Prinsip Dasar Ultrasonic Testing
Summary
TLDRThe video explains the evolution of ultrasonic technology, highlighting its history from the 1950s to modern applications. Initially used in large, bulky devices, ultrasonic tools have become more compact and efficient over the decades. Key applications include thickness measurement, flaw detection in metals, and medical uses like ultrasound imaging. The script also covers the underlying science of ultrasonic waves, including their frequency ranges and different types such as longitudinal and transversal waves. Various industrial sectors, from aviation to petrochemicals, use these tools for precise inspections, showcasing the technology's broad impact.
Takeaways
- ๐ The history of ultrasonic testing tools dates back to the 1950s, with the first large ultrasonic equipment appearing in the 60s for measuring thickness.
- ๐ In the 1970s, ultrasonic tools became smaller, and by the 80s, they were used for flaw detection in metal casting and welding.
- ๐ The 90s saw the development of portable ultrasonic devices, which made it easier to inspect materials, including in aviation and manufacturing industries.
- ๐ Ultrasonic technology, commonly known in medical imaging as ultrasound, uses sound waves to inspect materials or biological conditions.
- ๐ The basic principle of ultrasonic testing involves sending sound waves into materials and analyzing the echoes to detect flaws or measure thickness.
- ๐ Ultrasonic testing operates at frequencies above 20 kHz, beyond the range of human hearing, and can be used for both inspection and medical diagnostics.
- ๐ Various applications of ultrasonic technology include medical imaging (such as fetal ultrasound) and industrial inspections (such as metal fatigue detection).
- ๐ The frequency range for ultrasonic waves used in testing can reach up to several mega-hertz, with specialized tools operating between 2 MHz and 5 MHz.
- ๐ Ultrasonic transducers play a key role in these systems by generating and receiving sound waves, with different angles of transmission depending on the application.
- ๐ Ultrasonic waves are classified into two types: longitudinal (compressional) and transverse (shear), which have different applications depending on the material being tested.
Q & A
What is the history of ultrasonic testing mentioned in the transcript?
-The history of ultrasonic testing begins in the 1950s with the use of large, bulky instruments. By the 1960s, thickness gauges and ultrasonic tools were introduced for measuring material thickness. In the 1970s, these tools became more compact, and by the 1980s, ultrasonic testing was commonly used for flaw detection in metals. In the 1990s, portable, handheld devices were developed, making it easier to use in various industries.
What is the principle behind ultrasonic testing as explained in the script?
-Ultrasonic testing uses high-frequency sound waves to detect flaws or measure the thickness of materials. These sound waves are typically above 20,000 Hz (20 kHz), which is outside the range of human hearing. The waves are transmitted through a material and reflected back, allowing the system to analyze the material's properties.
What industries use ultrasonic testing?
-Ultrasonic testing is widely used across industries such as aerospace, manufacturing, automotive, power generation, construction, petrochemicals, and welding. It is particularly useful in detecting flaws in materials like metals and plastics, ensuring structural integrity.
How is ultrasonic testing similar to medical ultrasound?
-Both medical ultrasound (USG) and ultrasonic testing use the same principle of high-frequency sound waves to gather data. The main difference is that medical ultrasound uses lower frequencies to visualize soft tissues, while industrial ultrasonic testing uses higher frequencies to analyze material properties and detect flaws.
What types of ultrasonic probes are used in testing?
-There are different types of probes used in ultrasonic testing, including straight probes and angle beam probes. The angle beam probe, for example, is often used to inspect welds, where the angle of the sound waves is adjusted to detect flaws at different angles.
How does ultrasonic testing detect flaws in materials?
-Ultrasonic testing works by emitting high-frequency sound waves into a material. These waves travel through the material, and if there is a flaw, such as a crack or void, the waves will reflect back differently. The system then analyzes these reflections to determine the size, location, and type of flaw.
What is the difference between longitudinal and transverse waves in ultrasonic testing?
-Longitudinal waves are sound waves where the particles of the material vibrate in the same direction as the wave. These are typically used for normal ultrasonic probes. Transverse waves, also known as shear waves, cause the particles to vibrate perpendicular to the wave's direction. These are often used for angle beam probes, especially in welding inspections.
What was the significance of the evolution of ultrasonic devices over time?
