Ciclo PDCA: Como funciona
Summary
TLDRIn this video, the speaker introduces the PDCA (Plan-Do-Check-Act) cycle, a strategic tool for improving processes in businesses and daily life. The cycle helps identify problems, optimize resources, and increase productivity by continuously refining processes through planning, execution, monitoring, and adjustment. The speaker emphasizes the importance of thorough planning and consistent reflection to achieve better results. While PDCA is often used in industries and in implementing ISO standards, its principles can also be applied personally to enhance time management and efficiency. The video encourages viewers to embrace PDCA for continuous improvement.
Takeaways
- 😀 The PDCA cycle is a strategic management tool used to improve industrial processes and achieve better results.
- 😀 PDCA stands for Plan, Do, Check, Act, and it represents a continuous improvement cycle.
- 😀 The first phase, Plan, involves setting objectives, determining necessary resources, and identifying problems in the process.
- 😀 The Do phase is where plans are put into action by implementing strategies, processes, and workflows.
- 😀 In the Check phase, the results are analyzed to compare against the planned goals and indicators.
- 😀 The Act phase involves standardizing successful strategies and addressing problems that occurred during the Check phase.
- 😀 The PDCA cycle is iterative, meaning after completing one cycle, a new cycle is planned with corrective actions for continuous improvement.
- 😀 Proper planning is essential for the PDCA cycle to succeed, as skipping this step can result in ineffective execution and weak results.
- 😀 The PDCA cycle is widely used in quality management systems, including ISO 9001 and ISO 14000, as a foundational principle.
- 😀 PDCA principles can also be applied outside the industrial setting, such as improving personal productivity and eliminating waste at home.
- 😀 The PDCA method encourages continuous growth by regularly evaluating and refining processes and outcomes.
Q & A
What is the PDCA cycle and how does it work?
-The PDCA cycle (Plan-Do-Check-Act) is a strategic management tool used for continuous improvement of processes. It involves four stages: Planning the objectives and resources, Doing by implementing the plan, Checking the outcomes against set goals, and Acting on the results to correct and improve the process. The cycle repeats for continuous optimization.
Why is PDCA considered a cycle?
-PDCA is considered a cycle because it involves continuous loops of improvement. After completing one cycle, you plan again based on the results, then execute, check, and act on new findings, ensuring the process keeps improving over time.
What happens during the 'Plan' stage of PDCA?
-In the 'Plan' stage, objectives are established, resources (such as materials and personnel) are determined, process issues are identified, and measurable goals are set. This stage lays the foundation for the entire process.
What is the significance of the 'Do' stage in PDCA?
-The 'Do' stage involves putting the plan into action. It requires executing the processes as outlined in the planning stage, ensuring that all tasks and steps are followed and that resources are allocated effectively.
How does the 'Check' stage of PDCA contribute to the process?
-The 'Check' stage focuses on evaluating the results. This includes comparing actual outcomes with the predefined goals and indicators, identifying discrepancies, and finding areas that need improvement.
What is meant by the 'Act' stage in PDCA?
-The 'Act' stage is where corrective actions are taken based on the results from the 'Check' stage. If something went wrong, corrective measures are implemented, and improvements are made. This step ensures the process is refined before starting the next cycle.
How can PDCA be applied outside of industrial settings?
-PDCA can be applied in personal life to optimize time management, reduce waste, and increase productivity. For example, it can be used to streamline household activities, manage personal tasks more efficiently, and continuously improve daily routines.
What are the consequences of not following the PDCA cycle properly?
-If PDCA is not followed correctly, it can lead to poor results, as people may jump into execution without proper planning. This often results in weak checks, ineffective corrective actions, and a lack of continuous improvement, ultimately hindering overall progress.
Why is planning considered a crucial step in the PDCA process?
-Planning is critical because it sets clear objectives, defines resources, and outlines processes. A solid plan ensures that actions are focused and purposeful, reducing the chances of mistakes and making the subsequent 'Do' and 'Check' stages more effective.
How does PDCA relate to ISO standards like ISO 9001?
-PDCA forms the foundation of many ISO standards, including ISO 9001, which focuses on quality management. It ensures that organizations continuously improve their processes by planning, executing, evaluating, and acting based on results, aligning with ISO's focus on systematic quality control.
