Demonstration of wind power generation
Summary
TLDRThis video covers a detailed demonstration of wind power generation, focusing on the doubly fed induction generator (DFIG) setup used in modern wind turbines. It explains how wind energy is converted into electrical power through turbines, generators, and power converters. Key topics include the operating modes of DFIG (sub-synchronous, synchronous, and super-synchronous), the control strategies using rotor side converters (RSC) and grid side converters (GSC), and how power flows from the rotor and stator to the grid. The hardware setup and software integration are also highlighted, showing how wind emulation is achieved in a lab environment.
Takeaways
- 🌬️ Wind power generation involves capturing kinetic energy through wind turbines, which is converted to electrical energy via a gearbox, generator, and transformer.
- 🔋 The doubly fed induction generator (DFIG) is a partial variable wind system, known for its cost-effectiveness due to scaled-down converter sizes.
- ⚡ DFIG wind systems can inject power into the grid across a wide range of wind speeds, maintaining grid stability.
- 🔄 DFIG operates in three modes: sub-synchronous, synchronous, and super-synchronous, depending on the rotor speed relative to the grid frequency.
- 🌀 The rotor speed varies with wind speed, from sub-synchronous speeds in low wind to super-synchronous speeds in high wind.
- 📉 During sub-synchronous mode, the rotor draws power from the grid, while during super-synchronous mode, excess power is fed back to the grid.
- 🛠️ The DFIG hardware setup includes a wind emulator, slip ring induction motor, and back-to-back voltage source converters.
- 🔧 A DC motor emulates wind conditions and is controlled via a chopper, while buck converters manage the power flow.
- 🎛️ FPGA controllers, specifically the vivect FPGA, regulate the system, monitoring voltages, currents, and PWM signals for accurate control.
- 💡 Maximum power point tracking (MPPT) is implemented to optimize energy extraction from the wind turbine under varying wind conditions.
Q & A
What is the basic concept of wind power generation?
-Wind power generation converts kinetic energy from wind into electrical energy using wind turbines, a gearbox, a generator, power converters, and transformers to feed the energy into the power grid.
How does the Doubly Fed Induction Generator (DFIG) differ from conventional induction machines in wind systems?
-The DFIG allows power injection into the grid over a wide range of wind speeds, operating at both sub-synchronous and super-synchronous speeds. Unlike conventional machines, the DFIG's rotor can either absorb or deliver power, making it suitable for variable wind conditions.
What are the three modes of operation for a DFIG wind turbine?
-The three modes of operation are: sub-synchronous mode (rotor speed less than synchronous speed), synchronous mode (rotor speed equal to synchronous speed), and super-synchronous mode (rotor speed greater than synchronous speed).
What role does the rotor-side converter (RSC) play in DFIG systems?
-The RSC regulates the DFIG to operate in speed and power control modes, managing rotor current through field-oriented control (FOC) and facilitating maximum power point tracking (MPPT) under varying wind conditions.
How does power flow during sub-synchronous operation of the DFIG?
-In sub-synchronous operation, the rotor speed is less than synchronous speed, and power is drawn from the grid via the rotor-side converter to the rotor, enabling power injection into the grid through the stator.
What is the function of the grid-side converter (GSC) in a DFIG wind system?
-The GSC maintains the DC link voltage by controlling the flow of current between the DC link and the grid. It ensures smooth power transmission and reactive power management in coordination with the RSC.
What happens during synchronous mode of operation in a DFIG system?
-During synchronous mode, the rotor speed matches the synchronous speed, meaning no power is injected into or drawn from the rotor. All power is transferred to the grid through the stator.
What is the significance of Maximum Power Point Tracking (MPPT) in wind power generation?
-MPPT optimizes the rotor speed at different wind velocities to ensure maximum energy capture from the wind turbine. In DFIG systems, the RSC regulates rotor current to achieve MPPT.
How is the synchronization between the stator and grid achieved in a DFIG setup?
-Synchronization is achieved by adjusting the stator voltage and phase angle to match the grid's voltage and phase using rotor-side converter control. Once aligned, the stator can connect to the grid.
What hardware components are used in the DFIG wind turbine test bed demonstration?
-The DFIG test bed consists of a wind emulator, a slip ring induction machine, a DC motor, and back-to-back voltage source converters (RSC and GSC), controlled using an FPGA-based controller.
