FMEA Part-1: Planning and Preparing for DFMEA
Summary
TLDRThis video from the Institute of Quality and Reliability is divided into three parts, focusing on Design Failure Mode and Effects Analysis (DFMEA). Part 1 covers the history of FMEA, its applications, and the planning process. It explains who should conduct DFMEA and outlines important tools such as block diagrams, boundary diagrams, and interface matrices. The video also introduces a seven-step DFMEA process to assess risk and prevent potential failures before they impact customers. Viewers can expect insights on practical DFMEA techniques used across industries.
Takeaways
- 📜 Failure Mode and Effects Analysis (FMEA) was first used in the 1960s in the aerospace industry during Apollo missions, later adopted by the automotive industry in the 1970s.
- 🛠 FMEA is an engineering technique to identify and eliminate known or potential failures from design, processes, or services before they reach the customer.
- 🧑🤝🧑 FMEA is a cross-functional team activity, involving design engineers, quality engineers, service engineers, and sometimes suppliers and customers.
- ⚖️ FMEA assesses risks by analyzing potential failure modes, their causes, and the severity of their effects. It assigns rankings for severity, occurrence probability, and detection likelihood.
- 🔢 The Risk Priority Number (RPN) is calculated by multiplying the rankings for severity, occurrence, and detection (scored between 1 and 10).
- 📋 Design FMEA (DFMEA) is structured into seven steps: planning and preparation, structure analysis, function analysis, failure analysis, risk analysis, optimization, and risk communication/action plans.
- 📊 Tools like Quality Function Deployment (QFD), block diagrams, boundary diagrams, interface matrices, and parameter diagrams are recommended for DFMEA planning.
- 💻 Block diagrams visually represent relationships between system components, such as a central processing unit connected to a hard disk and display in a computer.
- 📈 Boundary diagrams break FMEA into manageable levels, showing subsystems, assemblies, and components in relation to neighboring systems and environments.
- 🔗 Interface Matrices and Parameter Diagrams illustrate interactions between subsystems and categorize factors such as control, noise, signal, and response.
Q & A
What is the purpose of the video series on FMEA?
-The video series aims to explain the Failure Mode and Effects Analysis (FMEA) process, specifically focusing on Design FMEA (DFMEA) in three parts: planning and preparation, using the DFMEA form and ranking guidelines, and DFMEA application case studies.
What is FMEA, and how is it defined?
-FMEA is an engineering technique used to identify and eliminate known or potential failures, problems, and errors in system design, processes, or services before they reach the customer. It is a risk assessment technique performed in a cross-functional team setting.
What industries were early adopters of FMEA, and how did it evolve?
-FMEA was first used in the 1960s by the aerospace industry during the Apollo missions. In 1974, the U.S. Navy developed the military standard MIL-1629, which included Failure Mode, Effects, and Criticality Analysis (FMECA). In the late 1970s, the U.S. automotive industry standardized its use.
Who typically conducts a Design FMEA (DFMEA)?
-DFMEA is conducted by a cross-functional team, including design engineers, design analysts, quality engineers, service engineers, suppliers, and sometimes customer representatives. The success of DFMEA depends on collective knowledge and participation.
What are the key steps in the Design FMEA (DFMEA) process?
-The DFMEA process involves seven key steps: planning and preparation, structure analysis, function analysis, failure analysis, risk analysis, optimization (failure analysis and risk mitigation), and risk communication with action plans.
What is Risk Priority Number (RPN) in FMEA?
-RPN is a numerical value obtained by multiplying three factors: severity, occurrence probability, and detection probability of a failure. Each factor is rated between 1 and 10, and the RPN helps prioritize risks in the design process.
What tools are recommended for preparing for Design FMEA?
-Several tools are recommended, including Quality Function Deployment (QFD), block diagrams, boundary diagrams, interface matrices, and parameter diagrams. These tools help visualize relationships, subsystems, and potential failure points.
What is a boundary diagram in FMEA?
-A boundary diagram is a graphical illustration that shows the relationships between subsystems, assemblies, and components of an object, as well as their interfaces with neighboring systems and environments. It helps break down complex systems for FMEA analysis.
What is an interface matrix, and how is it used in FMEA?
-An interface matrix is a tool used to illustrate relationships between subsystems, assemblies, and components. It helps evaluate physical, energy, information, and material exchanges, assigning ratings to interactions based on their impact on functionality.
What is the purpose of the parameter diagram in FMEA?
-A parameter diagram helps categorize and map various factors in a system, such as control factors, noise factors, signal factors, and response factors. It is often used to ensure robustness in the design and FMEA process.
