Pneumatic Drill How2
Summary
TLDRThe script provides a detailed tutorial on safely operating a pneumatic drill. It emphasizes starting with a disconnected tool, inspecting the tool and bit for damage, and checking the air hose for kinks. The importance of wearing proper PPE is highlighted, and the process of selecting and installing the bit is outlined. The script also covers starting a hole in metal by creating a dimple and the technique for drilling through metal without damaging the work surface. Finally, it advises on disconnecting the air supply for maintenance and cleaning the tool to prevent damage from dust and dirt.
Takeaways
- π Always start with a disconnected pneumatic drill to ensure safety.
- π Inspect the tool, housing, and bit before use to ensure they are in good condition.
- π¬οΈ Check the air hose for any damage or kinks, ensuring it's in good working order.
- π© The collet at the end of the air hose needs to articulate freely for proper connection.
- π·ββοΈ Use proper Personal Protective Equipment (PPE), including hearing protection if necessary.
- π© Select the appropriate bit for the material you're drilling, such as metal.
- π¨ Securely install the bit by tightening the chuck as much as possible to prevent bit wandering.
- π Make a mark on the metal where you want to drill to guide the drill bit.
- π¨ Use a nail set to create a dimple in the metal to help guide the drill bit and prevent bit wandering.
- π Connect the air hose correctly, ensuring a secure fit with the collet and ball bearings.
- π§ Select reverse drilling mode for starting the hole, and ensure the drill is set to forward only for drilling through.
- βοΈ Use caution when drilling through metal to avoid damaging the work surface, like using a support under the metal.
- β Disconnect the air supply before performing any maintenance or changing bits.
- π§Ό Keep the tool clean and dry, especially the air intake and exhaust, to prevent damage from dust and dirt.
- βοΈ Regularly check the sharpness of the bit and ensure it's not warped to maintain drilling efficiency.
Q & A
What is the Greek word for 'air' that the pneumatic drill's name, Numa, is derived from?
-The Greek word for 'air' is 'pneuma', which is the origin of the name Numa for the pneumatic drill.
Why is it important to start with a disconnected pneumatic drill?
-Starting with a disconnected pneumatic drill is important for safety reasons, allowing for inspection and setup without the risk of accidental operation.
What should be checked before using a pneumatic drill?
-Before using a pneumatic drill, one should check the housing for damage, ensure the bit is not warped, twisted, or too dull, and inspect the air hose for any kinks or damage.
Why is it necessary to check the collet at the end of the air hose?
-The collet at the end of the air hose must be checked to ensure it can articulate and release properly for connection, which is crucial for the proper functioning of the pneumatic drill.
What type of personal protective equipment (PPE) is mentioned in the script for using a pneumatic drill?
-The script mentions the use of PPE including hearing protection, although it acknowledges it's a personal choice due to the tool's noise level.
How does one select and install the bit for the pneumatic drill?
-To select and install the bit, one should hold the bottom part of the chuck and twist the top part to lock it down as tightly as possible to prevent it from straying during operation.
Why is it helpful to create a dimple before drilling into metal with a pneumatic drill?
-Creating a dimple before drilling into metal helps to prevent the bit from walking off the intended spot, ensuring accurate drilling.
What is the purpose of having a two-by-four under the metal piece when drilling?
-A two-by-four is placed under the metal piece to protect the worktable from damage when the drill bit goes through the metal.
How should one disconnect the air supply when finished using the pneumatic drill?
-To disconnect the air supply, one should first ensure the drill is not in operation, then disconnect the air hose to remove the power source, similar to disconnecting any power tool for maintenance or bit changes.
Why is it important to keep the pneumatic drill clean and dry?
-Keeping the pneumatic drill clean and dry is important to prevent dust and dirt from entering the tool and causing damage, as dirt is an enemy to the tool's longevity and performance.
What maintenance checks should be performed on the pneumatic drill after use?
-After use, one should check the air intake and exhaust for blockages, ensure the bit is not warped, and check the sharpness of the bit's edge.
