Lec 53: Example of Transformer Design
Summary
TLDRThis course on power electronic converter design focuses on the process of transformer design for a forward converter. Key topics include calculating turns ratios, inductor current ripple, and RMS values for both primary and secondary currents. It covers core material selection (ferrite for high-frequency switching), as well as the wire gauge selection based on current values. The tutorial also demonstrates practical steps in winding the transformer with different wire gauges, ensuring proper assembly. This detailed guide provides a comprehensive approach to designing transformers for DC-DC converters, making it ideal for learners in power electronics.
Takeaways
- π The design of a transformer for a forward converter involves understanding key specifications such as input voltage (12V), output voltage (30V), and switching frequency (200 kHz).
- π The turns ratio for the transformer is initially calculated as 5 based on the input and output voltage ratio and the chosen duty ratio of 0.5.
- π The output current is calculated to be 3.33A by dividing the power rating (100W) by the output voltage (30V).
- π Ripple current in the inductor (ΞiL) is calculated to be 0.75A using the equation involving the turns ratio, input voltage, output voltage, and inductance.
- π The maximum and minimum inductor currents are derived, with the maximum current being 3.705A and the minimum being 2.955A.
- π Current waveforms for the primary and secondary windings are plotted to show the behavior during the operation of the forward converter.
- π The RMS current for the secondary winding is 2.35A, while the primary RMS current is significantly higher at 11.77A.
- π The core material is selected based on switching frequency and flux density, with ferrite being chosen due to its suitability for high-frequency applications.
- π The area product equation is used to determine the size of the transformer core, leading to the selection of a ferrite core with an area product of 4800 mm^4.
- π The wire gauges for the transformer windings are chosen based on the RMS current calculations: 11 AWG for the primary, 18 AWG for the secondary, and 26 AWG for the tertiary winding.
- π The practical design process involves winding the transformer using copper wires (enameled), securing each winding with tape, and assembling the core with the necessary turns for each winding.
Q & A
What is the primary focus of the course in the transcript?
-The course focuses on the design of power electronic converters, with an emphasis on transformer design in the context of forward converters.
What is the significance of the area product method in transformer design?
-The area product method is a crucial technique in transformer design to determine the core area required to handle the magnetic flux and current density, ensuring efficient transformer operation.
What are the main specifications provided for the forward converter design example?
-The main specifications are an input voltage of 12V, output voltage of 30V, peak power rating of 100W, switching frequency of 200 kHz, and a duty ratio of 0.5.
How is the turns ratio (N2/N1) for the transformer calculated in this example?
-The turns ratio (N2/N1) is calculated using the formula Vo/Vin, which gives a ratio of 5, considering the chosen duty ratio of 0.5.
What is the inductor current ripple (delta iL) for the forward converter?
-The current ripple (delta iL) for the forward converter is calculated as 0.75A, based on the voltage inputs and the switching characteristics.
How do the primary and secondary current waveforms compare in the forward converter?
-The primary current waveform is reflected in the secondary current waveform, with the peak of the secondary current being the same as the inductor current, scaled by the turns ratio.
What are the RMS current values for the primary and secondary windings?
-The RMS current for the secondary winding is 2.35A, while the RMS current for the primary winding is 11.77A.
What role does the tertiary winding play in the transformer design?
-The tertiary winding, or demagnetizing winding, helps to ensure the transformer core gets demagnetized during the off-period, preventing a sudden shift in the magnetizing current when the switch is turned off.
How is the magnetizing inductance (Lm) of the primary winding calculated?
-The magnetizing inductance (Lm) of the primary winding is calculated using the formula involving the core material's permeability, the number of turns (N1), and the core's cross-sectional area.
What wire gauges are selected for the primary, secondary, and tertiary windings?
-For the primary winding, 11 AWG wire is selected, for the secondary winding, 18 AWG wire is chosen, and for the tertiary winding, 26 AWG wire is used.
Outlines
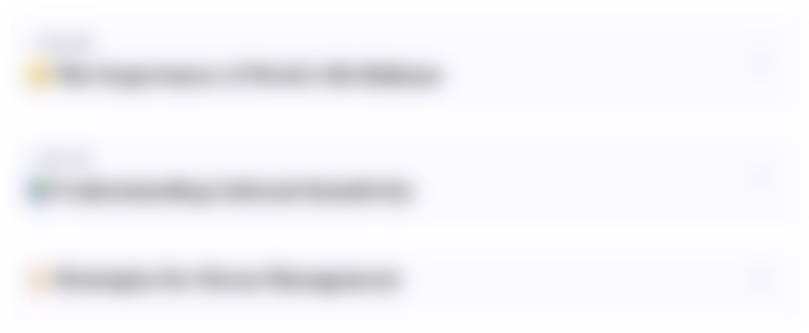
This section is available to paid users only. Please upgrade to access this part.
