Tutorial Penyusunan Anggaran Produksi Part 2 Kebijakan Stabilitas Persediaan
Summary
TLDRThis video explains how to create a production budget with stable inventory levels. The process involves calculating inventory differences, breaking them down by quarter, and adjusting for planned sales while maintaining consistent stock. Starting with an initial inventory of 5,000 units and ending with 7,500, each quarter sees an increase of 625 units in inventory. Production is calculated based on sales and inventory requirements, with a detailed breakdown for each quarter, ensuring that the production plan aligns with inventory stability and sales projections.
Takeaways
- ๐ The second policy is about creating a production budget using inventory stability.
- ๐ The example used for the production budget calculation remains the same throughout the explanation.
- ๐ The inventory level at the beginning is 5,000 units, and the ending inventory is 7,500 units, giving a difference of 2,500 units.
- ๐ This difference is divided by four because the budget is calculated on a quarterly basis, resulting in a quarterly difference of 625 units.
- ๐ If the initial inventory is lower than the ending inventory, the final inventory for each quarter is calculated by adding the difference (625 units) to the initial inventory.
- ๐ If the initial inventory is higher than the ending inventory, the final inventory for each quarter is calculated by subtracting the difference from the initial inventory.
- ๐ In this case, the initial inventory (5,000 units) is smaller than the ending inventory (7,500 units), so each quarterโs ending inventory is calculated by adding 625 units to the initial inventory.
- ๐ The quarterly inventory levels are calculated as follows: 5,000 + 625 = 5,625 for Q1, 5,625 + 625 = 6,250 for Q2, and so on, until reaching 7,500 units in Q4.
- ๐ The sales plan remains consistent at 5,000 units for each quarter, and these values are used to calculate production requirements.
- ๐ After calculating the ending inventories for each quarter, the production for each quarter is determined by subtracting the initial inventory from the desired ending inventory.
- ๐ The total production budget is derived by adding up the required production for each quarter, with a total value of 27,500 units.
Q & A
What is the main goal of the policy discussed in the script?
-The main goal of the policy is to maintain the stability of inventory while preparing production budgets. This involves ensuring a constant inventory level each period, calculated through specific inventory adjustments.
Why is the inventory difference divided by four in the script?
-The inventory difference is divided by four because the production budget is being prepared on a quarterly basis. This allows for equal distribution of inventory adjustments across the four quarters.
What happens when the beginning inventory is less than the ending inventory?
-When the beginning inventory is less than the ending inventory, the ending inventory for each quarter is calculated by adding the quarterly difference to the beginning inventory.
What method is used to calculate the ending inventory when the beginning inventory exceeds the ending inventory?
-When the beginning inventory is greater than the ending inventory, the ending inventory for each quarter is calculated by subtracting the quarterly difference from the beginning inventory.
What is the significance of using the same sales forecast for each quarter?
-Using the same sales forecast for each quarter simplifies the budgeting process, ensuring that production plans remain consistent and aligned with the forecasted sales throughout the year.
How is the production budget calculated in the script?
-The production budget is calculated by subtracting the beginning inventory from the total inventory needed for each quarter, considering the planned sales and adjustments for inventory stability.
Why does the script mention specific numbers such as 5,000 and 7,500 units for inventory?
-These numbers represent the initial and final inventory levels, which are used as examples in the script to demonstrate how the inventory adjustments are made to maintain inventory stability.
What role do the quarterly periods (TW1, TW2, TW3, TW4) play in the script?
-The quarterly periods (TW1, TW2, TW3, TW4) represent the four quarters of the year, where the inventory adjustments and production budgets are calculated to ensure that inventory levels are stable throughout the year.
How does the script handle the transition of inventory values between quarters?
-At the end of each quarter, the ending inventory becomes the beginning inventory for the next quarter. This ensures that inventory continuity is maintained across all four quarters.
What is the final step in the production budget calculation as mentioned in the script?
-The final step in the production budget calculation is summing up the values of production requirements across all quarters, ensuring that the total production needed matches the desired inventory levels and sales forecasts.