Outlines
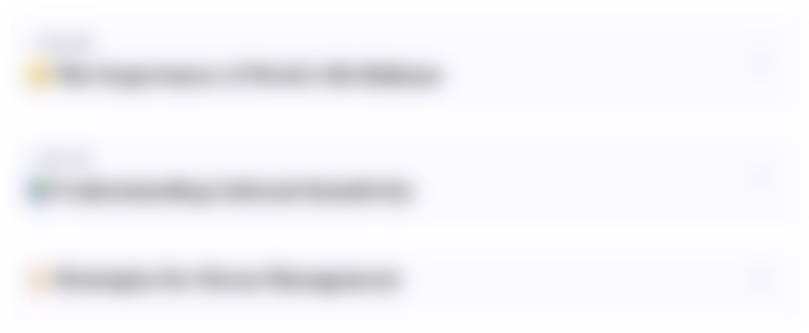
This section is available to paid users only. Please upgrade to access this part.
Upgrade NowMindmap
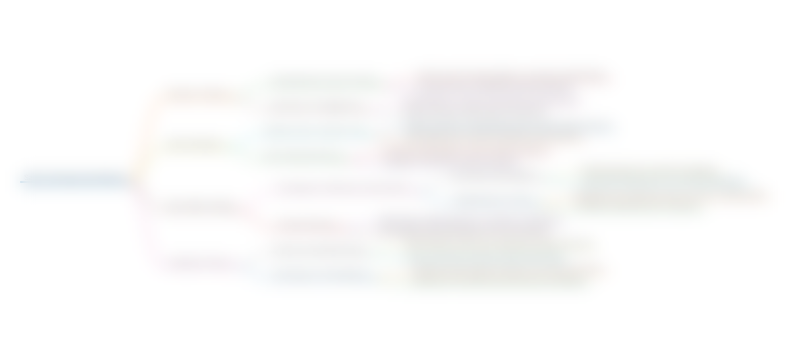
This section is available to paid users only. Please upgrade to access this part.
Upgrade NowKeywords
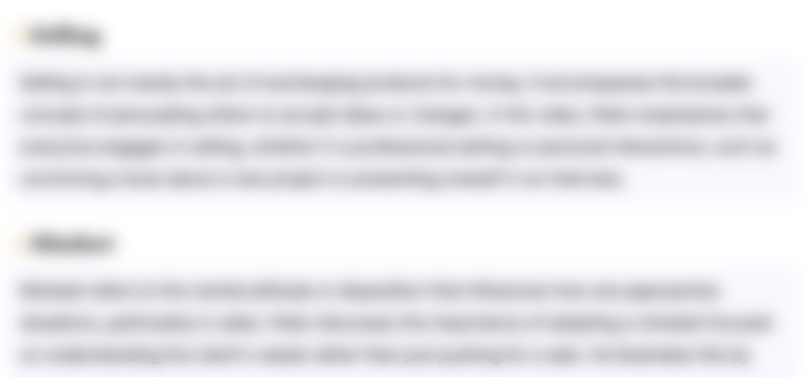
This section is available to paid users only. Please upgrade to access this part.
Upgrade NowHighlights
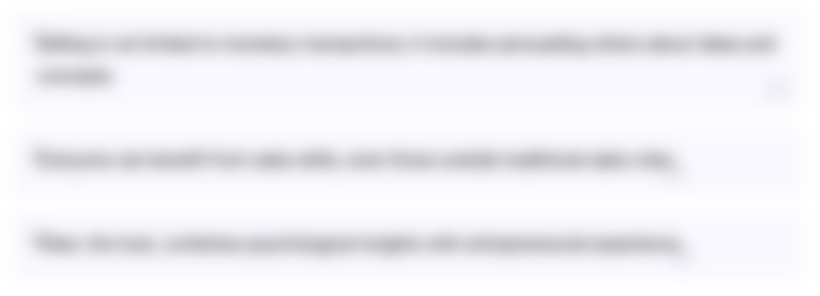
This section is available to paid users only. Please upgrade to access this part.
Upgrade NowTranscripts
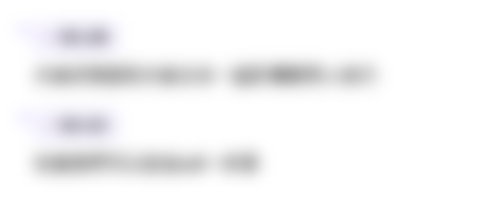
This section is available to paid users only. Please upgrade to access this part.
Upgrade Now5.0 / 5 (0 votes)