A320 Nose Wheel Steering Explained | A320 Landing Gear
Summary
TLDRThis tutorial provides an in-depth look at the A320's nose wheel steering system, emphasizing its critical role in ground maneuvering and taxiing operations. The system is linked to the yellow hydraulic system, with special considerations during one-engine taxiing and pushback procedures. Key aspects include the use of the tiller for precise steering, operational limits at various speeds, and the importance of resetting the steering system in case of faults. The video also highlights safety measures when taxiing with deflated tires and the necessary reliance on rudder control during steering failures.
Takeaways
- 😀 The nose wheel steering system is crucial for directional control during ground operations in the Airbus A320.
- 🚦 In newer Airbus models, the nose wheel steering is connected to the yellow hydraulic system, switching from the green system during one-engine taxi operations.
- ⚙️ During engine start, hydraulic pressure may briefly drop, affecting nose wheel steering; pilots should start the second engine while stopped or in a straight line.
- 🔧 Inserting the nose wheel steering disconnect pin triggers an ECAM memo indicating the system is disengaged, changing to an amber alert if one engine is running with the pin still in.
- 🛞 The tiller, located next to the side stick, controls the nose wheel directly and is effective up to 80 knots with a maximum steering angle of ±75°.
- 🌬️ Beyond 130 knots, the nose wheel steering disconnects, requiring pilots to use more rudder input for steering, especially in strong crosswinds.
- 🚚 During towing and pushback, the nose wheel steering angle can be increased to ±95° with a tow bar and ±85° without.
- 🔄 In case of a nose wheel steering fault, cycling the steering switch off and back on may reset the system and clear the fault.
- ⚠️ If nose wheel steering fails mid-flight, pilots should rely on rudder control to guide the aircraft off the active runway.
- 📖 Always refer to the flight crew operating manual for specific procedures regarding nose wheel steering, especially when taxiing with deflated tires, which limit steering angle to 30°.
Q & A
What is the primary function of the A320 nose wheel steering system?
-The primary function of the A320 nose wheel steering system is to provide precise directional control while the aircraft is on the ground, particularly during taxiing operations.
Which hydraulic system is the nose wheel steering connected to in newer Airbus A320 models?
-In newer Airbus A320 models, the nose wheel steering is connected to the yellow hydraulic system.
What happens during a one-engine taxi situation regarding hydraulic pressure?
-During a one-engine taxi situation, the yellow electric pump takes over to maintain hydraulic pressure, ensuring continued functionality of the nose wheel steering.
Why is it recommended to start the second engine while stopped or in a straight line?
-Starting the second engine while stopped or in a straight line is recommended to avoid losing nose wheel steering momentarily during the hydraulic pressure switch from the yellow electric pump to engine two.
What indicates that the nose wheel steering is disconnected when the disconnect pin is inserted?
-Inserting the nose wheel steering disconnect pin triggers an ECAM memo that displays 'NW steering disconnect' in green, changing to amber if one engine is running with the pin still in place.
What is the maximum steering angle when using the tiller at speeds up to 80 knots?
-When using the tiller at speeds up to 80 knots, the maximum steering angle is ±75°.
How does the nose wheel steering function with the rudder beyond 130 knots?
-Beyond 130 knots, the nose wheel steering disconnects, requiring pilots to rely more on rudder input for directional control, particularly in strong crosswinds.
What steering angles are possible during towing and pushback operations?
-During towing and pushback operations, the steering angles can reach ±95° with a tow bar and ±85° without a nose wheel steering fault.
What are the possible fault conditions for the nose wheel steering system?
-Nose wheel steering faults can occur if both Brake System Control Units (BSCU) fail or if the normal braking system is lost along with low yellow hydraulic pressure.
What should pilots do in the event of a nose wheel steering failure mid-flight?
-In the event of a nose wheel steering failure mid-flight, pilots may initially rely on the rudder to guide the aircraft off the active runway and may require ground assistance for operating with an offset nose wheel.
