KPI - The Best KPI (Key Performance Indicator) for Supply Chain & Logistics
Summary
TLDRThis episode of 'Supply Chain Secrets' spotlights the critical KPI of 'Probability of a Perfect Order' in supply chain and logistics. The host emphasizes the common mistake of focusing solely on 'Delivered in Full, On Time' and instead introduces a holistic approach. Key factors like order entry accuracy, inventory availability, warehouse performance, carrier delivery, customer acceptance, and timely payments are discussed. The video illustrates how multiplying these percentages reveals a mere 64% chance of a perfect order, urging companies to address weaker areas like inventory availability to improve overall customer service. The company example shared improved from 64% to 93% over two years, highlighting the power of cross-functional collaboration in enhancing supply chain efficiency.
Takeaways
- 📊 The video discusses the importance of Key Performance Indicators (KPIs) in supply chain and logistics, focusing on customer service measures.
- 💡 The presenter introduces 'Probability of a Perfect Order' as one of the best KPIs for supply chain and logistics operations.
- 🔍 Common KPIs like 'Delivered in Full, On Time' are often measured incorrectly, and the video aims to show the right way to measure it.
- 📋 The script emphasizes the need to measure order entry accuracy, inventory availability, warehouse default service level, carrier delivery, customer acceptance, and invoice payment accuracy.
- 📉 The company in the case study had an order entry accuracy of 98%, which means 2% errors were occurring right from the start.
- 📦 Inventory availability was a significant issue, with 20% of the time orders could not be fulfilled due to lack of stock.
- 🛠 The warehouse's ability to pick, pack, and dispatch products accurately was at 90%, indicating room for improvement.
- 🚚 The carrier delivery KPI was at 98%, which is often the focus but not the only aspect that should be measured.
- ✅ Customer acceptance of the order was at 95%, showing that most customers were satisfied with their orders.
- 💰 Invoice payment accuracy was at 98%, indicating that most payments were processed correctly and on time.
- 🔢 By multiplying all the individual percentages, the overall probability of a perfect order was calculated to be 64%, which is significantly lower than any individual KPI.
- 📈 The company focused on improving inventory availability to increase the overall probability of a perfect order, which eventually reached 93% within two years.
- 🤝 The 'Probability of a Perfect Order' KPI encourages cross-functional collaboration and cooperation to improve overall supply chain performance.
- 🔑 The video concludes by highlighting the effectiveness of this KPI in driving focus and collaboration across different functions within an organization.
Q & A
What is the main topic of the video?
-The main topic of the video is discussing Key Performance Indicators (KPIs) in supply chain logistics, with a focus on customer service measures.
Why are KPIs often misunderstood in supply chain and logistics operations?
-KPIs are often misunderstood because people either measure the wrong things or measure too many, which can lead to confusion and misrepresentation of performance.
What is the 'probability of a perfect order' and why is it considered a good KPI?
-The 'probability of a perfect order' is a KPI that measures the likelihood that all aspects of an order, from entry to delivery and payment, are executed flawlessly. It's considered a good KPI because it encompasses multiple aspects of the supply chain and logistics process, providing a comprehensive view of performance.
What is the first aspect of the supply chain that the speaker suggests measuring?
-The first aspect suggested to measure is order entry accuracy, which involves assessing how accurately orders are entered into the system.
Why is inventory availability an important metric to measure?
-Inventory availability is important because it directly impacts the ability to fulfill customer orders. If the stock is not available, it can lead to customer dissatisfaction and lost sales.
What does the speaker mean by 'warehouse default service level'?
-The 'warehouse default service level' refers to the efficiency and accuracy of the warehouse operations in picking, packing, and preparing products for dispatch.
Why is it a problem if the carrier delivers in full on time but other aspects of the order process are flawed?
-Even if the carrier delivers in full on time, if other aspects such as order entry accuracy, inventory availability, or warehouse operations are flawed, it can still result in a high probability of customer dissatisfaction and a lower overall performance score.