Outlines
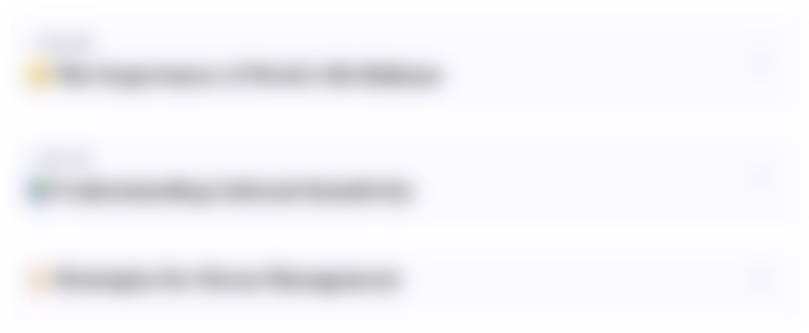
This section is available to paid users only. Please upgrade to access this part.
Upgrade NowMindmap
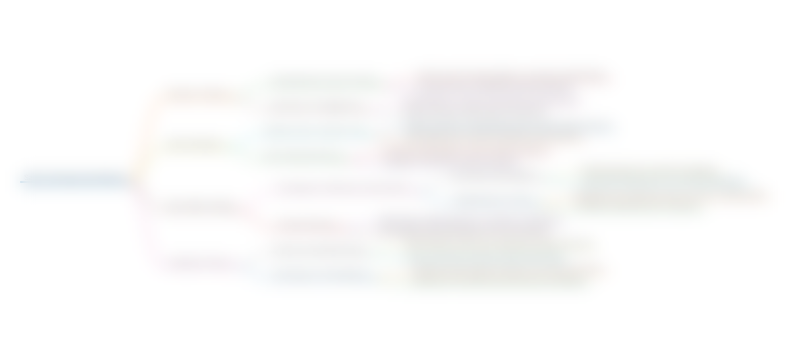
This section is available to paid users only. Please upgrade to access this part.
Upgrade NowKeywords
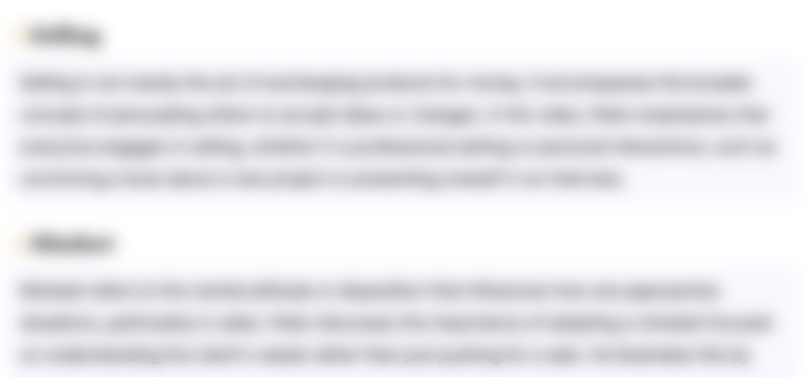
This section is available to paid users only. Please upgrade to access this part.
Upgrade NowHighlights
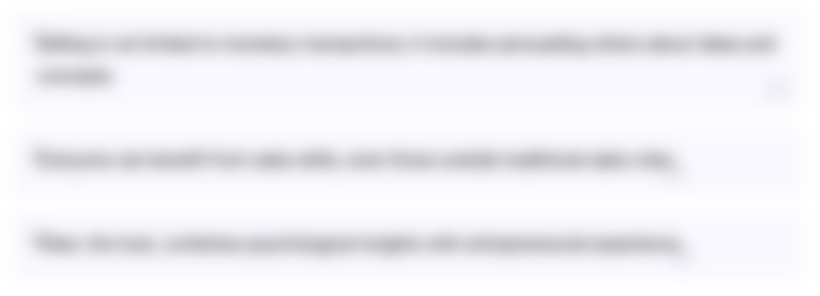
This section is available to paid users only. Please upgrade to access this part.
Upgrade NowTranscripts
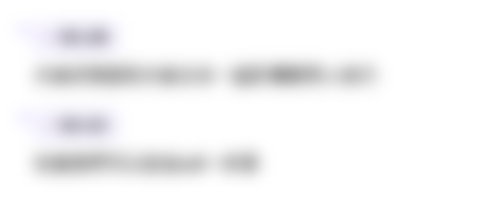
This section is available to paid users only. Please upgrade to access this part.
