Understanding Metals
Summary
TLDRThis video explores the fundamentals of engineering materials, focusing on metals and their properties. It discusses microstructures, alloying, and heat treatment techniques used to enhance metal performance. Key metals like iron, aluminum, and titanium are highlighted for their engineering applications. The video delves into crystal structures, dislocations, grain boundaries, and strengthening techniques such as work hardening and grain boundary strengthening. Additionally, it covers alloys, phase diagrams, and heat treatments that improve material strength. Viewers can learn more about metals and their applications through educational platforms like Nebula and CuriosityStream.
Takeaways
- 🔧 Engineering materials are typically divided into four categories: metals, polymers, ceramics, and composites.
- ⚙️ Metals are critical in engineering, with iron being the most important due to its role in creating steel.
- 🛩️ Aluminum and titanium are prized for their high strength-to-weight ratios, with titanium being especially valuable for high-temperature aerospace applications.
- 🔬 Metals have a crystalline structure where atoms are arranged in a regular lattice, but these lattices often have defects like vacancies or interstitial atoms.
- 🧩 Dislocations, or atomic misalignments, are responsible for plastic deformation in metals. Their movement causes permanent changes in structure when stress is applied.
- 🏗️ Strengthening metals can be achieved through methods like grain boundary strengthening, work hardening, and alloying with other elements.
- 🥇 Alloys are classified as ferrous (iron-based) or non-ferrous, with steel being the most significant ferrous alloy due to its various carbon content-based properties.
- 🔥 Heat treatment processes like quenching and tempering can further alter the properties of steels, enhancing their strength.
- 🧱 The arrangement of atoms in metals can follow structures like face-centered cubic (FCC), body-centered cubic (BCC), or hexagonal close-packed (HCP), affecting their density and strength.
- 🌐 Phase diagrams, such as the iron-carbon diagram, illustrate how metals change phases at different temperatures and carbon levels, helping engineers predict material behavior.
Q & A
What are the four categories of engineering materials?
-The four categories of engineering materials are metals, polymers, ceramics, and composites.
Why is iron considered the most important metal for engineering?
-Iron is considered the most important metal for engineering because it is used to create steel, which is a high-strength material with a wide range of engineering applications.
What makes aluminum a popular choice for engineering applications?
-Aluminum is popular for its high strength-to-weight ratios, relatively low melting temperature which facilitates casting, and its relatively low cost.
Why is titanium commonly used in aerospace applications?
-Titanium is commonly used in aerospace applications due to its excellent strength-to-weight properties, high strength, and suitability for high-temperature applications, despite its higher cost and difficulty in processing.
What is the difference between crystalline and amorphous materials?
-Crystalline materials, like metals, have atoms arranged in a regular, repeating grid called a crystal lattice. Amorphous materials, such as glass, have atoms arranged randomly without a long-range order.
What are the three most common crystal structures in metals?
-The three most common crystal structures in metals are face-centred cubic (FCC), body-centred cubic (BCC), and hexagonal close-packed (HCP).
What is a vacancy defect in a crystal lattice?
-A vacancy defect occurs when an atom is missing from its normal position in the crystal lattice.
How does the presence of dislocations affect the strength of a material?
-Dislocations can impede each other's motion through the lattice, which increases the material's strength. Materials with a higher dislocation density tend to be stronger.
What is the significance of grain size in polycrystalline materials?
-The presence of grains in polycrystalline materials impedes the motion of dislocations, making the material stronger. Smaller grain sizes result in stronger materials, as described by the Hall-Petch equation.
What is an alloy and how does it differ from a pure metal?
-An alloy is a mixture of metals or metals with non-metals created to improve the properties of the base metal. Alloys differ from pure metals in that they have added elements that can enhance properties such as strength, corrosion resistance, or ductility.
What is the role of heat treatment in improving the properties of steel?
-Heat treatment, such as quenching and tempering, can alter the microstructure of steel, leading to improved strength and toughness by controlling the formation of different phases like martensite.
Outlines
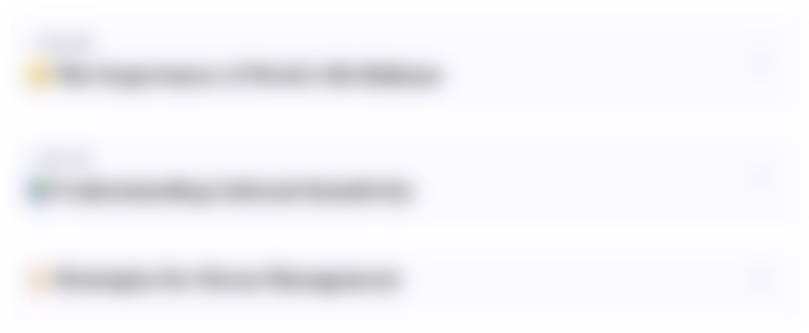
This section is available to paid users only. Please upgrade to access this part.
