How Toyota Maintains 99.9999% Quality | Toyota Quality Management System | Invensis Learning
Summary
TLDRThis video explores Toyota's strategies for maintaining high-quality standards in the automotive industry. As a pioneer of lean manufacturing, Toyota emphasizes efficiency, waste reduction, and continuous improvement. The company also adopts Total Quality Management (TQM), focusing on customer satisfaction and involving employees in decision-making to ensure quality at every stage. Toyota's robust quality control system, strong supplier partnerships, and emphasis on customer feedback contribute to its reputation for excellence. The video concludes by highlighting Toyota's commitment to quality through various practices.
Takeaways
- 🚗 Toyota is renowned for its commitment to quality and innovation in the automotive industry.
- 🌐 Toyota pioneered lean manufacturing, emphasizing efficiency, waste reduction, and continuous improvement.
- 🔍 The lean manufacturing process aims to optimize each manufacturing step and create a flawless product.
- 📈 Toyota's approach includes six objectives: efficient use of resources, flawless products, cost reduction, customer demand, system adaptability, and strong customer-supplier relationships.
- 🛠 Total Quality Management (TQM) is central to Toyota's philosophy, focusing on continuous improvement and customer satisfaction.
- 📊 Toyota uses strategic planning programs to maintain a culture of quality achievement, involving all managers and employees.
- 👥 Employee involvement is key; Toyota encourages contributions from all employees in decision-making and problem-solving.
- 🔧 Toyota's culture is built on mutual trust, with frontline employees empowered to implement improvements and halt production if necessary.
- 🔬 A robust quality control system with rigorous testing and inspection procedures ensures defects are addressed before a vehicle leaves the factory.
- 🔄 The '5 Whys' method is used to identify and correct underlying problems, preventing future occurrences.
- 🤝 Toyota collaborates closely with suppliers, ensuring they meet high quality standards and contributing to overall product quality.
- 🗣️ Customer feedback is highly valued by Toyota, used to identify areas for improvement and maintain high quality standards.
Q & A
What is Toyota known for in the automotive industry?
-Toyota is known for its commitment to quality and innovation, being one of the largest and most respected automotive brands in the world.
What are the core principles of Toyota's lean manufacturing process?
-The core principles of Toyota's lean manufacturing process include efficiency, waste reduction, and continuous improvement.
What are the six additional objectives essential to achieve the overall objective of lean manufacturing?
-The six additional objectives are: 1) Optimize each individual manufacturing process step, 2) Create a flawless product, 3) Reduce the cost of production, 4) Create a product in demand among customers, 5) Ensure the system has adaptability, and 6) Maintain a solid and trustworthy connection between customers and suppliers.
How does Toyota implement Total Quality Management (TQM)?
-Toyota implements TQM by focusing on continuous improvement in all aspects of the organization, with a strong emphasis on customer satisfaction.
What is the significance of employee involvement in Toyota's operations?
-Employee involvement is significant as it allows Toyota to tap into the expertise and creativity of its workforce, ensuring quality is maintained at every stage of the manufacturing process.
How does Toyota's culture encourage frontline employees to improve working conditions?
-Toyota's culture is built on mutual trust and respect, encouraging frontline employees to develop and implement local improvements, with a sense of pride and community.
What is the Jiko Takafunge principle and how does it guide Toyota's approach to quality?
-The Jiko Takafunge principle ensures that defects are never passed on to the next step, indicating that every member of the workforce takes responsibility for the quality of their work, and anyone can raise an alarm and halt production if they detect a problem.
How does Toyota manage its relationship with suppliers to maintain high standards of quality?
-Toyota works closely with its suppliers, partnering with those that share its commitment to quality, providing firm order commitments, and encouraging year-over-year quality improvements.
What role does customer feedback play in Toyota's continuous improvement process?
-Customer feedback is highly valued by Toyota and is used to identify areas for improvement and make changes that help maintain high standards of quality.
How does Toyota assess customer satisfaction and significance?
-Toyota assesses customer satisfaction and significance based on four key variables: Customer Loyalty, intention to repurchase, perceived product quality, and attribution satisfaction.
What is the 5 Whys technique used by Toyota in quality assurance?
-The 5 Whys technique is used to identify the underlying reasons for problems so that they can be corrected and avoided from recurring, by asking 'why' five times in every matter.
How does Toyota ensure quality consistency at each level of each procedure?
-Toyota ensures quality consistency by having a comprehensive quality control system with rigorous testing and inspection procedures at every stage of the manufacturing process.
