EV Electrical Systems BASICS!
Summary
TLDRThe video explores the exciting shift towards electric vehicle (EV) electrification, emphasizing its impact on motorsports and performance cars. It breaks down the complexities of EV electrical systems into three main subsystems: high voltage, low voltage, and CAN networks. Key components like battery packs, inverters, and power distribution units are discussed, highlighting their roles in vehicle performance and safety. The integration of these systems enables enthusiasts to enjoy tailored driving experiences while ensuring safety through advanced monitoring and control features. Overall, the content offers an insightful overview of the technology driving the future of electric propulsion.
Takeaways
- 🚗 The shift toward vehicle electrification is opening new frontiers for high-performance propulsion in both motorsports and street vehicles.
- 🔋 Electric vehicle (EV) systems can be categorized into three main subsystems: high voltage, low voltage, and multiple CAN networks.
- ⚡ High voltage systems are powered by batteries typically exceeding 200 volts, which include components like contactors, inverters, and DC to DC converters.
- 🔌 An on-board charger converts grid AC power to high voltage DC power to charge the high voltage battery.
- 🏎️ Motors propel the vehicle and require an inverter to convert high voltage DC from the battery into regulated AC voltage.
- 🛠️ The AEM VCU (Vehicle Control Unit) plays a crucial role in managing power delivery and safety features during operation.
- 🔄 The low voltage circuit powers standard vehicle accessories and can be retained from internal combustion engine vehicles during conversion.
- 💡 Power Distribution Units (PDU8) simplify the control of low voltage systems by allowing centralized management through the VCU.
- 🌐 CAN bus networking facilitates communication between multiple devices, improving wiring efficiency and system integration.
- 🔒 Advanced safety features, including pre-checks and voltage regulation, enhance the reliability and enjoyment of EV conversions.
Q & A
What are the three main subsystems in electric vehicle (EV) electrical systems?
-The three main subsystems are the high voltage circuit, low voltage circuit, and multiple CAN networks.
What is the role of the high voltage battery in an EV?
-The high voltage battery, typically over 200 volts, supplies power to high voltage components like the motor, inverter combos, and the DC to DC converter.