-The evolution of ultrasonic devices from large, bulky machines to compact, portable models greatly increased the accessibility and efficiency of ultrasonic testing. This made it possible for industries to perform inspections in various environments, such as on-site or in the field, rather than relying on stationary, industrial-sized equipment.
What are some challenges associated with ultrasonic testing?
-Challenges in ultrasonic testing include the need for skilled operators to interpret results accurately, the potential for surface roughness or material irregularities to affect readings, and the difficulty in accessing certain areas of large structures for inspection.
How does the frequency of ultrasonic waves affect the testing process?
-The frequency of ultrasonic waves determines the resolution and penetration ability of the test. Higher frequencies provide greater resolution but have less penetration power, making them suitable for detecting smaller flaws near the surface. Lower frequencies penetrate deeper into materials, which is useful for inspecting thicker materials.
Outlines
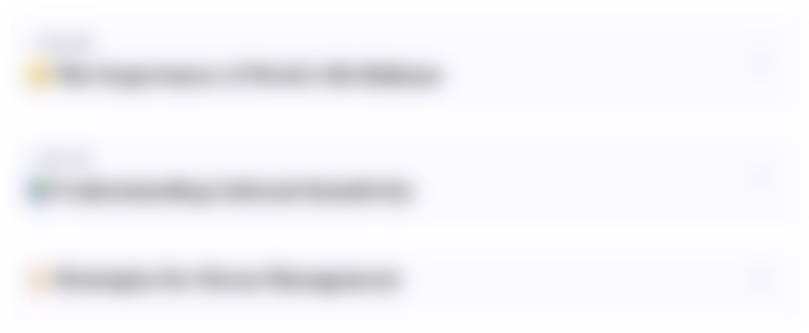
This section is available to paid users only. Please upgrade to access this part.
Upgrade NowMindmap
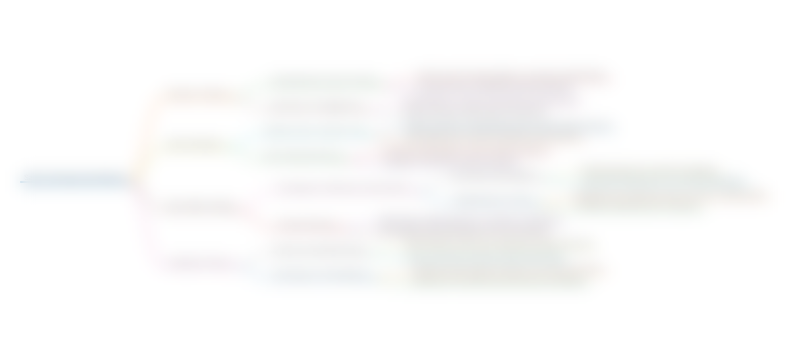
This section is available to paid users only. Please upgrade to access this part.
Upgrade NowKeywords
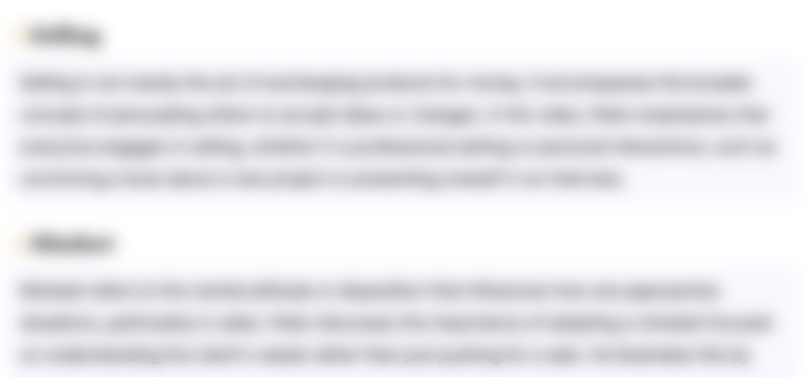
This section is available to paid users only. Please upgrade to access this part.
