The ISO Show Five Lessons from Boeing 737 Door Failure
Summary
TLDRIn this video, Oscar Colmes from ISO 901 Group discusses the Boeing 737 Max 9 door failure incident on January 5th, 2024. He outlines five key lessons from the event: the global impact of nonconformities, the importance of supply chain quality, the risks of assuming large suppliers are flawless, the necessity of thorough receiving inspections, and the role of proactive leadership in ensuring product safety. Colmes emphasizes that this incident, though non-fatal, serves as a critical reminder about quality control, operational vigilance, and the need for leadership to prioritize safety and quality at all stages.
Takeaways
- 😀 Non-conformities can have significant global impacts, not just localized ones. The Boeing 737 Max 9 door failure disrupted airlines and affected global flight operations.
- 😀 A non-conformity should never be seen as just paperwork; it requires careful documentation and analysis to understand its full impact across processes and products.
- 😀 A company’s supply chain can directly damage its brand and finances. Even a small supplier failure can have significant consequences for the end customer.
- 😀 Don’t assume large companies don’t face quality issues. Even major suppliers like Boeing can have failures, and those failures can affect other businesses.
- 😀 Always thoroughly vet suppliers, especially critical ones. This includes conducting audits, site visits, and evaluations to ensure quality and mitigate risk.
- 😀 Receiving inspections are crucial, even for new products. A thorough inspection should be done regardless of previous inspections to catch any potential issues.
- 😀 Proactive leadership in quality management is key. Leaders should regularly engage in discussions about quality and safety, not just react to problems after they arise.
- 😀 Hindsight is 20/20, but foresight can be just as powerful. Prevention through proactive measures, like thorough inspections, is crucial in avoiding future issues.
- 😀 Active leadership is necessary to promote a culture of quality and safety. CEOs and senior leadership must lead by example and foster a culture of quality throughout their organization.
- 😀 Safety is not just about immediate responses; it’s often a reflection of underlying quality issues. Both safety and quality must be prioritized to prevent incidents like the Boeing failure.
- 😀 Inspections should go beyond just visual checks. Sometimes non-destructive or even destructive testing is necessary to ensure parts and systems are functioning properly.
Q & A
What is the significance of the Boeing 737 Max 9 door failure incident on January 5, 2024?
-The Boeing 737 Max 9 door failure is significant because it highlights the risks of nonconformities in aviation and the broader implications they can have, including grounding of fleets, financial losses, and a damaged reputation for both airlines and manufacturers.
What happened during the Boeing 737 Max 9 incident on January 5, 2024?
-On January 5, 2024, an Alaska Airlines flight, number 1282, experienced a door plug failure at 16,000 feet. The door plug, which is used to seal unused exits, fell off mid-air and landed in a backyard. No one was injured, but the incident raised significant safety concerns.
What is a 'door plug' and why did it fall off during the flight?
-A door plug is a permanent seal used on planes for unused exits. The door plug on the Boeing 737 Max 9 fell off due to a nonconformity, which likely resulted from a manufacturing or design flaw.
What are the Five Lessons that can be learned from the Boeing 737 Max 9 incident?
-The Five Lessons are: 1) Nonconformities have global impacts. 2) Your supply chain can damage your brand. 3) Don’t assume large companies don’t have quality issues. 4) Receiving inspections are crucial. 5) Active leadership counts in quality management.
How did the Boeing 737 Max 9 door failure impact Alaska Airlines and other global airlines?
-The failure caused Alaska Airlines to ground 65 planes for inspections, disrupting flight schedules and incurring financial costs. The FAA also grounded 170 Boeing 737 Max 9 planes globally, affecting multiple airlines.
Why is it important to document nonconformities in a company?
-Documenting nonconformities is important because it helps track potential issues, identify patterns, and mitigate future risks. By thoroughly documenting and investigating nonconformities, companies can address root causes and prevent similar problems from spreading to other products or processes.
How can poor supply chain management lead to brand damage?
-If a supplier provides faulty parts or materials, it can directly affect the final product's quality, resulting in customer dissatisfaction, safety issues, or even legal liabilities. In the case of Boeing, both Alaska Airlines and Boeing’s reputation suffered due to the failure of the door plug.
What role does supplier auditing play in preventing quality issues?