Outlines
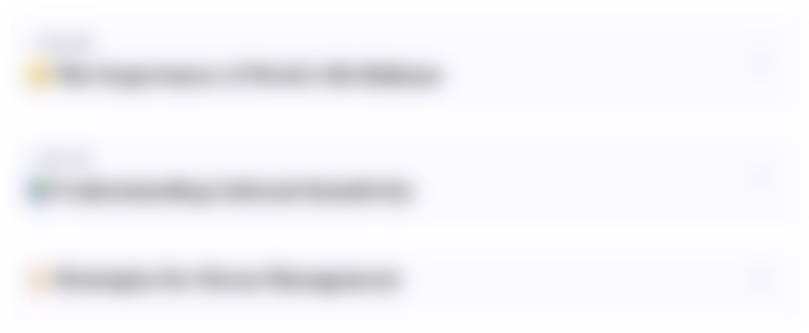
This section is available to paid users only. Please upgrade to access this part.
Upgrade NowMindmap
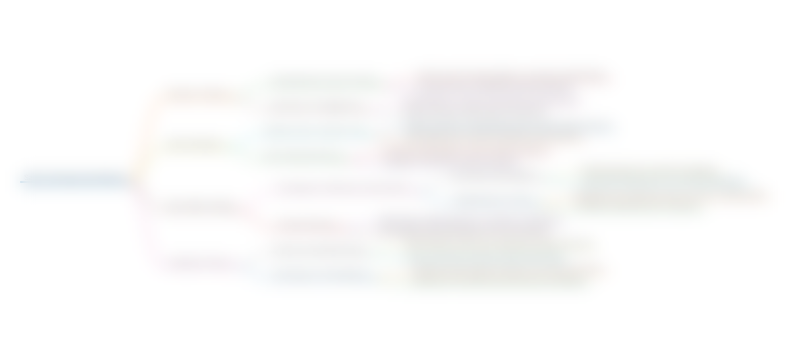
This section is available to paid users only. Please upgrade to access this part.
Upgrade NowKeywords
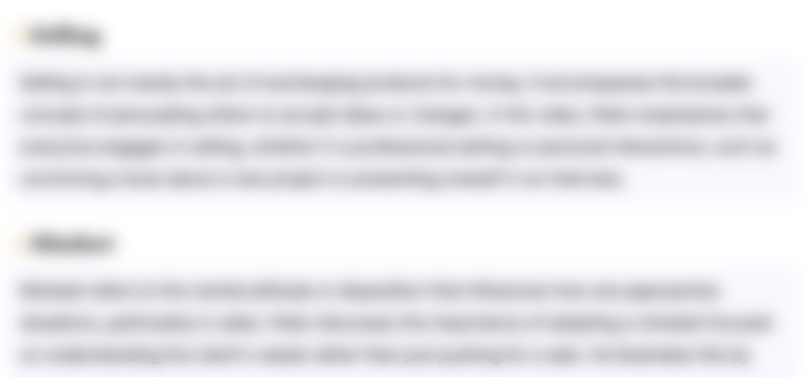
This section is available to paid users only. Please upgrade to access this part.
Upgrade NowHighlights
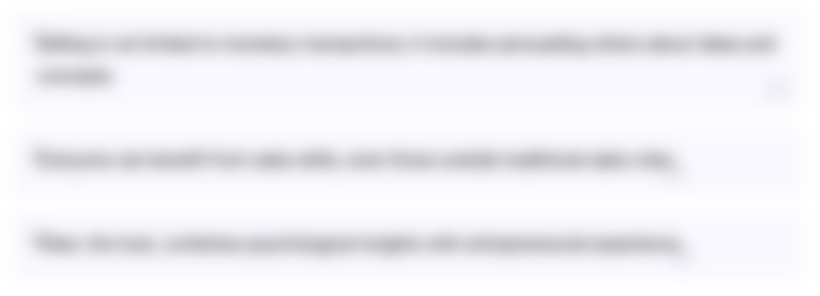
This section is available to paid users only. Please upgrade to access this part.
Upgrade NowTranscripts
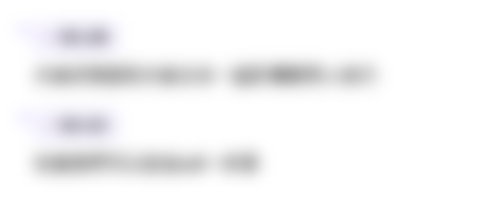
This section is available to paid users only. Please upgrade to access this part.
