How Skateboards Are Made
Summary
TLDRThe video script details the eco-friendly skateboard manufacturing process, starting with cutting and grading veneers from logs. Clean veneers become face layers, while those with defects are used in the core. Natural veneers are sanded for painted decks, while dyed veneers are soaked in a pressurized vat for color penetration. Laminated with water-based PVA glue, boards are cold pressed for strength. CNC machines increase efficiency in cutting and shaping, and all scrap wood is recycled. The finishing process involves water-based clear coats and heat transfers for graphics, emphasizing worker safety and environmental sustainability.
Takeaways
- 🌳 The wood used for skateboards comes in log run form, requiring peeling and grading to determine the placement on the skateboard.
- 🎨 Clean veneers are used for the top and bottom face veneers, while those with small defects are placed in the middle of the deck.
- 🛠️ The production process includes sanding, dyeing, and lamination, with a focus on using environmentally friendly materials and processes.
- 💧 Dyeing involves soaking veneers in a pressurized vessel with hot water and color, followed by drying in a large oven.
- 🔗 The use of PVA glue, which is water-based, is preferred over toxic alternatives for lamination.
- 🏗️ Cold pressing is used to create stronger boards, despite the higher investment in machinery compared to hot pressing.
- ⏱️ The curing process for the skateboards takes at least one week after pressing to ensure the glue is fully set.
- 🤖 CNC machines are utilized for increased efficiency in cutting and shaping the skateboards, reducing manual labor.
- 🔄 Scrap wood and other waste products are recycled, demonstrating a commitment to sustainability.
- 🎨 The graphics on the skateboards are created using water-based inks and heat transfers, which are then fused onto the deck.
- 🏷️ After a final quality check, skateboards are packaged with stickers and shipped to distributors worldwide.
Q & A
What form does the wood initially come in for skateboard production?
-The wood comes in log run form, meaning it is in the form of peeled veneers from the mill before being cut to size and graded.
How are the veneers graded for skateboard construction?
-The veneers are graded so that the cleanest ones are used as face veneers on the top and bottom, while those with small defects end up in the middle of the deck.
What type of veneers are used for a painted skateboard deck?
-For a painted deck, all natural veneers are used, including the faces, which are sanded during the process.
How is the dyeing process for skateboard veneers carried out?