Outlines
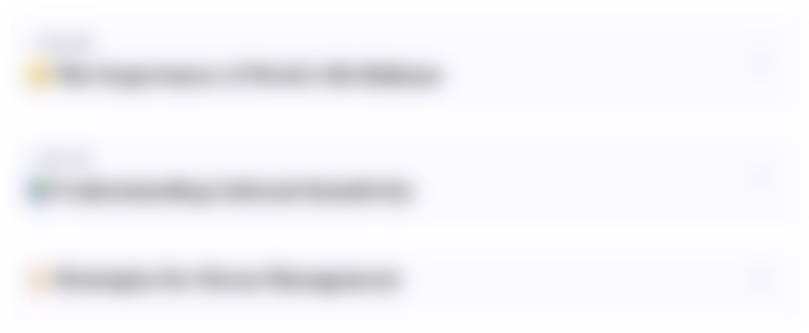
This section is available to paid users only. Please upgrade to access this part.
Upgrade NowMindmap
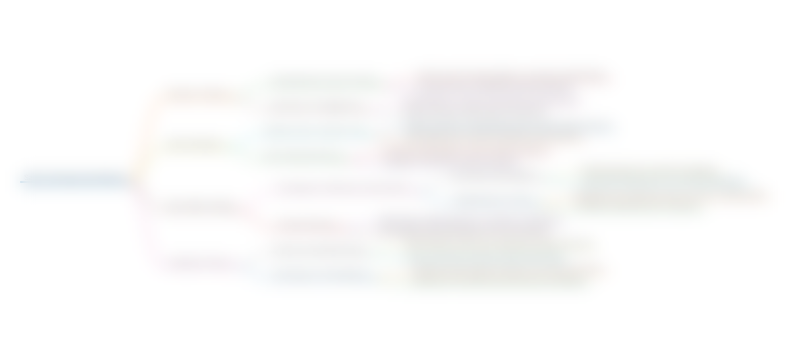
This section is available to paid users only. Please upgrade to access this part.
Upgrade NowKeywords
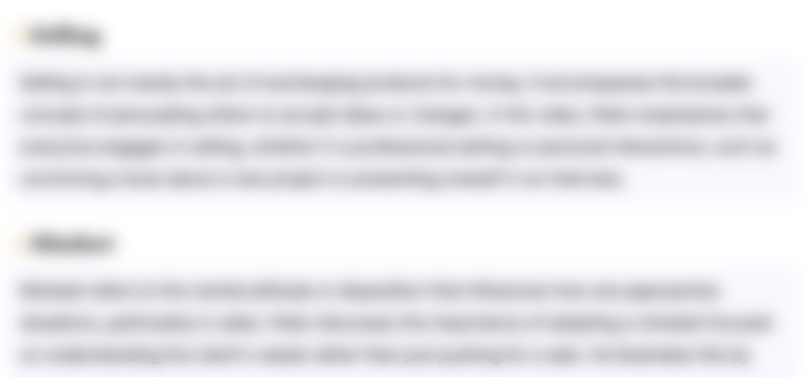
This section is available to paid users only. Please upgrade to access this part.
Upgrade NowHighlights
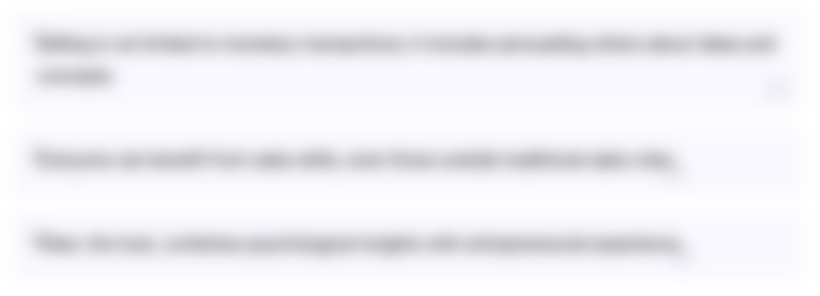
This section is available to paid users only. Please upgrade to access this part.
Upgrade NowTranscripts
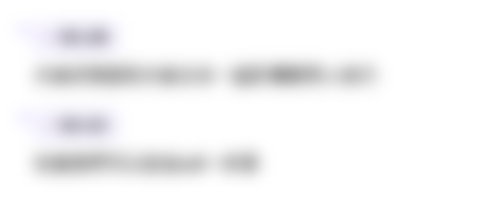
This section is available to paid users only. Please upgrade to access this part.
Upgrade NowBrowse More Related Video
5.0 / 5 (0 votes)