Directional Control Valve Basics - Part 1
Summary
TLDRIn this Lunchbox Sessions training, Carl introduces the basics of directional control valves, focusing on four-port designs. He explains two-position and three-position valves, detailing their functions in extending and retracting cylinders. The three-position valve allows for mid-stroke stopping, while the float center valve connects all ports, ideal for vertical applications when paired with check valves. Emphasizing the implications of valve selection in hydraulic systems, Carl highlights the importance of reliability and performance. This session sets the stage for more advanced topics in hydraulic control systems, encouraging viewers to explore interactive resources.
Takeaways
- ๐ Four-port directional control valves have ports labeled P, T, A, and B, where P is for pump supply, T is for tank return, and A and B are work ports connected to cylinders.
- ๐ The two-position valve allows extending and retracting the cylinder but does not stop it mid-stroke, automatically returning to the P to A position when released.
- ๐ The three-position valve features a spring-centered neutral position, which blocks the P port and allows for mid-stroke stopping of the cylinder.
- ๐ Internal leakage can occur in the three-position valve over time, leading to cylinder drift in vertical applications.
- ๐ The float center valve connects the A, B, and T ports in the center position, allowing the cylinder to float freely, which is useful for vertical installations.
- ๐ Pilot-operated check valves are needed in float center applications to hold the cylinder mid-stroke, preventing unwanted movement.
- ๐ The relief valve in directional control valves limits the maximum system pressure, ensuring safe operation of the hydraulic system.
- ๐ Closed-center hydraulic systems typically employ valves where the P port is blocked in the neutral position to maintain pressure.
- ๐ A pressure compensated variable displacement pump can be used instead of a gear pump in some hydraulic systems to avoid excessive relief valve activation.
- ๐ The video highlights the importance of understanding different directional control valve configurations for effective hydraulic system design.
Q & A
What are the four ports on a four-port directional control valve, and what do they represent?
-The four ports are labeled P, T, A, and B. The P port is for the supply from the pump, the T port is for the return to the tank or reservoir, and the A and B ports are known as the work ports, which connect to the cylinder.
What is the main function of a two-position four-port valve?
-The two-position four-port valve allows for extending the cylinder by directing flow from P to A and retracting the cylinder by directing flow from P to B. However, it does not permit stopping the cylinder mid-stroke.
How does a three-position valve differ from a two-position valve?
-A three-position valve includes a center position that allows for stopping the cylinder mid-stroke. In this position, the P port is blocked, and A and B ports are also blocked, creating a closed center configuration.
What is the purpose of the relief valve in a directional control valve system?
-The relief valve limits the maximum system pressure to prevent damage when the cylinder is deadheaded against the fully extended or fully retracted position.
What happens to the valve spool in a two-position valve when the lever is released?
-When the lever is released, the internal spring returns the valve spool to the P to A position, allowing the cylinder to extend again.
Why might a three-position valve not be ideal for vertical installations?
-Although the three-position valve allows mid-stroke stopping, internal leakage can develop after many cycles, leading to a slow downward drift of the cylinder when in the neutral position.
What is a float center valve, and how does it function?
-A float center valve allows the A, B, and T ports to connect in the center position, enabling the cylinder to float freely. This configuration is particularly useful for vertical applications.
How do pilot-operated check valves work in conjunction with float center valves?
-Pilot-operated check valves hold the cylinder mid-stroke by using pilot lines that provide a small fixed amount of fluid pressure. When the pilot piston extends, it allows reverse flow through the check valve.
What design considerations minimize leakage in check valves?
-Ball and seat style or poppet and seat style check valves are designed to be more reliable and leak-free since their main components do not wear against each other.
What is the advantage of using a pressure compensated variable displacement pump in a closed center hydraulic system?
-Using a pressure compensated variable displacement pump helps avoid excessive pumping over the relief valve, which can improve efficiency and reduce wear on the system.
Outlines
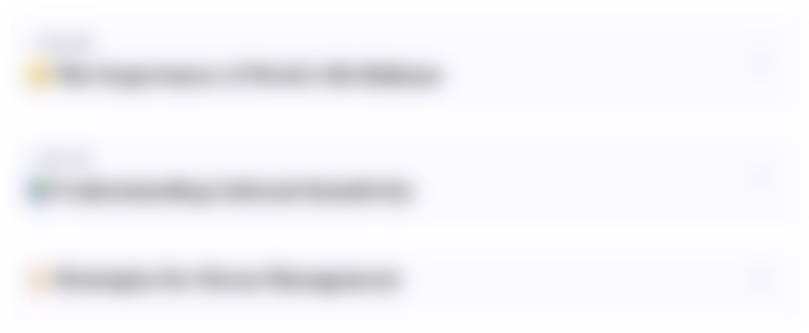
This section is available to paid users only. Please upgrade to access this part.