Upgrade NowMindmap
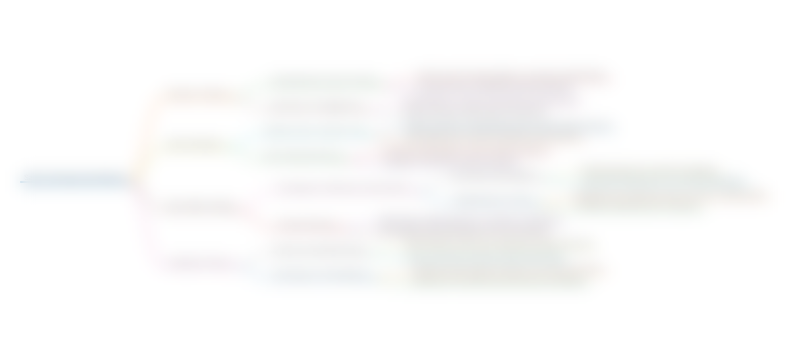
This section is available to paid users only. Please upgrade to access this part.
Upgrade NowKeywords
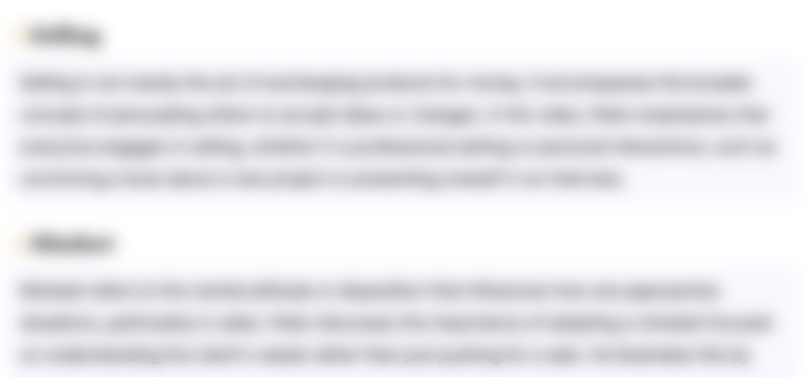
This section is available to paid users only. Please upgrade to access this part.
Upgrade NowHighlights
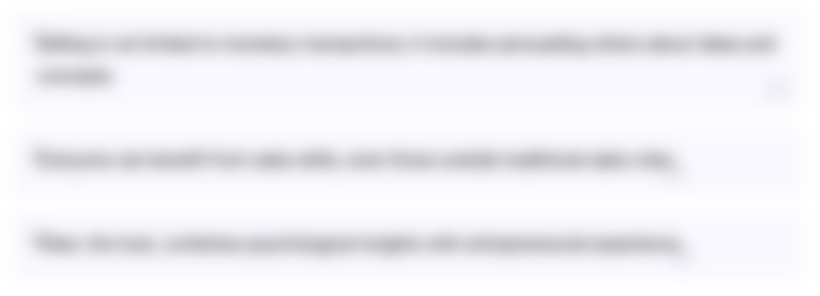
This section is available to paid users only. Please upgrade to access this part.
Upgrade NowTranscripts
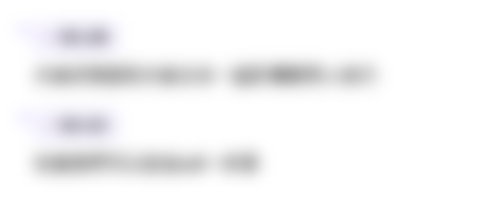
This section is available to paid users only. Please upgrade to access this part.
