The easiest way to make a robot arm base
Summary
TLDRIn this video, the creator builds a precise rotating base for a robot arm designed to hold a camera. By using an innovative cycloidal gear system and custom 3D printed bearings, the creator eliminates wobble and ensures smooth, stable motion. The robot arm is powered by a stepper motor controlled by an Arduino Mega, and design improvements, such as adding lubrication and replacing weak parts, are made to address stability issues. The video showcases the assembly process, testing, and plans for future upgrades, including a camera gimbal and full-axis motion control.
Takeaways
- 😀 The robot arm's shoulder and elbow were built using cycloidal drives, allowing movement on the X and Z planes.
- 😀 The goal is to create a rotating base for the robot arm to move it to any XYZ coordinate with high accuracy.
- 😀 Belt drives and traditional gears are not ideal for the rotating base due to issues like reliance on non-3D printed hardware and backlash.
- 😀 Eccentrically cycloidal gears were chosen for the rotating base as they provide a high reduction with fewer parts and no sliding friction.
- 😀 A custom-made, large eccentrically cycloidal gear with a 20:1 reduction ratio is used to prevent wobble and maintain stability.
- 😀 A combination of 3D printed bearings and steel balls in a cage was used to create cost-effective yet functional bearings for the base.
- 😀 The robot arm base assembly involves heat inserts, screws, stepper motors, bearings, and a custom-made large gear and pin setup.
- 😀 There was a mistake in the initial bearing placement, which was corrected by using super glue to secure it in place.
- 😀 After assembling the parts, the base was connected to a DM542 stepper motor driver and an Arduino Mega for testing the rotation.
- 😀 After testing, lubrication was added to improve the smoothness of the movement, and minor adjustments were made to reduce wobble in the arm.
- 😀 The camera setup was added to the robot arm, and two axes were successfully tested with the current stepper drivers. Future improvements include adding a third driver for full movement control.
Q & A
What is the main goal of building the rotating base for the robot arm?
-The main goal is to enable the robot arm to move to any XYZ coordinate while maintaining high accuracy and stability, especially since the arm will be used to hold a camera.
Why does the creator avoid using traditional belt drives or gears for the robot's base?
-Belt drives require non-3D printed hardware like belts, and traditional gears can exhibit backlash, which affects the accuracy of movement. The creator opts for eccentrically cycloidal gears to avoid these issues.
How do eccentrically cycloidal gears work, and why are they used in this project?
-Eccentrically cycloidal gears work by using a disc from a cycloidal reducer and simplifying the drive with a pin that meshes with the disc's nodes. These gears provide high reduction with minimal parts and avoid the sliding friction typical of worm drives.
What is the significance of using a large gear and small pin in the rotating base?
-The large gear and small pin provide a 20:1 reduction ratio, ensuring the robot's base is steady and free from wobble, which is crucial for holding a camera accurately.
Why does the creator prefer a 3D printed bearing over purchasing one?
-The creator found buying a large bearing to be expensive, so they opted to create a 3D printed bearing using a design with a cage holding steel ball bearings, which performs surprisingly well despite being more fiddly to assemble.
What role do heat inserts play in the assembly of the robot's rotating base?
-Heat inserts are used to reinforce the holes in the housing, allowing screws to be inserted securely and providing a strong, stable connection for the components.
What was the mistake made during the assembly of the rotating base, and how was it addressed?
-The mistake was placing the large bearing on the wrong side of the assembly. To fix this, the creator used super glue to hold it in place, though the bearing should have been placed on the opposite side.
What was the issue with wobble in the robot arm, and how was it fixed?
-The wobble was caused by movement inside the cycloidal drive and a flimsy component. The creator replaced the flimsy part with an aluminum tube and added a new lid to the cycloidal drive to stabilize the system.
How is the robot arm controlled, and what is the current status of its functionality?
-The robot arm is controlled by stepper motors connected to a DM 542 stepper driver and an Arduino Mega running code to rotate the base and shoulder. Currently, the arm moves smoothly, but the third motor for full 3-axis control is still pending.
What future plans does the creator have for the robot arm in the next video?
-The creator plans to build a camera gimbal to replace the current setup and integrate the third stepper motor to achieve full control over all three axes of the robot arm.