How does the speaker suggest calculating the overall performance of the supply chain?
-The speaker suggests multiplying the individual percentages of each aspect of the supply chain process to get the overall probability of a perfect order, which gives a more accurate reflection of performance.
What was the initial probability of a perfect order in the case study presented in the video?
-In the case study presented, the initial probability of a perfect order was 64 percent.
What was the industry average and best-in-class performance for the 'probability of a perfect order' in the case study?
-The industry average for the 'probability of a perfect order' was 68 percent, while the best-in-class performance was 93 percent.
How did the company in the case study improve their 'probability of a perfect order' over time?
-The company focused on improving inventory availability, along with other aspects of their operations, which helped them increase their 'probability of a perfect order' from 64 percent to 68 percent within nine months, and eventually to 93 percent within two years.
Why is the 'probability of a perfect order' considered a cross-functional KPI?
-It is considered a cross-functional KPI because it involves multiple departments such as customer service, supply chain, warehousing, inventory management, and finance, promoting collaboration across functions to improve overall performance.
Outlines
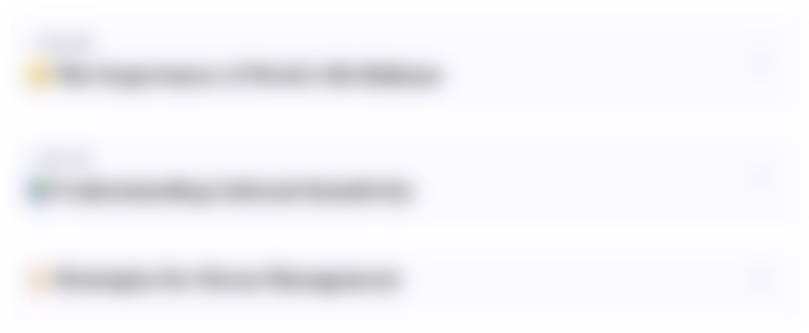
This section is available to paid users only. Please upgrade to access this part.
Upgrade NowMindmap
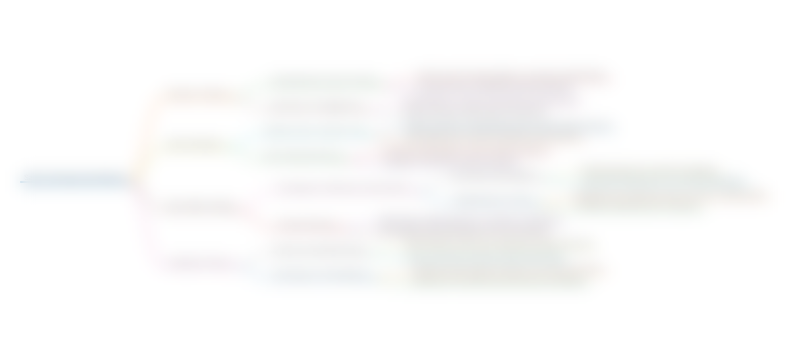
This section is available to paid users only. Please upgrade to access this part.
Upgrade NowKeywords
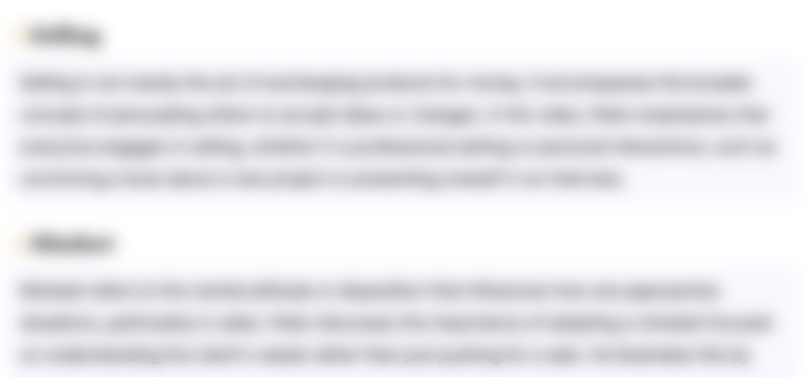
This section is available to paid users only. Please upgrade to access this part.