-Supplier auditing helps ensure that suppliers meet quality standards and comply with contractual agreements. On-site audits provide a deeper understanding of a supplier’s practices, helping companies detect and resolve potential issues before they impact the final product.
What is the importance of receiving inspections, especially for new products?
-Receiving inspections are crucial because even new products may have hidden defects that weren’t identified during manufacturing or pre-shipment inspections. Thorough checks at the receiving stage can catch issues before they escalate and prevent costly disruptions or safety concerns.
How can leadership influence the quality culture within a company?
-Active leadership is essential in promoting a quality-driven culture. Leaders must regularly engage with their teams, emphasize the importance of quality and safety, and ensure that all employees are proactive in identifying and addressing potential issues before they become problems.
Why did the CEO of Boeing, Dave Calhoun, emphasize the importance of safety after the incident?
-After the door failure incident, Dave Calhoun emphasized safety to reassure employees and customers. While safety is crucial, the speaker also pointed out that the issue was likely a quality problem that could have been addressed by focusing more on the overall quality of the product and process, not just safety.
What is the significance of 'foresight' in quality management?
-Foresight in quality management refers to the proactive measures taken to identify and address potential issues before they occur. By conducting thorough inspections and being vigilant about potential risks, companies can prevent quality failures and avoid costly and dangerous incidents.
Outlines
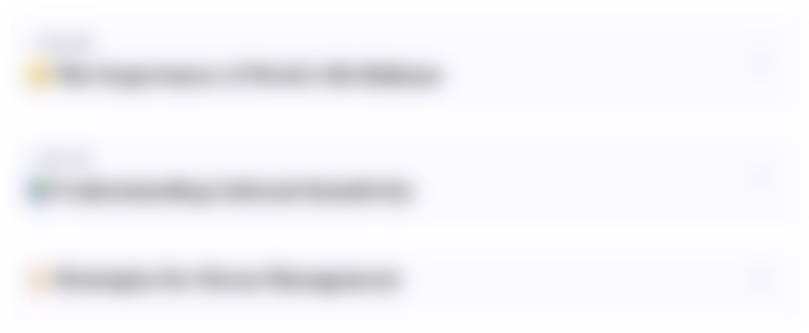
This section is available to paid users only. Please upgrade to access this part.
Upgrade NowMindmap
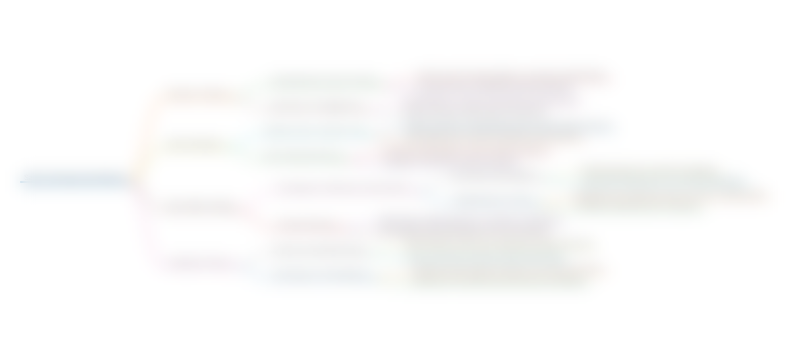
This section is available to paid users only. Please upgrade to access this part.
Upgrade NowKeywords
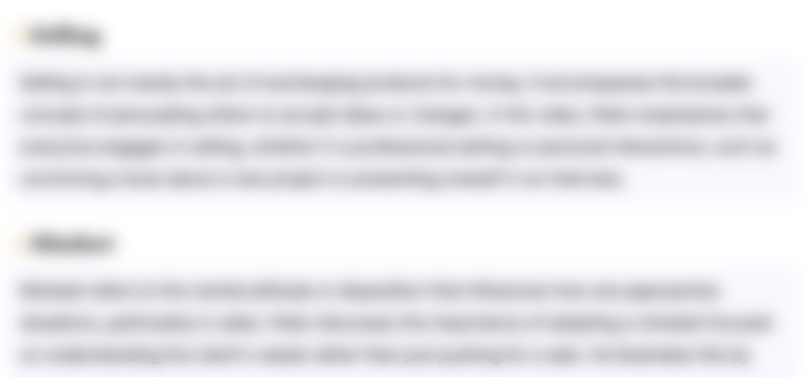
This section is available to paid users only. Please upgrade to access this part.