Upgrade NowBrowse More Related Video
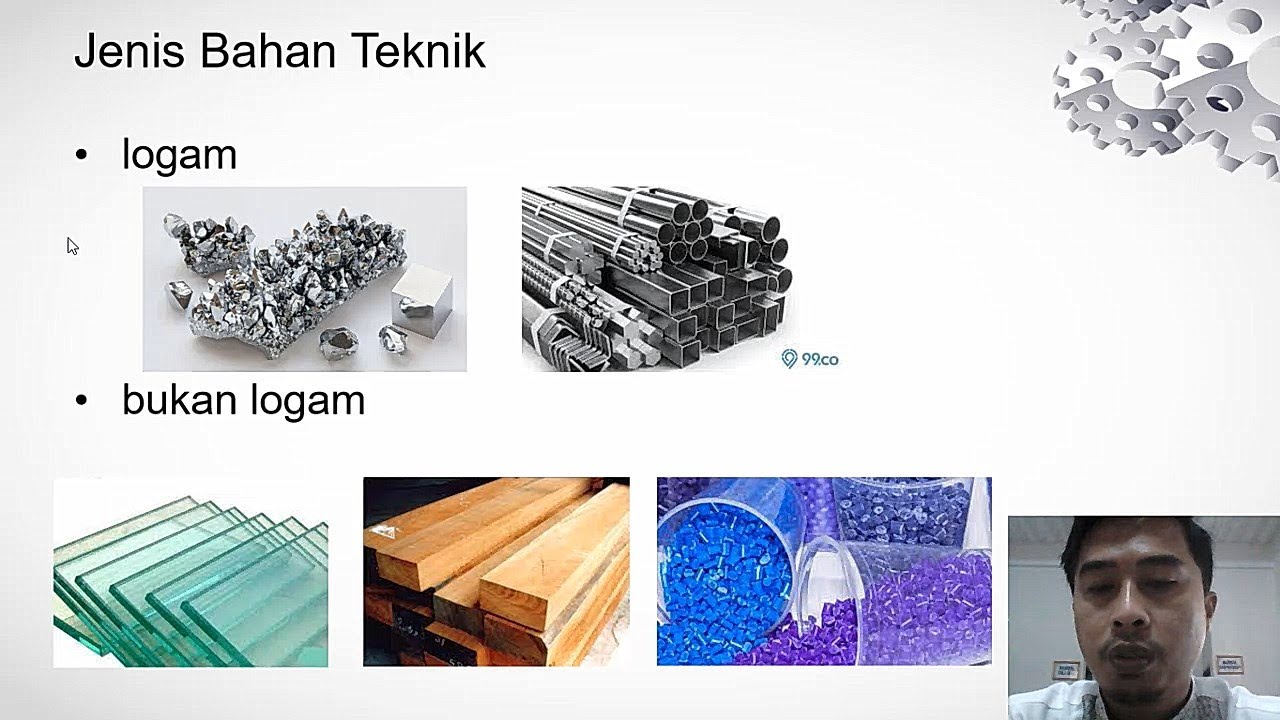
Pengetahuan Bahan Teknik
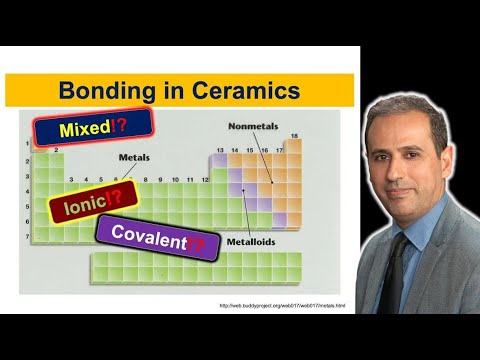
Bonding in Ceramics: Understand the Physical & Chemical Properties of Ceramics | #EME230
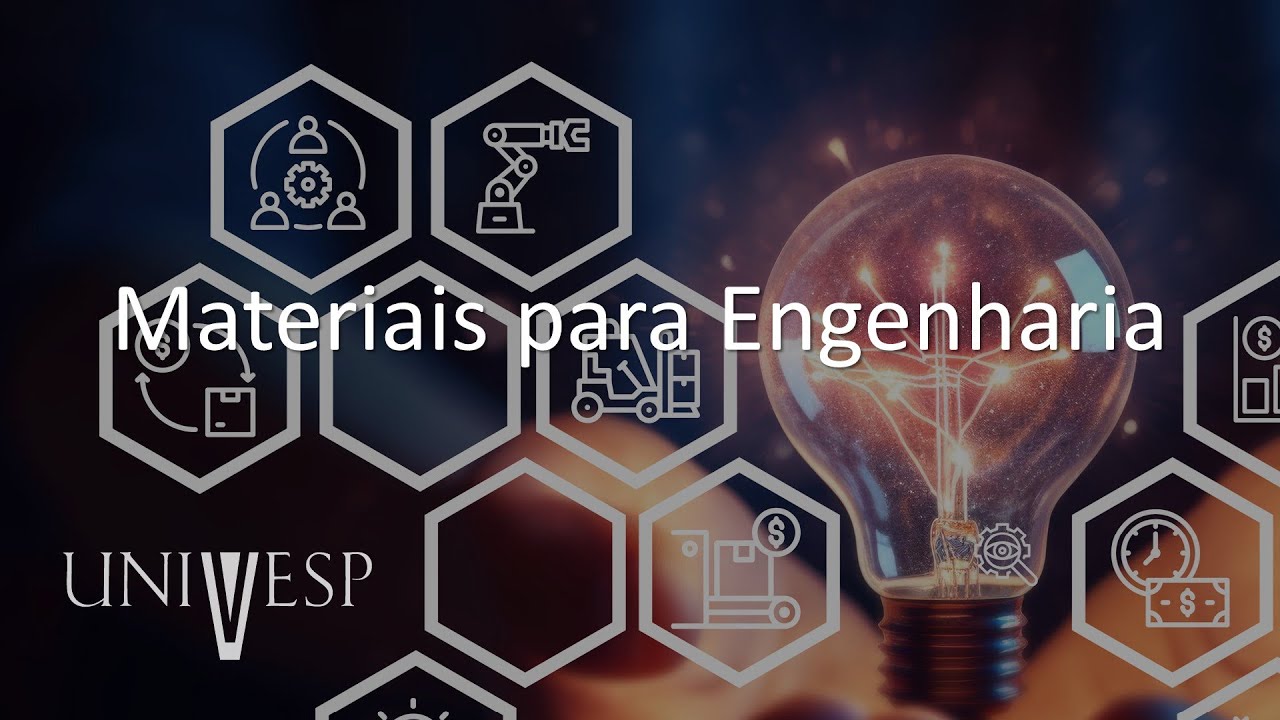
