Repairing a Cylinder Barrel for BIG D11 Bulldozer! | Machining, Welding & Honing
Summary
TLDRThe video follows Kurtis doing a cylinder rebarrel job on a bulldozer blade tilt cylinder. He shows the worn area of the barrel that needs replacing, cuts the original barrel off to salvage the head flange, machines a new barrel section, welds the head flange onto it, hones the new barrel to spec, welds on the other barrel end, reclaims the cylinder eye, and completes the rebuild. There is friendly banter with his partner Karen and the camera operator, demonstrating the amiable shop environment.
Takeaways
- 😀 This video covers the process of rebarreling a bulldozer blade tilt cylinder barrel that had an imperfection
- 👷♂️ The original barrel was borderline out of spec due to being oversized, so a full rebarrel was required
- 🔨 The old barrel was cut off, and a new pre-honed tube was machined to size and welded on
- 📏 The heat affected zone caused the barrel to shrink 0.4mm which needed to be honed out
- 💎 Rough honing stones were used first, followed by finishing stones to get the final dimension
- ⚙️ The barrel end was precisely reattached using alignment marks taken before disassembly
- 🌡️ Preheating was used for the large barrel weld to prevent too rapid cooling
- 🛠️ The weld tops were sanded smooth and the eye was reclaimed after honing was complete
- ✅ The rebarreling restored the cylinder to 100% standard spec
- 😊 The completed job was wrapped up, strapped down and returned to the happy customer
Q & A
What is the name of the part being worked on?
-A blade tilt barrel off a D11T bulldozer, used to tilt the blade left and right.
What was the original job for this part?
-To have an eye reclaim and the barrel rehoned, as there was an imperfection in the barrel.
Why couldn't the imperfection in the barrel be honed out?
-The barrel was already 8 thou oversized, which is borderline out of spec. More material would need to be removed, making it way out of spec.
What is the solution for the barrel imperfection?
-To do a full barrel replacement by machining and welding a new barrel.
What material is used for the new barrel?
-Pre-honed ST52 steel tube, with 10.5 inch ID and 12.75 inch OD.
What welding process is used?
-GMAW or MIG welding, using a dual shield wire backed up with Argon/CO2 shielding gas.
How much did the heat from welding shrink the barrel?
-0.4 thou in the heat affected zone, which is pretty standard.
What tools are used to bring the new barrel to the proper dimensions?
-Rough honing stones, then finishing stones to obtain the final size and surface finish.
How will the old barrel eye be refurbished?
-A standard eye reclaim procedure will be done, but not recorded, to bring it back into spec.
What is the final step once all machining and welding is complete?
-The part will be wrapped, strapped down securely, and shipped back to the customer.
Outlines
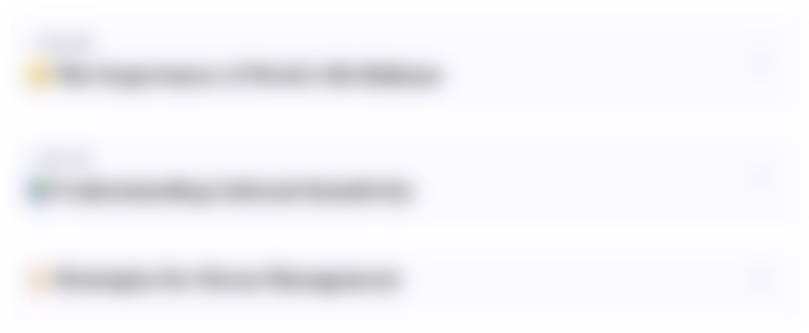
This section is available to paid users only. Please upgrade to access this part.
Upgrade NowMindmap
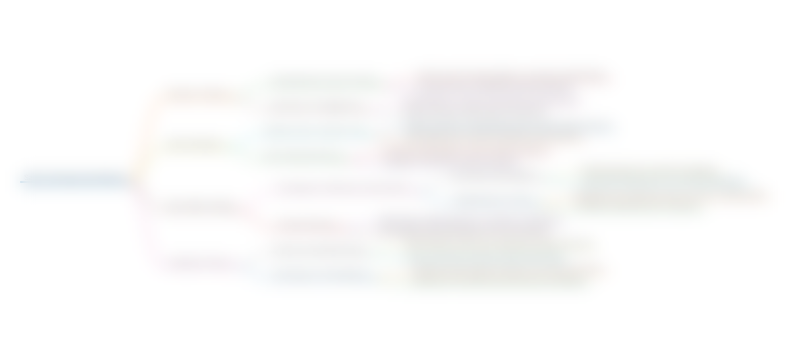
This section is available to paid users only. Please upgrade to access this part.