Outlines
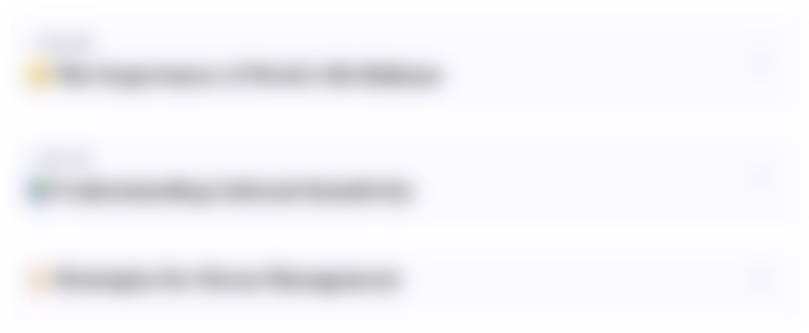
This section is available to paid users only. Please upgrade to access this part.
Upgrade NowMindmap
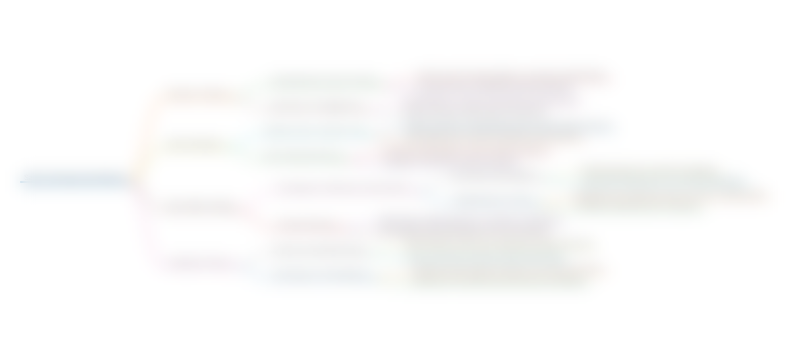
This section is available to paid users only. Please upgrade to access this part.
Upgrade NowKeywords
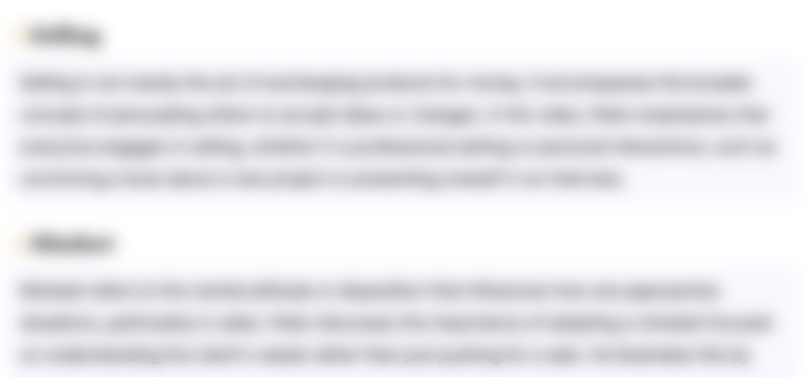
This section is available to paid users only. Please upgrade to access this part.
Upgrade NowHighlights
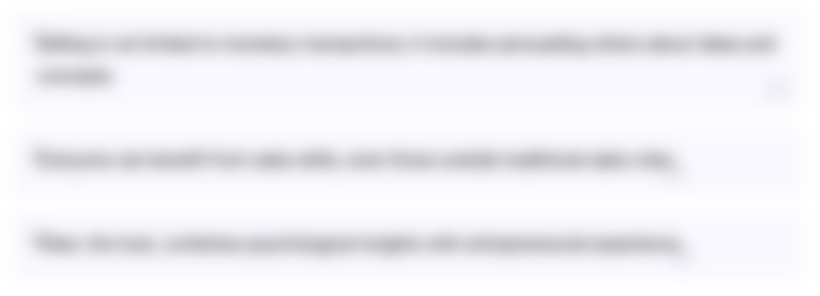
This section is available to paid users only. Please upgrade to access this part.
Upgrade NowTranscripts
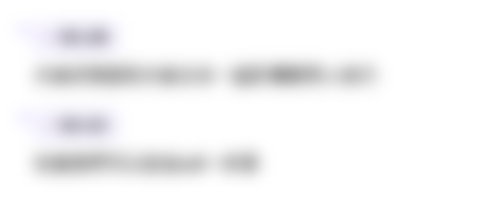
This section is available to paid users only. Please upgrade to access this part.
Upgrade Now5.0 / 5 (0 votes)