Upgrade NowHighlights
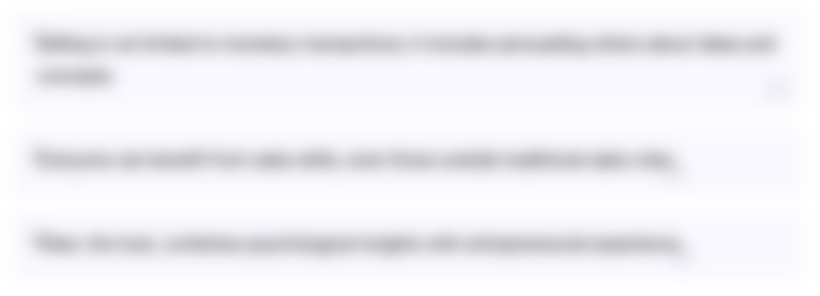
This section is available to paid users only. Please upgrade to access this part.
Upgrade NowTranscripts
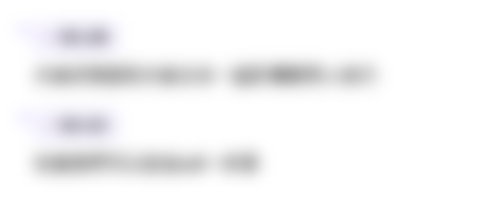
This section is available to paid users only. Please upgrade to access this part.
Upgrade NowBrowse More Related Video

What is Logistics & Logistics Management | What are Modes of Transport | How to select TransMode