Upgrade NowHighlights
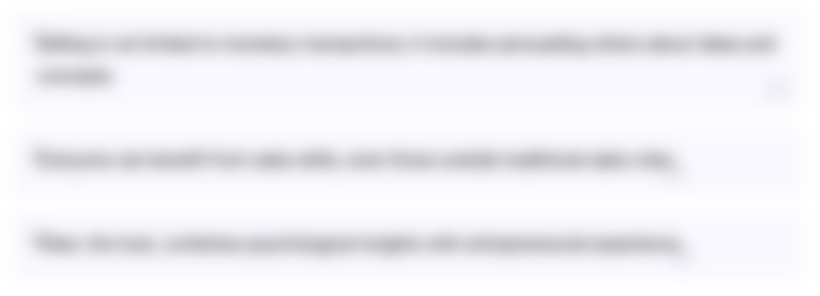
This section is available to paid users only. Please upgrade to access this part.
Upgrade NowTranscripts
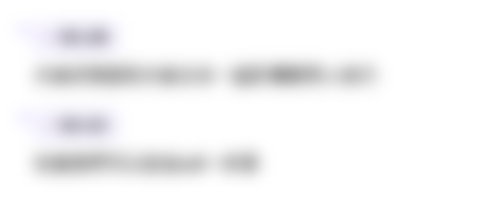
This section is available to paid users only. Please upgrade to access this part.
Upgrade NowBrowse More Related Video

Terbang Tenggelam Boeing, Ironi Raksasa Manufaktur Pesawat Asal AS