Outlines
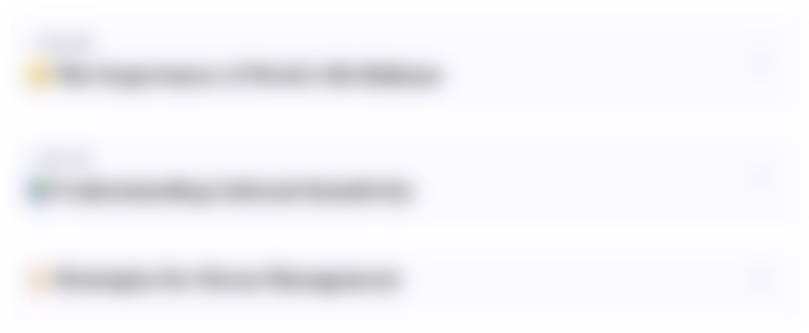
This section is available to paid users only. Please upgrade to access this part.
Upgrade NowMindmap
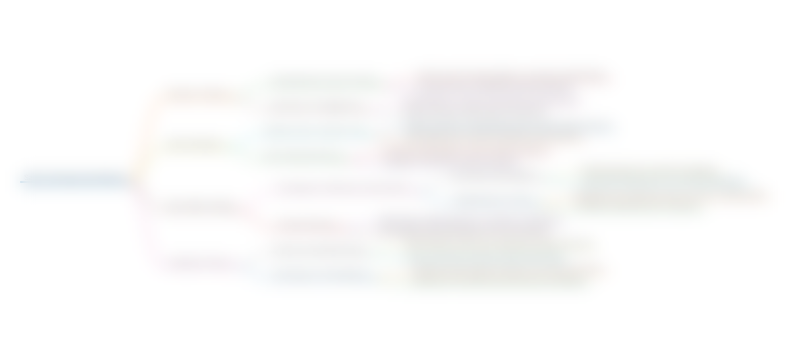
This section is available to paid users only. Please upgrade to access this part.
Upgrade NowKeywords
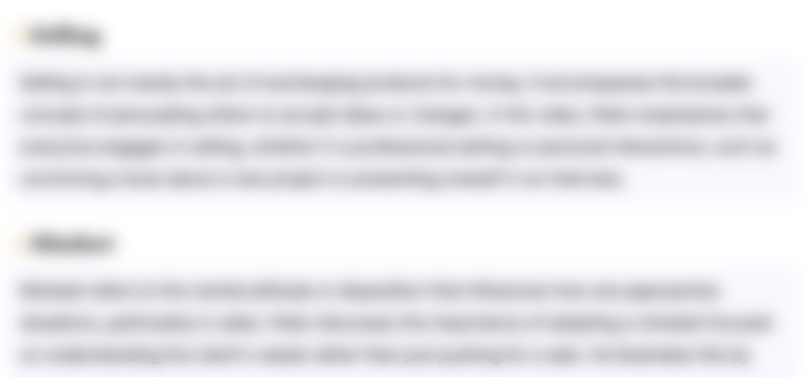
This section is available to paid users only. Please upgrade to access this part.
Upgrade NowHighlights
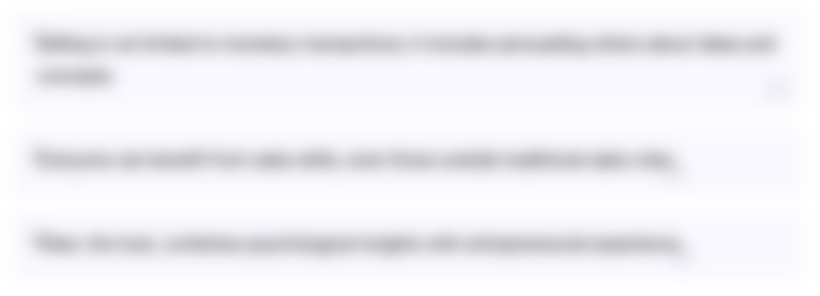
This section is available to paid users only. Please upgrade to access this part.