#135 Supply Chain Management vs Logistic (Part 1)
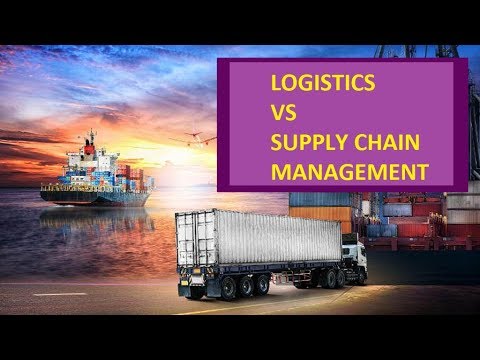
LOGISTICS VS. SUPPLY CHAIN MANAGEMENT| WHAT IS THE DIFFERENCE?| COMPARISON| DEFINITION| EXPLANATION|
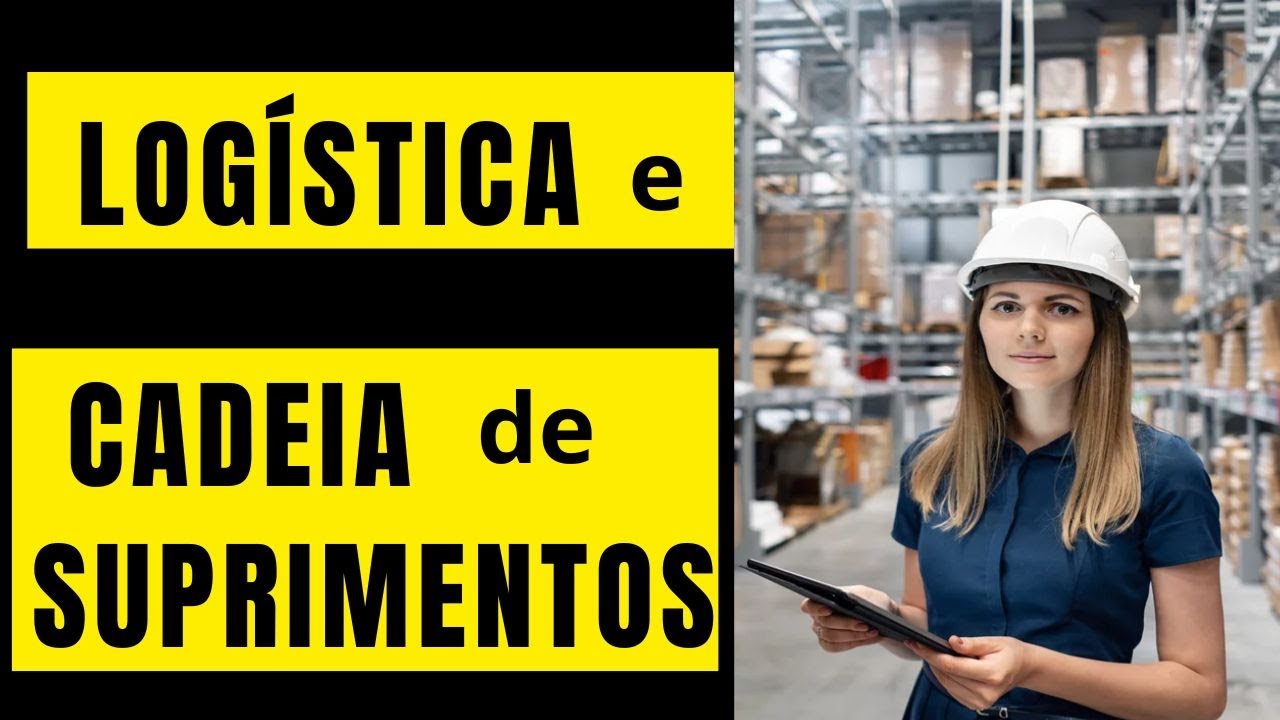
CADEIA de SUPRIMENTOS e LOGÍSTICA
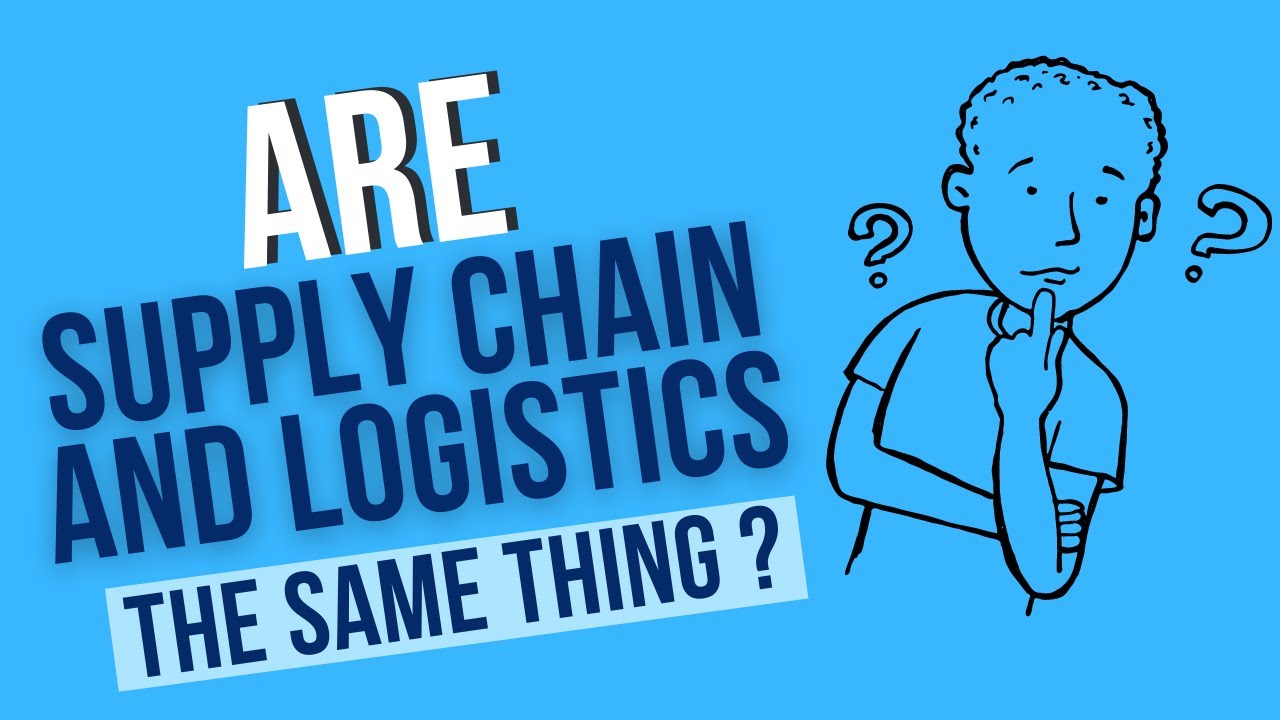
WHAT is the DIFFERENCE between SUPPLY CHAIN and LOGISTICS?