Upgrade NowHighlights
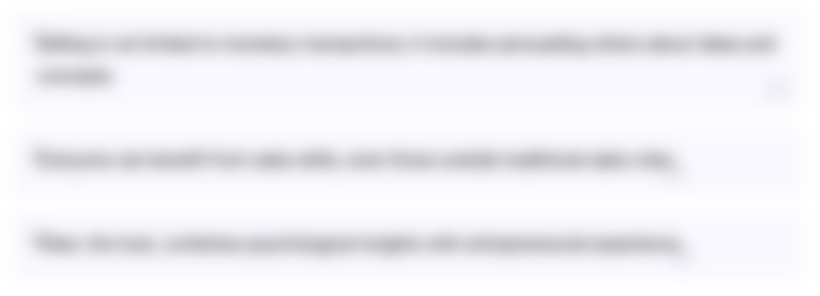
This section is available to paid users only. Please upgrade to access this part.
Upgrade NowTranscripts
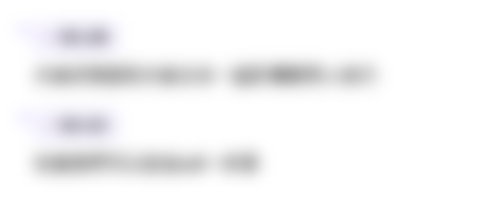
