How It's Made Metal Plating
Summary
TLDRThe video explains the process of metal plating, particularly focusing on cadmium plating for corrosion-resistant aerospace parts. The process involves cleaning steel parts to remove contaminants, roughening their surface with abrasive blasting, and using electroplating to bond cadmium to the steel. An electric current causes cadmium particles to form a smooth, even layer on the parts. Additional chemical treatments enhance corrosion resistance, though they can alter the color. The entire process takes about 90 minutes, and similar methods apply for plating with other metals like chrome and gold.
Takeaways
- ๐ฉ Plating is the process of applying a metal coating to an object made of a different metal, often for decorative or practical purposes.
- ๐ก Industrial plating, such as zinc or cadmium plating, prevents rusting and adds corrosion resistance, while nickel or chrome plating protects against wear.
- ๐ To prepare steel parts for plating, contaminants like oil and grease must be removed using boiling chemical solvents.
- โ๏ธ The parts are also sandblasted with aluminum oxide powder to roughen the surface for better adhesion of the plating metal.
- ๐ Electroplating relies on electricity to deposit a layer of metal onto the parts. Common plating metals include zinc, chrome, and nickel for industrial purposes, and tin, brass, gold, or silver for decorative items.
- ๐ฆ The steel parts are suspended in an electroplating tank where electricity dissolves the plating metal and transfers it onto the negatively charged parts.
- โก A steady DC current (6 volts) is used during electroplating, causing positively charged cadmium particles to adhere to the steel, forming a smooth, even layer.
- ๐งช After electroplating, the parts are rinsed and sometimes treated with chemical compounds to enhance their corrosion resistance.
- ๐จ Some metals like chrome and gold require special chemical compounds for plating since electricity alone can't dissolve them properly.
- โณ The plating process varies in time depending on the thickness required, and if subjected to wear and tear, the plating may need to be redone.
Q & A
What is metal plating?
-Metal plating is the process of applying a layer of metal onto the surface of an object made of a different metal. This can be done for decorative purposes or to improve the objectโs resistance to corrosion, wear, and other types of damage.
What are some common metals used in industrial plating?
-Some common metals used in industrial plating include zinc, cadmium, nickel, and chrome. These metals are often used because they enhance corrosion resistance and durability in various parts, such as aerospace components.
Why is the steel surface cleaned before plating?
-The steel surface is cleaned before plating to remove contaminants like oil and grease. This ensures that the plating metal can properly bond to the surface, resulting in a more effective and durable coating.
How is the steel cleaned before plating in this process?
-The steel is cleaned by suspending it over a vat of boiling chemical solvents. The hot vapor condenses on the metal, removing contaminants, and then evaporates, leaving the steel clean and dry.
Why is sandblasting used in the plating process?
-Sandblasting is used to roughen the surface of the metal, which helps the plating metal adhere better. The abrasive action of the aluminum oxide powder creates a textured surface that allows for a stronger bond.
What is electroplating, and why is it called that?
-Electroplating is the process of using an electric current to coat a metal object with a layer of another metal. It's called electroplating because electricity is essential to the process, driving the chemical reactions that deposit the plating metal onto the object.
How does the electric current work in the electroplating process?
-In the electroplating process, a DC electric current is used. The metal object being plated is connected to the negative terminal, while the plating metal is connected to the positive terminal. This causes the positively charged particles of the plating metal to move toward and bond with the negatively charged object.
What is the role of the chemical compounds added to the water in the electroplating tank?
-The chemical compounds are added to the water to improve its ability to conduct electricity. Without these chemicals, the water would not be able to carry the electric current efficiently enough for the electroplating process to work.
What happens to the color of the plated parts after the additional corrosion-resistant treatment?
-The color of the plated parts may change after the corrosion-resistant treatment. This happens due to a chemical reaction that enhances the metal's ability to resist corrosion but also alters its appearance.
Why is a chemical compound required for plating with gold or chromium?
-A chemical compound is required for plating with gold or chromium because electricity alone cannot dissolve these solid metals well enough. The compound dissolves in the plating bath and then solidifies on the object's surface during the process.