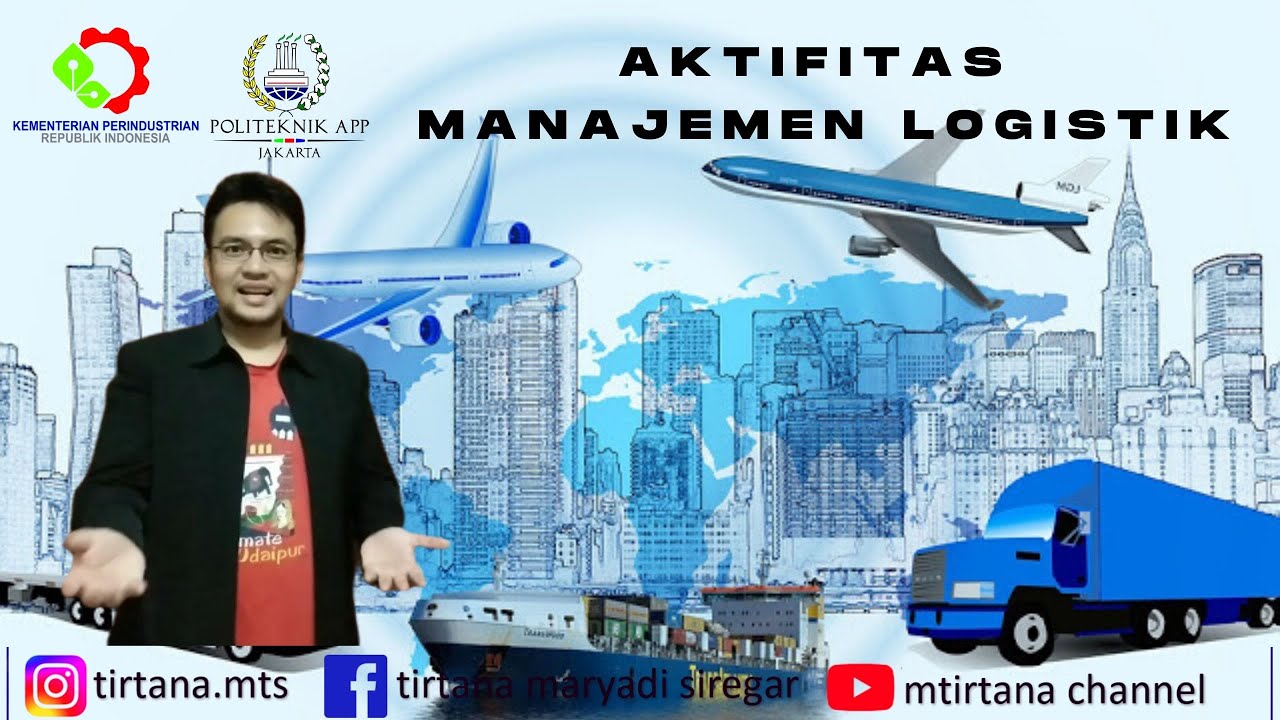
(PART 1) : Aktifitas Manajemen Logistik
5.0 / 5 (0 votes)