Automated Industrial Lines | Production Lines
Summary
TLDRThis video provides a comprehensive overview of automated production and assembly lines, focusing on their key components, advantages, and configurations. It explains the differences between production and assembly lines, highlighting fixed automation's suitability for mass production. The lecture covers work handling systems, such as synchronous and asynchronous mechanisms, as well as different transport configurations like inline, segmented inline, and rotary setups. Additionally, the video delves into the role of controllers in managing sequence control, safety, and quality assurance, emphasizing the use of PLCs and PCs in automation systems. The session concludes by preparing learners for a deeper exploration of assembly lines in the next video.
Takeaways
- 😀 Automated production lines are designed for mass production of stable products with long lifespans and minimal changes in design.
- 😀 Fixed automation setups are specialized for producing a single type of product and are difficult to alter once production starts.
- 😀 Automated production lines reduce labor costs, improve production rates, and make efficient use of factory space, enhancing overall safety.
- 😀 The work handling system in automated lines transfers work units between workstations in a sequence, ensuring smooth operation.
- 😀 Synchronous systems are used when machine tool processing times are similar, ensuring smooth work unit movement without delays.
- 😀 Asynchronous systems with storage buffers help maintain system efficiency when machine tools have varied processing times.
- 😀 Segmented inline configuration is used when space optimization or changes in work unit orientation are needed, involving bends or turns in the production line.
- 😀 Rotary configuration involves circular movement of work units around a worktable and is best suited for small-sized workpieces.
- 😀 Sequence control is crucial in managing the order of operations and movement of work units across workstations.
- 😀 Safety monitoring ensures both machine and worker safety by controlling and limiting unsafe operations and potential risks in the production line.
- 😀 Quality control is necessary to ensure that manufactured parts meet design specifications and quality standards, often using both on-line inspection and dedicated inspection workstations.
- 😀 PLCs (Programmable Logic Controllers) are the most widely used controllers for automated production lines due to their reliability and robustness, while personal computers are more commonly used at supervisory levels.
Q & A
What is the main focus of the lecture in the provided script?
-The lecture focuses on automated production and assembly lines, discussing their components, configurations, and control functions, particularly in the context of fixed automation.
What makes automated production and assembly lines an example of fixed automation?
-Automated production and assembly lines are considered examples of fixed automation because they are specialized for producing one type of product, and changes to the product design are difficult once the line is operational.
What are the advantages of using automated production lines?
-Automated production lines offer several advantages, including reduced labor costs, higher production rates, shorter manufacturing lead times, efficient use of factory space, and a safer work environment.
How do automated production lines function to produce finished products?
-Work units enter the line from one side, pass through each workstation in sequence where they are processed, and exit the line as finished products after all operations have been performed.
What is the difference between a production line and an assembly line?
-In a production line, processing is performed on the work part, whereas in an assembly line, no processing occurs—only assembly operations are performed.
What is the role of the work handling system in an automated production line?
-The work handling system's main role is to transport work units from one workstation to another in the correct sequence and position them properly for each workstation's operation.
What is the key distinction between synchronous and asynchronous work transportation systems?
-Synchronous systems move work units in sync, with processing times aligned across workstations, while asynchronous systems allow for storage buffers between workstations, enabling independent operation of each workstation.
What are the three main configurations for work transportation systems in automated lines?
-The three main configurations are: 1) Inline configuration, which is used for large parts or workstations; 2) Segmented inline configuration, which allows for turns and space-saving; 3) Rotary configuration, which uses a circular layout and is suitable for small parts.
Why are buffers important in asynchronous systems?
-Buffers are important in asynchronous systems because they store work units between workstations, allowing continuous operation even if a workstation breaks down or requires maintenance.
What types of controllers are typically used in automated production lines, and why?
-Programmable Logic Controllers (PLCs) are typically used in automated production lines due to their ruggedness and long history in industrial applications. Personal computers are also used, but mainly for supervisory functions and not directly on the factory floor.