Outlines
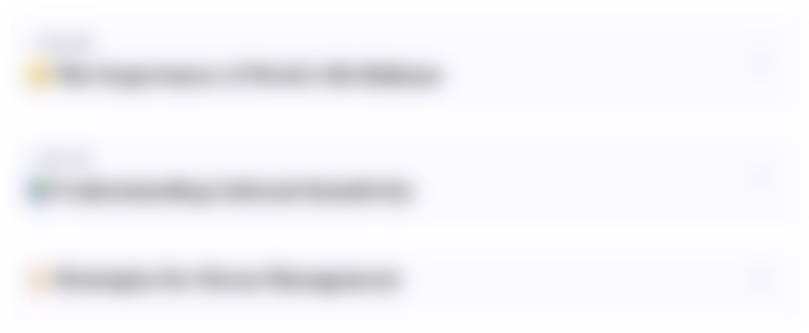
This section is available to paid users only. Please upgrade to access this part.
Upgrade NowMindmap
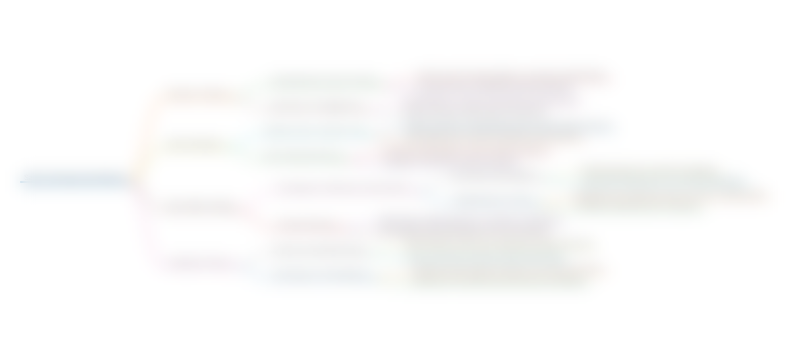
This section is available to paid users only. Please upgrade to access this part.
Upgrade NowKeywords
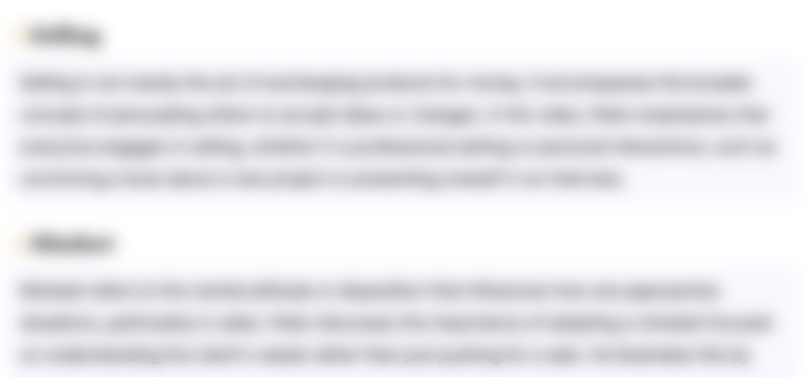
This section is available to paid users only. Please upgrade to access this part.
Upgrade NowHighlights
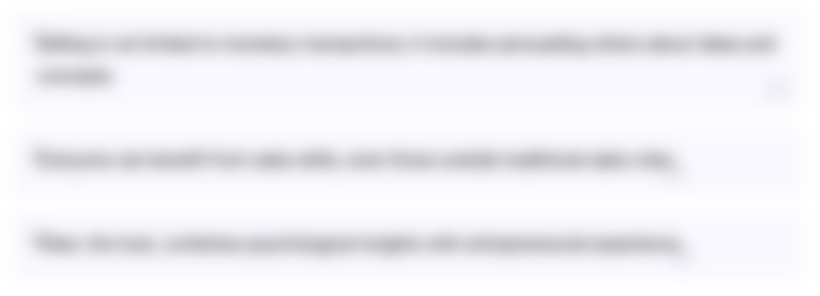
This section is available to paid users only. Please upgrade to access this part.
Upgrade NowTranscripts
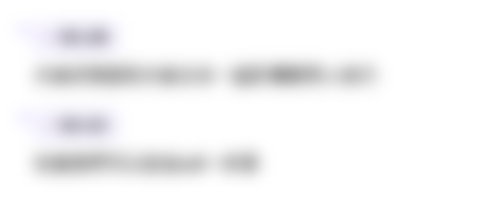
This section is available to paid users only. Please upgrade to access this part.