How does an on-board charger function in an EV system?
-An on-board charger converts grid AC power to high voltage DC power to charge the high voltage battery.
What is a DC to DC converter and how does it work?
-A DC to DC converter acts like an alternator in internal combustion engine vehicles, converting high voltage power to maintain the charge of the low voltage battery.
How are motor inverters used in electric vehicles?
-Motor inverters convert high voltage DC power from the battery to regulated AC voltage for motor propulsion, and each motor requires its own inverter.
What advantages do EV conversions have regarding low voltage systems?
-EV conversions can retain the existing low voltage systems from internal combustion engine vehicles, making the transition easier.
What is the function of the PDU8 power distribution unit?
-The PDU8 power distribution unit allows for the control of 12-volt switch devices through the VCU, simplifying wiring and programming.
What is CAN bus networking and why is it beneficial in EV systems?
-CAN bus networking allows multiple devices to share data over a two-wire network, simplifying wiring and enhancing communication between components.
How does the VCU improve performance and safety in EV conversions?
-The VCU integrates multiple systems, receiving data from various devices to ensure optimal performance and safety through pre-checks and real-time monitoring.
What safety features are incorporated into the EV conversion systems?
-Safety features include redundant pre-checks before startup, voltage regulation based on battery temperatures, and checks on pedal sensor voltages to prevent failures.
Outlines
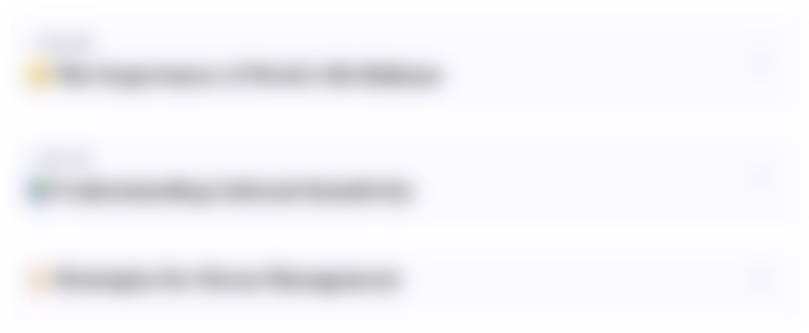
This section is available to paid users only. Please upgrade to access this part.
Upgrade NowMindmap
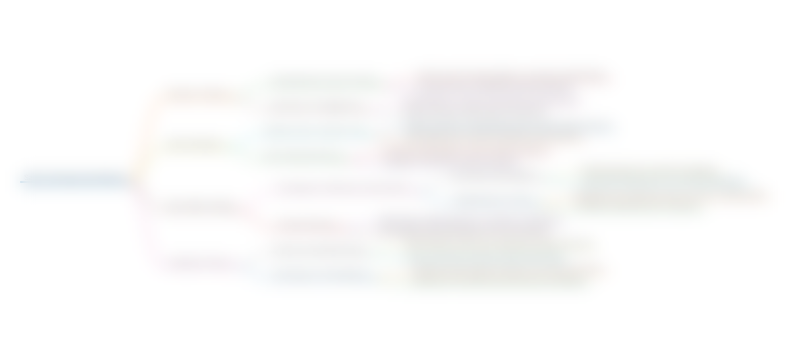
This section is available to paid users only. Please upgrade to access this part.
Upgrade NowKeywords
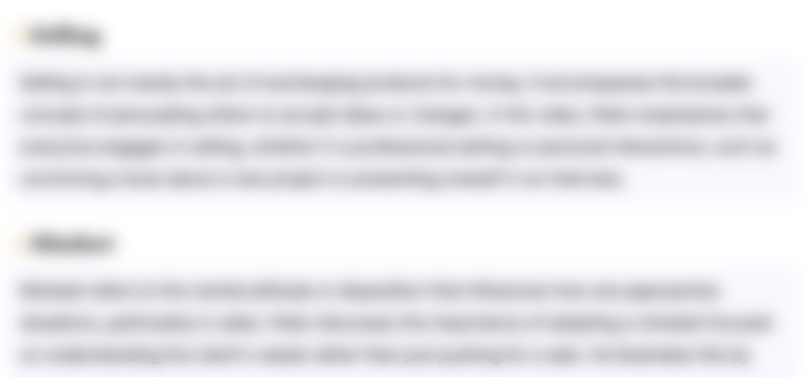
This section is available to paid users only. Please upgrade to access this part.
Upgrade NowHighlights
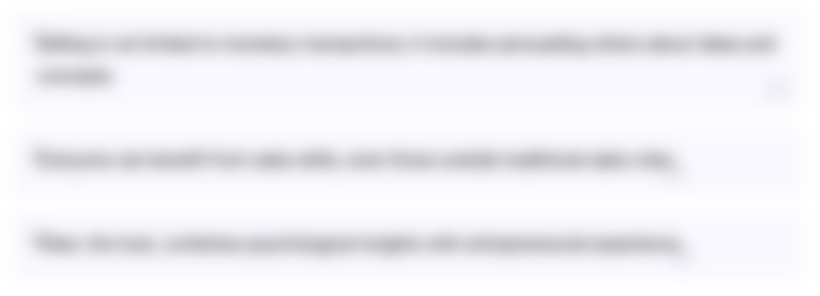
This section is available to paid users only. Please upgrade to access this part.
Upgrade NowTranscripts
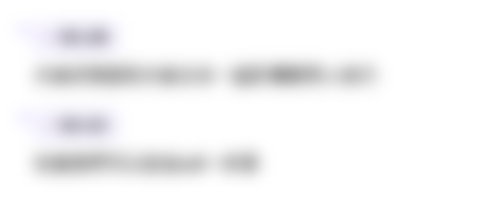
This section is available to paid users only. Please upgrade to access this part.
Upgrade NowBrowse More Related Video