Upgrade NowBrowse More Related Video
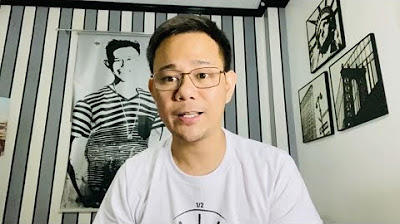
CBME 1 | Lesson 2 | Part 1/3
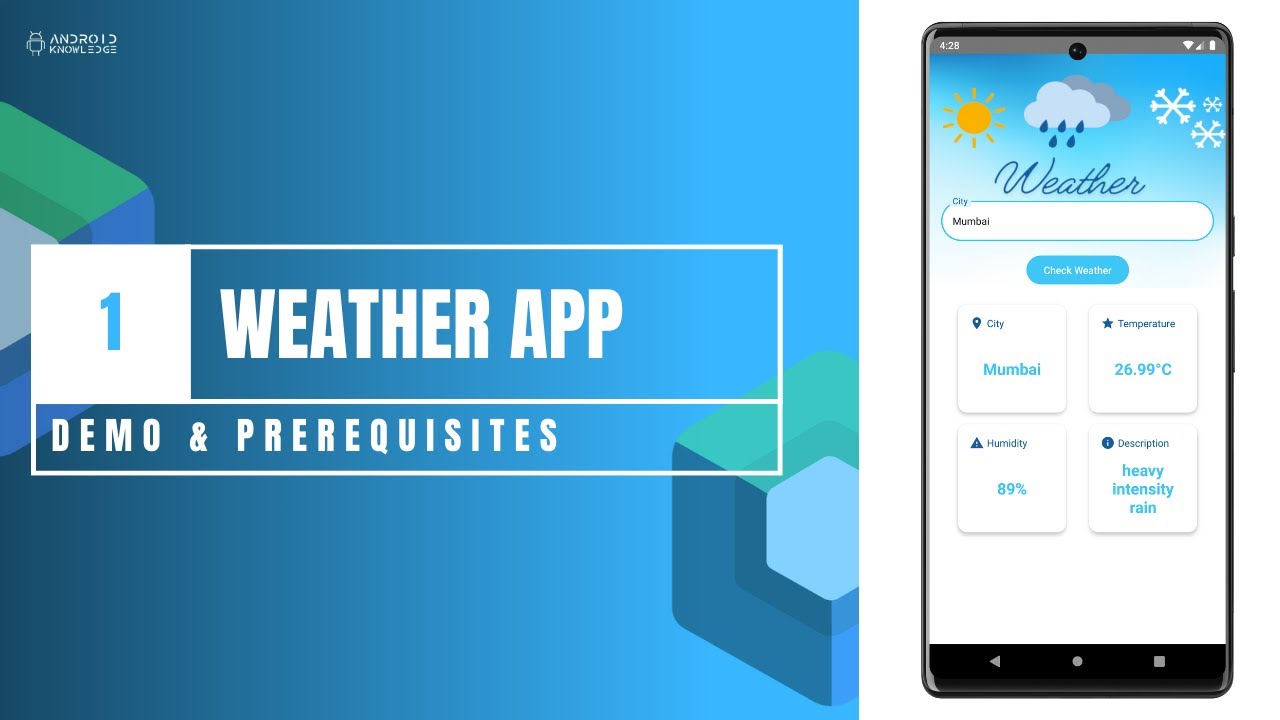
The Weather App in Jetpack Compose using Kotlin | Part 1: Prerequisites | Android Knowledge
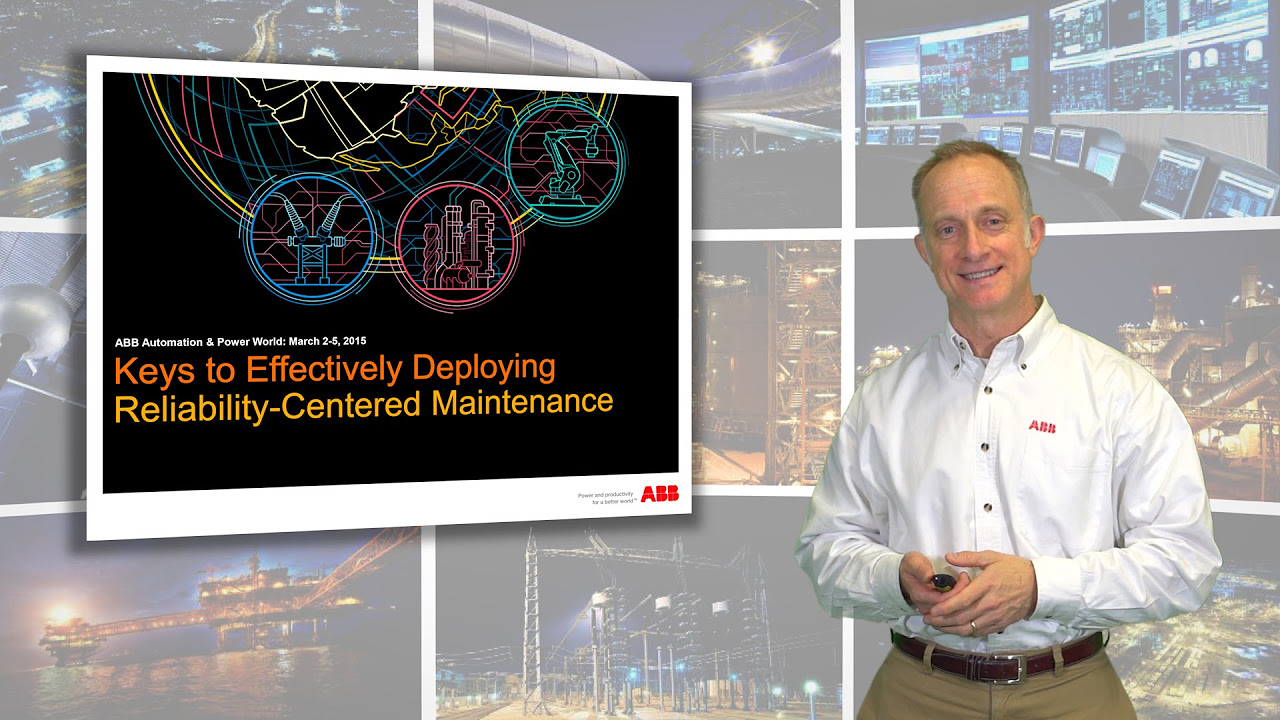