-The veneers are soaked in a vat of hot water mixed with the specified color, then placed in a pressurized vessel where the colored water penetrates the veneer. Afterward, the colored wet veneer is dried in a 50-ft oven.
What type of glue is used for laminating the skateboard veneers?
-A water-based PVA glue is used for lamination, avoiding the use of epoxy or toxic chromium-based catalysts.
What is the difference between cold pressing and hot pressing in skateboard production?
-Cold pressing makes the strongest board as the glue slowly dries and cures under pressure for 1 hour. Hot pressing, on the other hand, takes only 2 minutes and weakens the wood.
Why is there a higher investment in machinery for cold pressing compared to hot pressing?
-Cold pressing requires more presses to achieve the same volume as one hot press, but it results in stronger boards, which is why the higher investment is made.
How does the use of CNC machines improve the skateboard production process?
-CNC machines increase efficiency by drilling holes, cutting shapes, and rounding edges all in one step, ensuring accuracy and reducing the physical strain on workers.
What is done with the scrap wood and other waste products from the skateboard production?
-All scrap wood is recycled and made into particle board, and almost every other waste product from production is also recycled.
What type of clear coat is used in the spray line, and why is it preferred?
-A water-based clear coat is used instead of solvent-based, which is more worker and environmentally friendly and also sprays at the highest efficiency.
How are the graphics applied to the skateboard decks?
-The graphics are printed on plastic in reverse using water-based inks, one color at a time. After all colors are printed and dried, the transfers are bonded to the finished deck using heat and pressure.
What is the final step in the skateboard production process before shipping?
-After a final quality check, the decks are shrink-wrapped with stickers and other items, then boxed and shipped to brands for distribution worldwide.
Outlines
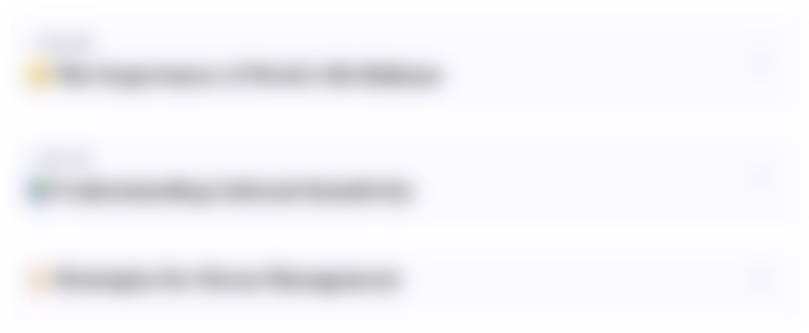
This section is available to paid users only. Please upgrade to access this part.
Upgrade NowMindmap
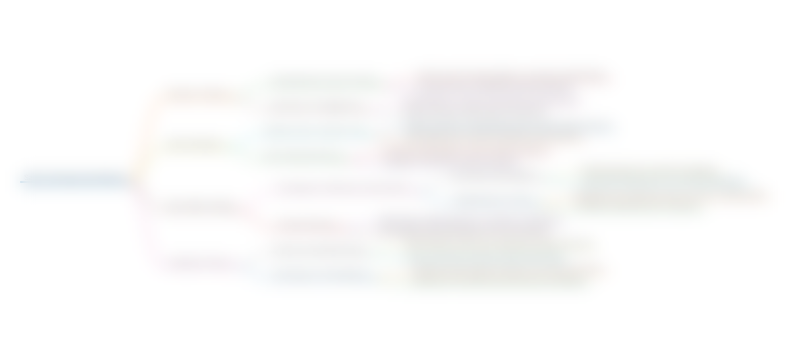
This section is available to paid users only. Please upgrade to access this part.
Upgrade NowKeywords
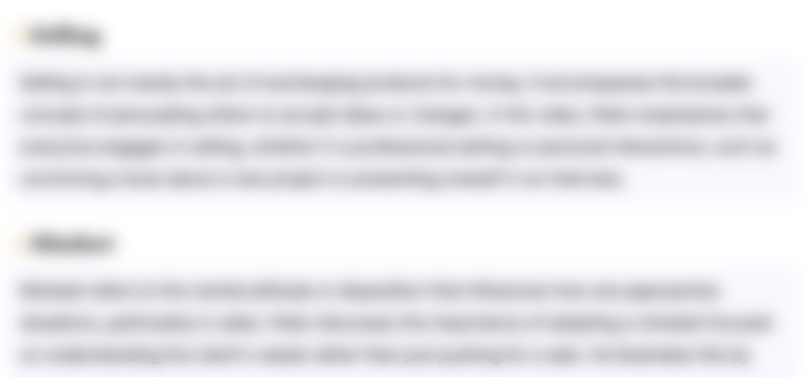
This section is available to paid users only. Please upgrade to access this part.
Upgrade NowHighlights
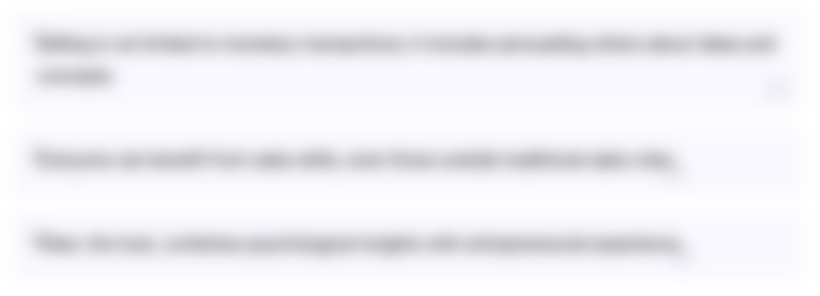
This section is available to paid users only. Please upgrade to access this part.
Upgrade NowTranscripts
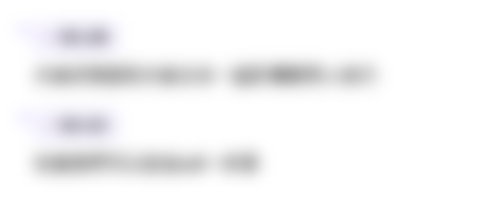
This section is available to paid users only. Please upgrade to access this part.
Upgrade NowBrowse More Related Video