Upgrade NowMindmap
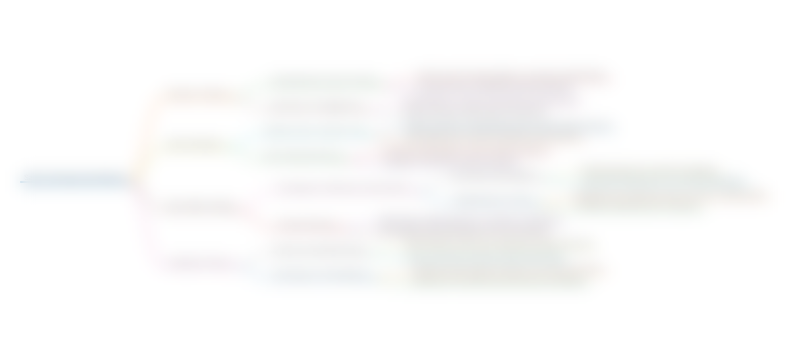
This section is available to paid users only. Please upgrade to access this part.
Upgrade NowKeywords
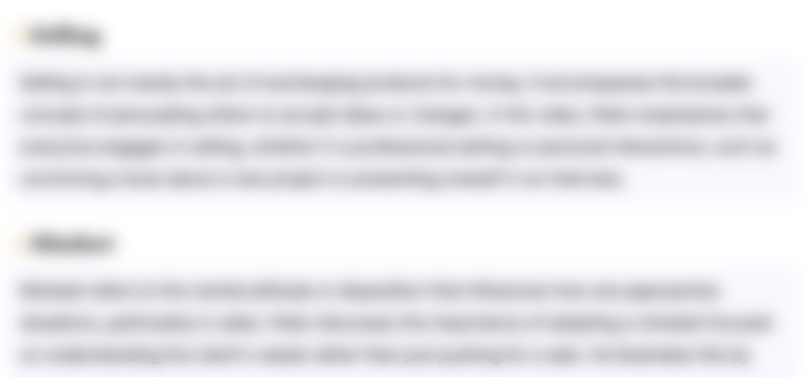
This section is available to paid users only. Please upgrade to access this part.
Upgrade NowHighlights
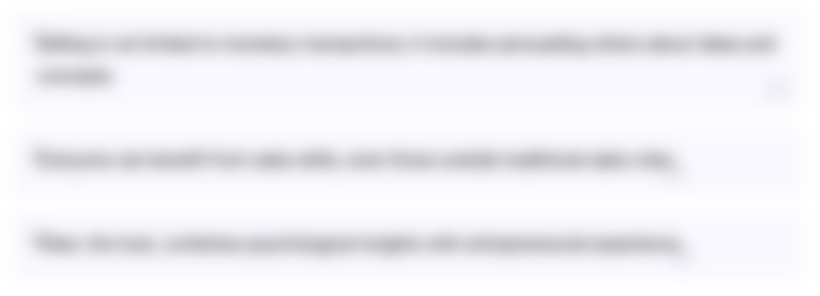
This section is available to paid users only. Please upgrade to access this part.
Upgrade NowTranscripts
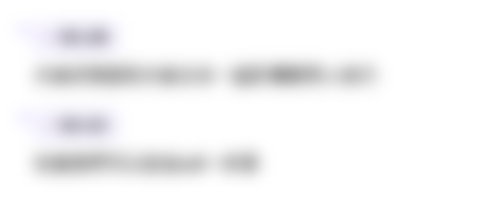
This section is available to paid users only. Please upgrade to access this part.
