The Seven Tools of Total Quality Management (TQM)
Summary
TLDRThis video script discusses the seven quality control tools used in Total Quality Management, applicable across various fields like operations and supply chain management. The tools are categorized into idea generation (check sheets, scatter diagrams, cause and effect diagrams), data organization (Pareto charts, flow charts), and problem identification (histograms, control charts). Each tool's application is explained with examples, highlighting their utility in identifying areas for improvement and managing quality effectively.
Takeaways
- ๐ The seven quality control tools are essential for quality management and can be applied across various areas such as operations and supply chain management.
- ๐ These tools are categorized into three subgroups: tools for generating ideas, organizing data, and identifying problems.
- ๐ Tools for generating ideas include check sheets, scatter diagrams, and cause-and-effect (fishbone) diagrams, which help to brainstorm and identify areas for focus.
- ๐ Tools for organizing data, like Pareto charts and flow charts, help make sense of collected data and guide problem-solving efforts.
- ๐ Tools for identifying problems, such as histograms and statistical process control charts, assist in tracking data trends and identifying issues in a process.
- โ๏ธ A check sheet is a simple tool used for recording and categorizing data to identify where potential problems might occur.
- ๐ฏ A cause-and-effect diagram (fishbone diagram) is used to find potential causes for a problem, organizing possible causes into categories such as materials, methods, manpower, or machines.
- ๐ A Pareto chart is a tool that organizes data to highlight the most frequent problems or defects, often revealing that a small number of causes result in the majority of issues.
- ๐ Histograms show an empirical frequency distribution of events, helping to visualize the spread of data over time or across occurrences.
- โ๏ธ Control charts help to monitor process control, using upper and lower control limits to determine whether a process is operating within acceptable parameters.
Q & A
What are the three main subcategories of the seven quality control tools?
-The three subcategories are: tools for generating ideas, tools to organize data, and tools to identify problems.
Which tools fall under the category of 'generating ideas'?
-The tools for generating ideas include check sheets, scatter diagrams, and cause and effect (fishbone) diagrams.
How does a check sheet help in quality control?
-A check sheet helps in organizing and collecting data. It provides a simple method for problem identification by tallying issues based on categories, allowing teams to see where problems are occurring most frequently.
What is the purpose of a scatter diagram?
-A scatter diagram shows the degree and direction of the relationship between two variables. It helps determine whether two variables are correlated.
What is another name for a cause and effect diagram, and what is its purpose?
-A cause and effect diagram is also known as a fishbone diagram. Its purpose is to organize the search for the causes of a problem, focusing on areas like materials, methods, manpower, or machines.
What is a Pareto chart and how is it used?
-A Pareto chart is a graph that identifies and plots problems or defects in descending order of frequency. It follows the 80/20 rule, showing that 80% of problems typically come from 20% of causes.
How does a flowchart help in quality control?
-A flowchart is a visual representation of a process. It helps to outline the steps involved in a process, identify decision points, and locate potential errors or non-value-added steps.
What does a histogram represent in quality management?
-A histogram is a chart that shows an empirical frequency distribution. It is used to display the frequency of occurrences of certain events, such as repair times or defect rates, helping to identify patterns in data.
What is a control chart and how is it used?
-A control chart is a type of run chart that includes upper and lower control limits, helping to determine whether a process is in control or out of control. It can be used to monitor various factors such as time, temperature, or weight in a process.
How can the seven quality control tools benefit areas outside of quality management?
-The seven quality control tools can be applied to various areas such as operations management, supply chain management, and problem-solving in general. They help in organizing data, identifying root causes of issues, and improving processes in a variety of contexts.
Outlines
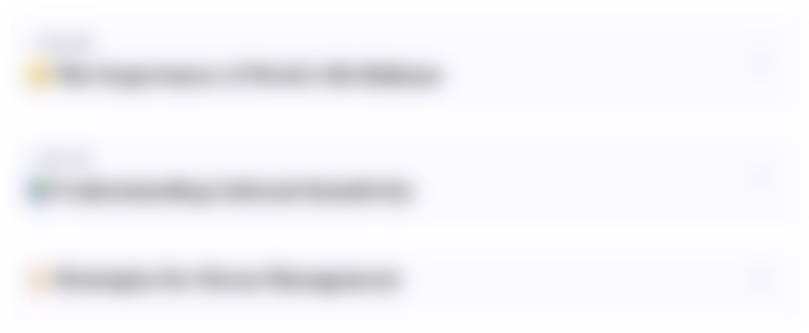
This section is available to paid users only. Please upgrade to access this part.
Upgrade NowMindmap
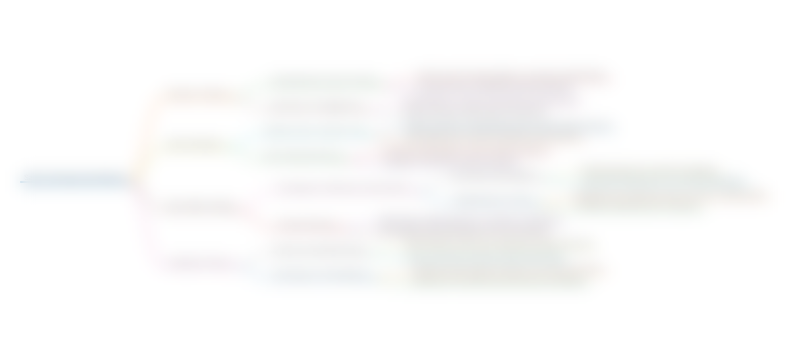
This section is available to paid users only. Please upgrade to access this part.