How T-Shirts Are Made In America | From The Ground Up

How Linen Is Made
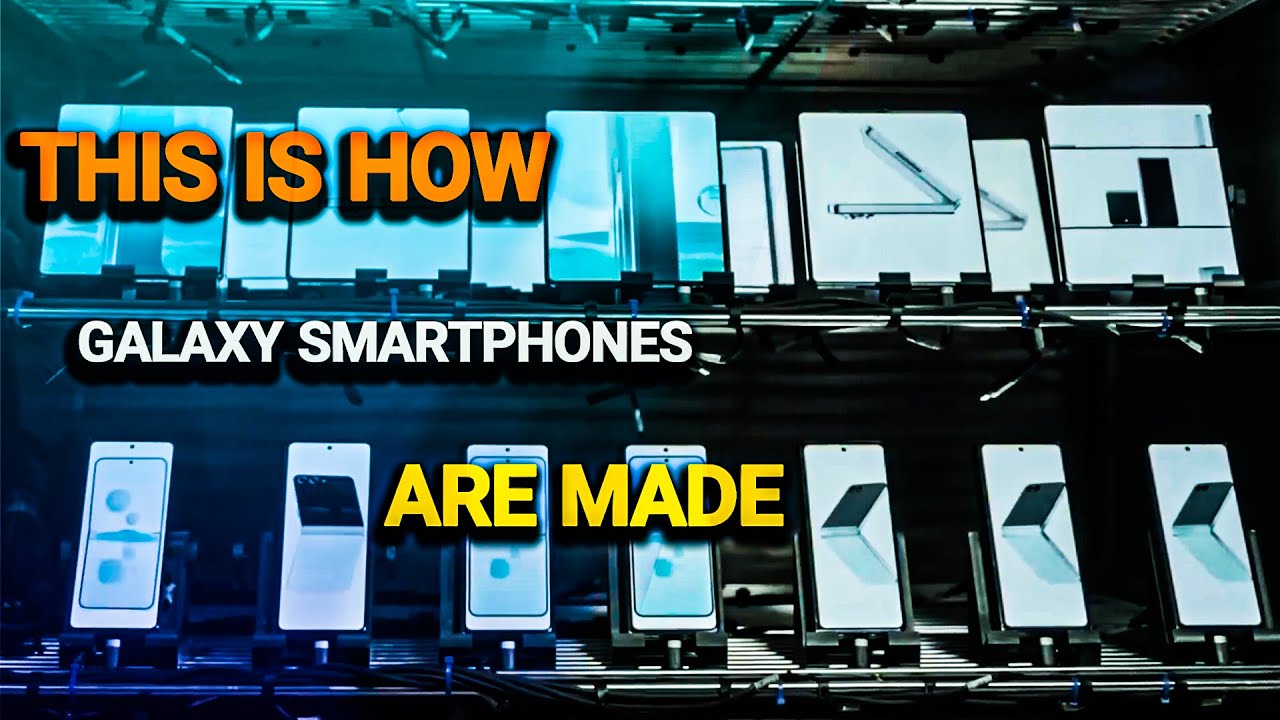
From Raw Materials to Your Hands | How Samsung Builds the Galaxy Smartphones

PROSES PEMBUATAN PAPAN DARI BAMBU! Ternyata Begini Cara Pabrik Pengolahan Bambu Jadi Papan Laminasi

Revolutionary Two Tone Paint Technology for Renault 4 E Tech Explained

KALUNG ADAT DARI KARDUS BEKAS DAN KERTAS EMAS
5.0 / 5 (0 votes)