Upgrade NowBrowse More Related Video
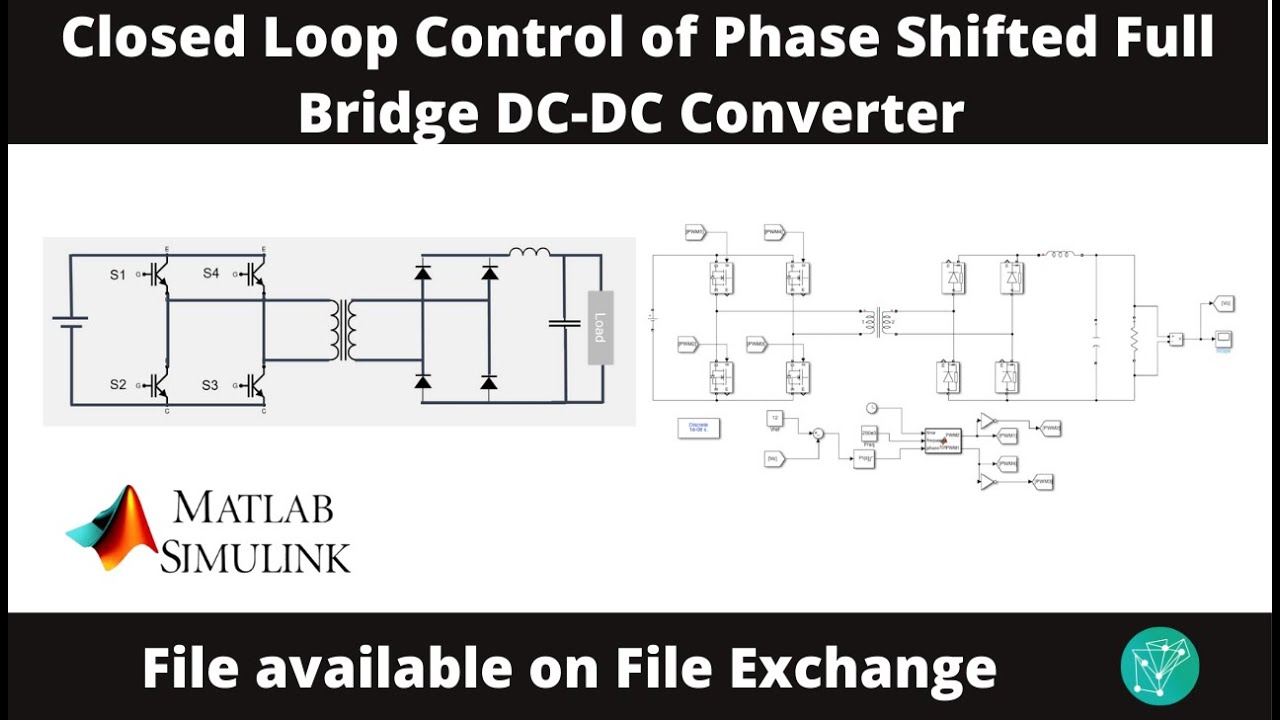
Closed loop control of Phase-Shifted Full bridge DC-DC Converter in MATLAB/Simulink!