Outlines
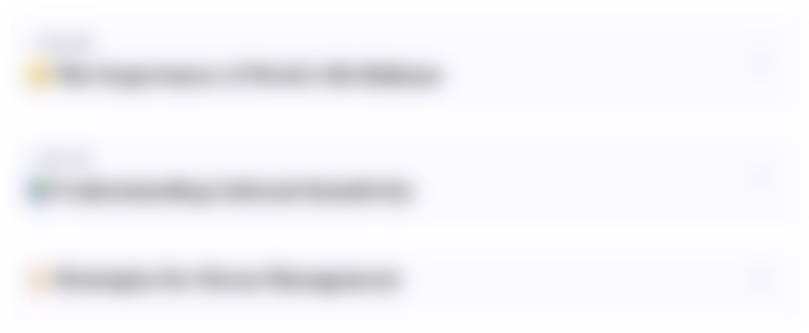
This section is available to paid users only. Please upgrade to access this part.
Upgrade NowMindmap
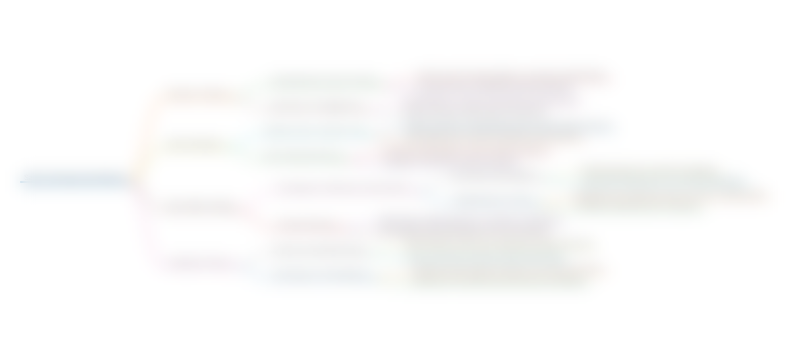
This section is available to paid users only. Please upgrade to access this part.
Upgrade NowKeywords
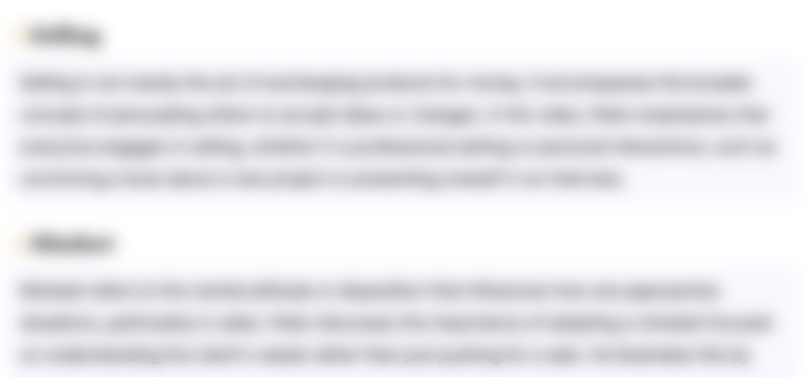
This section is available to paid users only. Please upgrade to access this part.
Upgrade NowHighlights
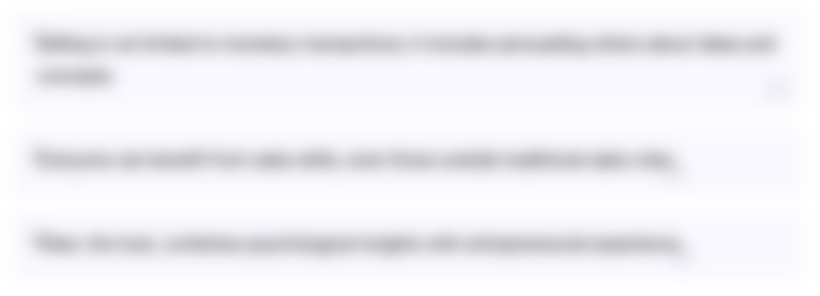
This section is available to paid users only. Please upgrade to access this part.