Materiais e Processos de Fabricação para Engenharia de Produção - Materiais para Engenharia

Introduction to engineering materials

stress strain curve explained with tensile test.
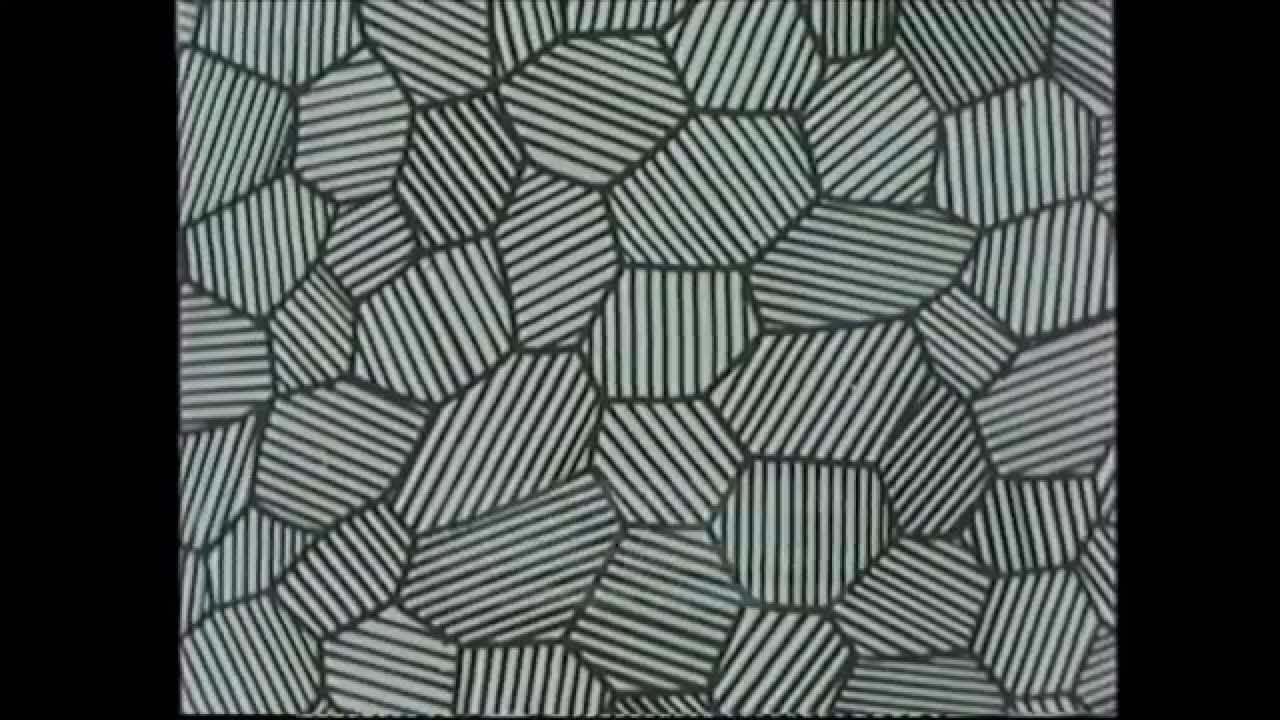
Properties and Grain Structure
5.0 / 5 (0 votes)