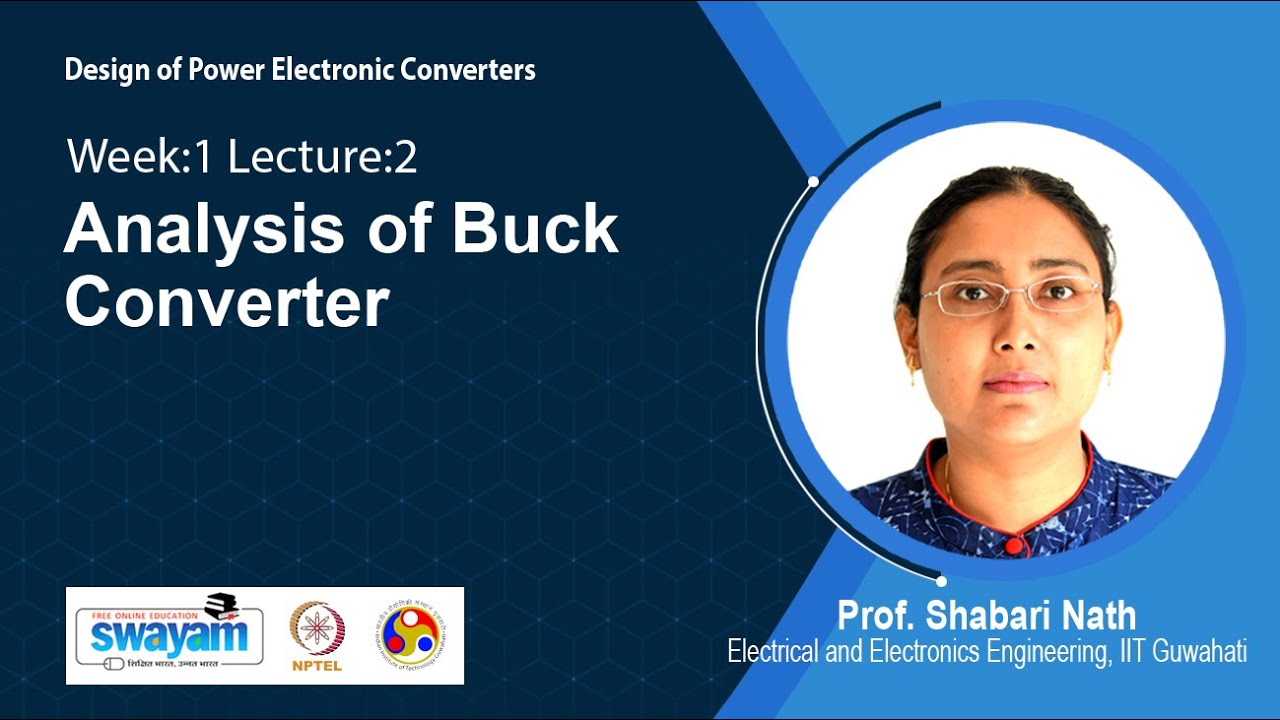
Lec 2: Analysis of Buck Converter
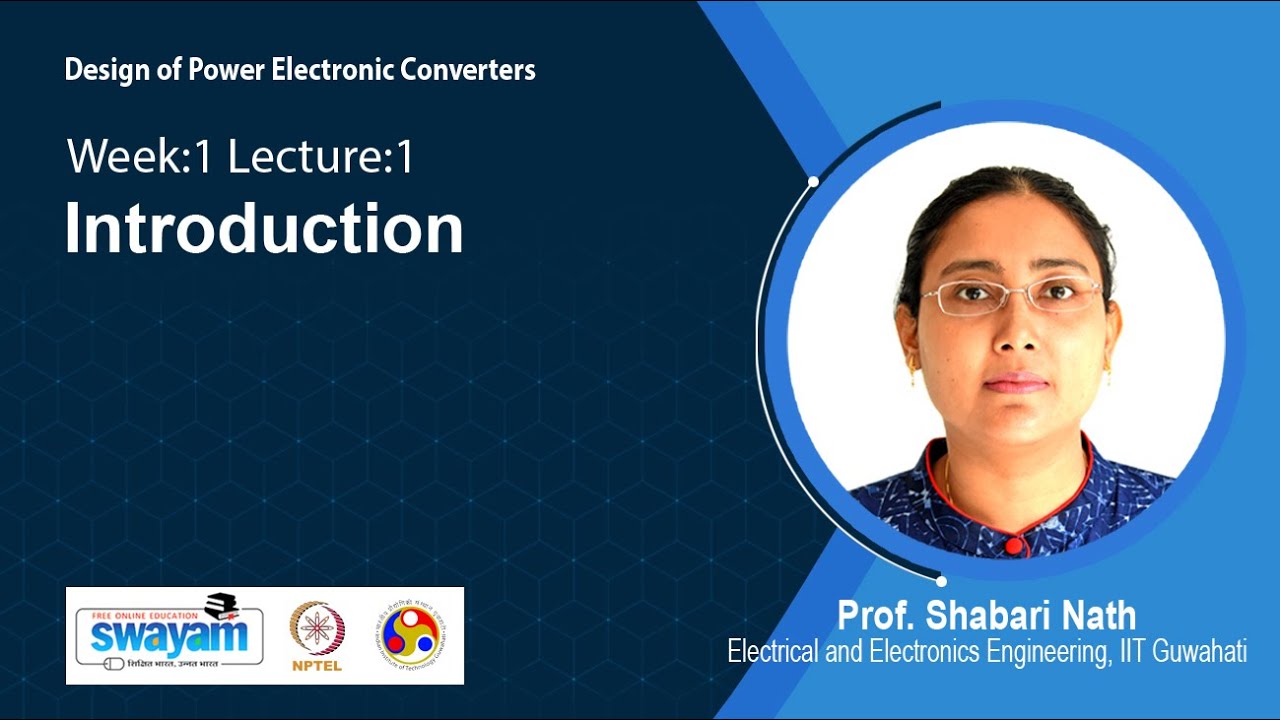
Lec 1: Introduction
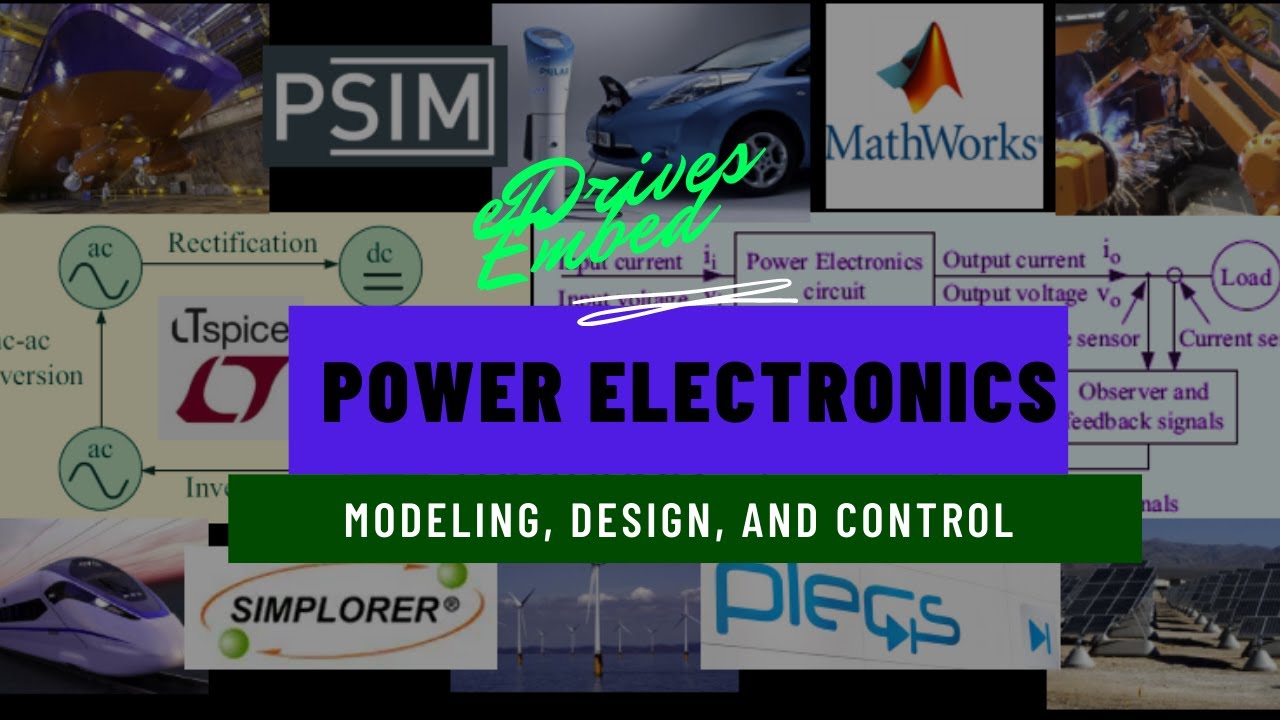