Upgrade NowBrowse More Related Video
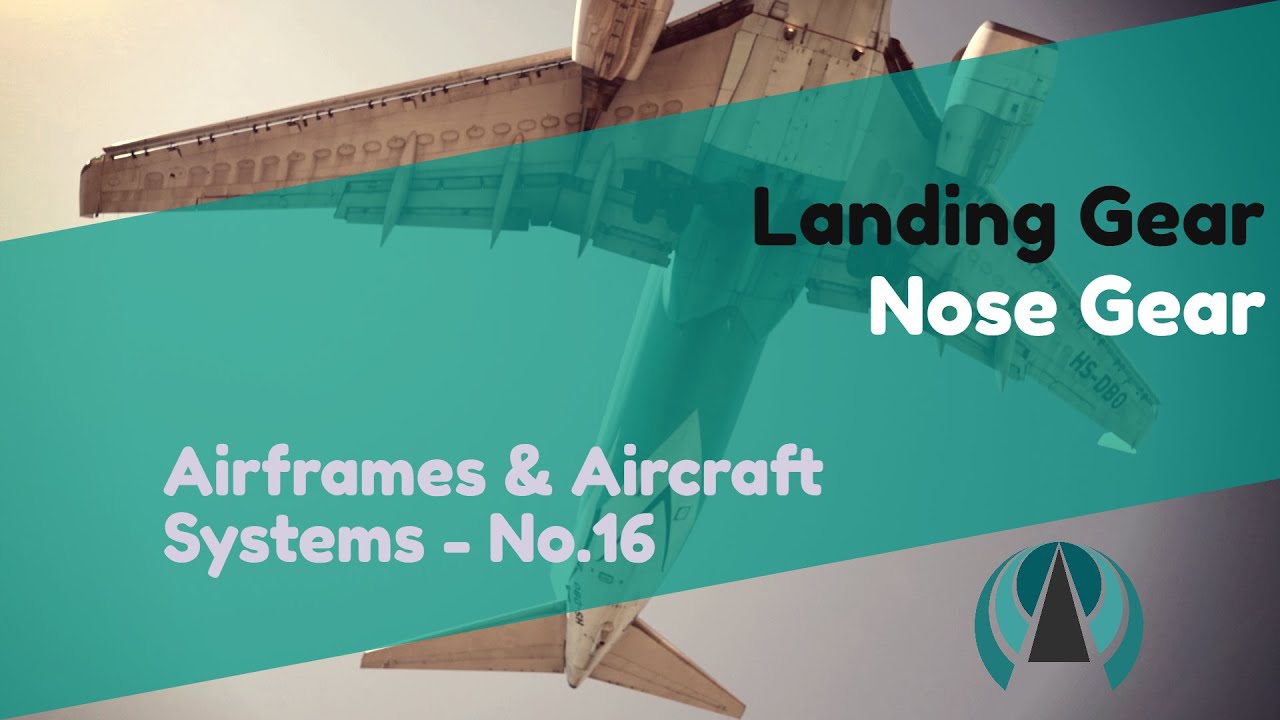
Nose Gear - Landing Gear - Airframes & Aircraft Systems #16
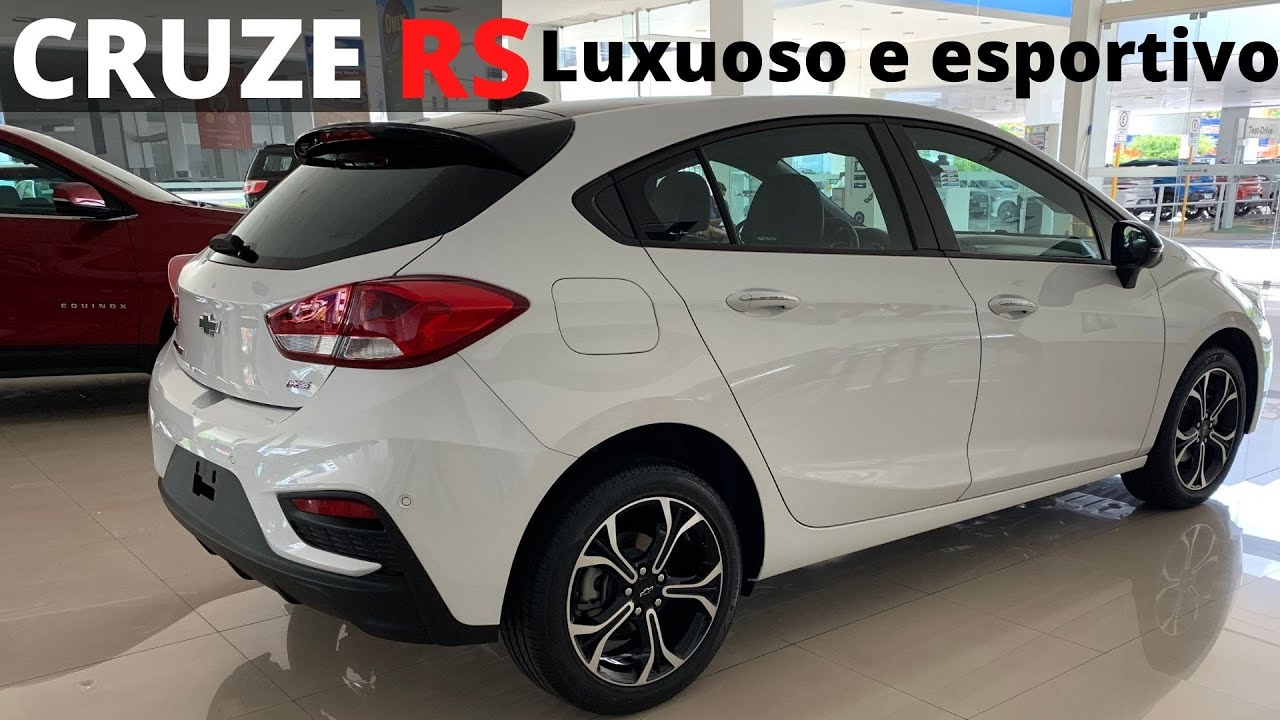
