The Genius of 3D Printed Rockets
Summary
TLDRRelativity Space, a pioneering startup, is revolutionizing space travel with the world's largest 3D metal printer, capable of manufacturing an entire rocket, including fuel tanks and engines, within 60 days. This innovative approach reduces the need for traditional manufacturing tools and accelerates production time from years to months. The company's vision is to democratize space access, potentially making space travel more affordable and contributing to humanity's expansion to Mars. The video also features an Omaze campaign offering a chance to win a trip to space with Virgin Galactic, supporting Space for Humanity's mission for a sustainable future.
Takeaways
- ๐ Relativity Space is a startup that has built the world's largest 3D metal printer to manufacture entire rockets, including fuel tanks and engines, within 60 days.
- ๐ฅ The printing process involves a plasma discharge and wire melt team, with the rocket's body being effectively melted together one tiny bit at a time.
- ๐ก๏ธ The temperature used in the process is just above the melting point for aluminum, which is approximately 660 degrees Celsius.
- ๐งต The raw material for the rocket is an aluminum alloy wire spool, from which the printer operates at about 10 inches per second.
- ๐ฐ๏ธ 3D printing a rocket offers advantages such as reduced manufacturing time and the ability to create complex parts that are difficult with traditional techniques.
- โ๏ธ Traditional rocket manufacturing requires building tools before the rocket, like NASA's Space Launch System which took 11 years to develop compared to Relativity Space's 5.5 years.
- ๐ก Relativity Space uses software to simulate the print before printing, which helps to avoid issues like warping and material falling out of place.
- ๐ฉ The surface roughness of the 3D printed rocket does not cause aerodynamic problems and is smoothed out in the joint sections post-printing.
- ๐ Metal 3D printing has been used in the aerospace industry for over a decade, mainly for small complex parts like injectors, and has been adopted industry-wide.
- ๐ ๏ธ 3D printing reduces the number of parts needed, which is beneficial for high-heat areas like the combustion chamber, where traditionally thousands of small pipes would be needed.
- ๐ The strength of 3D printed materials can be greater than traditionally built parts due to the rapid melting and cooling process, allowing for the development of custom strong alloys.
- ๐ Rapid iteration is another benefit of 3D printing, enabling quick building, testing, and redesigning of parts, which is integral to software-driven manufacturing.
- ๐ The future of Relativity Space includes plans for rockets capable of reaching the moon and Mars, with the ultimate vision of building an industrial base on Mars.
Q & A
Who built the world's largest 3D metal printer?
-Relativity Space, a startup aiming to print an entire rocket in just 60 days, built the world's largest 3D metal printer.
What is the melting point of aluminum?
-The melting point of aluminum is 660 degrees Celsius.
Why are stiffeners added to the rocket structure?
-Stiffeners are added to prevent the rocket from buckling and crumpling, similar to how pressure inside an unopened Coke can prevents it from being easily crushed.
What is the primary reason for using 3D printing to manufacture rockets?
-3D printing allows for rapid iteration, reduces the number of parts, and eliminates the need for custom tooling, significantly cutting down production time and costs.
What are the four major systems of a rocket?
-The four major systems of a rocket are payload, guidance, structural, and propulsion.
How does 3D printing improve the manufacturing of rocket injectors?
-3D printing allows rocket injectors to be made in one piece, reducing the production time from nine months to two weeks and cutting costs by ten times.
What is one of the challenges in 3D printing rockets, and how is it addressed?
-One challenge is that printing without prior simulation can result in warped and unusable parts. Relativity Space addresses this by using software that reverse warps the parts before printing to ensure they are perfectly straight.
What is the temperature inside a rocket's combustion chamber?
-The temperature inside a rocket's combustion chamber can reach up to 3,500 Kelvin, which is hot enough to melt virtually any metal.
How does 3D printing reduce the complexity of manufacturing rocket nozzles?
-3D printing allows for the creation of cooling channels directly within the rocket nozzle, eliminating the need for thousands of individual pipes and significantly simplifying the manufacturing process.
What long-term vision does Relativity Space have for its 3D printing technology?
-Relativity Space aims to shrink its factory down to something that can be launched to Mars to build an industrial base, ultimately supporting the vision of human settlement on Mars.
How does the surface roughness of 3D printed rockets affect their performance?
-The surface roughness only adds an extra 5 to 10% of the mass and does not cause any aerodynamic problems, making the rockets aerodynamically equivalent to traditionally manufactured rockets.
Why is rapid iteration a significant advantage in 3D printing rocket parts?
-Rapid iteration allows for quick testing and redesigning, enabling continuous improvements in rocket parts without the need for fixed tooling, which speeds up the development process.
How does 3D printing contribute to lowering the cost of space travel?
-3D printing reduces the number of parts, eliminates the need for custom tooling, and allows for rapid iteration, which collectively lowers the production costs and, consequently, the cost of space travel.