Upgrade NowKeywords
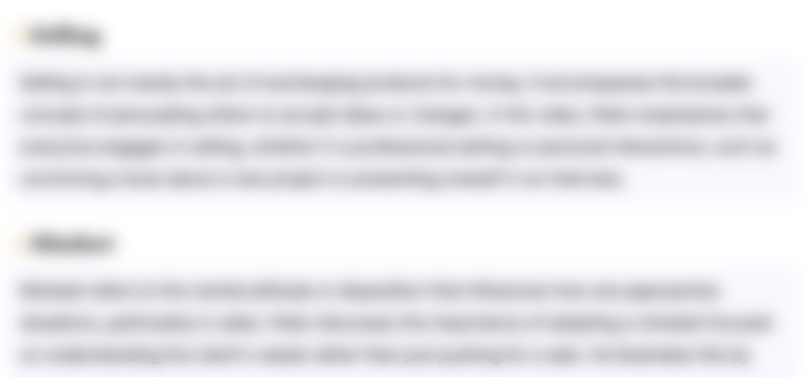
This section is available to paid users only. Please upgrade to access this part.
Upgrade NowHighlights
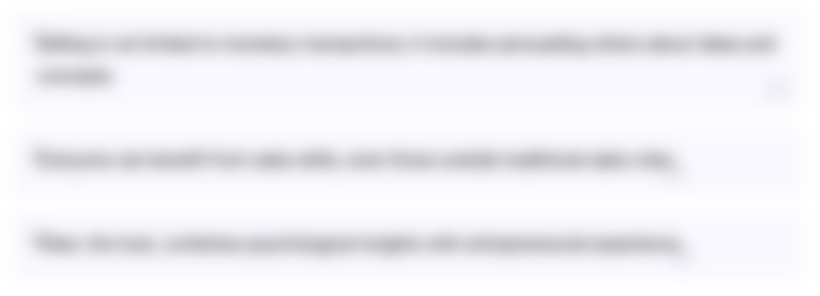
This section is available to paid users only. Please upgrade to access this part.
Upgrade NowTranscripts
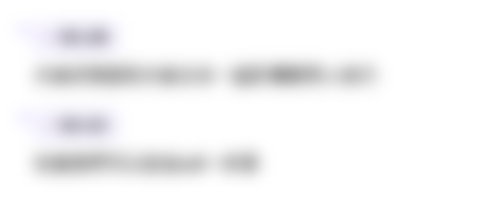
This section is available to paid users only. Please upgrade to access this part.
Upgrade NowBrowse More Related Video