ABB - Reliability-Centered Maintenance

External and Internal Criticism: Readings in Philippine History

Application of Risk Management Principles for Medical Devices
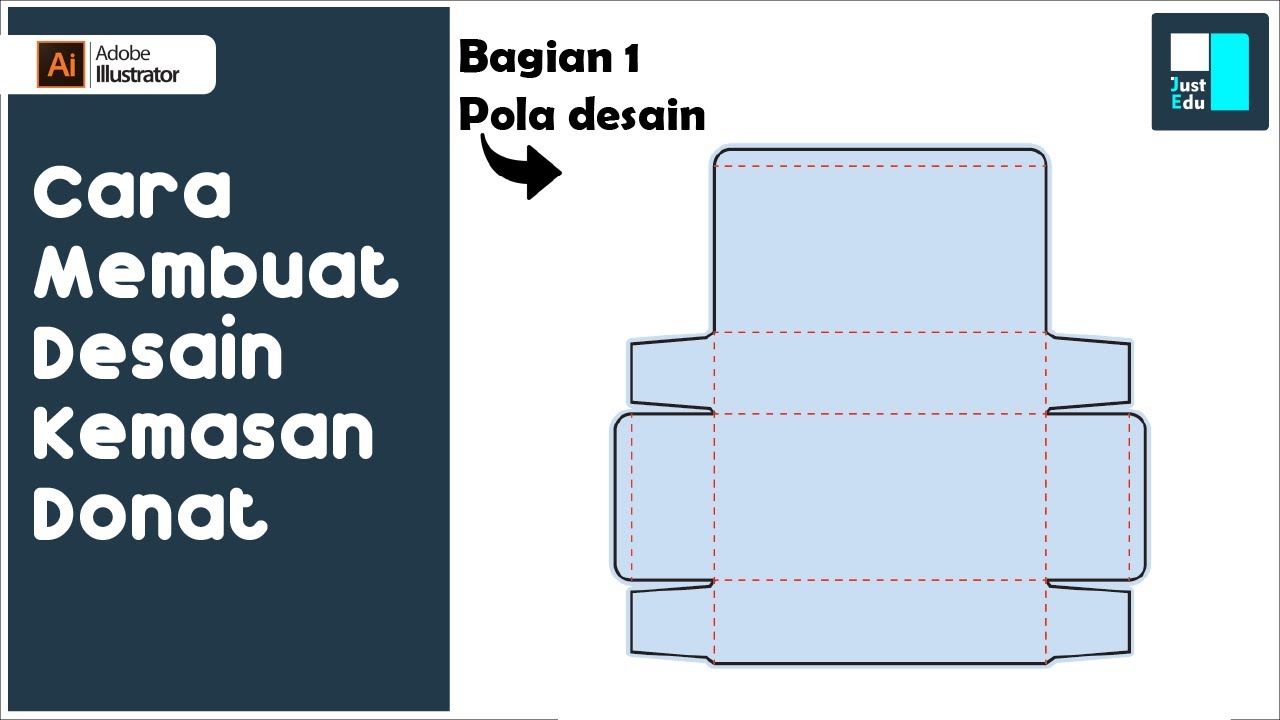
Cara Membuat Desain Kemasan Box - bagian 1
5.0 / 5 (0 votes)