Outlines
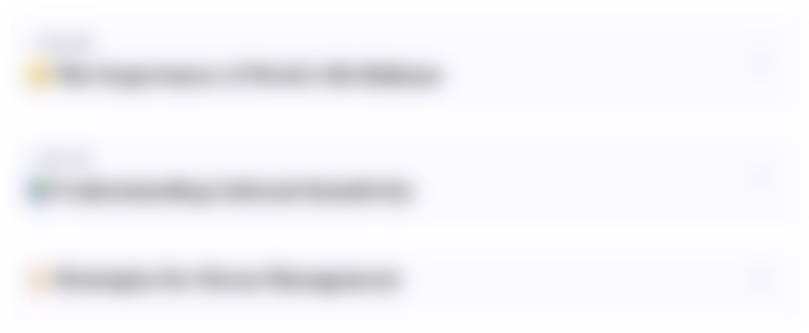
This section is available to paid users only. Please upgrade to access this part.
Upgrade NowMindmap
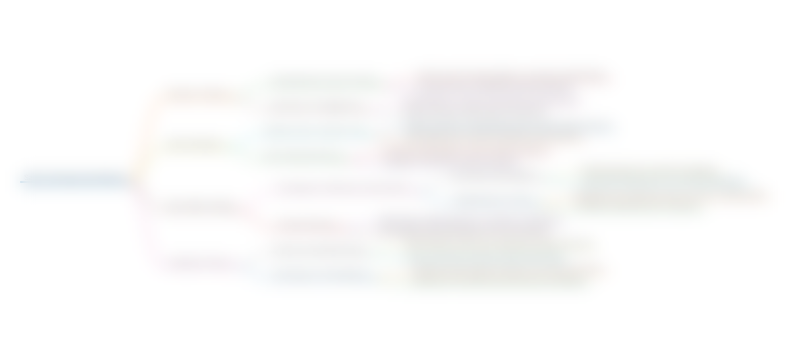
This section is available to paid users only. Please upgrade to access this part.
Upgrade NowKeywords
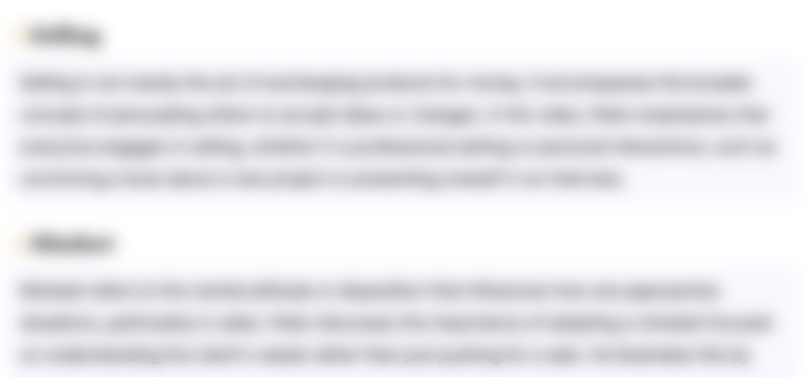
This section is available to paid users only. Please upgrade to access this part.
Upgrade NowHighlights
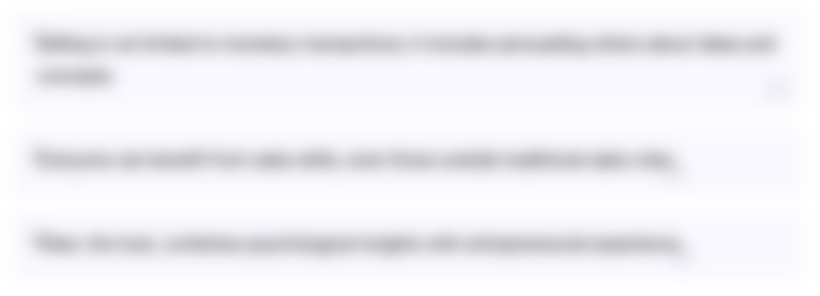
This section is available to paid users only. Please upgrade to access this part.
Upgrade NowTranscripts
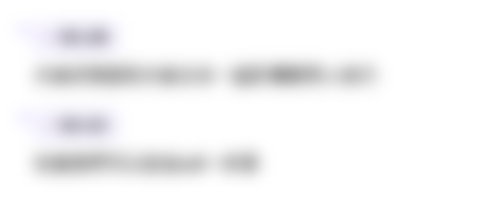
This section is available to paid users only. Please upgrade to access this part.
Upgrade NowBrowse More Related Video
5.0 / 5 (0 votes)