Upgrade NowTranscripts
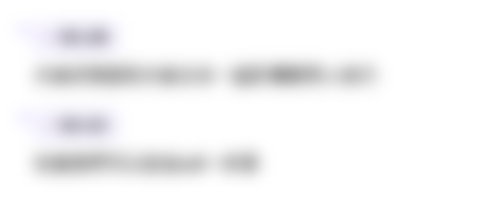
This section is available to paid users only. Please upgrade to access this part.
Upgrade NowBrowse More Related Video

1000A Foothill Robotics | Pits & Parts | High Stakes
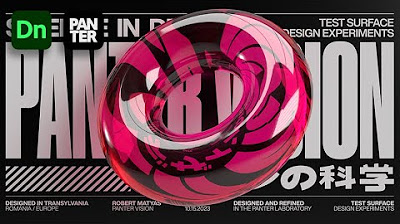
How to Add Background Image and Glass Materials in Adobe Dimension

7 Alat Ini Dijamin Akan Mempermudah Pekerjaan Kalian yang Berat Sekalipun!

I Built a Robot Dog Using... Rope?
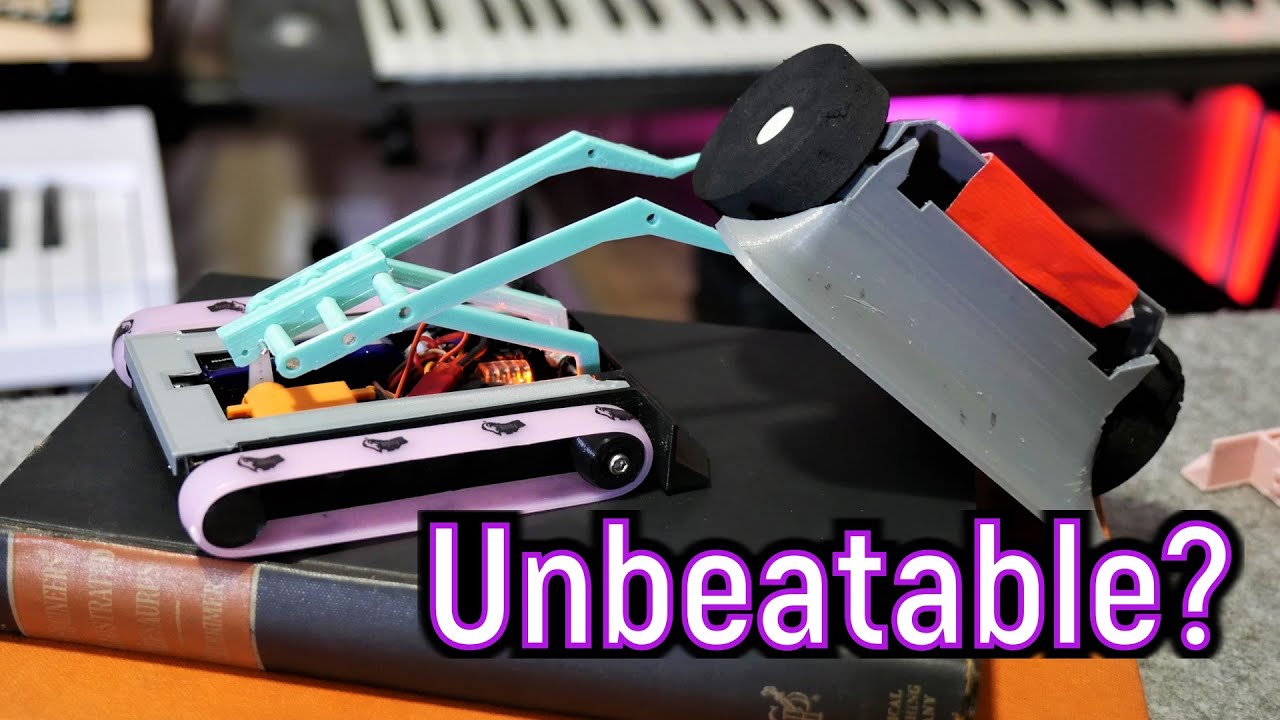
My 3D Printed Robot sucked... so I made an UNBEATABLE one!

Building a Generator
5.0 / 5 (0 votes)