Dinamika Industri Mobil Listrik Global || Klinik Otomotif Sonora
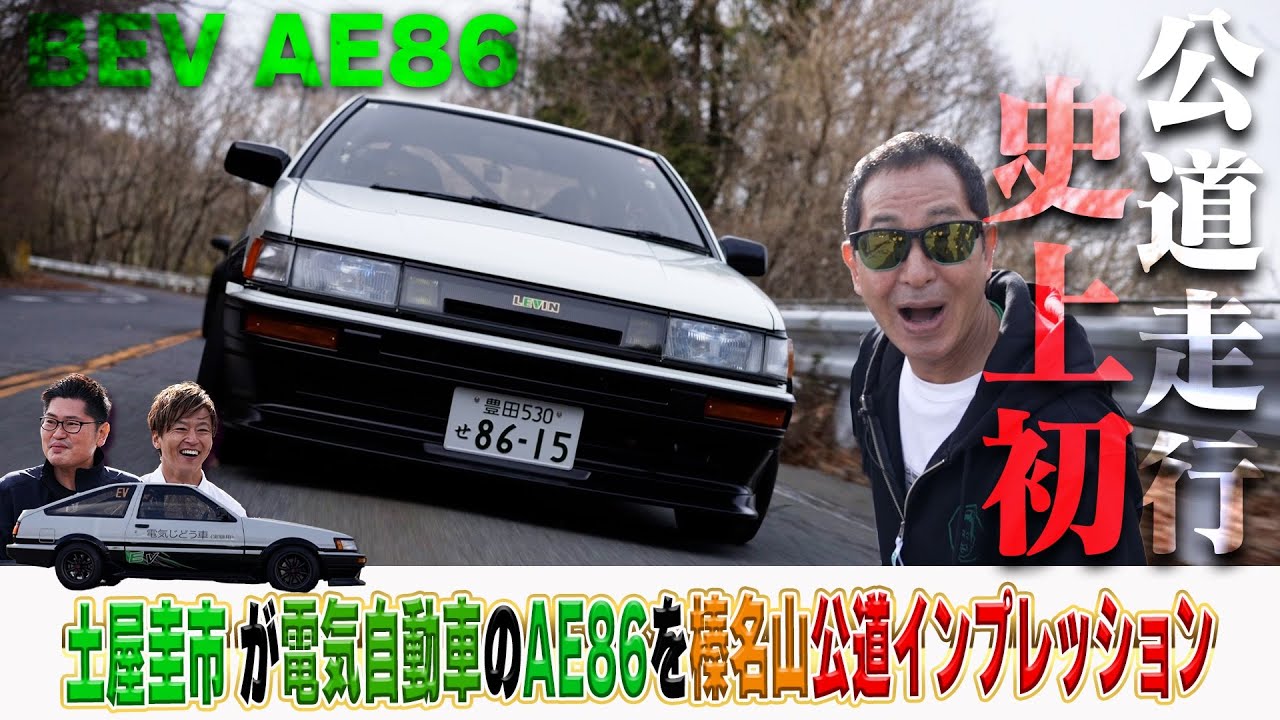
電気自動車に生まれ変わったAE86を土屋圭市が榛名山で史上初インプレッション!【テリー土屋のくるまの話】

Is it time to scrap electric cars? With Rory Sutherland | SpectatorTV

도대체 뭘 했기에? G80 NVH가 이럼?

Para saber cómo es el futuro del coche eléctrico solo hay que mirar a Noruega

QUAL A HORA CERTA PARA COMPRAR UM CARRO ELÉTRICO? - ADG (HIGH TORQUE) - TUNERCAST
5.0 / 5 (0 votes)