Diagrama de Ishikawa (Ferramenta da Qualidade): Teoria + Exemplo Prático
Summary
TLDRThis video explains the concept and construction of a cause-and-effect diagram, also known as a Fishbone or Ishikawa diagram. It highlights the diagram’s use in identifying potential causes of a problem, emphasizing its role in root cause analysis. The video covers various categories for grouping causes, such as method, workforce, machine, material, measurement, and environment. It uses the example of misaligned seams in garment production, demonstrating how to categorize and address different causes. The video stresses the importance of collaboration in creating the diagram and provides practical guidance on its application for problem-solving.
Takeaways
- 😀 A Fishbone Diagram (also called a Cause and Effect Diagram) is a tool used to identify potential causes of a problem or effect.
- 😀 The tool is widely used in root cause analysis and was popularized by Kaoru Ishikawa, a quality expert.
- 😀 Another name for the diagram is 'Fishbone Diagram' because of its appearance, resembling a fish skeleton.
- 😀 There are three main strategies to address problems: preventive actions (address causes before they occur), corrective actions (address causes after detection), and containment actions (limit the spread of the problem).
- 😀 An example of a problem could be a power outage in a factory, with corrective actions including upgrading the electrical system, preventive actions involving proper energy monitoring, and containment actions like using backup generators.
- 😀 To build a Cause and Effect Diagram, first, identify the effect you want to study (e.g., a problem with poorly aligned seams in a clothing factory).
- 😀 After identifying the effect, categorize the causes into groups like Method, Manpower, Machine, Material, Measurement, and Environment using tools like the '6M' approach.
- 😀 Categories help group causes related to the problem and make it easier to analyze. Other categorization approaches include '4P' and '4S' for specific industries.
- 😀 Brainstorming and group collaboration are key to identifying potential causes for the problem. It's important to avoid spending too much time on categorizing the causes at this stage.
- 😀 Causes identified are only hypotheses, and further analysis is required to confirm their relationship to the problem. Tools like a correlation diagram may be used to test cause-effect relationships.
- 😀 The diagram is a starting point for problem-solving, but further steps, such as action planning and data collection, are required to address and eliminate the issue.
Q & A
What is a cause and effect diagram (also known as a fishbone diagram)?
-A cause and effect diagram, also called a fishbone diagram, is a tool used to identify the potential causes of a problem, helping to identify the root cause. It is commonly used in quality management to find the source of issues.
Why is a cause and effect diagram sometimes referred to as a 'fishbone' diagram?
-It is referred to as a 'fishbone' diagram because its shape resembles a fish skeleton, with a central 'spine' representing the problem and branches representing different categories of potential causes.
What are the three main strategies to deal with problems as discussed in the video?
-The three main strategies for dealing with problems are: preventive actions (addressing causes before problems occur), corrective actions (eliminating causes after a problem is detected), and containment actions (limiting the spread of a problem when the cause can't be eliminated).
What example was used in the video to explain the application of a cause and effect diagram?
-The example used was a factory experiencing power outages, where the effect is the stoppage of production due to lack of electricity, and the cause might be an undersized electrical system.
What are the main categories used in a cause and effect diagram, and what do they represent?
-The main categories in a cause and effect diagram are: Method (process/procedures), Manpower (training/skills), Machine (equipment), Material (resources), Measurement (how the process is measured), and Environment (working conditions). These categories help group potential causes related to the problem.
What is the '6M' approach for categorizing causes, and what do the letters stand for?
-The '6M' approach is a method used to categorize causes in a cause and effect diagram, standing for: Method, Manpower, Machine, Material, Measurement, and Environment.
Can categories in a cause and effect diagram be customized, or are there predefined options?
-Categories can be customized. While the '6M' is a common approach, other methods like the '4P' (Place, Procedures, People, Policies) or '4S' (Surroundings, Suppliers, Systems, Skills) can also be used, depending on the context.
What is the importance of brainstorming when constructing a cause and effect diagram?
-Brainstorming is crucial because it allows a group of people to generate a wide range of potential causes without getting bogged down in debates about category assignment. It helps in gathering diverse perspectives to identify all possible causes.
Why are the causes identified in a cause and effect diagram considered hypotheses?
-The causes are considered hypotheses because they are potential causes that might contribute to the problem. Further analysis is needed to confirm the actual relationship between the causes and the effect.
What should be done after constructing a cause and effect diagram to solve a problem?
-After creating the diagram, further data collection is needed to verify the identified causes. Once confirmed, action plans should be proposed to address the root causes in order to eliminate the problem.