Upgrade NowBrowse More Related Video
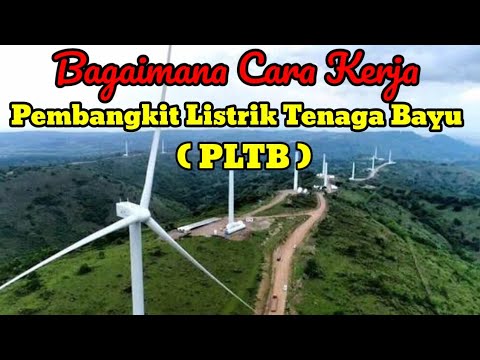
PLTB || Sejarah, Komponen Utama dan Cara Kerja Pembangkit Listrik Tenaga Bayu (Angin)

Wind Power - IB Physics
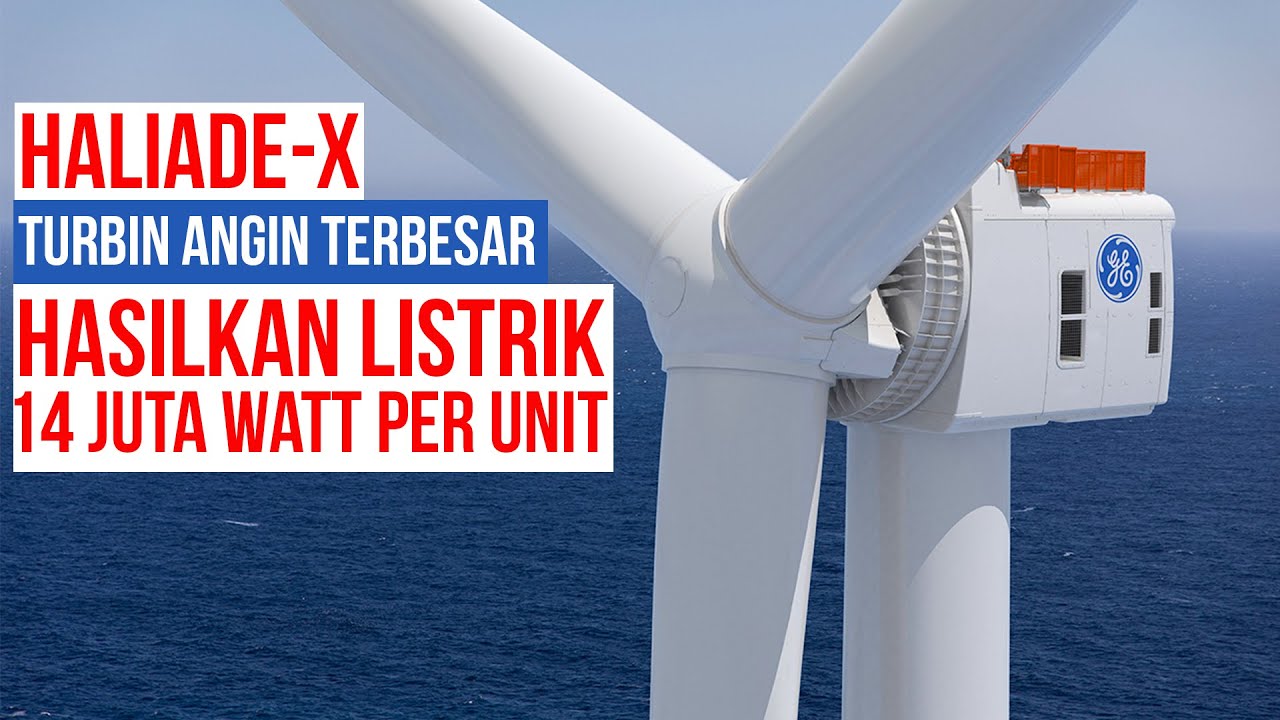
Cara Kerja Turbin Angin Raksasa Haliade-X, PLTB