Outlines
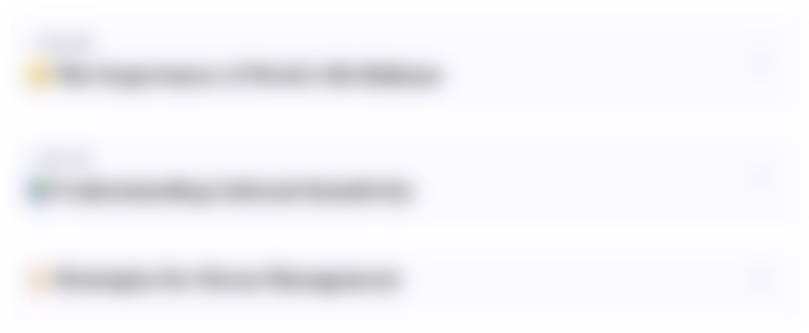
This section is available to paid users only. Please upgrade to access this part.
Upgrade NowMindmap
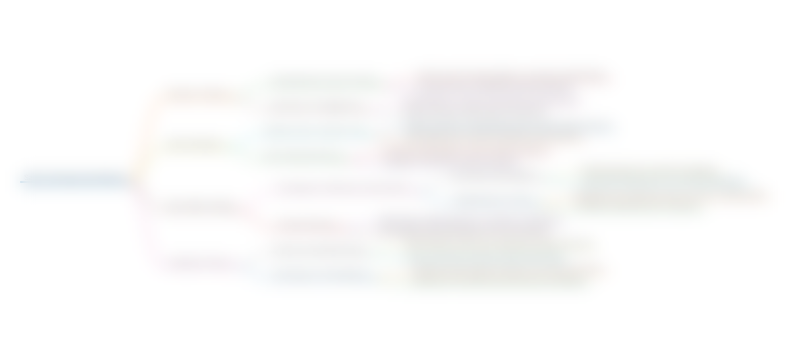
This section is available to paid users only. Please upgrade to access this part.
Upgrade NowKeywords
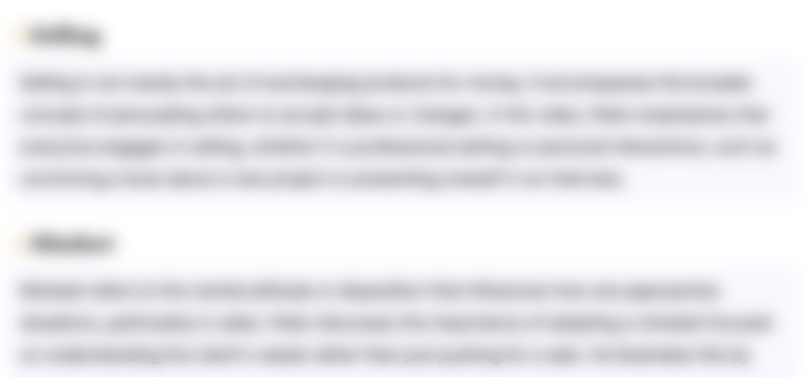
This section is available to paid users only. Please upgrade to access this part.
Upgrade NowHighlights
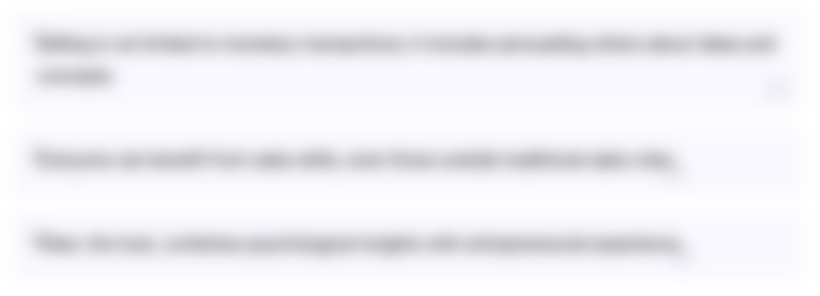
This section is available to paid users only. Please upgrade to access this part.
Upgrade NowTranscripts
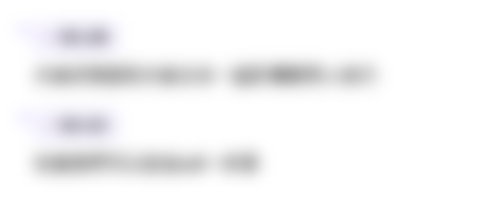
This section is available to paid users only. Please upgrade to access this part.
Upgrade Now5.0 / 5 (0 votes)