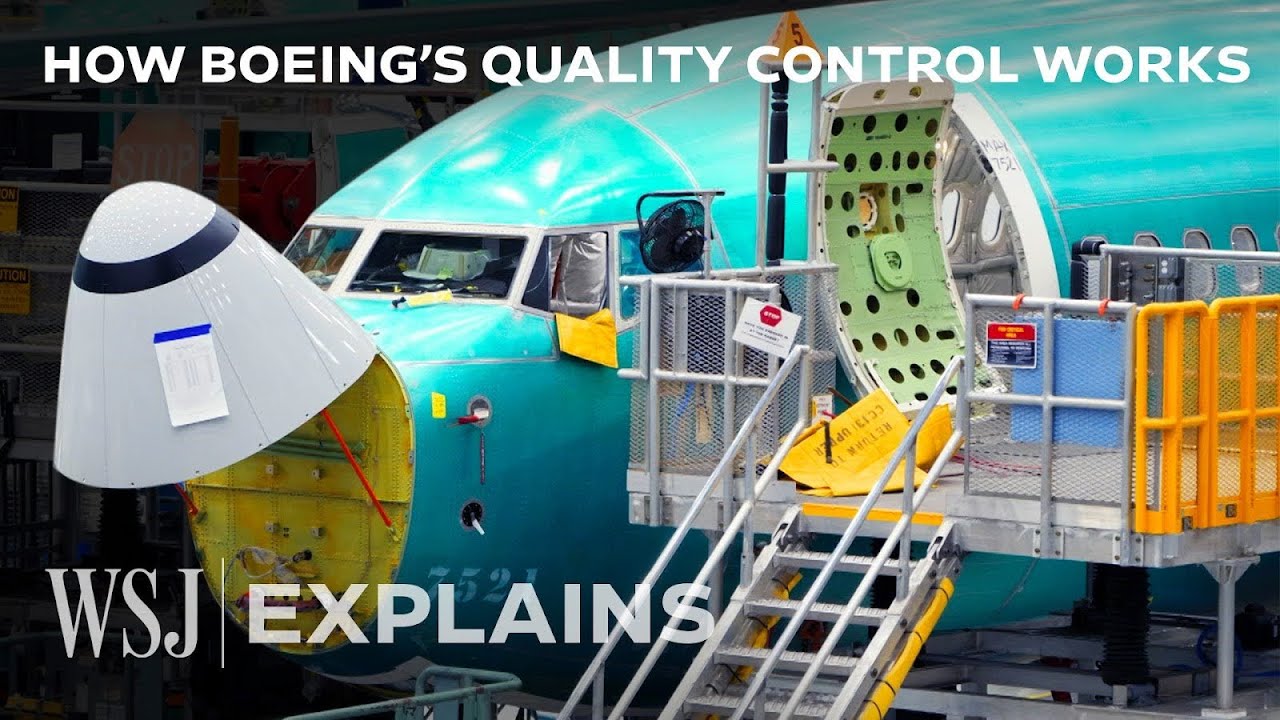
Boeing Whistleblower on 737 Factory’s Quality Control Process | WSJ

Why The Boeing 737 Max Has Been Such A Mess

Supply Chain System - Apple.Inc
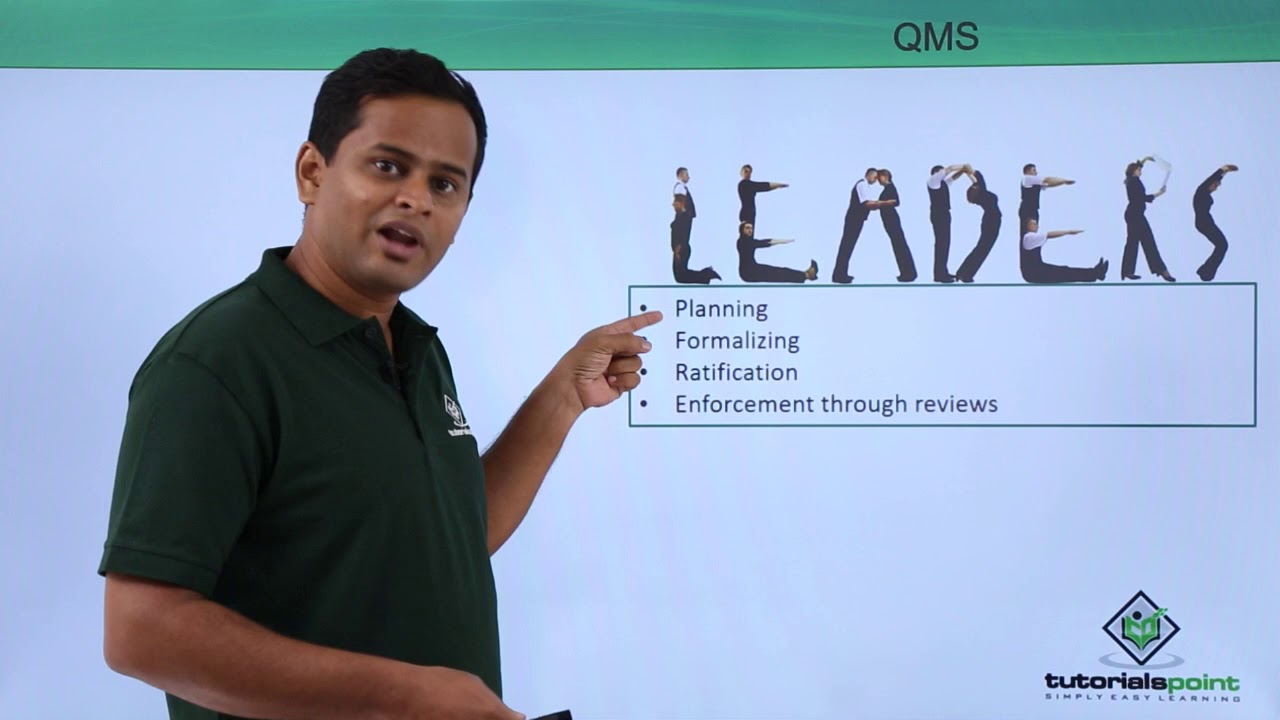
Quality Management - Leadership
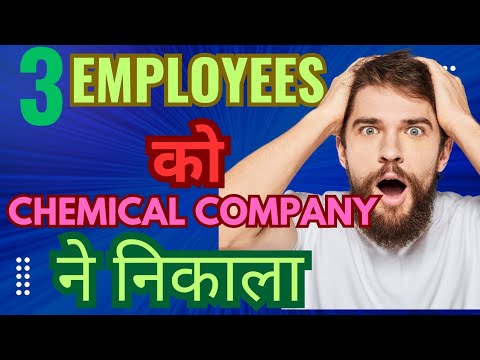
Chemical company ने 3 Employee koi nikala ??Three Employees Fired from Chemical Industry
5.0 / 5 (0 votes)