Upgrade NowKeywords
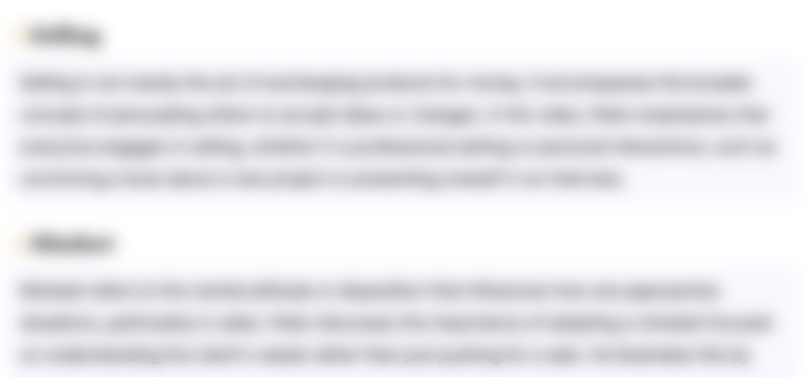
This section is available to paid users only. Please upgrade to access this part.
Upgrade NowHighlights
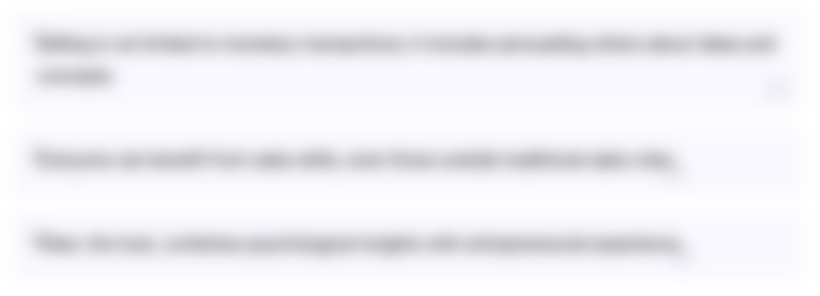
This section is available to paid users only. Please upgrade to access this part.
Upgrade NowTranscripts
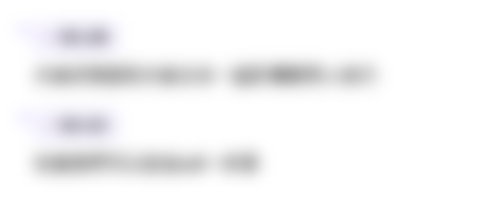
This section is available to paid users only. Please upgrade to access this part.
Upgrade NowBrowse More Related Video