Upgrade NowMindmap
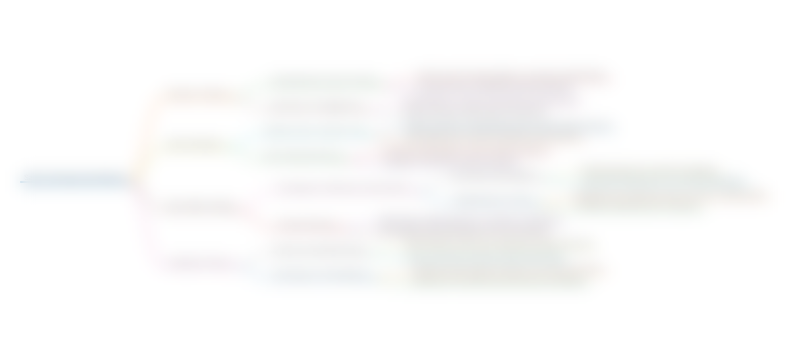
This section is available to paid users only. Please upgrade to access this part.
Upgrade NowKeywords
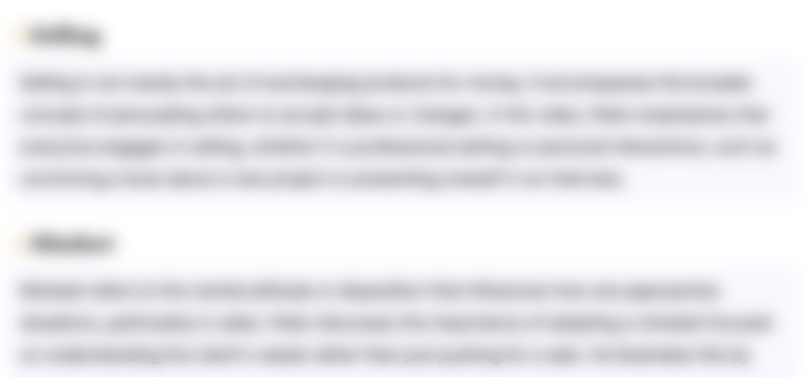
This section is available to paid users only. Please upgrade to access this part.
Upgrade NowHighlights
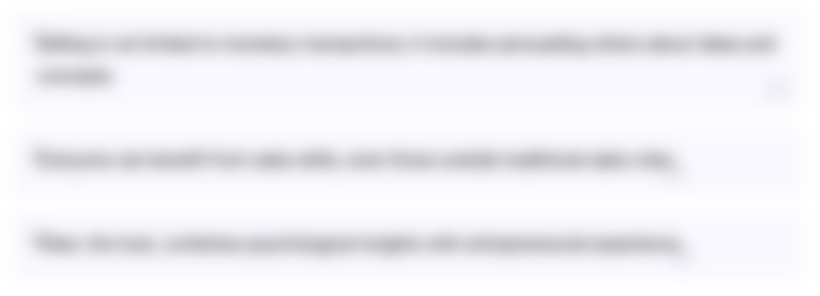
This section is available to paid users only. Please upgrade to access this part.
Upgrade NowTranscripts
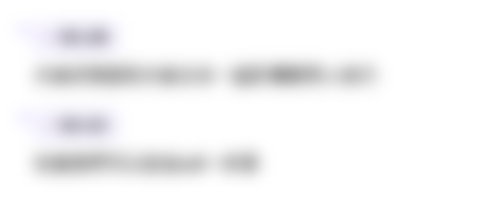
This section is available to paid users only. Please upgrade to access this part.