I Bought a COLOSSAL Caterpillar D9 Dozer, DIRT CHEAP!!
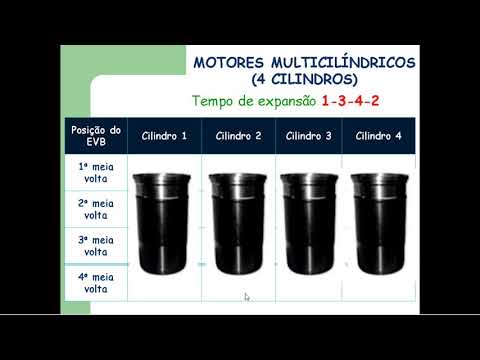
MultiCilindricos
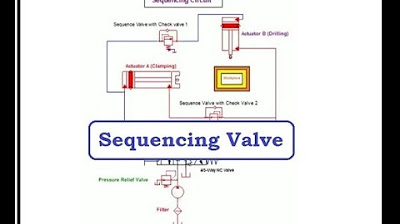
Sequencing circuit in hydraulics |Application of Sequencing Valve |Sequencing of hydraulic Actuators
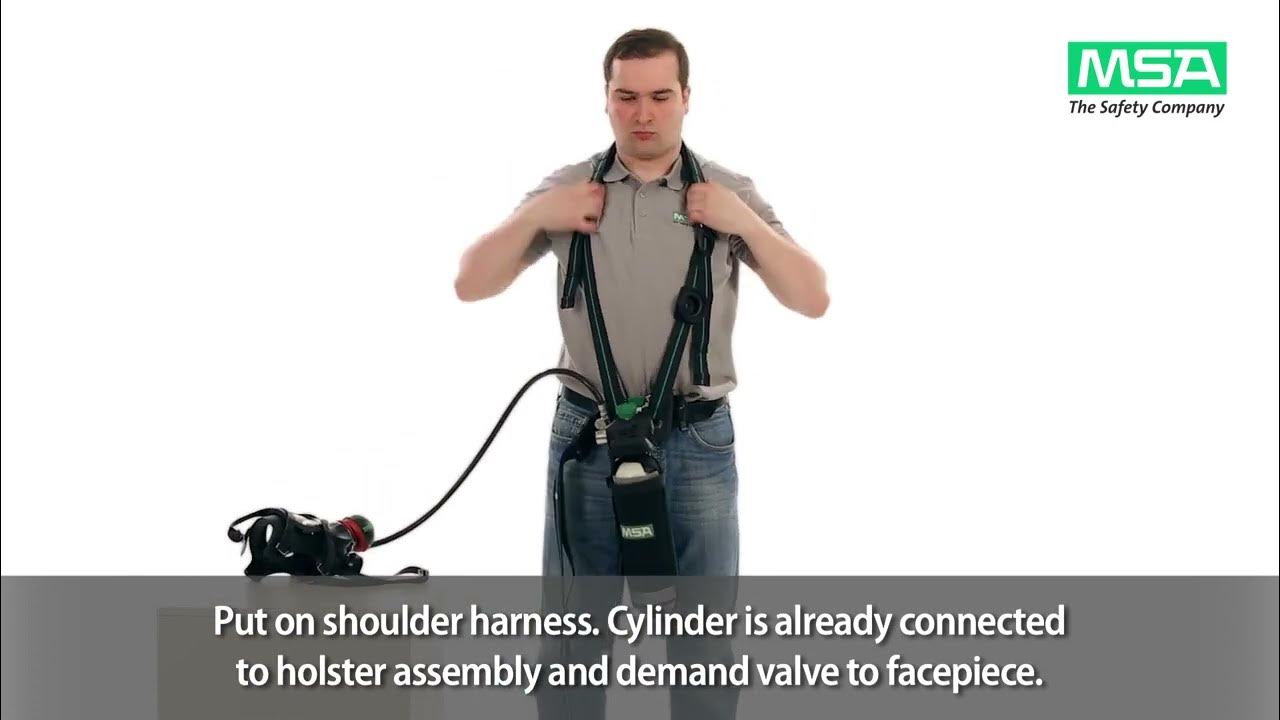
PremAire® Combination Supplied Airline Respirator
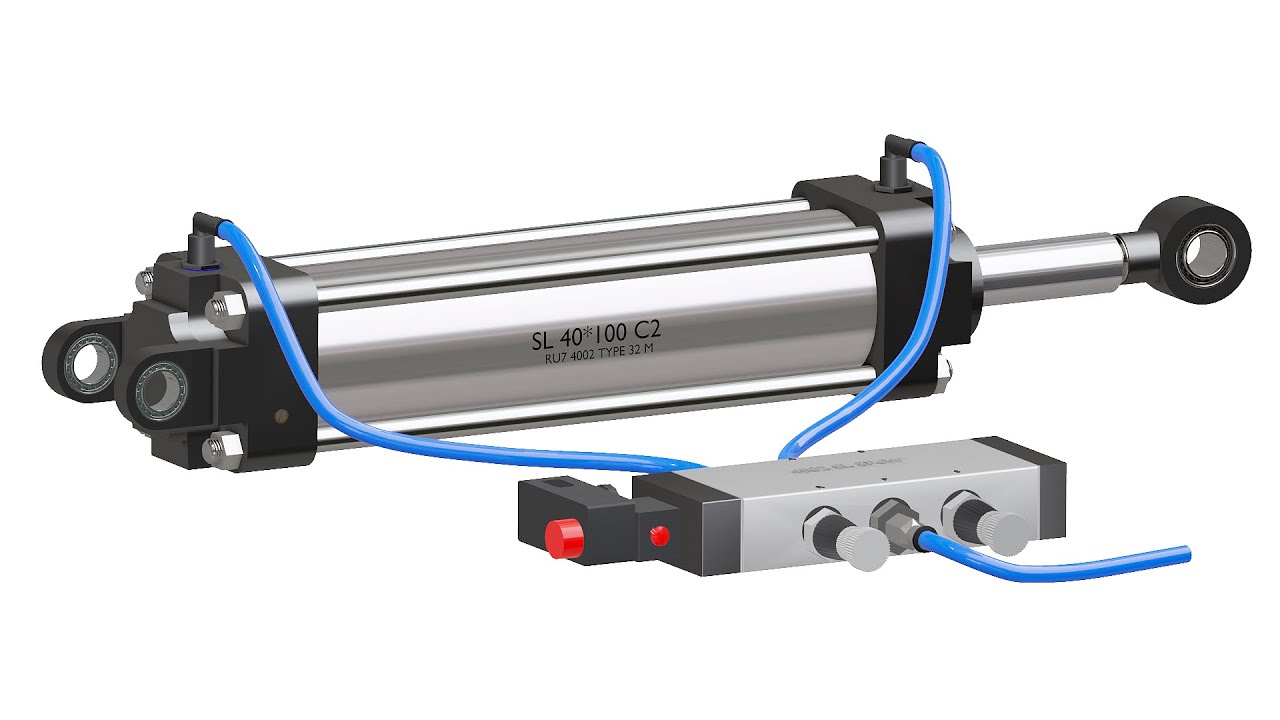
Pneumatic Cylinder Working explained (Animation)

2024 Landcruiser 2.8l Auto TOWING TEST vs the V8 70 series
5.0 / 5 (0 votes)