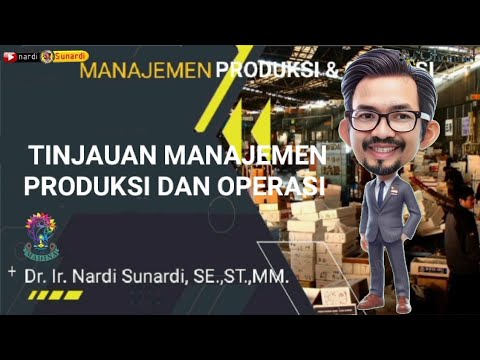
Bab 1 Tinjauan Manajemen Produksi dan Operasi

SQC

3 Kunci Sukses Bisnis Kuliner, Belajar Dari Menantea, Kopken, dll
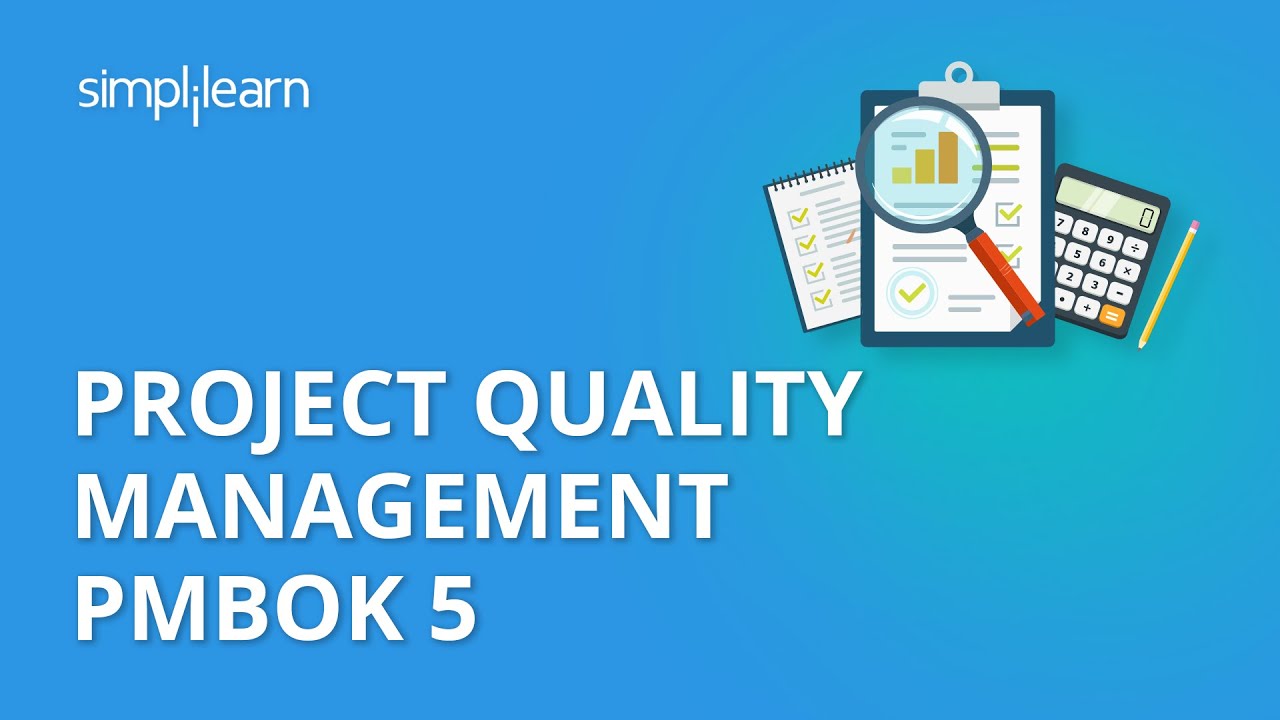
Project Quality Management PMBOK 5 | PMPยฎ Training Videos | Project Management Tutorial |Simplilearn
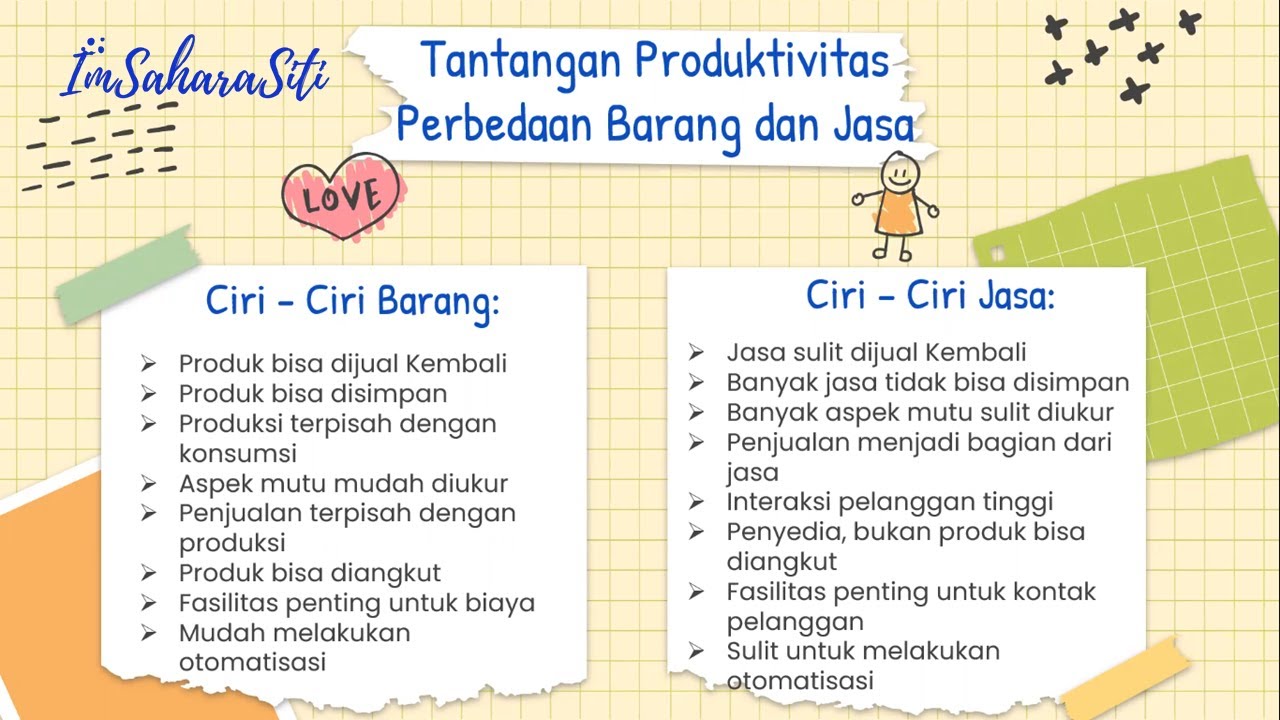
Video Pembelajaran Pengantar Manajemen _ Manajemen Operasional

Supply Chain Management PT. Garudafood Putra Putri Jaya - Kelompok 5
5.0 / 5 (0 votes)