Upgrade NowBrowse More Related Video
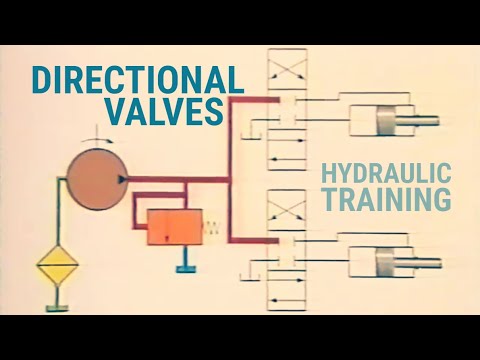
Hydraulic Training Series - Chapter 5 - Directional Valves
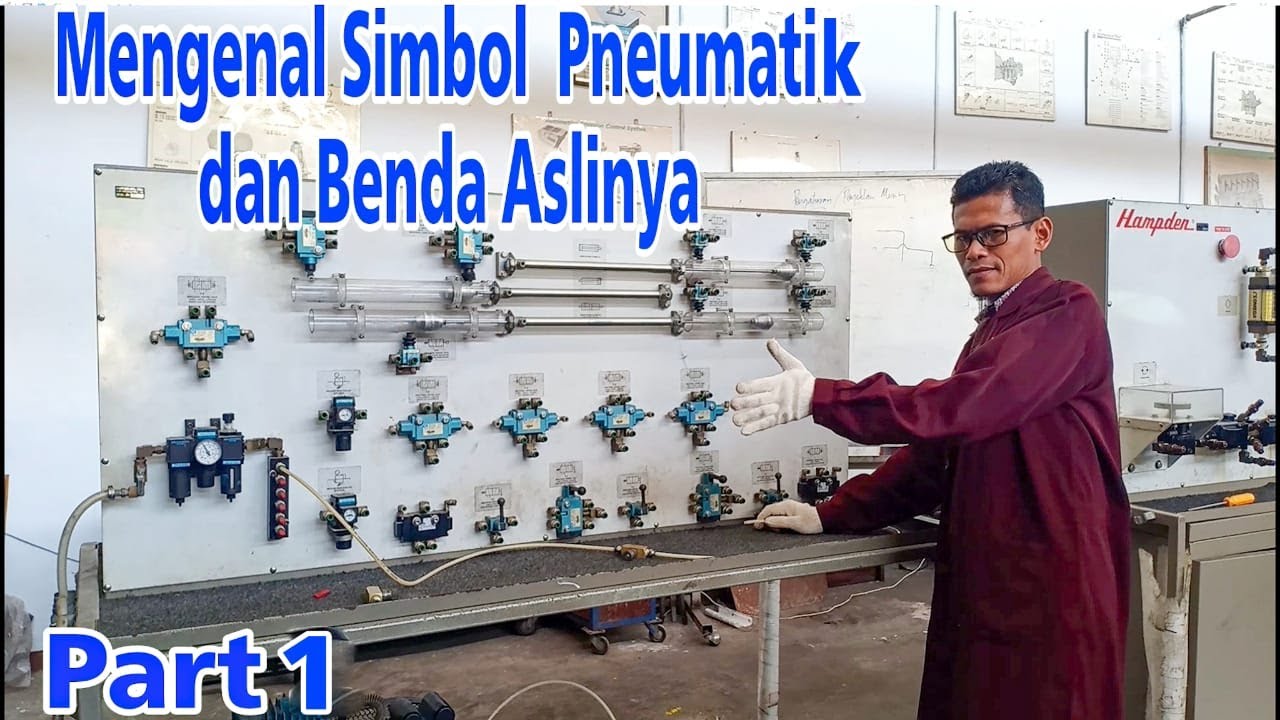
Mengenal Simbol Pneumatik dan Benda Aslinya #waginothok

Mengenal Simbol Hidrolik dan Benda aslinya #waginothok

Electro hydraulic steering system/ships steering gear/4 ram type steering system