Terbesar Bisa Produksi Listrik 14 Juta Watt Per Unit
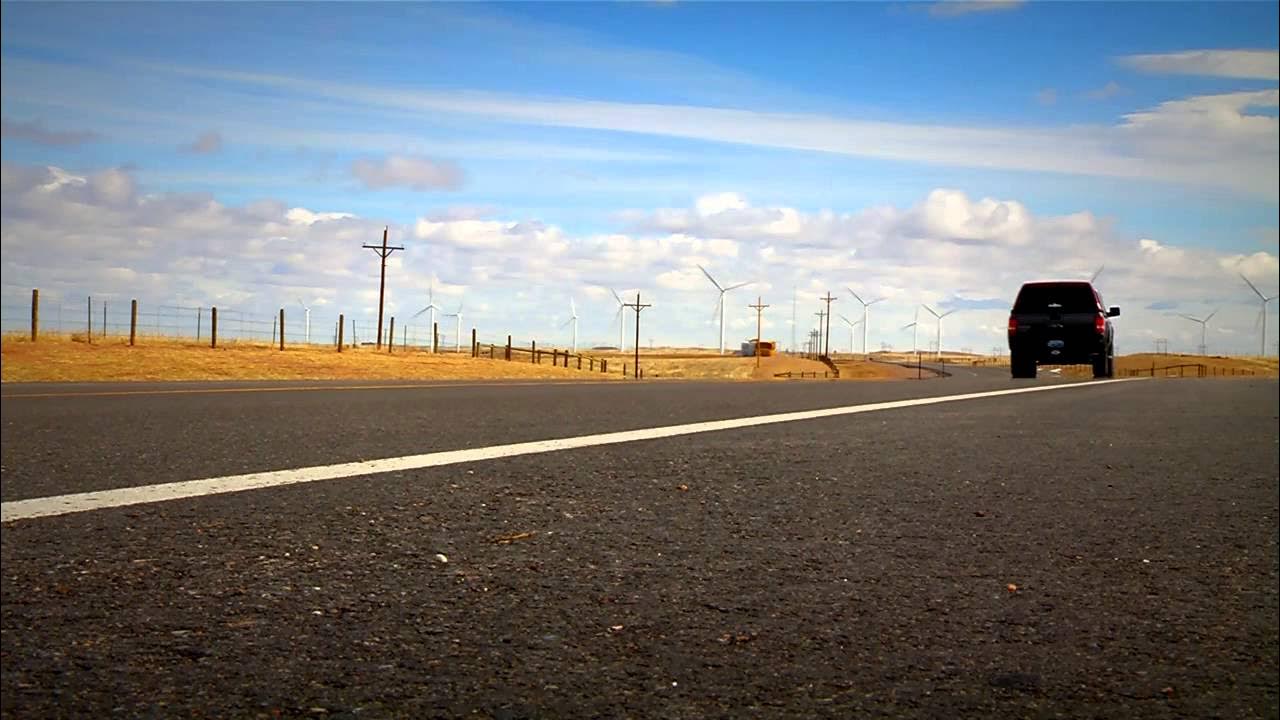
Energy 101: Wind Power

Energi Angin
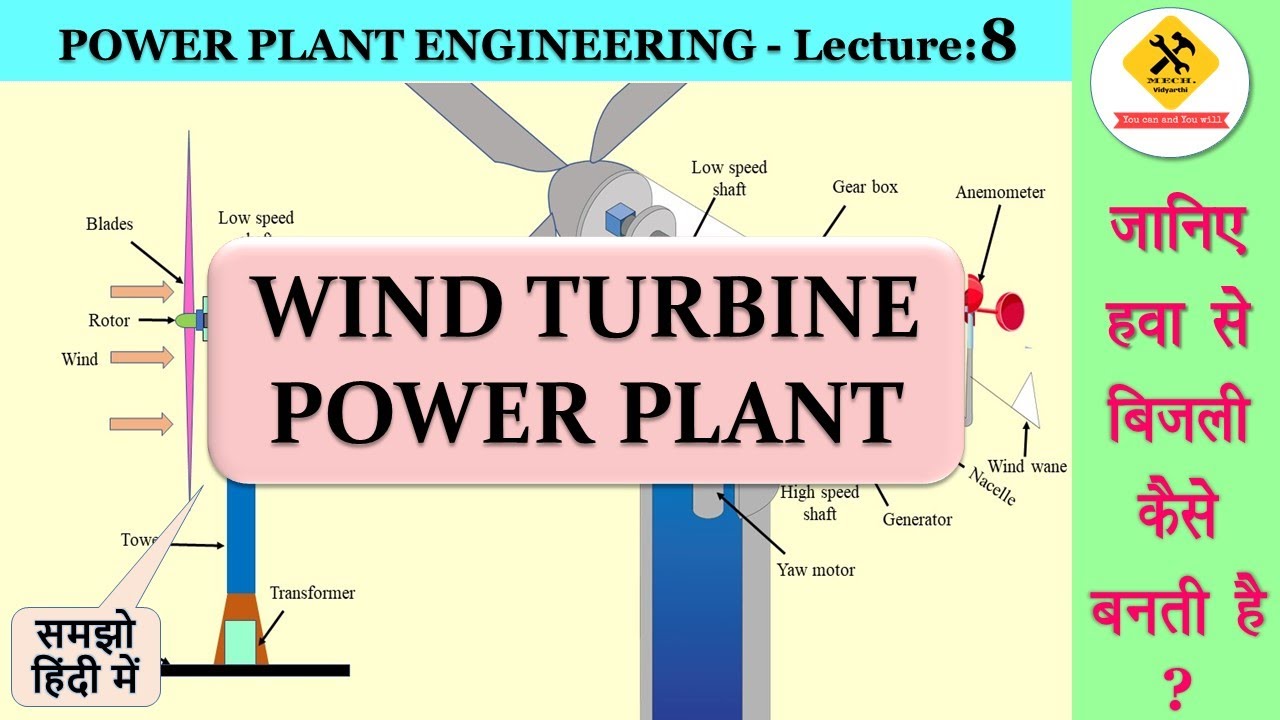
How does Wind Turbine power plant works? (in hindi) विंड टर्बाइन पावर प्लांट (हिंदी में)
5.0 / 5 (0 votes)