This section is available to paid users only. Please upgrade to access this part.
Upgrade NowBrowse More Related Video
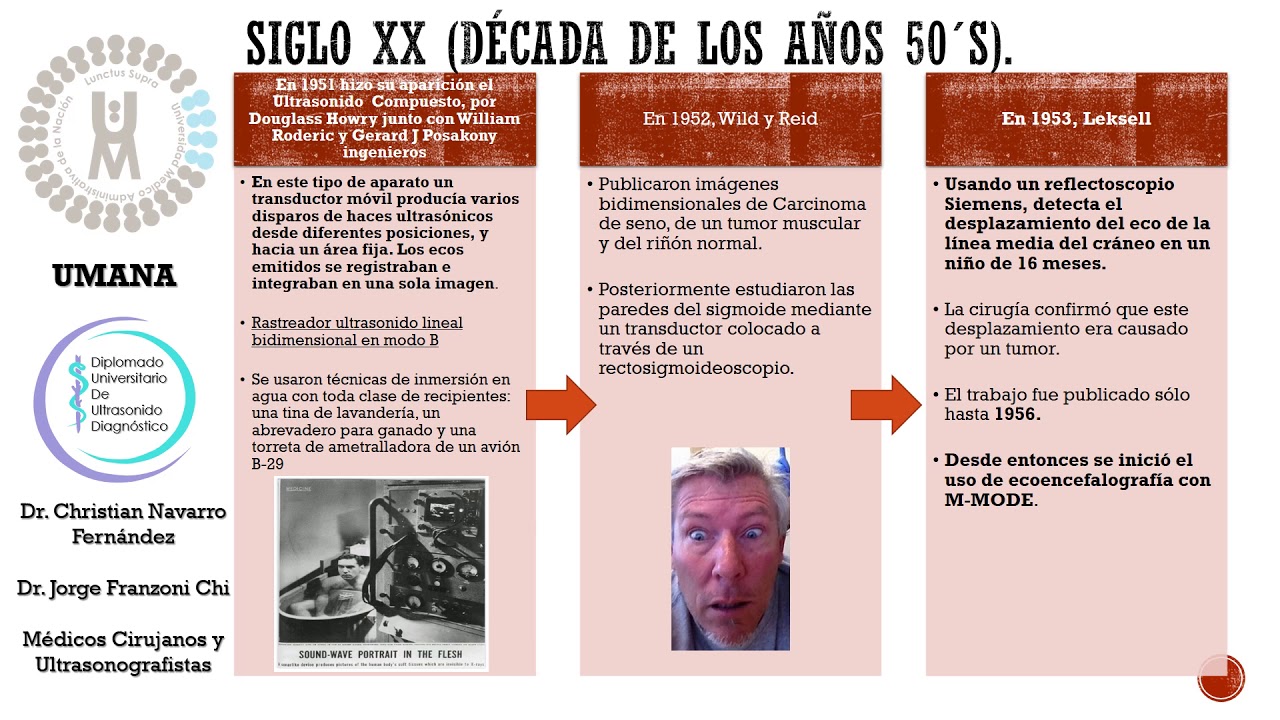
1 1 2 HISTORIA DE LA ULTRASONOGRAFIA
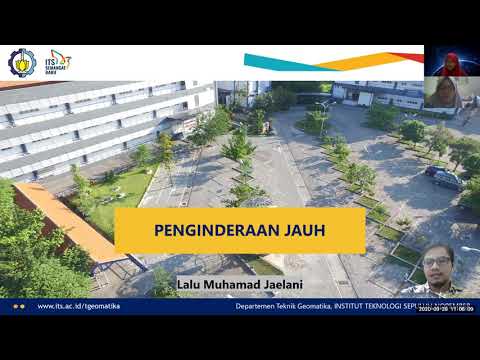
Penginderaan Jauh: Pertemuan 1