Outlines
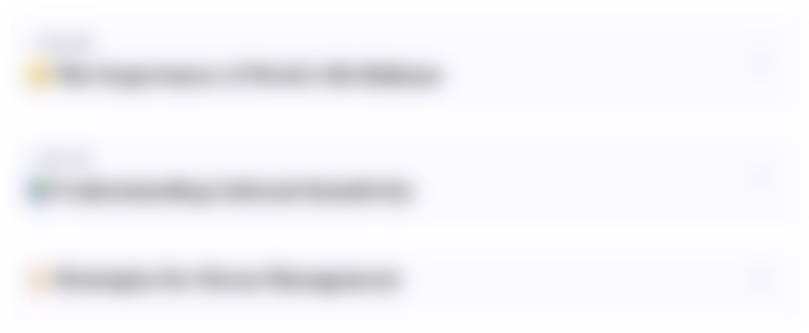
This section is available to paid users only. Please upgrade to access this part.
Upgrade NowMindmap
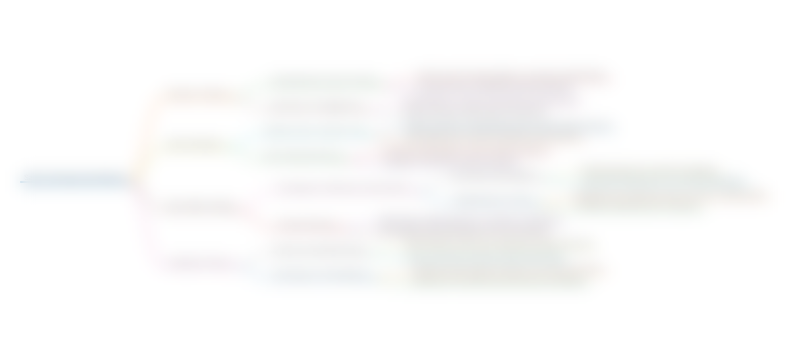
This section is available to paid users only. Please upgrade to access this part.
Upgrade NowKeywords
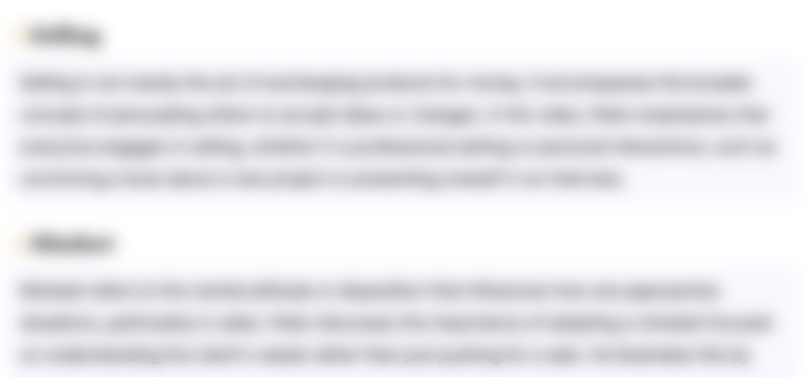
This section is available to paid users only. Please upgrade to access this part.
Upgrade NowHighlights
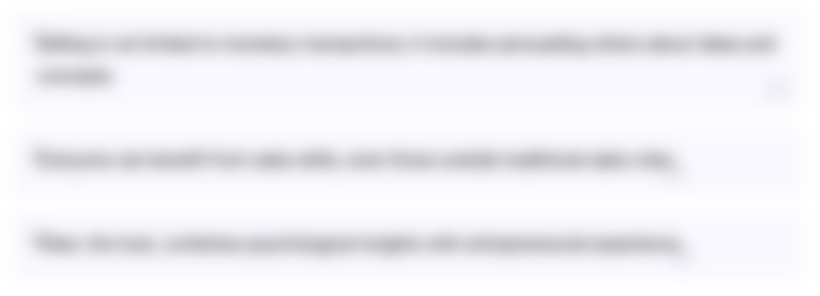
This section is available to paid users only. Please upgrade to access this part.
Upgrade NowTranscripts
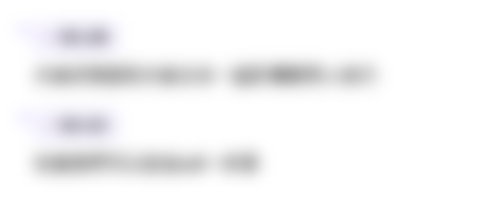
This section is available to paid users only. Please upgrade to access this part.
Upgrade Now5.0 / 5 (0 votes)