Upgrade NowTranscripts
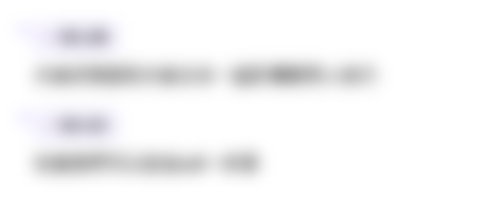
This section is available to paid users only. Please upgrade to access this part.
Upgrade NowBrowse More Related Video
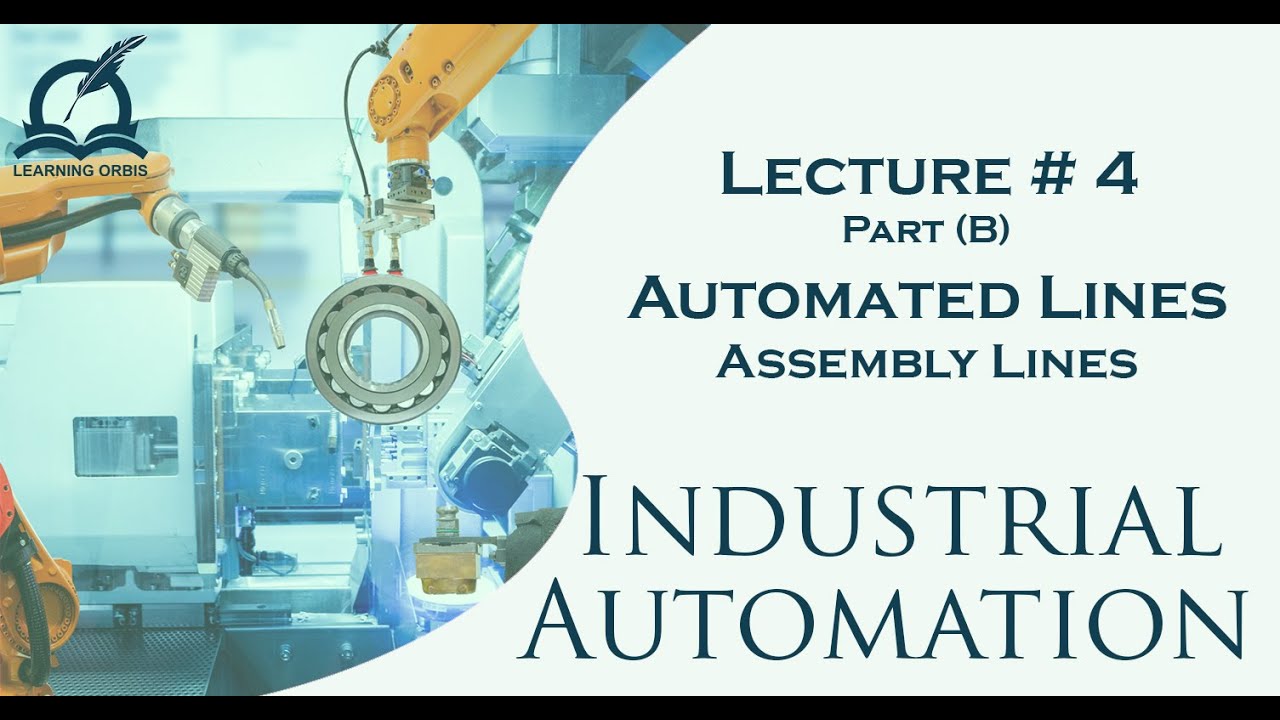
Automated Industrial Lines | Assembly Lines
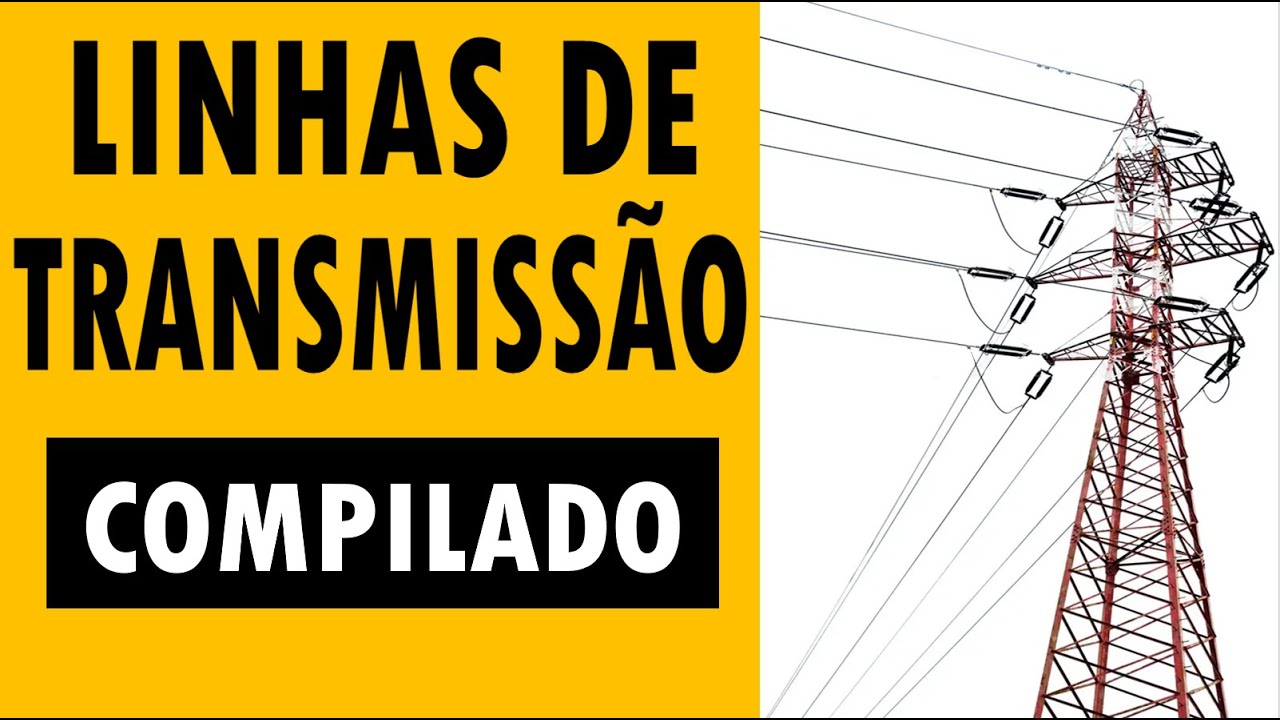
Resumão sobre LINHAS DE TRANSMISSÃO
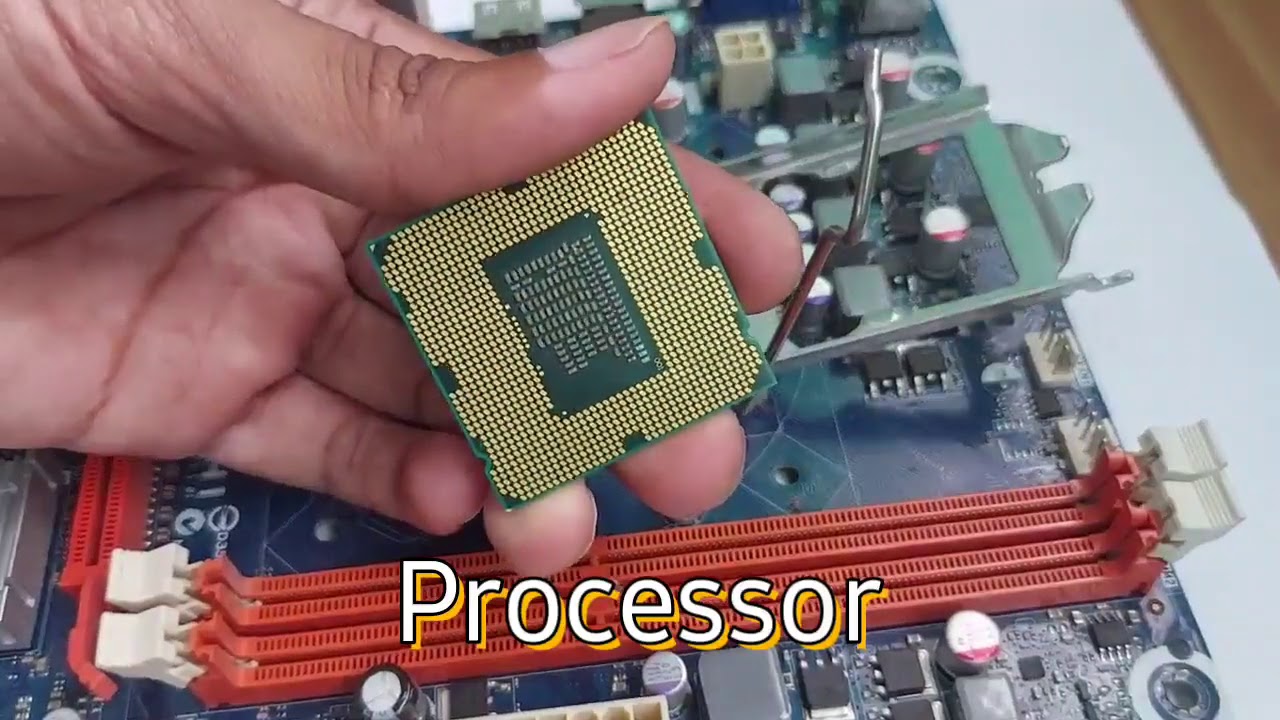