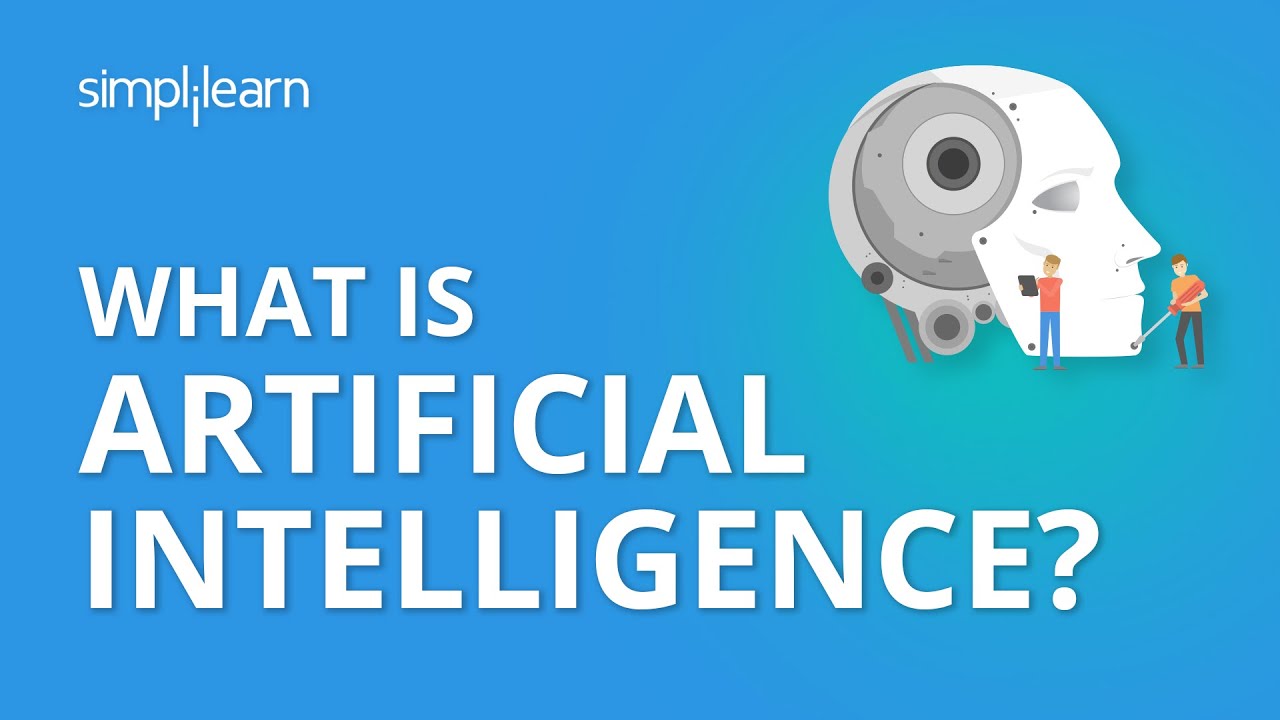
What is Artificial Intelligence? | Artificial Intelligence in 10 Minutes | What is AI? | Simplilearn
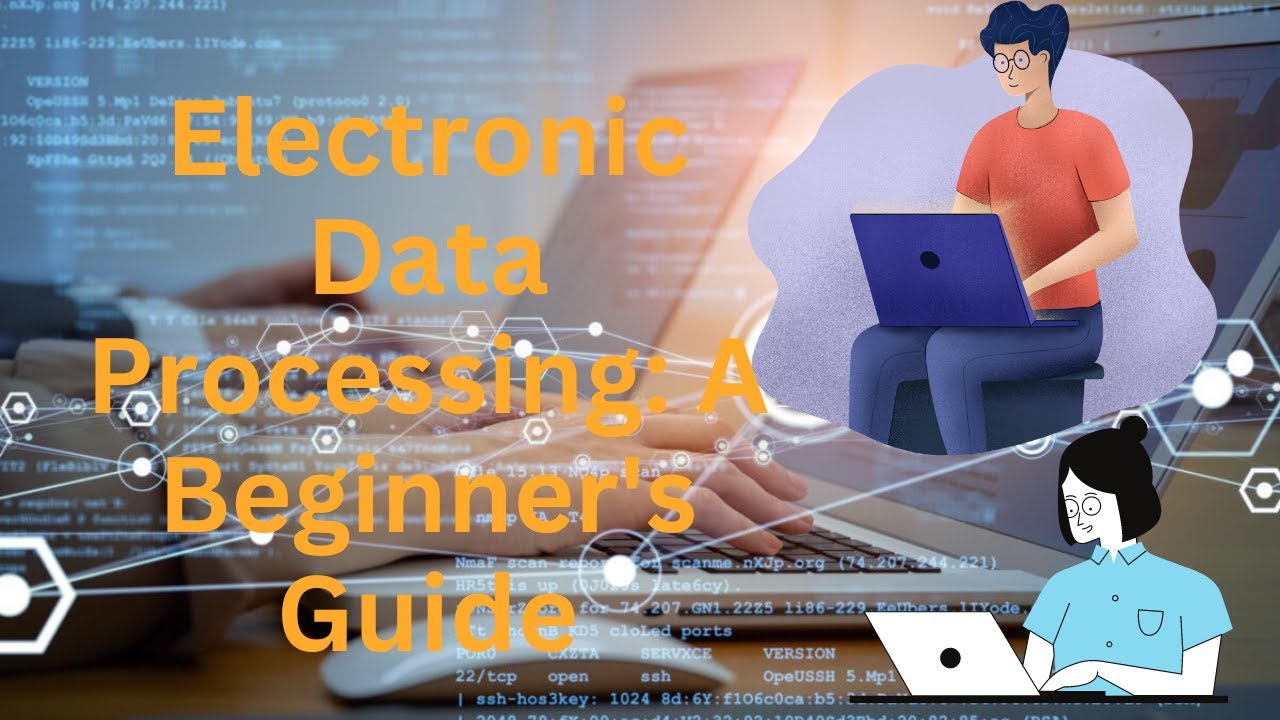
Electronic Data Processing: A Beginner's Guide
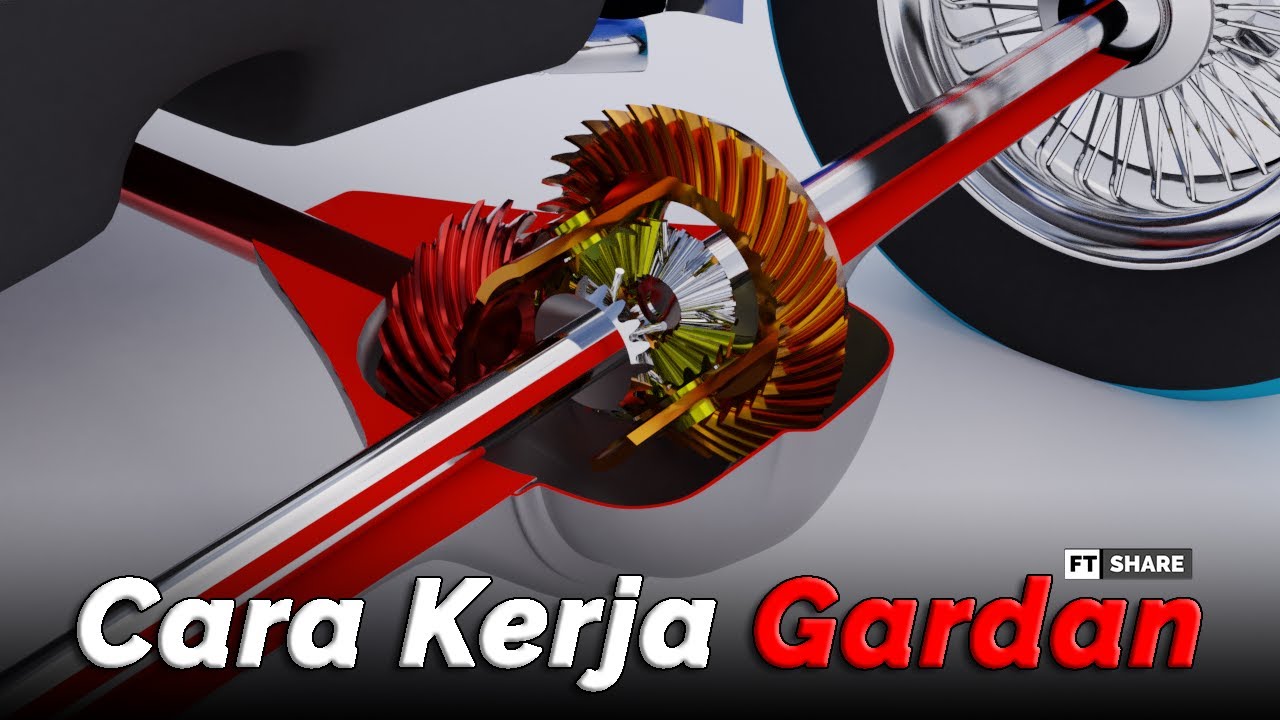
