Inventory Control Technique: ABC Analysis
Summary
TLDRIn this session, the concept of ABC analysis in inventory control is explained. The technique categorizes inventory into three classes: A, B, and C, based on their cost contribution to the total material budget. A Class materials are high-cost items, consuming 70-80% of the budget, requiring close monitoring. B Class items consume 20-30%, while C Class materials represent 50% of the inventory but only 5-10% of the cost. The session details the steps of performing an ABC analysis, from calculating item costs to ranking and classifying materials, with practical examples and graphical representation for better understanding.
Please replace the link and try again.
Q & A
What is the purpose of the ABC analysis technique in inventory control?
-The purpose of the ABC analysis technique in inventory control is to categorize inventory into three classes (A, B, and C) based on the consumption value and quantity of materials. This helps in prioritizing management efforts and resources accordingly.
How are the materials categorized in the ABC analysis?
-Materials are categorized into three classes: A class, B class, and C class. A class materials make up 20% of the total quantity but consume 70-80% of the total budget, B class materials make up 30% of the total quantity and consume 20-30% of the budget, and C class materials make up 50% of the total quantity but consume only 5-10% of the budget.
What is the observation level for A class materials?
-A class materials require high observation due to their high consumption value, accounting for 70-80% of the total budget.
What is the observation level for C class materials?
-C class materials require low observation because, despite comprising 50% of the total quantity, they account for only 5-10% of the total cost.
How do you calculate the cost for each item in the ABC analysis?
-The cost for each item is calculated by multiplying the unit quantity by the unit price. For example, for an item with 700 units priced at 50 rupees each, the total cost would be 35,000 rupees.
What is the next step after calculating the cost for each item in ABC analysis?
-After calculating the cost for each item, the next step is to determine the percentage contribution of each item's cost to the total cost, followed by ranking the items from highest to lowest based on their percentage contribution.
What role does ranking play in the ABC analysis process?
-Ranking helps in organizing the items from highest to lowest based on their percentage of total cost, which is crucial for determining which materials require more attention and which can be managed with less oversight.
What does the cumulative percentage represent in ABC analysis?
-The cumulative percentage represents the accumulated cost percentage as items are ranked from highest to lowest. It helps to visualize how much of the total budget is accounted for by each material group.
How are the materials classified visually in the graphical representation of ABC analysis?
-In the graphical representation, materials are classified by plotting their rankings and cumulative percentages. The A class is marked from the origin to about 73.81%, B class from 73.81% to around 90%, and C class from 90% to 100%.
Why is ABC analysis important for material management?
-ABC analysis is important for material management because it helps prioritize materials based on their consumption value, enabling more efficient resource allocation and focused management efforts for high-impact items.
Outlines
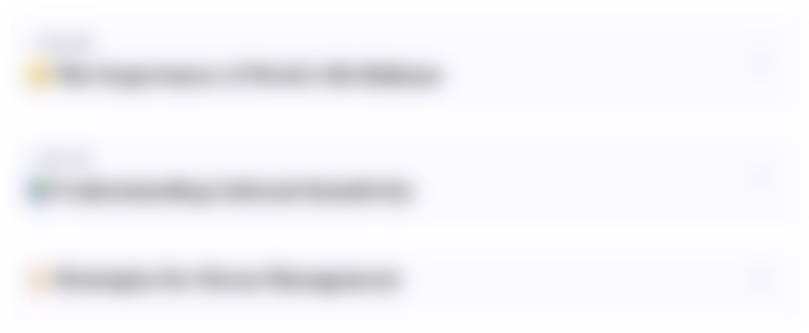
This section is available to paid users only. Please upgrade to access this part.
Upgrade NowMindmap
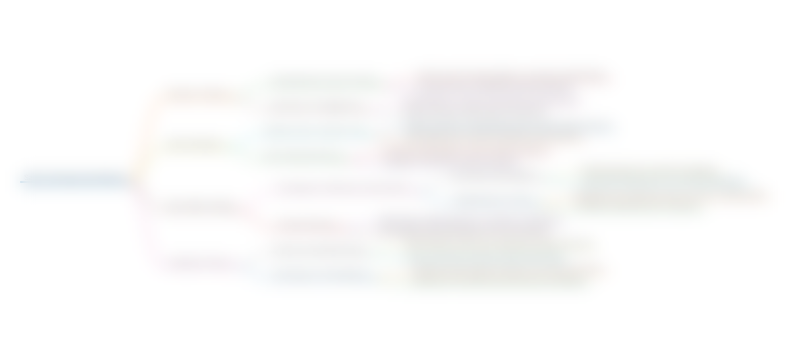
This section is available to paid users only. Please upgrade to access this part.
Upgrade NowKeywords
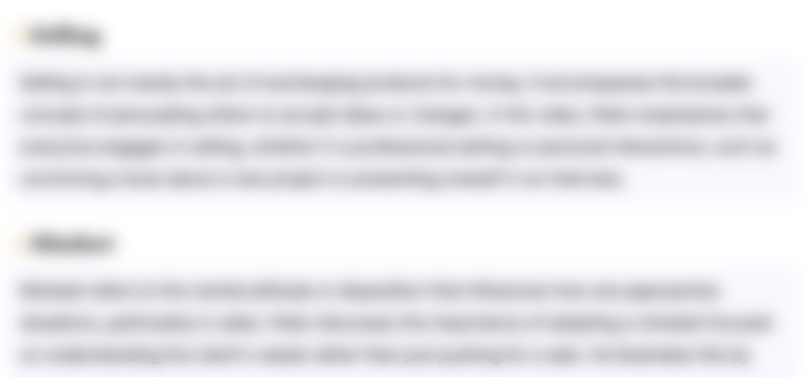
This section is available to paid users only. Please upgrade to access this part.
Upgrade NowHighlights
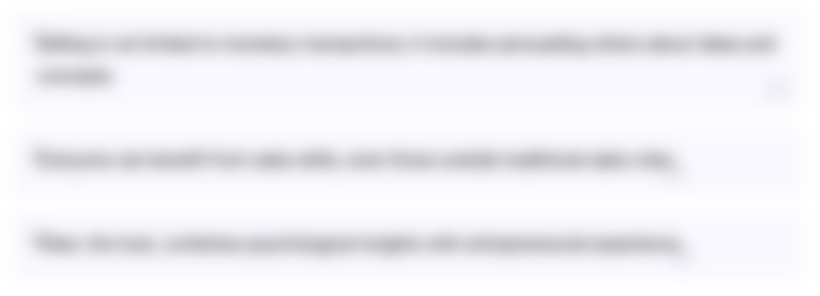
This section is available to paid users only. Please upgrade to access this part.
Upgrade NowTranscripts
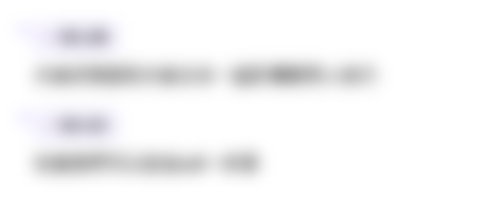
This section is available to paid users only. Please upgrade to access this part.
Upgrade NowBrowse More Related Video
5.0 / 5 (0 votes)