Bongkar PC dan Penjelasan Komponen Perangkat Keras di Dalam Komputer
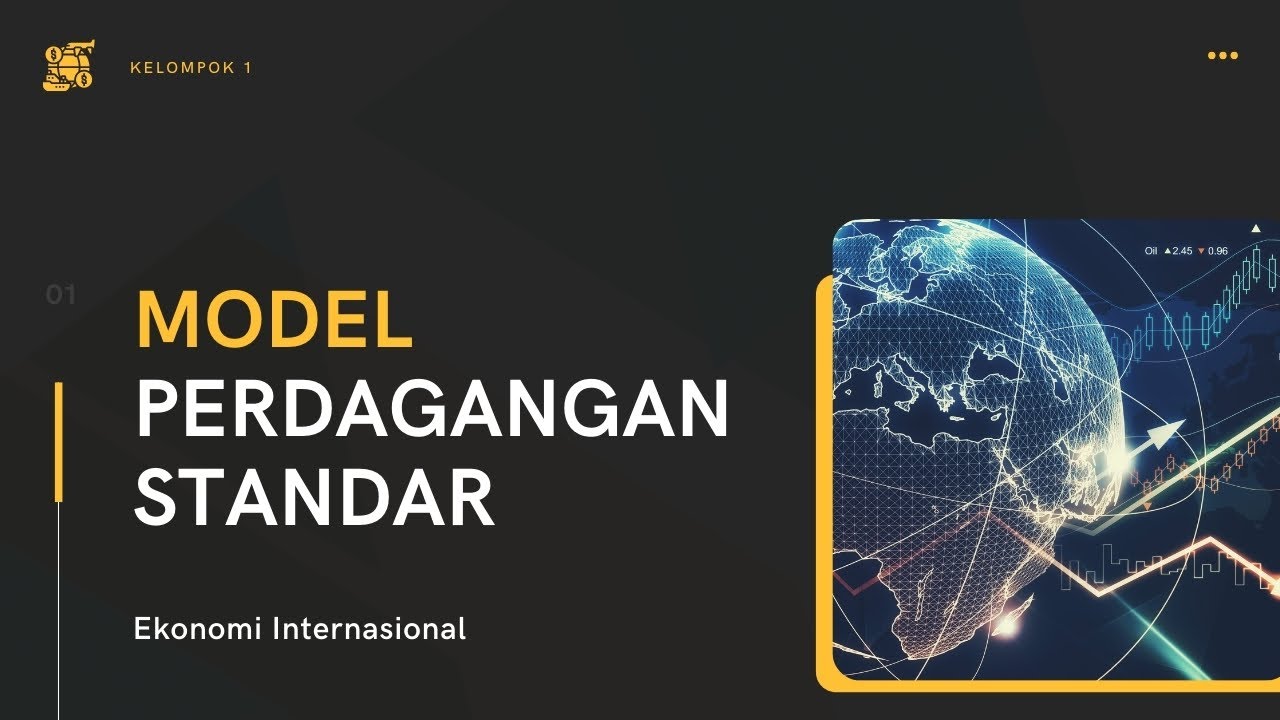
Model Perdagangan Standar

What Are The Common Types Of Metal Casting Process In Engineering and Industry?