Cruze LTZ OU RS 2022 - O chevrolet mais injustiçado! Anda bem, consumo, detalhes, opiniao sincera.
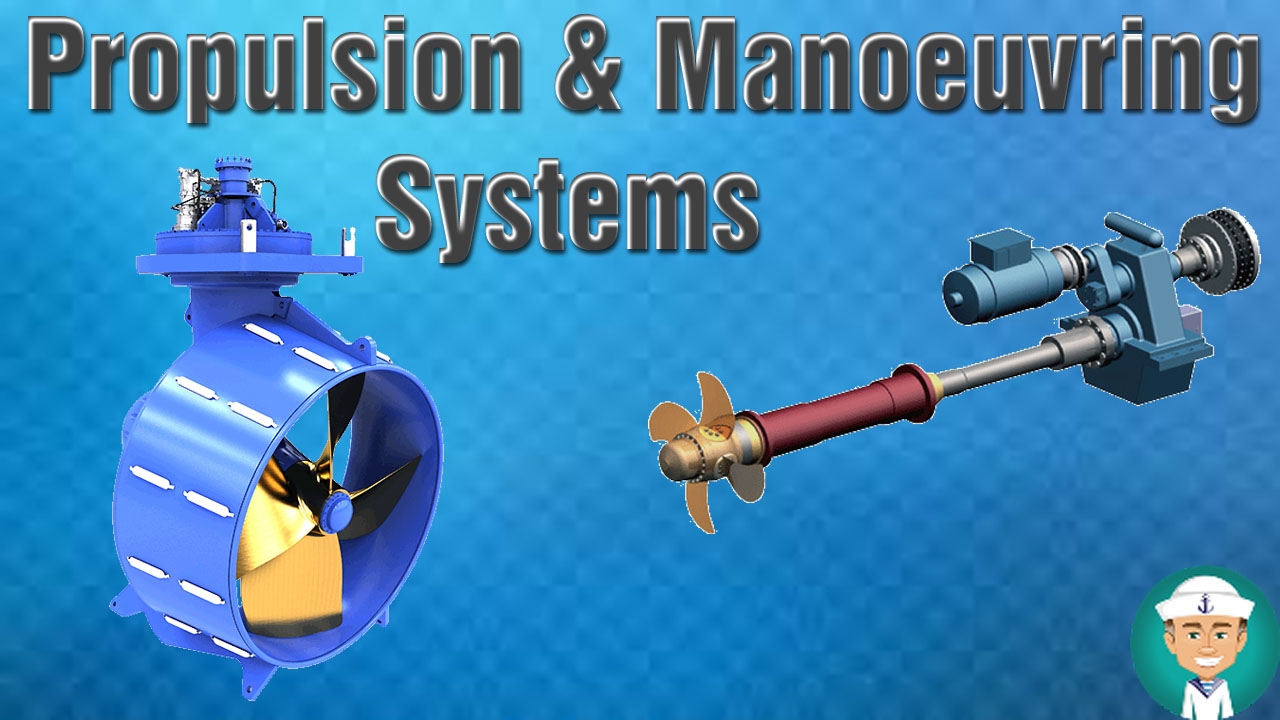
Propulsion And Manoeuvring Systems

ME396 2024 11 22 Advisor Review Video