Bagaimana Differential / Gardan Bekerja | Komponen Simple Yang Terlihat Rumit - Real Wheel Drive
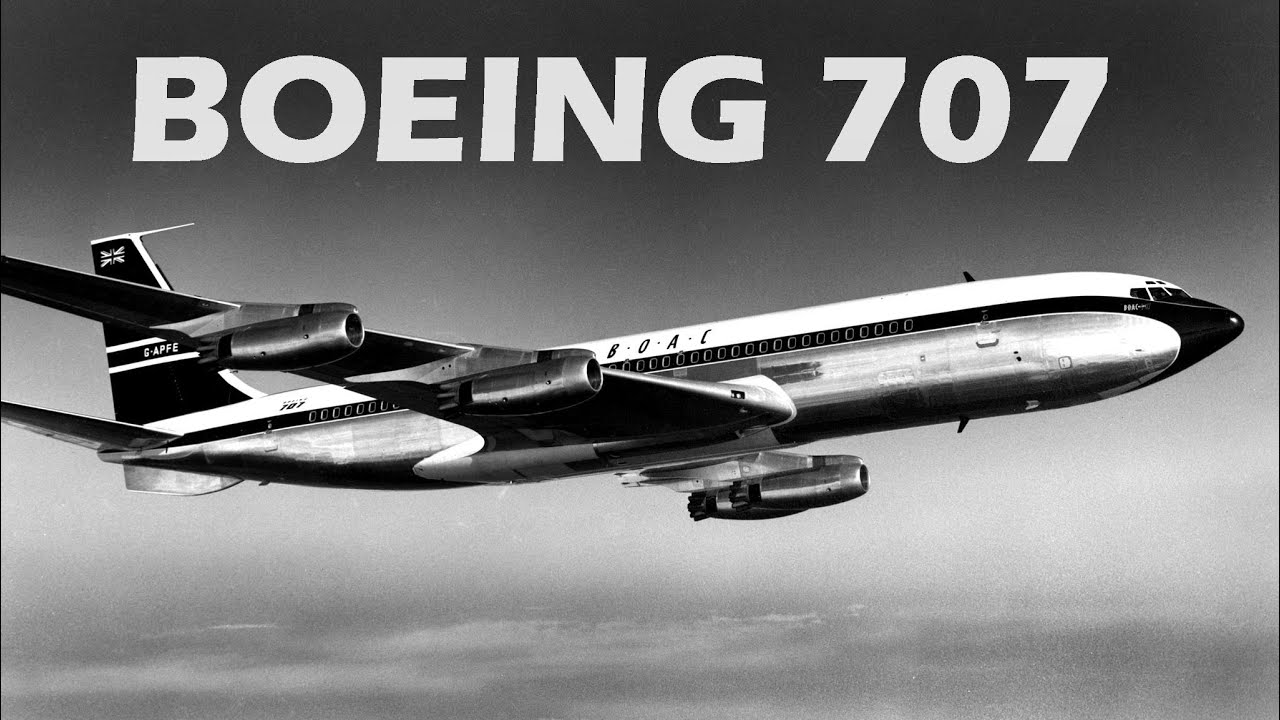
BOEING 707 - America's Revolutionary First Commercial Passenger Jet!
5.0 / 5 (0 votes)