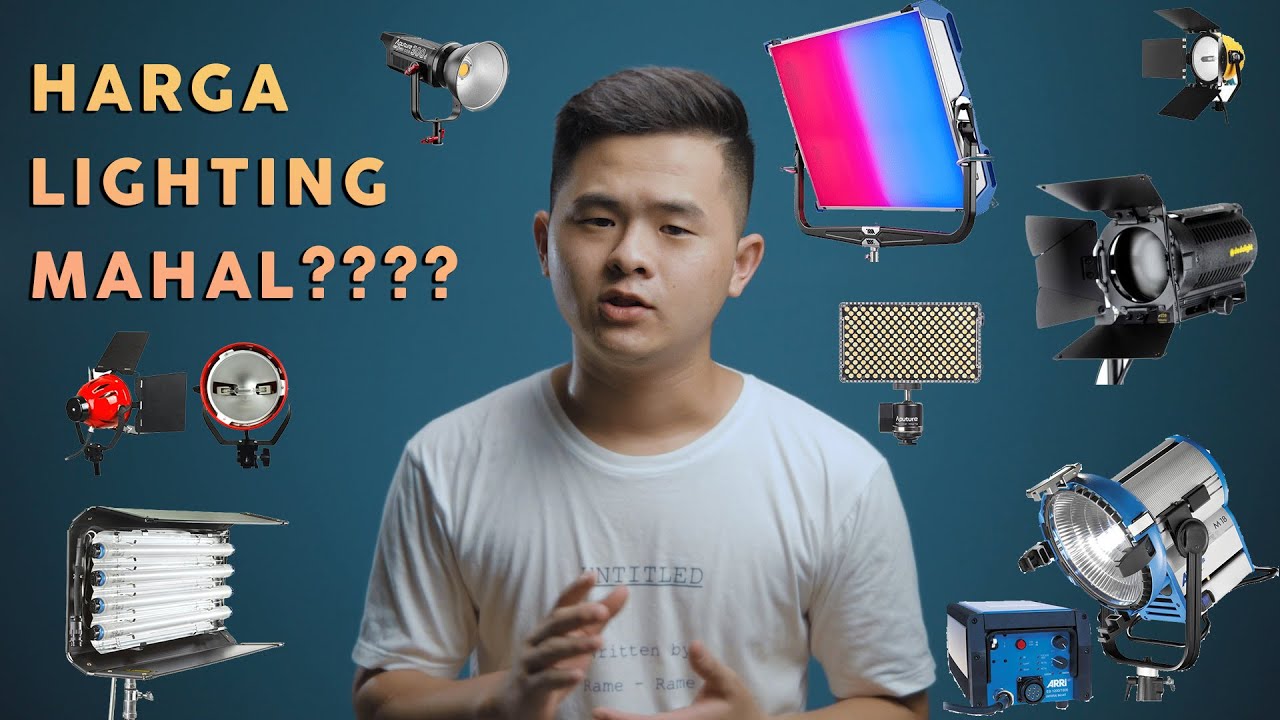
Jenis-Jenis Lighting Film - Tutorial Dasar Videografi & Sinematografi
5.0 / 5 (0 votes)