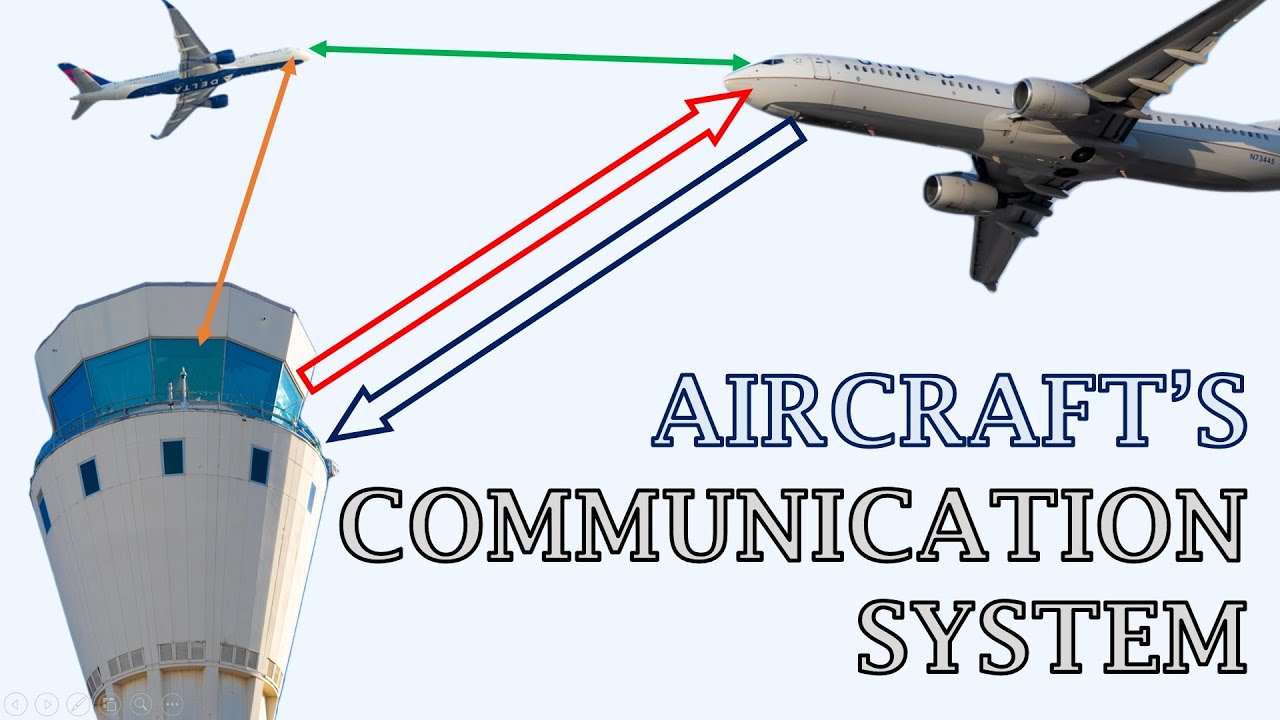
Understanding Aircraft's Communication System | ACARS | Voice & Data | Antennas on an Aircraft!

Taxiing Lesson 1
5.0 / 5 (0 votes)