlenecks can be caused by temporary issues such as an operator being absent, delay in receiving materials, supply chain obstructions, or limited staff during holidays.
What factors contribute to a long-term bottleneck?
-Long-term bottlenecks are often due to lack of appropriate technology, limited funds and resources, an unorganized workforce, or insufficient training in lean manufacturing techniques.
What is bottleneck analysis and why is it conducted?
-Bottleneck analysis is the process of identifying where the actual problem is occurring in a production process. It is conducted to find the root cause of delays and inefficiencies, rather than just addressing the symptoms.
What are some common tools used in bottleneck analysis?
-Common tools used in bottleneck analysis include the 5 Whys root cause analysis, fishbone diagrams for visual representation of causes, and the Theory of Constraints to identify and remove limitations hindering goal achievement.
How can a company deal with identified bottlenecks?
-Companies can deal with bottlenecks by increasing capacity, eliminating non-value-added steps, and balancing the production line to ensure workload is evenly distributed across workstations.
What are the benefits of conducting bottleneck analysis?
-The benefits of bottleneck analysis include waste elimination, streamlined processes, reduced inventory, minimized poor product quality, reduced downtime, increased production capacity, and shorter lead times.
What should a viewer do if they have specific questions or comments about the video content?
-Viewers with specific questions or comments can leave them in the comment section of the video, where they may receive further clarification or discussion.
Outlines
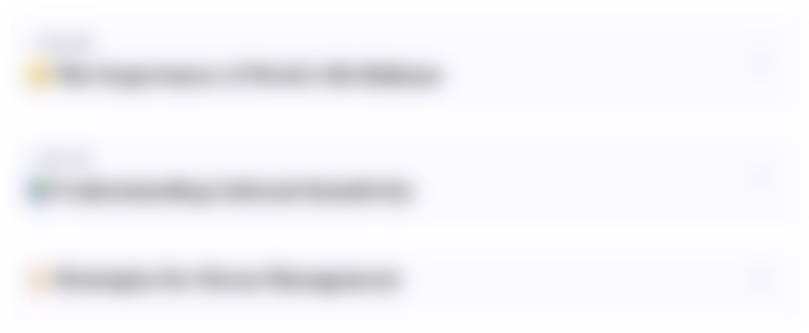
This section is available to paid users only. Please upgrade to access this part.
Upgrade NowMindmap
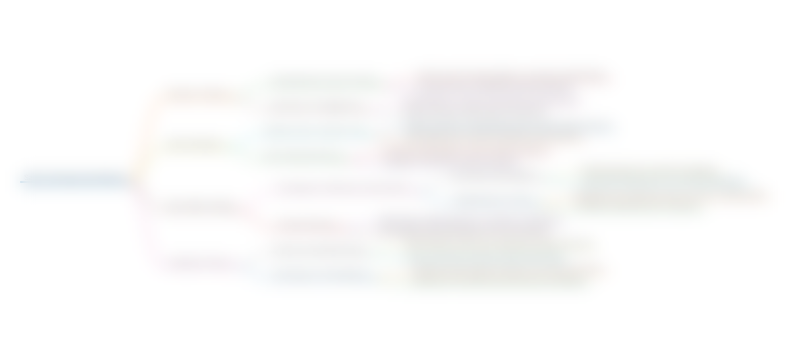
This section is available to paid users only. Please upgrade to access this part.
Upgrade NowKeywords
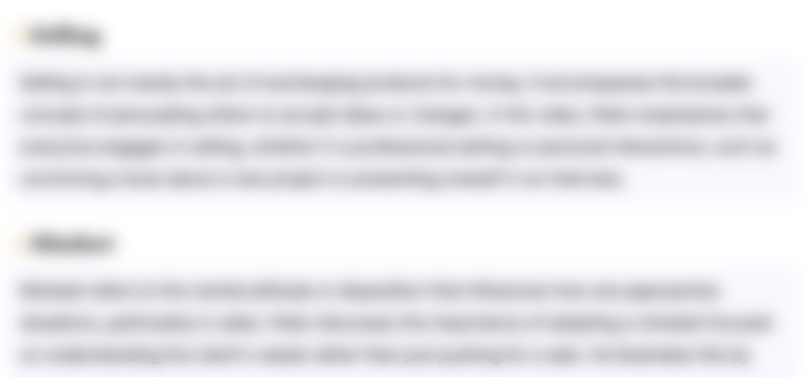
This section is available to paid users only. Please upgrade to access this part.
Upgrade NowHighlights
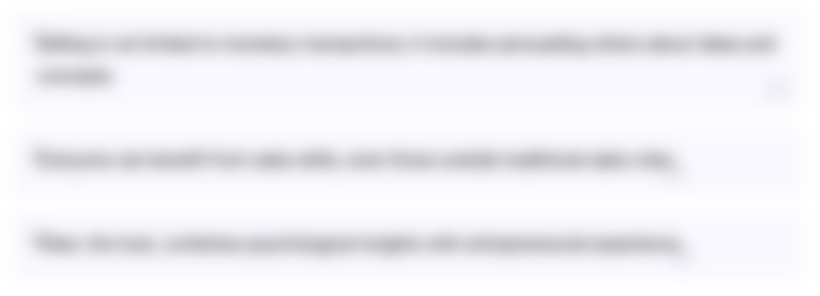
This section is available to paid users only. Please upgrade to access this part.
Upgrade NowTranscripts
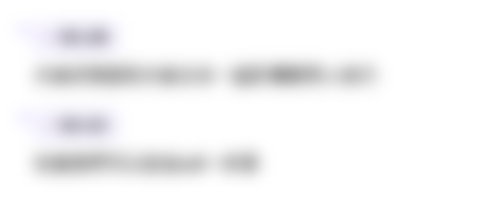
This section is available to paid users only. Please upgrade to access this part.
Upgrade Now5.0 / 5 (0 votes)