What is the purpose of the partnership between Omaze and Space for Humanity?
-The partnership aims to expand access to space and train global leaders to create a sustainable future, with part of the contributions supporting this cause.
Outlines
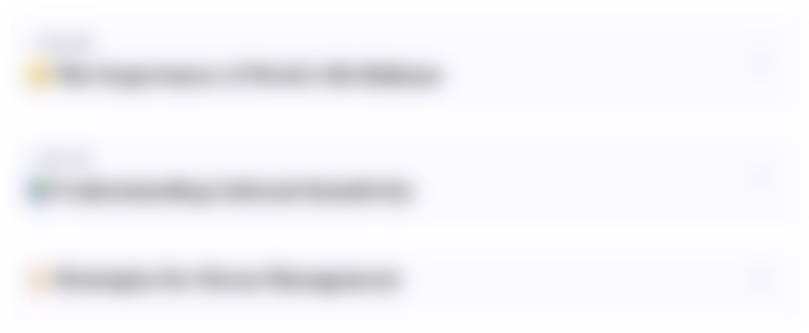
This section is available to paid users only. Please upgrade to access this part.
Upgrade NowMindmap
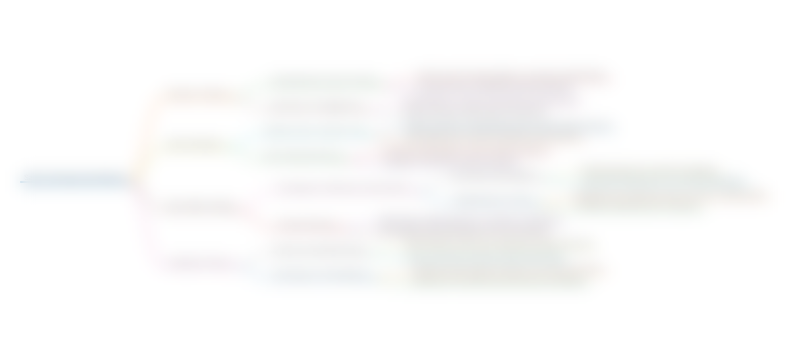
This section is available to paid users only. Please upgrade to access this part.
Upgrade NowKeywords
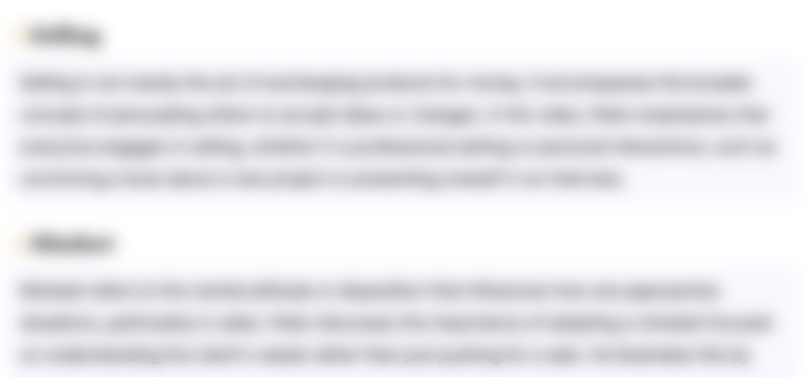
This section is available to paid users only. Please upgrade to access this part.
Upgrade NowHighlights
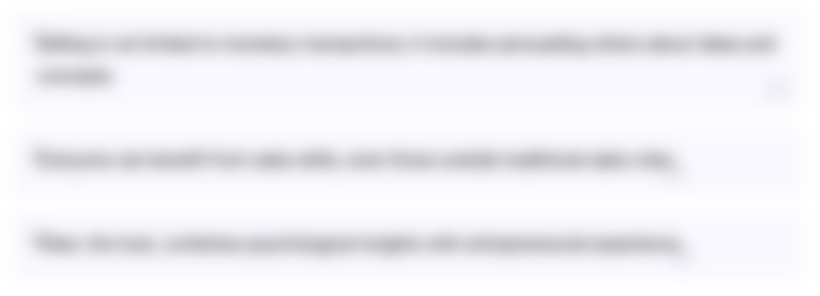
This section is available to paid users only. Please upgrade to access this part.
Upgrade NowTranscripts
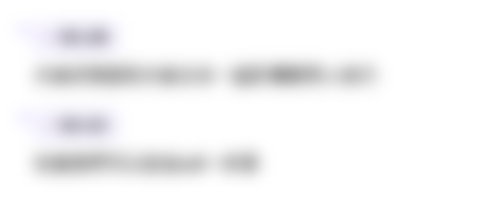
This section is available to paid users only. Please upgrade to access this part.
Upgrade NowBrowse More Related Video
5.0 / 5 (0 votes)