Capacitor Amp Second Balance and LTspice Buck converter Simulation
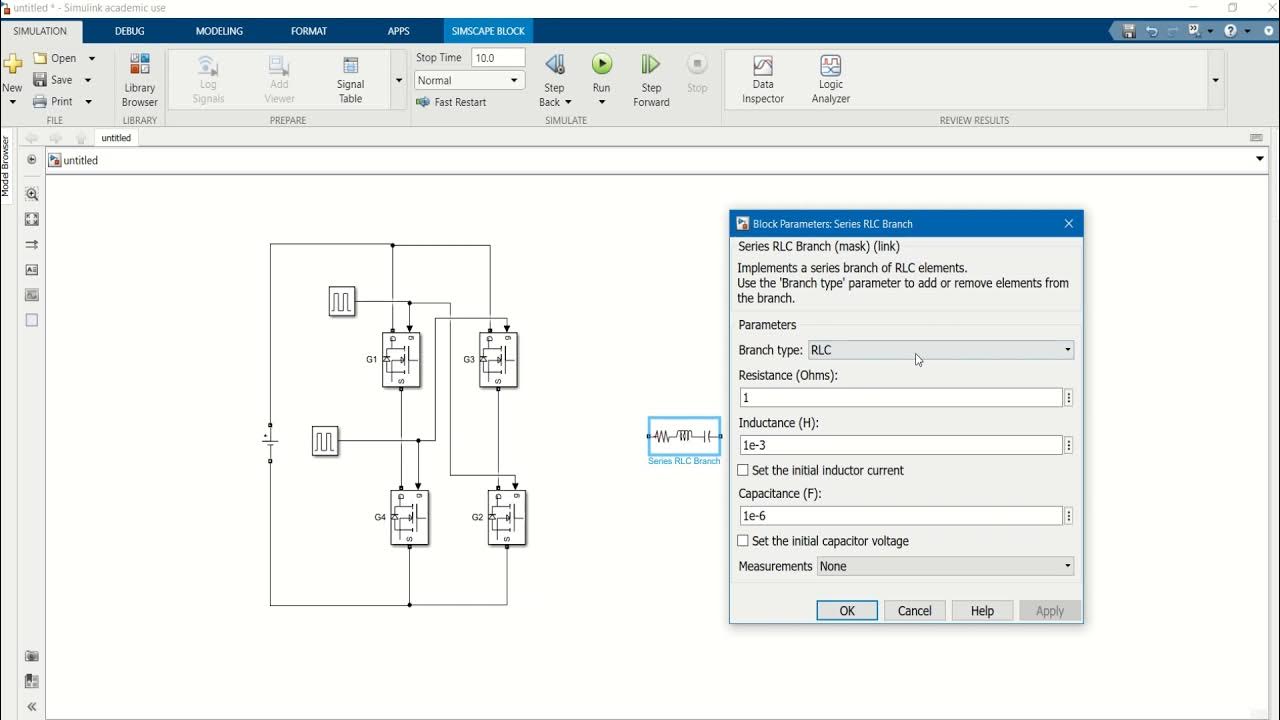
Design of DC AC Converter Using MATLAB SIMULINK