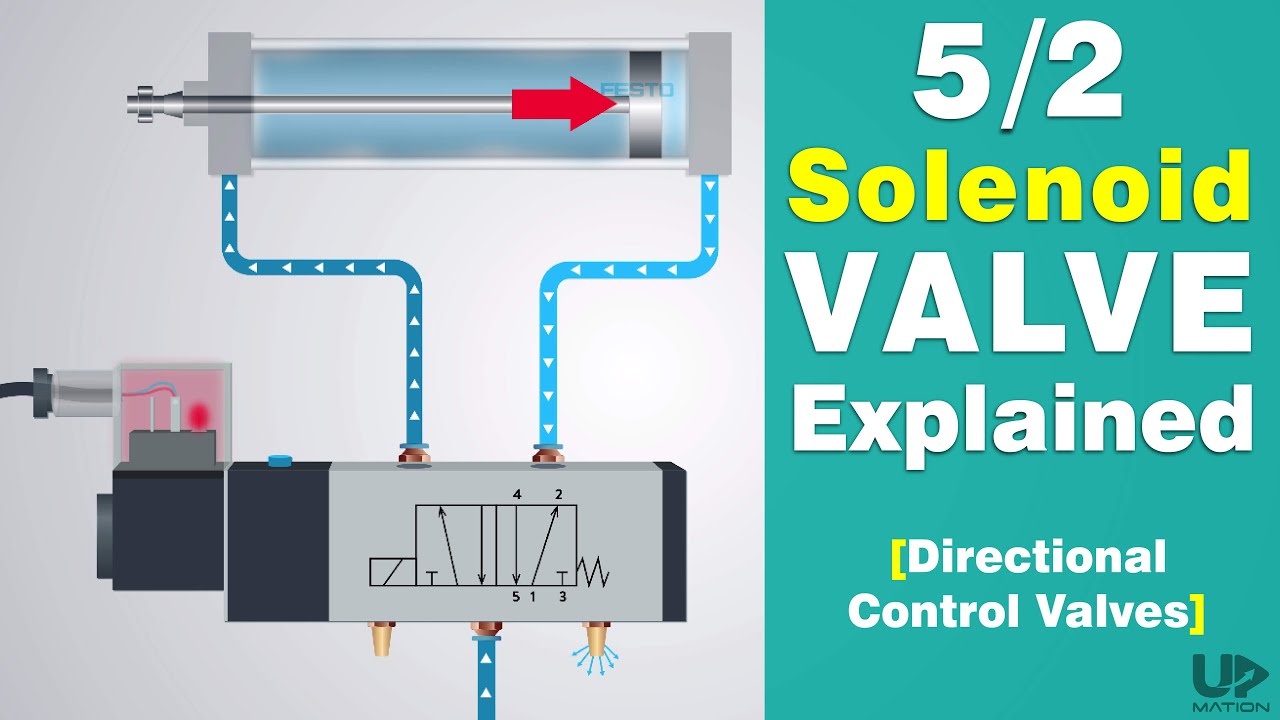
Directional Control Valve Working Animation | 5/2 Solenoid Valve | Pneumatic Valve Symbols Explained
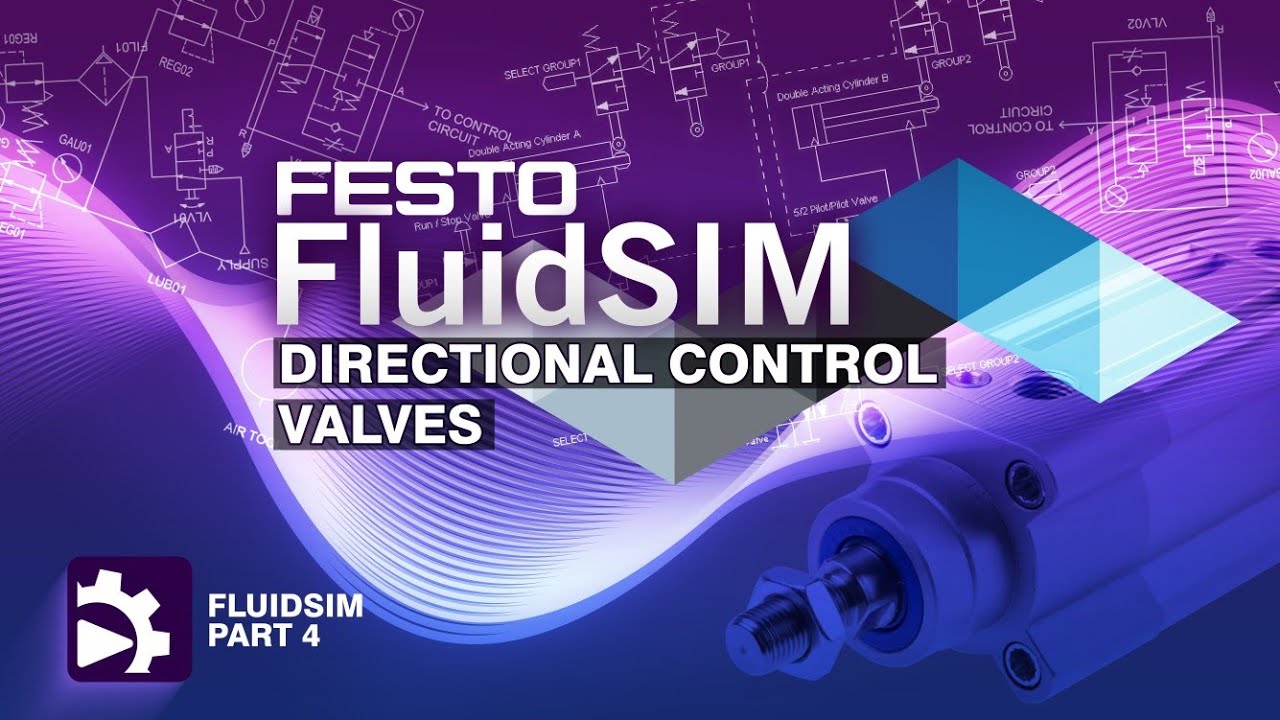
Understanding Directional Control Valve Basics & Symbols | Introduction to FluidSIM | Tutorial 4
5.0 / 5 (0 votes)