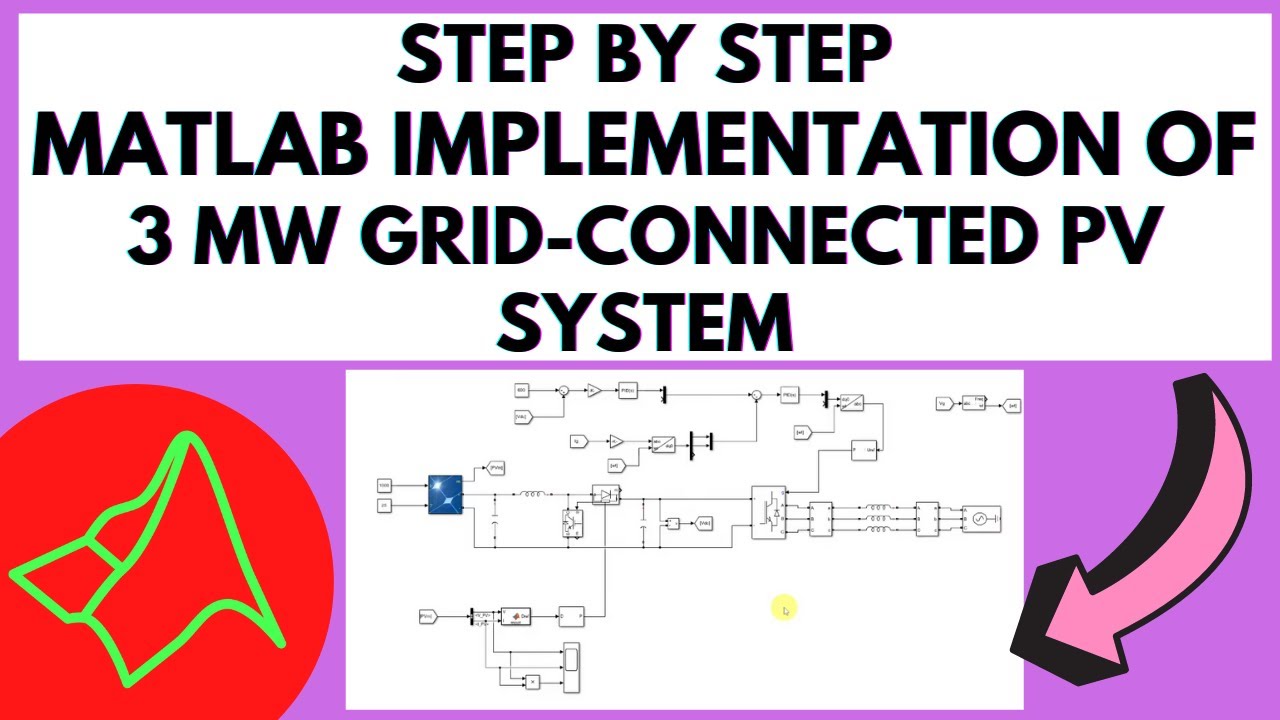
grid connected pv system | Step by step implementation of 3 MW Grid-connected Solar PV System
5.0 / 5 (0 votes)